Latest News
The questions this issue relate to the maintenance and servicing of corrosion monitoring devices for pipelines and process pipework, and conflicts between coating specifications and the product data sheet requirements.
Question:
In a previous issue (editor, March/April 2020) the question of the selection of suitable equipment for effective corrosion/erosion monitoring in process plants and pipelines operating across a wide range of temperatures and pressures, was discussed.
In order to be in contact with the process fluids to test them, devices such as coupons (normally of same material as the pipe), electrical resistance probes, bio probes, chemical injection quills, galvanic probes and other sampling equipment are inserted through proprietary access fittings, either flanged or welded connections.
Can you explain how these devices are maintained, and serviced, in a safe and cost-effective manner? What precautions should be taken before engaging a vendor to perform this work, and what preparations are required at the worksite? AB
Answer:
This type of monitoring equipment is manufactured in many countries by a wide range of vendors (in varying degrees of quality and equipment monitoring sensitivity), therefore carefully review, all associated QA documentation, materials of construction, test certification and installation procedures.
Great care should be taken in the selection and purchase of such intrusive equipment to check that it complies with all relevant standards such as NACE MR0175 requirements (Parts 1/2/3 – Cracking resistance of materials) and NACE MR0103 (specifically for sour service in refineries).
An intrusive monitoring, and associated servicing, system normally comprises of 5 main components – high pressure (HP) online retrieval tool, a HP double block and bleed service / safety valve, a mechanical or hydraulic access fitting system (permanently connected to outside of the pipe/pipeline or pressure vessel), the internal monitoring device holder (with seals for primary pressure isolation) and the device itself that is to be serviced, such as a test coupon. In addition, a heavy-duty cap provides secondary pressure sealing/containment in normal operation, after the tool has been removed for service.
It should be noted that these monitoring devices form part of a pressurised system for process containment, and the regular corrosion risk assessment data obtained from them contributes to determining how frequently the remaining piping circuit (which can be of considerable length) requires to be monitored by full inspection and other NDT – non-destructive testing methods such as ultrasonic or radiography. The data from these devices (often now transmitted wirelessly), also influences other mitigation measures such as control of water content and chemical injection, with adjustments made to chemical dosing according to the corrosion rate measured on the test device, to within agreed targets / KPI’s – Key Performance Indicators. Further, these devices also monitor problematic contaminants such as bacteria (through sessile swabs taken at device retrieval) that can accumulate in the system, especially when the system is put out of service for any significant period of time without pre-treatment (e.g. biocide addition).
Removal of these in-service devices should only be undertaken by competent/trained personnel, due to the risks of injury and potential loss of process containment, if not performed in accordance with established practices for safe retrieval. All such measuring equipment would normally be pressure tested and checked as being in good condition prior to shipping to site, this being independently witnessed as compliant with agreed pressure test procedures. Every test fitting at the workplace will have its own unique ID (Tag. No.) and set of risks, therefore as well as utilising the relevant fitting retrieval procedure (either for online or offline servicing) a task risk assessment must be performed to identify all hazards (and required mitigations), specific to the retrieval/service location. For example, the device may be located at height and require scaffold erection for the service team (normally 2 people), or the fitting maybe located to the underside of the pipework (6 o’clock position), in which case, there may be risks of fitting/thread blockages from internal debris or spillage of fluids at device removal (when environmental precautions will be required), especially if it has not been serviced regularly. It is also not recommended to perform the 1st service of any such equipment on a live / online basis.
Before the start of any work, it is necessary to consult with the facility’s owner/client who should have maintained an access fittings register (with the vendor’s assistance), of the operating and service history of each Corrosion Monitoring fitting installed on the facility. Generally speaking, a good and frequent service history will allow regular safe in-service/live retrieval and maintenance activities to be performed, and these previous operations will have already identified the risks and should such information not be forthcoming, or is lacking in detail, then only offline/non-live retrieval should be performed (with hand tools), by persons competent to do so.
It is strongly recommended that reference should be made to the new Energy Institute (EI) Guidelines 1st Edition, for the management of access fittings for pressurised systems, published in August 2020.1
This document covers the lifecycle from the design, application, registration and safe handling of the different types of fittings through to abandonment/removal. The types of degradation which can be expected are defined, as well as methods of monitoring and the maintenance required. For more general guidance on effective corrosion control and prevention, the EI Guidance for corrosion management in oil and gas production and processing, 2nd edition should also be consulted.2
Primary pressure retention/process containment is of the utmost importance to all operators for reasons of personnel safety and good control of environmental and business risks. ST
1) https://publishing.energyinst.org/topics/asset-integrity/guidelines-
for-the-management-of-access-fittings-for-pressurised-systems
2) https://publishing.energyinst.org/topics/asset-integrity/corrosion/
guidance-for-corrosion-management-in-oil-and-gas-production-and-
processing
Question:
How should a conflict between the requirements, such as for film thickness, in a product data sheet, and the specification, be resolved? JS
Answer:
The fast and easy answer is that the detailed requirements (specification) will always take priority over the general. With this I mean, the specification is specific or unique for a project or a certain application, and this would supersede the more general content of a Product Data Sheet (PDS).
A typical PDS in the paint industry consists of:
- Description and recommended use
Recommendations on pre-treatment
Guidelines on application, methods, thinning, mixing, film thickness,
overcoating intervals etc.
Physical data for the product, drying time, solid content, colour(s),
Volatile Organic Compounds (VOC), specific gravity etc.
Some PDSs are more detailed than others ranging from one to up to ten pages. A well written PDS presents the framework for the product so that the optimum required product can be chosen and application process be decided upon.
The specification requirements should always be based within the parameters of the PDS framework. If there are deviations from this framework this indicates that the requirements may not be met by the product as it will be used for something which it was not designed to be used for, risking a poor result or at the very least some difficulties in application.
In other words, the specification should always be built within the parameters, directly or indirectly, outlined in the PDS and that is normally how the majority of specifications are developed. But a few do stray outside the framework, some for sound reasons and some for less so.
When data for a PDS is processed it is an integral part of product development. Before a product is released from the R&D lab it will have passed stringent testing and trials to make sure that it meets the product profile, both with regard to performance as a coating and with regard to application properties. The resulting data including the tolerance is recorded into the PDS. Normally these data and tolerances are on what can be considered the conservative or careful side.
Developing or building specifications can be for both a broad range of applications or be more for specific or customised use. The latter is often dealt with by a specialist who can evaluate the solution needed, and design the specification accordingly. For this category it is not uncommon to see deviations from the guiding data in the PDS.
Looking more specifically at deviation from the recommended film thickness as mentioned in the question, how can that be a sound specification? If we assume that the specifier has good insight into the application conditions, (for example they may know that the spraying is undertaken in an automated installation and the control of overthickness is strong) then here there is room for extending the thickness range upwards as the tolerance does not need to be able to absorb the extra thickness that can be expected from manual application.
Similarly, if drying times are considered, the specifier will know if the ventilation is very efficient and there is strong temperature control, meaning matters such as over coating intervals and dry to handle times may be shorter than indicated in the PDS. This can also be applied in reverse of course, if the conditions are poor the times in the specification may be increased.
Simply put there may be good reasons for deviating, but they should always be defendable if challenged and they should be expected to be very close to the values stated in the PDS. Deviations wildly off should not be accepted as they, in principle, constitute a set of questionable data in either document.
As specifications are normally the result of serious work, they should have priority over the product data sheet.
Niels Lund Jensen (Subject Matter Expert, Hempel A/S)
Fellows Corner
The latest article from ICorr Fellows who have made a significant contribution in the field of corrosion control is by Dr Sadegh Parvisi, Senior Principal Materials Engineer, McDermott, who describes the role of a Corrosion, Materials and Metallurgy Engineer. With some decades of professional engineering experience in engineering companies, operations and R&D, the author now shares this experience with fellow workers in ICorr.
The role of the Corrosion, Materials and Metallurgy Engineer in the integrity of Oil and Gas projects
This brief article is intended to highlight some strategic ideas to enhance the interaction of the Corrosion, Materials and Metallurgical (CMM) discipline with other fields, to improve the integrity of a project and enhance the reliability of the plants. It also aims to show the workflow, and identify the mechanism of interaction between all the disciplines engaged in the execution of a project.
Why CMM ?
Today’s corrosion engineers cannot produce meaningful and reliable outputs without having a proper relevant knowledge of Materials and Metallurgy. For instance, for a corrosion engineer it is not sufficient to only know the electrochemical processes well, but it would also be necessary for him/her to have a clear idea of the difference between PVC and CPVC. The CMM engineer should also understand, for example, the role of molybdenum on pitting and crevice corrosion of stainless steels, and to assess that even if this is not an issue, it is still vital to be aware of the huge cost impact of selecting between SS304 and SS316 steels in a LNG project. Hence this being considered as a single discipline which is named CMM.
Why is this subject important?
Consistency between the engineering project specification documents has a significant effect in the integrity of a project. This consistency cannot be achieved unless a dynamic interaction is built between the engineering disciplines. Quite often, it has been experienced that the final version
of the Piping and Instrumentation Diagram (P&ID) is not compatible with the material selection specification or report. Piping classes specifying the material of construction’s corrosion allowance divert from the
as-built P&IDs etc. The root cause of these discrepancies lies in the lack of
proper communication between relevant engineers, in particular in the CMM discipline.
Phases of Project
Any project can go through different phases before it reaches a ‘live’ production. For example:
- Conceptual
FEED
Detailed Engineering
Procurement
Fabrication & Inspection
Installation
Pre-commissioning
Commissioning
Trial Period
Operation
Maintenance
Mothballing
Extension/Revamping
Conceptual
Front End Engineering Design (FEED)
Detailed Engineering
Procurement
Fabrication & Inspection
Installation
Pre-commissioning
Commissioning
Trial Period
Operation
Maintenance
Mothballing
Extension/Revamping
This article intends to briefly address some of the key activities in each phase.
Conceptual Phase
The most fundamental phase in which preliminary materials selection and
corrosion control, based on Statement of Requirement (SOR), and in line
with process design parameters, are made.
- Innovation, discussion meetings with reputed vendors
Risk of employing new technologies should not be ignored
Optimisation and cost savings to be looked at carefully
Discussion and agreement with the client on any software to be utilised
before it gets too late
Site visit by CMM engineer can be very useful, if not crucial
FEED Phase
- The project statement of requirements should detail scope of work for
this discipline
Optimisation process, i.e. risk analysis and economic analysis should
be conducted
Detailed Engineering comprises
- FEED endorsement
Endorsement correction, HAZOP, licensor, etc. Corrosion control check-
ups, Approved changes
Full definition of materials (e.g. exact grade of titanium, etc., for example)
Basis of material selection to be consistent with FEED
Materials requisition and any technical deviation
Critical review of package material, request for compliance
Setting and finalising materials selection, as built
Material selection control manual
Procurement and Construction
- CMM to ensure compliance to specifications, and ensure that an exotic
material choice is not necessarily fit for service.
Vendors technical bid and Concession Request (CR) document
Upgrade requests from vendor should be assessed carefully
Participate in pre-production meeting
Materials selection change request during construction on CP, painting,
storage, etc.
Issuing close-out report for as built condition
No compromise to be made if it could affect integrity
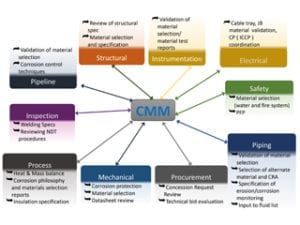
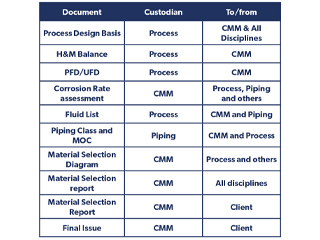
Table of typical workflow for issuing a corrosion control material selection table/report.
Pre-commissioning
The CMM engineers to be alert to some of the procedures in the manual, such as hydro testing, and that they are practiced carefully.
The Interaction mechanisms
The simple diagram shows the relationship between the CMM engineer and the other disciplines, and the table summarises the links between a process engineer and a piping engineer, as the main disciplines interacting with the CMM engineer in any oil and gas project, in order to have a robust and solid material selection philosophy. Similar tables can be produced to include other disciplines’ scope of activities, for instance in applying a corrosion mitigation technique by ICCP, the interaction between CMM, pipeline, civil and electrical engineers should be clearly defined.
Summary
It is important to note that a continuous and integrated input and engagement of the CMM engineer is vital throughout all stages of a project, since the integrity, reliability and safety of the plant depends significantly on the degradation mechanisms and materials selection strategy – the backbone of a CMM engineer’s expertise.
The Oil & Gas company should ensure active participation of the CMM engineer and appropriate interaction of them with other disciplines throughout the project.
It is recommended that
- The engineering director/company should ensure that there is a
continuous active participation, and appropriate interaction, of the
CMM engineer with other disciplines. It is also important that a proper
organisational chart is developed before the start of the project, and
the position and the work scope of the CMM engineer is defined for the
project, without any budget constraints for this important discipline.
The harmful misconceptions that “Nothing Can Be Done About
Corrosion!” are avoided
There is increased awareness of the large cost of corrosion and potential
savings that can be made
A sound Corrosion Management strategy should be set-up by changing
policies, regulations, standards, management practices and attitudes, to
increase corrosion mitigation savings
The education and training of staff in recognition of corrosion control
should be improved
Latest News, Midlands Branch
The branch has the following two online talks planned. Tuesday 20th October, starting at 12.00 Social Media for Professional Growth – Tips and Best Practices, Presenter – Dr Dawid Hanak, Senior Lecturer, Cranfield University, and Friday 27th November, Introduction to Mental Health – (MHFA England, Mental Health Aware Taster), Presenter – Russell Mott Lead Auditor & Trainer ATAS UK. Official Building Mental Health in Construction (BMH) toolbox talk and promoting both chat and poll questions in Zoom, again starting at 12.00. In the interim, the following links maybe useful to members for support and help on mental help; https://www.samaritans.org/, https://www.mind.org.uk/, https://mhfaengland.org/, https://atas-uk.com/, and specifically for younger members, https://www.studentminds.org.uk/
Full details can be found on the events page of the ICorr website.
Aberdeen Branch, Latest News
The branch has always been active in organising technical talks, annual conferences, industrial visits as well as collaborations with other institutes in various subjects that overlap with corrosion management. On the technical aspect, attending the monthly events gives members a chance to gain perspective on how others approach their work and to stay up to date with the current corrosion management tools. Apart from gaining knowledge, it is a perfect setting to get out of the rut of a normal workday and to network with other like-minded people. Also, you never know if you could be sitting next to a prospective employer, or client!
In addition to the technical aspects, the branch also supports, and helps, young engineers progress their careers, in line with ICorr values, and the latest addition to the branch committee, Mei Ling Cheah, is a perfect example of this.
Mei Ling Cheah began her higher education in 2008, at the University of Science, Malaysia gaining a BEng (Hons) in Materials Engineering, followed by Post-Graduate studies at The University of Manchester and the award of Master of Science (MSc) in Corrosion Control Engineering in 2013. She then started work immediately as a graduate Corrosion Engineer at CAN (Offshore) Ltd., Aberdeen, acting as the focal point for all integrity and corrosion matters for Bluewater’s FPSO. She was responsible for the delivery of RBI, pressure system inspection work scopes, fitness for service assessments, and technical reports outlining corrosion related issues, ensuring the constant update of risk-based assessments for all integrity related offshore facilities, and development of shutdown scenarios.
The following 3 year chapter in her life took her to Lloyd’s Register Aberdeen, working as a Corrosion Engineer on asset life extension assessments for SABIC petrochemical plant static equipment and piping, for sites at Teesside (UK), Mount Vernon (USA), Burkville (USA) and Petrokemya North & South (KSA). Other overseas related projects at Lloyd’s included RBI for the S-Chem (Saudi) petrochemical refinery, and a corrosion study for the ZADCO Sulphate Reducing Plant, where the scope of work included static equipment and piping criticality assessment and generating inspection plan for all static equipment, piping and PSV’s. As well as dealing with a number of UK offshore facilities, new experiences of pipeline corrosion management were gained, including cathodic protection reviews and developing corrosion control schemes. Most recently she joined the Aberdeen based IMRANDD Asset Integrity Management Firm, where she provides ongoing engineering support for Chrysaor’s offshore assets – Armada, Lomond and North Everest.
According to Mei Ling, her journey into the field of corrosion started with her fascination on what was known as the greatest technological prediction for half a century, Moore’s Law – cramming more transistors onto integrated circuit boards which lead to the age of computing and personal mobile devices. One of the challenges of keeping up with Moore’s Law was around the limitations with materials science, which decided her to study Materials Engineering at university. It was during this when they had a module on energy storage and battery systems that got her interested in the subject of electrochemistry. The process in a battery and corrosion of steel are chemically similar.
Mei Ling’s CV is typical of new corrosion engineers, in that experienced engineers in the branch are supporting her as she works toward Chartered status. In addition, Mei Ling is assisting Young ICorr nationally under chair, Caroline Allanach.
If you are a newly qualified engineer working the corrosion protection industry, then, just as with Mei Ling, your local branch can support you in your career development. A list of branch contacts can be found on the diary page of this magazine.
As usual, full details of future Aberdeen branch events can be found on the diary page of this magazine and on the ICorr Website, or by contacting, ICorrABZ@gmail.com. Copies of the majority of past branch presentations can be found at, https://www.icorr.org/aberdeen/, and a photo gallery for all Aberdeen events can also be found at, https://sites.google.com/site/icorrabz/event-gallery.
It should be noted that the planned ‘Industrial visit (Oceaneering), an Alternative/Interactive Industrial Event’, will now take place on 15thOctober 2020.