The cart is empty!
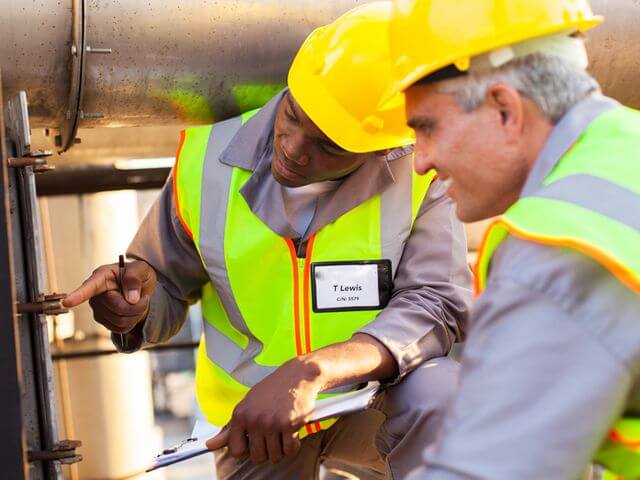
The Critical Nature of Coating Inspection in Corrosion Management
The Essential Role of the Coating Inspector
Effective corrosion management relies on coating inspection, carried out by a certified coating inspector. In this article, you’ll learn why coating inspection is critical, and the responsibilities of contractors and asset owners.
Quality of protective coating is not just desirable – it’s critical
As consumers, we are used to goods and services that we buy meeting a certain standard. In fact, quality is something we expect. After all, if the produce we buy from a supermarket isn’t up to scratch, we won’t shop there again. We expect a restaurant that comes recommended to produce the finest cuisine with exceptional service. If we’re disappointed, we make a complaint and refuse to pay the service charge.
However, in some situations we cannot afford to take a chance on quality. In industries such as oil and gas, rail, highways, and infrastructure, poorly executed work can be disastrous – not only financially but also with potential loss of life.
When a coating is applied to an asset, its primary purpose is to protect it against corrosion and give longevity of life to the asset; this process needs managing. The coatings need to be applied correctly by trained and certificated applicators, and certificated inspectors play a vital role in ensuring the process is delivered correctly.
A coating inspector’s work is to confirm that coatings have been applied correctly, to prevent corrosion that can have disastrous consequences.
Why can’t we just trust coating applicators?
In the UK, coating applicators are trained and qualified under the Industrial Coating Applicator Training Scheme (ICATS). Such training should ensure that applicators carry out their work in a professional manner and deliver a high quality of work. But it’s not quite that simple, and the risks associated with errors are too large to leave work unchecked.
People make mistakes, and a quality check makes sure that mistakes are corrected before they become expensive errors. A specification could be misread, or a detail missed.
In short, the coating inspector is a safety net, to help avoid dire consequences of human error.
Who is responsible for coating inspection?
The responsibility for coating inspection falls on both the contractor and the asset owner.
Contractors should have their own coating inspectors to check the work of their applicators. This is a mandatory requirement in industries such as rail and highways. It’s good business practice, and helps to foster good client relationships by ensuring quality of work is maintained.
However, the asset owner should never rely on the contractor to confirm the quality of their own work. That’s one huge conflict of interest to be avoided. So, good asset owners will employ their own coating inspectors, or hire a third-party coating inspector to check the protective coating application a second time. Using this strategy, asset owners should avoid the disasters that could be caused by contractors who may be tempted to cut corners.
In summary
Protective coating systems are complex. As we have been highlighting in our series outlining ISO 12944, coating is impacted by a range of factors that include:
Such factors make application complicated. It is therefore preferable for highly trained and suitably qualified professionals to collaborate. This should ensure that:
- Specifications are met
- Standards are maintained
- Quality is assured
While the contractor will wish to ensure their work is of the highest quality, the ultimate responsibility rests on the asset owner. After all, it is in their best interests to make certain that disastrous failures of coating systems are avoided – a valuable by-product of which is that properly applied protective coatings will protect assets more effectively and reduce the costs of ongoing maintenance.
For more information about our Coatings Inspector Training, please email the Institute of Corrosion at admin@icorr.org.