The cart is empty!
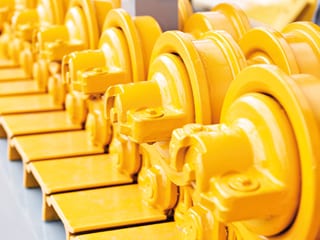
ISO 12944-7: Execution and Supervision of Paint Work
A Path to Ensure Quality Coating is Maintained
Continuing our series providing an overview of ISO 12944, in this article we discuss part 7 of the international standard. This takes us to the execution and supervision of paint work on steel structures in the workshop and on site. This does not include the preparation of surfaces (which is covered in 12944-4: Surface Preparation Standards). Nor does it apply to pre-treatment; application methods such as dipping, coil coating, and powder coating; or metallic coatings.
Here we outline the main points of the standard.
What is the scope of ISO 12944-7?
The standard deals with the execution and supervision of paint work, setting out:
- The preconditions for paint work to be executed
- The coating materials to be used
- Execution of paint work
- Supervision of paint work
- Reference areas
Preconditions
Companies (and their personnel) who are contracted to apply protective coatings to steel structures must be capable of doing the work required. Coating applicators should be suitably qualified (see Coating and Inspection Training).
Ideally, a quality plan should be prepared by the contractor, detailing methods to be used and quality levels to be achieved at each stage (ISO 9001/9002).
Though part 7 of ISO 12944 does not cover surface preparation, it does expect preparation to be made in line with part 4 of the standard, and the client must be informed if the condition of the surface differs from that described in the specification.
All relevant health and safety regulations must also be complied with.
Coating materials
Coating materials must be supplied ready to use, and in accordance with the coating method to be used. If any testing is needed, it must be specified.
Coating materials should be stored securely, at recommended temperatures (between 3 °C and 30 °C) or as otherwise stated by the manufacturer, and used within their shelf-life period.
Execution of paint work
This section of the standard deals with the following requirements:
- General requirements
Surfaces to be coated should be well lit and accessible, the manufacturer’s technical data observed, and coating materials should be verified as being acceptable to use (no skin formed, no irreversible settling, compatible with site conditions, etc.).
The standard also details acceptable dry-film thickness, uniformity of coating, and the need to pay particular attention to difficult to access surfaces (corners, edges, welds, connections, etc.).
It should also be noted that any defects in a coat must be repaired before the next coat is applied.
- Application conditions
Maximum protection can only be assured when the ambient conditions on site meet the requirements as laid out in the coating manufacturer’s technical data. Applicators should consider adverse conditions that may exist on site and take care that outside influences do not reduce the quality of paint work during application.
Applicators must also ensure that the coating is not applied when the steel temperature is less than 3 °C above the dew point (ISO 8502-4) and wet surfaces should only be coated with appropriate coating materials as outlined in the manufacturer’s technical data sheet.
- Application methods
Whichever application method is used, it should be evaluated to ensure that it provides the required protection. If it doesn’t, then the specification should be amended.
The coating application methods must be suitable for the coating materials to be applied, and may include:
- Brush application, particularly at corners, edges, angles, and difficult to access areas
- Roller application, though this is not usually recommended for anticorrosive primers
- Spray application, using the correct equipment to ensure that spray mist does not spread to surrounding areas
If other application methods are to be used, then the applicator must follow the manufacturer’s instructions.
Supervision of paint work
Paint work should be supervised at all stages of application, by qualified inspectors. Though the contractor can do this work themselves, it is advised that the client also provides supervision. If unfamiliar coating materials are used, the manufacturer should be consulted.
Supervision should be appropriate to the difficulty of work, local conditions, type of coating, expected life, and the project itself.
Supervisors should use a range of methods to assess the coating applied, including:
- Visual assessment
- Measuring instruments
- Test equipment and instrumentation
Reference areas
Reference areas should be used to establish a minimum standard of coating that is acceptable for protection of the structure. Any reference area established should be in a location that will receive typical corrosive stress associated with the structure, and application on this area should be carried out in the presence of representatives of all concerned parties.
The assessment of this coating should be made by methods that have been agreed and in line with international standards.
Summing up ISO 12944-7
In summary, ISO 12944-7 sets out the standards to which coatings applicators and supervisors must adhere in paint work that is designed to protect steel structures as covered by ISO 12944.
In short, this part of the standard seeks to ensure that paint work is executed and supervised to a minimum acceptable level – a level that ensures the coating system used maximises its potential to protect the structure being coated.
To ensure your painters and inspectors are fully up to date with ISO 12944 and all of its parts and are working to the latest industry standards and best practices, the Institute of Corrosion offers Coating and Inspection Training Courses presented by IMechE Argyll Ruane and Corrodere. For more information, contact us today.