The cart is empty!
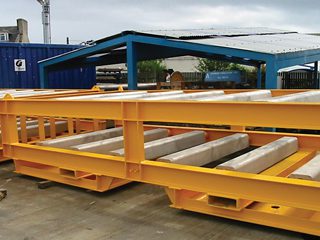
Aberdeen Branch – November Technical Meeting
The branch’s November technical meeting was held on 30th, to a large online audience of nearly 60 people including many international attendees. This was a joint meeting with IOM3 and MIS (Mining Institute of Scotland) with Dr Nigel Owen, Operations Manager of Aberdeen Foundries, presenting “Sacrificial Anodes: Material Specifications, Manufacturing and Anode Design for Effective Cathodic Protection Systems”.
The opening notes for the IOM3/MIS were given by Babs Oyeneyin of IOM3’s Energy Transition Board and retired Professor of Engineering at RGU who recently participated in COP26, Glasgow.
Aberdeen Foundries are one of the last remaining foundry operations in Scotland for non-ferrous castings and have been involved with the offshore energy and marine services industries for over 40 years, and is the last remaining working foundry in Aberdeen.
Nigel, who gave a most informative and heart-felt talk, has worked in the aluminium Industry for over 35 years after completing a B.Sc. in Metallurgical Engineering at Salford and subsequently a PhD in Materials at Imperial College before working in a variety of companies, including R&D of cast and rolled Aluminium products in Australia & USA, along with smelter waste recycling in New Zealand.
At the foundry he is responsible for all manufacturing, testing and technical specifications of marine and subsea sacrificial anode supplies. In addition, Nigel is a long-serving member and officer of the Aberdeen ICorr Committee.
The raw materials used for sacrificial anode manufacture are by necessity, high-purity based metals with very specific alloying requirements and final properties, in order to achieve the desired effective and long-lasting CP system operation.
The typical process for manufacturing anodes was presented, from a ‘metallurgical standpoint, the alloying, pouring, testing and finishing processes of various product types were then described in great detail.
The base materials, properties and costs of modern sacrificial alloys for cathodic protection purposes were detailed along with the conditions and applications for which they are generally used and the complexities of building moulds for casting operations. Nigel illustrated the importance of the Periodic Table and how alloying from different elements can be used to control/increase electro-negativity, and also the importance of the Galvanic Series showing how CP currents from sacrificial alloys are applied to counter corrosion currents.
Other key aspects covered included, the role of calcareous deposits and simultaneous reactions occurring at the anode and cathode. The talk also included a very interesting history of anode production and how this has developed into the tightly regulated industry of today, with recent concerns over contaminants like mercury (an effective addition) and also highlighted other bad contaminants like iron and copper that can affect anode performance.
In summary he concluded that:
- Aluminium alloys (of aluminium/zinc/indium) generally provide low-cost reliable anodes and account for 90% of offshore anode manufacture.
- Magnesium anodes remain particularly useful for onshore applications and for de-scaling operations.
- Zinc anodes are still well used for both brackish waters/harbours and offshore (buried applications).
Nigel emphasised the need for good quality control of raw materials sourcing and at all subsequent manufacture stages which can be of very complex geometries and which require very careful planning and preparation. Analysis of cast composition is normally performed together with electrochemical testing and optical emission spectrometry tests, to a combination of client purchase specifications and International Standards.
Good electrical continuity must be ensured between alloy material and surface profiled steel inserts and finally to the structure itself being protected by CP. Some materials like zinc naturally bond to inserts at casting temperatures while other rely on the mechanical key. Critically, all cathode areas to be protected must be identified at the design stage and then geometry of anode made to suit the area/life/current distribution to achieve Initial polarisation and required final design life.
CP system life extensions were also touched upon with illustrations of some recently shipped anode skids.
The presentation then moved on to discuss the design of Sacrificial Anode Cathodic Protection systems for a Marine Environment including prevailing standards, which involved selection of anode configuration, a detailed calculation process, combined with rules of thumb and practical experience to design an effective working CP system (that is capable of manufacture).
This very engaging presentation generated many questions from the audience that were expertly responded to by the author. The closing remarks for this well attended event were given by Hooman Takhtechian, the current Chair of Aberdeen Branch, who thanked all participants.
Slides of technical papers for branch events, along with their respective Q&A’s can be found at, ICorr Aberdeen Branch (google.com) under Local Technical Programme Aberdeen Branch – Institute of Corrosion (icorr.org). A library of event recordings may also be found at: ICorr Aberdeen – YouTube.
The branch has a very fully year ahead, running the Young Engineer Programme (YEP) alongside its normal busy technical programme for 2021-2022 Session. With Scottish Govt. guidance still discouraging large public events, initial meetings of 2022 will be held online and recordings published post-event.