The cart is empty!
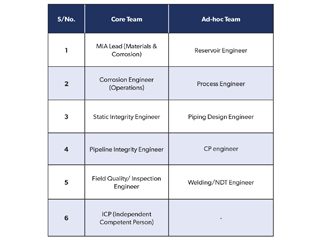
The problem with black powder deposits
The article by Al-Otaibi and Deshmukh (p23 Corrosion Management September/October 2020) provided important insights into how intractable black powder problems can be in hydrocarbon systems. It also reminded Chris Googan of a recent investigation into a black powder problem on a floating production storage and offloading (FPSO) installation. Here’s his anonymised summary of that case…
The Problem
The FPSO operated independently under contract to a major oil producer. In around 2014, a black powder problem became apparent in the gas processing system. The rogue solids periodically blocked strainers at the gas cooler inlets, necessitating shut-down of one of the twin gas processing trains. To avoid flaring the gas, the rate of oil production had to be reduced. Unless the FPSO operator could demonstrate that the black powder problem originated subsea or downhole, its contract required it to carry the costs of unblocking the strainers. It also incurred financial penalties arising from the cut-backs in oil production.
The FPSO Operator’s Investigation
The FPSO operator embarked on an investigation which, unfortunately, lacked both objectivity and any corrosion specialist support. Every time a strainer blocked, samples of the black powder were sent to a commercial laboratory where they underwent comprehensive, and not inexpensive, analysis: wet chemical, infra-red and x-ray spectroscopy and x-ray diffraction (XRD). The FPSO operator’s desire was that the results would identify corrosion of the oil major’s subsea infrastructure, or solids from the reservoir, as the source of the deposits.
In parallel investigations, the FPSO operator also embarked on an intensive, and likewise not inexpensive, campaign of non-destructive testing (NDT) of its own carbon steel pipework and equipment upstream of the strainers. Its ambition was to demonstrate that the topsides gas processing system was not corroding; so the black powder must be originating subsea.
Analytical Results
Chemical Components
Table 1 summarises a typical set of results from some of the many analyses of iron-based deposits collected from the strainers. It also records the presence of other (non-iron) salts found.
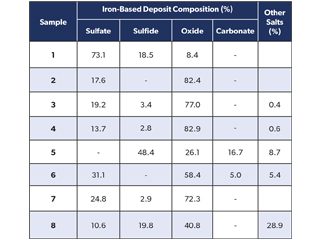
If the information in Table 1 were not perplexing enough, drilling down to the crystallographic nature of the compounds, as revealed by XRD, prompted even more head scratching. For example, the sulfate minerals observed included: szomolnokite, melanterite, jarosite and rozenite, which hardly ever appear in the corrosion literature. None is expected to form in anoxic hydrocarbon production environments. It seems most likely that the sulfate deposits were formed by the post-sampling oxidation of iron sulfide corrosion products when exposed to air. This process would be in addition to the known conversion of iron sulphide to iron oxides in the presence of atmospheric oxygen. (It seems that the need to maintain samples under an inert atmosphere was not fully appreciated by all involved). The relative absence of carbonate (siderite) from the majority of samples suggests that the corrosion products were formed when the H2S to CO2 ratio in the gas favoured the formation of sulphide ahead of carbonate.
The whole assessment, however, was complicated by the bewildering multiplicity of other iron-bearing compounds observed in the deposits. These included sulfides: pyrite, mackinawite, pyrrhotite, marcasite and greigite. There were also oxides and oxy-hydroxides: geothite, lepidocrocite, akageneite, wuesite, magnetite and maghemite. Thus, the vast majority of the deposits in the strainers was corrosion product; but the plethora of crystalline forms obscured the corrosion mechanisms; and provided no information at all on where the corrosion had occurred.
In addition to iron corrosion products, small amounts of halite (NaCl) were detected in some; but by no means all, of the debris samples.
Chasing Isotopes
The nucleus of the iron atom has 26 protons; but the number of neutrons combined with these protons can vary considerably. This means that there are 34 known isotopes of iron. Most are exceedingly rare, and of no interest for our purposes. They undergo radioactive decay to daughter isotopes of manganese, chromium or cobalt with half-lives ranging from nanoseconds to millions of years. On the other hand, there are three stable isotopes: 56Fe, 57Fe and 58Fe, with relative abundances of (approximately) 91.75%, 2.12% and 0.28% respectively. Another isotope, 54Fe, has a decay half-life of a mind-boggling 4.4×1020 years; so is stable as far as we are concerned. It makes up the remaining 5.85% of the iron atoms found in nature.
It has been known for some time that there are slight variations in the iron isotope balance for steels, depending on the ores from which they are derived. This prompted the FPSO operator to commission isotope analysis of samples of the debris, and of the process system steelwork. Its expectation was that this would demonstrate that black powder iron did not originate from the gas system steel. The ratios of 56Fe to 54Fe, and 57Fe to 58Fe were measured for nine steel samples and ten debris samples. To cut a long story short: the results were inconclusive. The span of measured isotope ratios observed in the deposits overlapped the span of ratios observed from the steel specimens. Beyond that, no conclusion as to origin could be drawn.
Inspection Results
As with all such exercises, the NDT campaign produced a glut of data, Unfortunately, however, there had never been a base-line wall thickness survey of the as-built pipework. The best that could be concluded, therefore, was that there had only been “marginal” metal loss compared with the nominal values. The FPSO operator interpreted this as supporting its case.
The Corrosion Assessment
After three years of heroic analytical endeavour, the FPSO operator decided it was time to involve a corrosion specialist in the investigation of this corrosion problem. I was commissioned to review the voluminous data and come up with a report that determined whether the operator or the oil major held the responsibility for the black powder problem.
My analysis took a lot less time than my client expected. Instead of delving into the minutiae of what was in the black powder, I focussed on what was not there. The missing ingredient was the salt (halite).
If, as hoped by the operator, the black powder originated subsea, then the only mechanism for it to have entered the gas production system was in aerosol droplets of produced water carried over with the gas from the slug catcher or gas-oil separators. Any such droplets would have to possess a much greater salt content than iron compound content. Incoming produced water analyses showed typical values of 13 000 mg/l chloride, less than 130 mg/l in total of suspended solids, and less than 1 mg/l of soluble iron. Thus, any droplets carried over would have had to contain hundreds, more likely thousands, of times as much halite as iron. Although there was evidence of isolated instances of produced water carry-over, analysis of the solids, and of the water separated from the gas system, simply failed to find anything like enough chloride to tie the iron to a subsea source.
The remaining plank of the FPSO operator’s case, namely that its gas piping was exhibiting only “marginal” corrosion was also soon jettisoned. Elementary calculations, based on the surface area of upstream off-gas pipe wall exposed, showed that even very low corrosion rates, well below those predicted by CO2 corrosion rate algorithms, would result in ample iron-based corrosion product to account for the observed quantities of black powder.
Lessons Learned
Numerous lessons emerged from this exercise. Some related to the original corrosion engineering of the FPSO’s gas processing facilities. For example, hindsight prompted reconsideration of the original design decision to omit the option of being able to inject vapour phase corrosion inhibitors into the system. It also forced a re-sizing and re-design of the strainers.
From the corrosion perspective, however, I offer two learnings. The first, unsurprisingly, is that it is a good idea to involve a corrosion specialist from the beginning of a corrosion investigation. The second, and perhaps more difficult to ensure, is always to keep an open mind when embarking on a corrosion failure analysis. Conducting the exercise with a pre-disposition to an intended outcome invites the risk of a biased and confused investigation.
Chris Googan, antiCORR