The cart is empty!
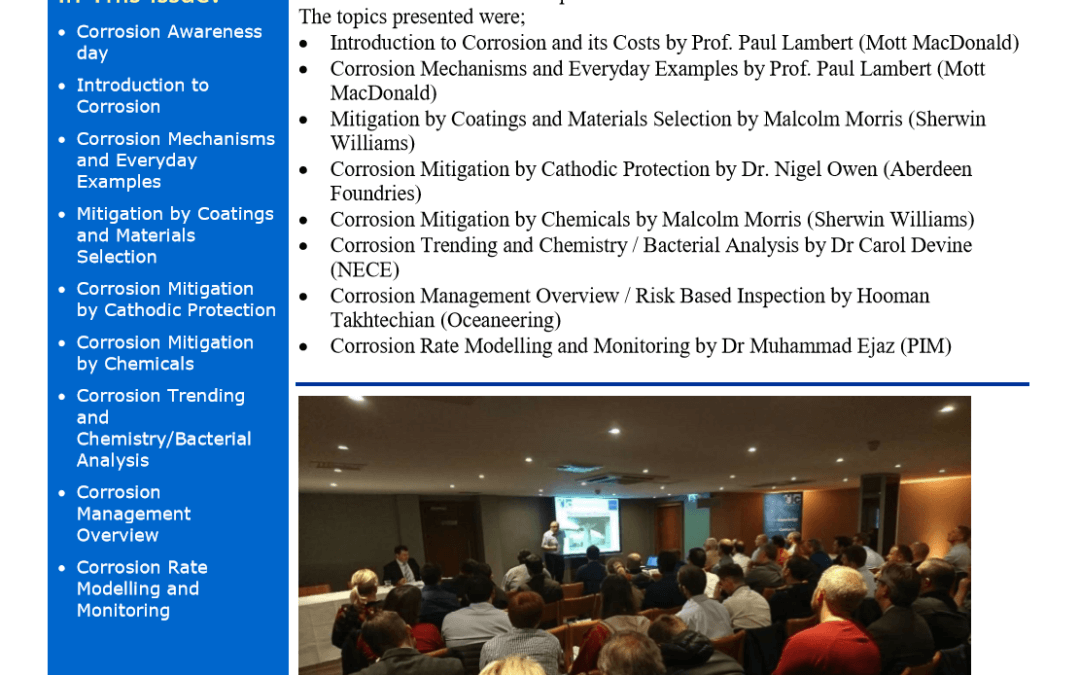
Defects and failure of assets during service may often be traced back to corrosion deterioration, thus corrosion monitoring and corrosion protection become a vital and integral part of asset construction and maintenance. Corrosion protection is valuable in preventing unplanned production stoppages or safety risks as result of asset performance reduction.
Assets such as bridges, platforms and transportation equipment require corrosion protection or monitoring as an integral part of the maintenance programme throughout the life of the asset. Several corrosion protection and monitoring techniques have been developed and these are widely used in the industry with the objective of slowing down the inevitable corrosion degradation process. The techniques selected will vary depending on the material to be protected and the exposure environment. It is important to note that application and maintenance of corrosion protection such as painting, cathodic protection are time consuming, costly and have safety implications.
The construction industry has adopted Lean thinking in order to improve the effectiveness and efficiency of construction work. This new working practice requires the use of specialist tools and techniques. Lean training is required to be undertaken so that Lean can be deployed throughout the supply chain. It is therefore essential for corrosion specialists to become acquainted with this new work practice and to have an understanding of its potential benefits.
In the construction environment corrosion protection and monitoring are often carried out, not as standalone activities, but alongside other work activities. This is more so during major maintenance works. For example, in road maintenance work several work activities compete for time and space in order to maximise traffic management. This means that a variety of work activities will be carried out in parallel, often within a restricted space and adjacent to live traffic. Therefore, good planning, logistics and engagement with other work trades become even more crucial to ensure that the corrosion protection processes can be carried out and delivered within time, budget and at the desired quality standard.
Furthermore, as part of the Highways England supply chain, contractors are required to adopt the Lean approach. Quoting from the Capital Efficiency Delivery Plan from Highways England, “It is recognised within Highways England that Lean deployment substantially contributes to the efficiency savings as set by the UK Government Road Investment Strategy (RIS) which runs from 2015 to 2020.”
Also, quoting from the Lean Support to Highways England 2015-2020 plan (1), “Lean has a target contribution of £250m towards the total of £1.2bn efficiency target. The objective is only realised by developing the Lean capability of HE staff and those of our suppliers. The supply chain organisations are now required to adopt these principles and are assessed in their progress by the Highways England Maturity Assessment (HELMA). Furthermore the application of Lean tools and techniques direct supports Highways England to achieve the Organisation Strategic Outcomes and Key enablers as set out in the Highways England Delivery plan.”
The corrosion community is part of the civil construction supply chain and it will be expected to demonstrate adoption of Lean as part of their organisation objectives, which will be assessed regularly.
The corrosion protection/ monitoring methodology is essentially a process which includes and relies on elements such as: manpower, machinery and equipment, material, method and information and design. This can be compared to the process requirements of a production system, with the activities forming an essential pre-requisite to delivering an effective task planning and process control. As a general rule, corrosion protection processes comprise of the following elements or activities (Figure 1).
Fig.1. Simplified generic corrosion protection/ monitoring process
By mapping and analysing the process stages and identifying what activities are value added or non-value added (waste), the opportunities for improvement will be revealed. Removal of waste from the process will result in projects being delivered efficiently, safer, within budget, providing required performance, and at rate required by the customer.
Background:
Over the past 40 years, many different industries, such as automotive, service, shipbuilding, healthcare, software and construction have adopted the principles and methodology of a renowned production system developed by the Toyota Motor Corporation to attain the same overarching operational targets of having a consistently effective production system and efficient processes. This production system is often called the Lean Production System (LPS), and will be referred to as Lean from now on. Lean has proven effective in contributing to a sustainable operational success on many occasions in different industries.
After the Latham report published in 1994, the UK Government set out to improve efficiency within the public sector. The Lean Production System (LPS) and its tools and techniques have been deployed since the late 2000s in large public organisations in the UK. For instance, Highways England has generated over £80M of benefits to date by applying the Lean tools and techniques to several of its schemes and projects within both the organisation’s internal processes, and across the supply chain (2).
This article will introduce some of the key principles and methods of Lean which, if deployed, are thought to be relevant to improving the effectiveness and efficiency of corrosion protection processes. The link between Lean and some common corrosion protection methods will also be discussed.
What is Lean?
Lean is a customer focused and structured production management system and process improvement methodology which aims to ensure the delivery of customer requirements at the required quality standards and rates. While delivering customer expectations, Lean utilises several tools and techniques to support the removal of waste within a process, thus ensuring a more efficient process.
An important aspect of Lean is the collection, understanding and analysis of the ‘as is’ state before the deployment of appropriate Lean tools and techniques. By achieving an in-depth understanding of the present state of the process, a Lean practitioner will be able to challenge the present process activities/practices.
There are five main Lean principles, which are described below and can be easily applied to corrosion protection:
In Lean, work activities of the ‘end to end’ process are assessed and categorised into:
A model of a Value Stream mapping analysis when all activities and links are shown and classified as VA, NVA and ENVA within a timeline, is shown in Figure 2. This provides a good visual representation of the activities that can and should be reviewed/ removed from the process, or to highlight where the main process improvement opportunities are.
Fig. 2. Schematic example of value stream mapping for corrosion protection
In general, works across the construction industry are impacted by environmental and weather conditions and differ from those of controlled and repetitive processes found in the manufacturing industry. It is important to understand and adapt the fundamental Lean principles in order to effectively deploy these into one’s own work conditions. This needs to be done through customised applications.
In line with the five principles, Lean identifies process wastes that need to be eliminated in a production system. In brief, the main wastes are those activities which the customer is not prepared to pay for, such as:
The use of untrained staff to perform specialised activities creates defects in the short, medium and long term and has direct impact on the protection and asset performance. Corrosion specialists are aware that the application of specialised corrosion protection and corrosion monitoring relies heavily on how they are executed. A lot of the times the execution of the protection is as important as the materials used. Therefore staff training is vital to the performance of the corrosion protection.
Lean Methods and Systems
At the operational level, the Lean principles are realised by implementing some Lean methodologies, tools and techniques. The selected tools and techniques outlined in this section have been chosen as their use seems to fit with the corrosion protection and monitoring activities, and where the corresponding benefits can easily be identified.
The Last Planner System or Pull Planning
Unlike highly structured and controlled work environments like factories and shop floors, corrosion protection of large structures/assets generally take place in dynamic and complex environments, such as, construction sites, motorways or oil platforms, where the tasks of trades are interconnected and dependent on many uncontrollable factors. In those complex work environments, alongside systematic coordination and constant planning and re-planning, proactively and collectively eliminating task constraints takes precedence. For those purposes, the Last Planner System (or Collaborative Planning as it is called in the UK) has been successfully used in project-based production systems for more than 25 years to provide a “pull-based” production planning and control mechanism that is executed by the very “doers” of tasks. (Plans are not pushed by “planners, schedulers or senior managers” who are detached from the actual production.) The Last Planner System goes beyond the Critical Path Method (CPM) by not only effectively controlling tasks themselves, but also controlling complex process flows and trade interactions (3).
The Last Planner System is essentially a collaborative planning process or method that involves the stakeholders such as, trade foremen and design team leaders (the last planners) in planning in detail the work to be done throughout the project. The discussions become more and more detailed as the work progress. This technique was created to enable more reliable and predictable production in projects. It also supports the flow of work through the project, building trust and collaboration within a project team and delivering safer projects faster. It brings together those who will execute the work (the team) to plan when and how work will be done through a series of conversational processes. It requires the group to remove constraints collaboratively as a team and to promise delivery of each task for the team.
The use of the Last Planner will promote engagement and discussions with stakeholders’ representatives at the beginning of the project, allowing for their understanding of the work interactions, any issues or any ideas they may have for improvements, and will lead to their consensus on the rate of work. The teams will actively work together and cooperate with other teams and trades to remove any process constraints to keep their planning promises on track. The 6 week look-ahead, with a review process every 2 weeks, has proven to be an effective approach to reduce project durations by up to 30%. Weekly meetings offer valuable learning and improvement opportunities for even more reliable planning in the future. It is also important to collect data on percentage planned completed (PPC) to measure performance against targets and review what went well and what didn’t go so well, to ensure lessons learned are understood and communicated to the team in order to drive Continuous Improvement.
These systematic processes increase the chances that the work flows reliably, and recognizes that personal relationships and peer pressure are critical to that process. The basic planning stages of the Last Planner include,
The Last Planner System is highly applicable in corrosion protection planning and control. As there are several trades working together under complex project systems in corrosion protection, and sometimes within confined spaces and with limited time to complete the work, the Last Planner System would render an effective mechanism to engage the trades, and to ensure they all understand the impact of each of their activities on others. Such as, if the scaffolding is not in place in time, the blasting is delayed or the fact that the paint or the equipment is not in place, will impact on the delivery time and the process flow.
As the process progresses, a daily stand-up meeting around a Continuous Improvement cell or board should take place to check, in detail, what has gone well, what has not gone well, and why. This is known as the 3C’s tool (Concern, Cause and Countermeasure) and it makes certain that the day meeting is focused on these points. This practice also ensures that all raised concerns are discussed and addressed by those involved in doing the work, as resulting actions will promote improved work flow for the next day or shift.
Caption : The daily meeting, credit Katie Jones, Graham construction
Visual Management and the 5S
Lean work places rely extensively on visual communication (i) to make deviations and non-compliances obvious, (ii) to increase coordination, (iii) to reduce complexities in the work environment, (iv) to help teams to understand the purpose of communication easily, (v) to facilitate process transparency to reduce the number of work-related questions people may pose, (vi) to guide people to work efficiently on their own (self-control), and (vii) to reduce human-related errors. This conscious information visualization, or work-facilitation strategy, is called Visual Management. For instance, daily team meetings are held around performance boards to review past performance and future constraints, which openly display the Key Performance Indicators (KPIs). Standard operating sheets and instructions (i.e. process, health and safety, quality etc.) are highly visual and integrated into the workplace, close to the operations, not in drawers or anywhere far from the operational area. Daily and look-ahead work plans are communicated to the teams on visual boards or sheets in an easy-to-understand fashion. Problems in the processes are immediately signaled by the workforce using ‘andon’ lights. (The term ‘andon’ most often refers to a signaling system used to call for help when an abnormal condition is recognized, or that some sort of action is required.) The pace of processes and material consumptions as per production plans can be regulated in a “pull” fashion by using simple cards called kanban. (Kanban is Japanese for “visual signal” or “card.” Toyota line-workers used a kanban, i.e., an actual card, to signal steps in their manufacturing process.)
In order to realise Visual Management, a systematic visual workplace framework should be followed (see Figure 3).
Fig 3. Visual workplace framework (Adopted from Tezel and Aziz, 2015, reference 4)
A brief explanation of the framework elements is as follows:
Continuous Improvement tools
Continuously improving process (i.e. methods, tools/equipment, and information systems) and workplace elements are an integral part of Lean. There are some frequently employed continuous improvement strategies, tools and techniques
Corrosion Protection and Lean
The table below summarise’s the Lean tools and techniques that could be deployed in corrosion protection/monitoring processes, and identifies their potential benefits. It should be noted that this table highlights only some initially conceived connections that can, and will be expanded as the implementation progresses and matures.
Table1. Conceptual link between corrosion protection methods and some Lean tools/ techniques
Corrosion protection | Lean tools/ techniques | Objective | Benefit/s |
Anti-corrosive painting | The Last Planner System | Ensure all stakeholders/trades are aware of the various activities and their impact on the overall process & understand customer expectations at every stage of the process | Check the opportunities for changes within the work activities to minimise, effort, time, e.g. This can be as simple as leaving access ladders in place for the next work activity |
Painting | Critical to quality (CTQ) analysis | Ensure that stakeholders understand what and how their work needs to be performed to the satisfaction of their customers. That should reduce time waste as result of re-work before the follow up activity can be performed. | Reduce constraints/ re-work |
Painting | 5S | Ensure that materials and equipment are kept under controlled environments, ready to be handed at the start of the work and labelled and within up to date calibration dates | Prevent delays to the process, ensure PPE reducing H&S issues. Ensure paint material not exposed to temperature extremes which will result in material deterioration. Prevent wasted time trying to find the right equipment/ materials to perform the work. |
Painting | Use of kanban | Ensure that there is a flag raised at the end of each stage to ensure the next stage starts only once the previous is completed, thus preventing awaiting time and uncertainties | Maximize performance, managing workflow and ensure each stage is finalized and/or inspected before next one starts to prevent defects |
Painting/ Cathodic Protection | Skills checking | Ensure workmanship has necessary training and skills to perform the tasks | Maximise coating/ anti-corrosive performance thus prevent early failures increasing asset whole life costs. Prevent waste due to skills misuse. |
Cathodic protection | The Last Planner System | Ensure all stakeholders/ sub-contractors are aware of the required access, tools, materials & skills necessary to allow for the implementation of the Cathodic protection | Prevent time waste, delay on the works, reduce performance of the system. |
Conclusion & Recommendations
Material deterioration as result of corrosion is often accepted as unavoidable and it has led to the lack of awareness of the economic aspects of corrosion. The estimated cost of corrosion as per Hoar committee findings is around 3.5% of the UK GDP (Hoar report – 1971, reference 5). For major asset owners, maintenance of the anti-corrosion technology is an integral part of the asset design and management to ensure asset integrity throughout its service life.
Maintenance intervention for corrosion protection is costly and the number of interventions will vary with asset design life, quality of the protective material, workmanship and service environment. Deployment of Lean is likely to improve the efficiency and effectiveness of corrosion protection/monitoring. This can be achieved by using the Lean techniques described in the previous sections.
As examples:
Deployment of the Lean tools and techniques will result in reduction of time, cost and H&S risks associated with corrosion protection and monitoring. Applying the Lean principles to corrosion protection and monitoring will also improve the quality and reduce the whole life cost of major assets, which will be of a direct benefit to asset owners and customers.
Raising awareness of Lean among corrosion protection professionals, and documenting some implementation cases, seem of critical importance for Lean to diffuse into the corrosion protection sector.
References
Acknowledgments
The authors would like to thank John Fletcher of Elcometer, and past President of the Institute of Corrosion, and Katie Jones – Lean Manager of Graham Construction, for their contributions to this article.
Notifications