Rob Allan, Emre Karapinar, Malcolm Morris, Neil Wilds and Sarah Vasey, Sherwin-Williams Protective & Marine Coatings.
Glass Flake Epoxy (GFE) technology has been a main stay of the Oil &Gas (O&G) offshore market for many years, particularly for highly aggressive splash zone areas, despite other technologies for similar end uses having been investigated. This, consequently, resulted in the opportunity of assessing the performance of these materials in real life conditions and enabled coating suppliers to optimize their GFE formulations for wider end uses and longer service life times.
The versatility of glass flake epoxy technology allows it to be used not only for O&G offshore applications but for buried steel in O&G downstream applications, subsea pipelines and equipment, and even for bridges & highways where local authorities – such as Network Rail and Highways Agency in the UK – dictate the use of such a technology due to its superior anti-corrosion properties and longer service life times.
Use of glass flakes in combination with other functional pigments (for example, aluminium) or more advanced epoxy polymers (such as surface tolerant epoxies, epoxy novolacs, amine cured epoxy linings…etc) delivers effective long term protection of water, fuel, and chemical tanks, vessels and pipelines, as well as maintenance and repair of such steelwork whether it’s immersed or atmospheric.
Traditionally, glassflake coatings were based on relatively large particle size glass flake pigments (nominal width 0.4mm). These coatings typically required approx. 500µm to achieve a full film and an overall specification could be in excess of 1mm dry film thickness. However extensive research and development using significantly smaller glass flakes has enabled the production of formulations which could deliver equivalent performance at much lower film thickness, and with a vastly superior aesthetic appearance.
In this respect various tests have been conducted to understand the effect of glass flake pigmentation on the overall performance of epoxy coating systems. It is commonly accepted in the coatings industry that glass flake pigmentation increases barrier properties of the dry film and enhances mechanical properties, making it an ideal choice for immersed and buried steel. Table 1 clearly displays the benefit of using glass flake in a 500 microns thick dry epoxy film, which was loaded with 20% w/w glass flake at an average particle size of 0.4mm.
Benefits of incorporating glass flake in modern coating specifications
The current criteria for selection of coating specifications includes, reduced VOC and elimination of toxic components to comply with ever more stringent environmental legislation; fewer coats to reduce application costs; improved performance to give longer life to first maintenance compared to traditional multi-coat systems; and proven performance with external independent test evidence – NORSOK, Oil Company, Highway, Network Rail, specifications and ISO 12944.
Glass flake pigmentation is a primary weapon in the formulator’s armoury, which can be incorporated in a range of high performance binder systems to produce coatings with the following benefits;
• Very low VOC content.
• User friendly – easily applied over a wide range of specified film thickness.
• Superior resistance to water ingress.
• Good mechanical properties – adhesion, abrasion resistance, flexibility.
• Compatible with cathodically protected steel on immersed structures.
• Capable of withstanding a wide range of chemical resistance and high temperature conditions, depending on the binder
system used.
Glass flake
Borosilicate glass (c – glass), with a thickness of 1 – 7 microns, and various nominal particle width grades, viz,
3.2mm – used for trowelling compounds
0.4mm – used in high build spray applied coating
micronised – used in spray applied coatings – low and high (typical 45 micron) build.
Binder types
The main properties of a coating are dependent upon the resin system employed. These may be enhanced, or even detracted from, by the pigments and other ingredients included.
Epoxy
The properties of epoxy resins enable them to be formulated into coatings to provide protection over a wide range of specification requirements, including, excellent corrosion protection for subsea, splash zone and atmospheric environments, excellent resistance to cathodic disbondment, toughness and abrasion resistant. They have a long track record, and there are no catalyst storage problems. The disadvantages however are, maximum immersion temperature typically 60C, maximum dry heat resistance typically 120C, chalking/colour retention problems on atmospheric exposure, and generally poor acid resistance.
Polyester
These consist of isophthalic or bisphenyl polyester resins, cured with organic peroxide catalysts. They offer improvement in performance over epoxy in terms of mechanical properties and temperature resistance, with maximum immersion temperaturetypically 80C and maximum dry heat resistance typically 140C. The isophthalic polyesters are more resistant to chalking and offer superior colour retention on atmospheric exposure compared against epoxy. Polyesters can also offer faster curing rates than high solids epoxies, although applicators need to be sufficiently aware of the relatively short pot life, and safety aspects of the catalyst. In order to minimise potential problems with the relatively short pot life of these products, twin component application equipment is used.
Vinyl Esters
These have the ultimate performance in terms of chemical and temperature resistance, with maximum immersion resistance typically 120C and maximum dry heat resistance typically 220C. (in sea water immersed structures, the cooling effect of the water allows application onto substrates operating at much higher temperature, e.g. pipelines with an internal temperature of 180C).
Specification philosophy – film thickness
Traditionally glass flake coatings have needed to be specified at dry film thicknesses in the order of 500 – 1000 microns, due to constraints caused by their application characteristics. These thicknesses are required for performance under some, but not all, environments. For atmospheric anticorrosive protection of structural steel, for example, such thicknesses can be over-engineered, and uneconomical. A range of glass flake coatings which can be applied at different film thickness, ie to give the required protection without the need to apply more paint than is necessary is now available. Extensive laboratory testing, and track record in the field, have proved the validity of such specifications which can be devised in conjunction with the ISO 12944 standard, plus testing to NORSOK or oil company performance testing.
Formulation Aspects
Given the available raw materials, how can they be combined to achieve the required performance?
The theory of glass flake pigment particles aligning within an applied paint film to give an extended diffusion pathway through the film is well documented, as is the reinforcing nature of the lamellar pigment. There are, however possibilities where particles of glass can end up misaligned in the film and if these particles have a length greater than the film thickness, they can create a potential fault within the coating leading to accelerated permeation through the film. This effect can lead to the necessity of applying very thick films or multi coat application to compensate for these defects, and pass high voltage pinhole detection testing.
Micronised glass “Controversy”
The incorporation of micronised glass flake into high build epoxy coatings has been a cause for debate. It is accepted that the lower aspect ratio of the micronised flake does not give the same potential diffusion pathway as the larger flake sizes, and indeed a straight A versus B comparison of 0.4 mm flake against micronised flake at constant loading in the same resin system will show that the micronised flake pigmented system has higher rates of water absorption and vapour permeability compared with the larger flake (tables 1 and 2).
Research has shown however that in epoxy systems, combination of the micronised flake with other lamellar fillers and zinc phosphate, gives a synergistic effect which offers similar permeability characteristics to large flake systems (tables 1 and 2), coupled with a closed, defect free film which offers, ease of application using smaller spray tips than standard glass flakes allow, film thickness variable from 200 microns to 1000 microns depending on end requirements, retention of mechanical properties, abrasion resistance, cathodic disbondment, coupled with outstanding corrosion resistance (tables 3 – 5).
Glass flake levels
There are no official standards governing glass flake levels compared with the criteria laid down for zinc phosphate for example in BS 5493. The factors to be considered include:
1. Steric effects of glass flake – overloading will cause physical interference between flakes which may in turn give rise to film defects.
2. Viscosity increase – Higher levels of glass flake cause increased viscosity which will eventually affect application characteristics,
and that actual test data shows that more is not necessarily better. In short, there is no such thing as a universal optimum for glass flake loading. This is a case of “horses for courses” with the type of glass flake and its level of incorporation having to be thoroughly researched with the particular end use in mind. An epoxy based formulation intended for anticorrosive protection of structural or immersed steelwork will be quite different in terms of glass type and content to a vinyl ester for chemical resistant vessel linings.
Primer requirements
In the case of glassflake epoxy materials formulated on a blend of glassflake and zinc phosphate, a separate primer coat is not necessary from the viewpoint of anticorrosive performance, although in practice they are often used in conjunction with a proprietary epoxy blast primer or epoxy zinc phosphate primer.
In the case of polyester or vinyl ester specifications, a vinyl ester based holding primer is available to maintain the integrity of grit blasted substrates prior to application of the glassflake coating. For non-immersed systems it is permissible to apply specially formulated glassflake polyester over epoxy primer. Work is ongoing to confirm whether epoxy primers may be used under immersed polyester/vinyl ester systems. However until results are confirmed, the vinyl ester primer should be used under any immersion system.
There is a synergistic effect of incorporation of zinc phosphate with micronised glass flake with gives similar results to larger flakes.
Increasing glass flake size reduces permeability of vinyl ester systems. In this case, zinc phosphate cannot be incorporated due to its effects on the curing mechanism of the resin system.
Abrasion resistance is improved with increasing 0.4 mm glass content up to 20%, however further increases actually cause an increase in loss of coating.
Coating Applied at 500 microns dft
|
Water Vapour Permeability g/m²/day ASTM E96
|
Water Absorption % to Equilibrium ASTM 570-81
|
Control. No Glassflake or
Zinc Phosphate
|
5.9
|
6.54
|
Epoxy, 0.4 m Glassflake
|
1.05
|
1.18
|
Epoxy, Micronised Glassflake. No Zinc Phosphate
|
3.5
|
2.8
|
Epoxy Micronised Glassflake & Zinc Phosphate
|
1.26
|
1.21
|
Table 2 – Water Absorption/Permeability Vinyl Ester.
Coating Applied at 500 microns dft
|
Water Vapour Permeability g/m²/day ASTM E96
|
Water Absorption % to Equilibrium ASTM 570-81
|
Control. Unpigmented Vinyl Ester
|
8.24
|
7.3
|
Vinyl Ester Micronised Glass
|
2.24
|
3.56
|
Vinyl Ester 0.4 mm Glass
|
1.04
|
0.25
|
Vinyl Ester 3.2 mm Glass
|
0.59
|
0.15
|
Table 3 – Abrasion Resistance Comparison – Taber Abrador
Weight Loss Per 1000 Revolutions, 1000 gm Load H22 Wheel
Resin Type
|
Glass Type
|
Glass Loading
|
Wt Loss
|
Epoxy at 500 microns dft
|
|
0%
|
0.703g
|
|
0.4 mm
|
5%
|
0.692g
|
|
|
10%
|
0.499g
|
|
|
15%
|
0.463g
|
|
|
20%
|
0.120g
|
|
|
25%
|
0.806g
|
Epoxy at 500 microns dft
|
|
0%
|
0.612 g
|
|
Micronised & Zn Phos
|
10%
|
0.403g
|
|
|
25%
|
0.392g
|
Vinyl Ester at 500 microns dft
|
|
0%
|
0.725 g
|
|
0.4 mm
|
5%
|
0.621g
|
|
|
10%
|
0.306 g
|
|
|
20%
|
0.300g
|
|
|
25%
|
0.378g
|
Increasing glass flake levels improve cathodic disabondment performance (CD). However zinc phosphate content would appear to be a major contributory factor in CD of epoxy glass flakes.
Micronised glass flake does not perform well in polyester (or vinyl ester) resin systems on CD testing, and a glass flake loading of approx 20% of 0.4 mm flake is necessary for acceptable performance. Dft is also a crucial factor in the performance of these systems.
Accelerated laboratory tests further confirm the superior performance of micronized glass flake epoxies (MGFE) over non-glass flake or ceramic filled epoxies. Figure 1 highlights this superior performance by carrying out salt spray (ISO 9227) tests for up to 6,000 hours, which is well over typical test durations in O&G, Power, Mining and Minerals and other industrial end uses.
Figure 1 – Micronised glass flakes epoxy versus ceramic filled epoxy.
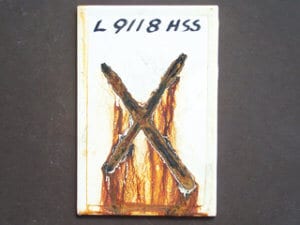
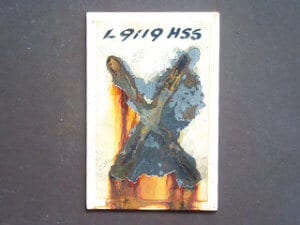
Micronised Glassflake Epoxy @ 200µm Ceramic filled epoxy
Table 4 – Cathodic Disbondment Testing – Epoxy Formulations
28 Days at -1.50 Volts wrt Silver/Silver Chloride Electrode
Resin Type
|
Glass Type
|
Glass Loading % Wt on Pigments
|
Temp
|
mm Disbondment
|
500 µm Epoxy
|
0.4 mm
|
0
|
23°C
|
28mm
|
|
|
5
|
|
25mm
|
|
|
10
|
|
16mm
|
|
|
15
|
|
17mm
|
|
|
20
|
|
13mm
|
|
|
25
|
|
7mm
|
1000 µm Epoxy
|
|
0
|
|
14mm
|
|
|
5
|
|
10mm
|
|
|
15
|
|
5mm
|
|
|
20
|
|
4mm
|
|
|
25
|
|
5mm
|
400 µm Epoxy
|
Micronised & Zn Phos
|
0
|
|
10mm
|
|
|
10
|
|
7mm
|
|
|
25
|
|
6mm
|
800 µm Epoxy
|
|
0
|
|
4mm
|
|
|
10
|
|
1-2mm
|
|
|
25
|
|
1mm
|
Table 5 – Cathodic Disbondment Testing – Vinyl Ester/Polyester
28 Days at -1.50 Volts wrt Silver/Silver Chloride Electrode
Resin Type/ Glass Type
|
Glass Loading
|
Temp
|
mm Disbondment
|
500 µm Micronised Polyester
|
25%
|
23°C
|
Film degraded at holiday Polyester
|
500 µm 0.4 m Polyester
|
10%
|
23°C
|
20 mm Some degredation
|
500 µm 0.4 m Polyester
|
20%
|
23°C
|
4-5 mm
|
1000 µm 0.4 mm Polyester
|
20%
|
23°C
|
0 mm
|
500 µm 0.4 mm Vinyl Ester
|
20%
|
23°C
|
2 mm
|
1000 µm 0.4 mm Vinyl Ester
|
20%
|
23°C
|
0 mm
|
1000 µm 0.4 mm Vinyl Ester
|
20%
|
60°C
|
0.5 – 1.0 mm
|
Table 6 – Hot CD Testing – 28 Days at -1.50 Volts wrt
Silver/Silver Chloride Electrode
Internal Wall Temp
|
1mm dft
|
2mm dft
|
3mm dft
|
100°C
|
4mm
|
9mm
|
|
120°C
|
5mm
|
5mm
|
|
140°C
|
|
5mm
|
4mm
|
160°C
|
|
|
5mm
|
The micronized glass flake epoxy technology has delivered excellent performance over a 25 year track record. Relying on experiences gained from this success, the technology has been extended for end uses where properties such as surface tolerance, high film build in one layer by brush application, ability to go over damp surfaces, suitability to be applied over hot substrates are amongst the key requirements sought by asset owners, engineering contractors and paint applicators. This makes the micronized GFE technology, which is capable of building up to 400µm in a single brush coat and able to go over hot substrates up to 120C, ideal for challenging maintenance and repair scenarios typically observed in O&G offshore and other similar heavy industries. It allows for maintenance painting on hot process steel (up to 120C) without the need to take the asset or process unit out of service, saving time and cost for the asset operator.
A proprietary product, which was formulated on the basis of micronised glass flake epoxy technology, has been evaluated to determine the effect of prolonged high temperatures on it after being applied to Sa2.5 blasted, and St2 and St3 hand prepared steel, at high temperatures (110C and 120C) and then stored at 150C, in comparison to when applied and kept at ambient temperature. In summary, the testing on heat aged samples showed that there was very little change on cross cut adhesion (ASTM D3359) over 1-6 months (see Figures 2 and 3); no or other deterioration of the film was observed after 6 months heat ageing, and Thermogravimetric Analysis (TGA) showed no weight loss in the samples test up to 6 months in test area i.e. 150C (Figure 4).