Institute News
hope you are all looking forward to a ‘normal’ summer, certainly more and more meetings are being held in person, and physical exhibitions have restarted.
This in another bumper issue, with three technical articles, a lot of Institute news, together with the other usual columns The technical articles cover the application of a health and safety management approach to corrosion and degradation in the oil and gas industry, the defects which can occur with PFP systems over time, and a personal view of what to look for when choosing a consultant.
The “Ask the Expert” column as usual contains a coatings related and a CP related questions, and readers are reminded to send in their technical questions to be answered by our panel of experts.
Finally, I welcome comments from readers as to what topics they would like to see in future.
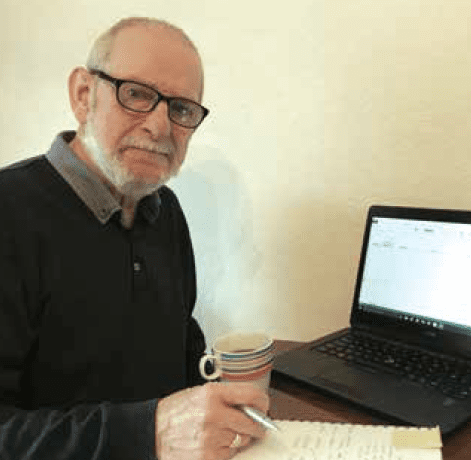
Brian Goldie, Consulting Editor
Email: brianpce@aol.com
Fellows Corner
This series of articles is intended to highlight industry-wide engineering experiences, practical opinions and guidance, to provide improved awareness for the wider public, and focussed advice for practicing technologists. The series is prepared by ICorr Fellows who have made significant contributions to the field of corrosion management. This month’s articles include, John Boran on measuring hardness in sour service, and Bob Crundwell on sacrificial anodes.
Think about where you measure hardness for sour service applications – weld root hardness.
Great care must be taken in the control of welding processes, as they may introduce significant metallurgical defects and detrimentally alter material performance in the sometimes ‘adverse’ conditions of Oil and Gas operations.
Hydrogen sulphide in oilfield fluids can cause sulphide stress cracking (SSC) in metals and alloys used in oil and gas production for pipelines, piping, pressure vessels, and other items that may come into contact with the sour fluids. SSC occurs if a material is not sour service rated at design, along with other cracking mechanisms, such as hydrogen induced cracking (HIC), step wise cracking (SWC) and stress-oriented hydrogen induced cracking (SOHIC), but this article will concentrate on SSC aspects.
Oilfield fluids are classified partly on the presence of acid gasses in the fluids. Carbon dioxide (CO2), when dominant, results in so-called sweet fluids where it is the major integrity threat in the presence of moisture. Trace amounts of hydrogen sulphide (H2S) are almost always present but when these exceed safe limits, the fluids are termed sour. Acid corrosion of metals and alloys in sour oilfield fluids result in the production of monatomic hydrogen, the hydrogen sulphide present acts as a catalyst to the hydrogen recombination reaction where diffused monatomic hydrogen recombines to form the diatomic hydrogen molecule.
Monatomic hydrogen can diffuse relatively easily into the metal lattice and embrittle the metallic matrix, subsequently causing cracking that can have catastrophic consequences for the integrity of the pressure containment envelope and result in leaks of the well fluids. The hydrogen molecule cannot diffuse into the metallic matrix to embrittle the metal.
The control and assessment of SSC is described in the International Standards Organisation (ISO) and National Association of Corrosion Engineers (NACE) standard ISO 15156 / MR 0175 – Petroleum and Natural Gas Industries – Materials for use in H2S – containing environments in oil and gas production, parts 1 – 3, henceforth referred to as ISO 15156.
One principal method of controlling SSC in low alloy carbon steels is to control the hardness of the base metal, weld, and heat affected zone (HAZ). It has been established over 45 years ago that carbon steels would not suffer SSC if the steel had a hardness less than 250 hardness Vickers (HV) or 22 hardness Rockwell scale C (HRC). Carbon steel can tolerate any partial pressure of H2S if the steel hardness is sufficiently low and the corrosion rate can be tolerated within the corrosion allowance.
The hardness of a metal is measured and controlled during weld procedure qualification and steel plate production to assure the suitability of the parent material and the weld for service in sour conditions, and ISO 15156 specifies how the hardness should be measured as discussed below.
ISO 15156 specifies a number of configurations for the hardness survey, including for butt welds, fillet welds, weld repairs and weld overlay.
The principal ISO 15156 configurations are for a Vickers hardness survey and a Rockwell hardness survey of a butt weld. The Rockwell test is generally easier to perform but the Vickers test has the advantage of an optical system that enables magnification of the material’s target area that allows the tester to pinpoint microelements on the surface for a more accurate and test.
It is important to note that the line of hardness test locations adjacent to the weld root, which is the region of the metal that faces the sour fluid, is 1.5 mm from the inside surface for Vickers hardness surveys and 3 mm for Rockwell hardness surveys. The tip of the root weld will be even further away from the line of the inside surface hardness survey.
It is well known that when welding, the quenching action of the base metal and any root weld backing such as the copper backing shoes or other conductive metallic materials, may result in more rapid weld root cooling rates, resulting in higher hardness’s in the vicinity of the tip of the weld root due to chilling effects.
In a recent sour service pipeline construction that suffered extensive SSC, hardness values of up to 350 HV were recorded at the tip of the weld root, despite passing the ISO 15156 weld procedure test hardness requirements and values of up to 290 HV on the inside surface of the parent pipe which also suffered SSC. It is clear that the hardness traverses specified in ISO 15516, are not adequate to detect all hardened zones in both weld roots and parent plate.
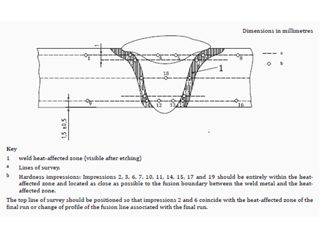
Figure 1: Butt weld survey method for Vickers Hardness measurements. From BS EN ISO 15156.
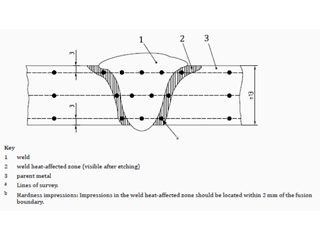
Figure 2: Butt weld survey method for Rockwell Hardness measurements. From BS EN ISO15156.
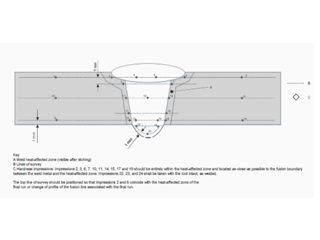
Figure 3: Hardness traverse to extreme tip of weld root.
Sacrificial anodes in the future
The largest consumption of sacrificial anodes is in the protection of energy related structures in seawater.
• Anode Alloys
Zinc was the initial choice for marine protection systems and is now mainly related to shipping applications. Zinc alloys do not perform well at elevated temperatures, loss of driving potential and formation of adherent corrosion products, with some reports of high consumption rates, means that they are not considered at temperatures much above ambient. Zinc anode alloys have the advantage that their current capacity is unaffected by operating current density and are therefore well suited to applications where an anticorrosion coating is present.
Aluminium alloys, based on the addition of 5% of zinc and 0.15% tin give a desirable driving potential but only very low efficiency unless solution heat treated after casting, when better capacity is achieved. Aluminium with 5% zinc, 0.02% indium and 0.2% silicon, is the commonest in general use and has found application at higher temperatures, driving potentials hold up but at the cost of a significant proportion of current capacity. Aluminium anode alloys experience a reduction in current capacity at reduced operating current density, this being significant at very low current density such as may be found with well-coated pipelines.
There are unlikely to be any fundamental advances in anode alloys in the foreseeable future. The use of zinc in offshore applications has been limited by opposition from environmental lobbies leading to banning of their use, and the issue of anode performance at elevated temperatures still has to be resolved. Testing has shown that anode performance is significantly reduced at elevated temperatures, but virtually all that testing has been under isothermal conditions, with little testing under heat transfer conditions, which is much more likely to be the actual service situation.
Future offshore developments are venturing into environments more aggressive than plain seawater. The particular issues surrounding Lake Maracaibo are well documented, less well known are those of the Black Sea, where the seabed is at a great depth and covered with centuries of organic matter. The suitability of existing materials and engineering practices will need to be confirmed and if necessary, adapted to such applications. Seawater having limited access to oxygen replenishment is another design challenge.
• Production of anodes
Most anodes are produced by casting the alloy onto an insert (usually a steel pipe or frame which supports the anode material and facilitates its attachment to the structure to be protected) in a permanent mould usually made of steel. Care must be taken in the casting process to take account of expansion of moulds and inserts, and contraction of anodes. Anode alloys are formulated for their electrochemical properties rather than their structural ones and this has led to problems of cracking of the anode material particularly with aluminium anodes. It is unlikely that production techniques will change significantly.
• Application engineering
The shape of an anode will contribute markedly to its performance in a cathodic protection system.
Fixed production platforms have a life expectancy of 30+ years and are usually only provided with coatings in the tidal areas. Anodes for these applications are generally up to 30cm in section and up to 300cm in length with a trapezoidal or circular cross section. Inserts are now invariably a tube with ends bent to facilitate attachment some 30 cm from the surface to be protected. Inserts are made from steels with a composition compatible with welding direct to the structure or via a doubler plate. A typical production platform may stand in 200 metres or more of water and have 1000 tonnes of anodes providing protection for the life of the structure. Care must be taken in the design to allow for current drain to assorted attachments, including but not limited to, production risers, export pipelines and piling. Failure to make due allowance for such current drain may compromise the protection system life, or in extreme cases prevent protection being achieved at all.
Probably the most interesting application engineering challenge is with anodes for submarine pipelines. These traditionally are segmented or semi cylindrical (half shell) bracelets which are a tight fit to the pipe. A taper may be cast into the leading and trailing edges of the anodes for smaller diameter pipelines. Larger diameter pipes often have a reinforced concrete weight coating several centimetres thick over the anticorrosion coating, and in this case the bracelets are made to a corresponding thickness in order to minimise any ‘step’ in the surface profile causing impact as the pipe passes over the stinger or boom on the lay-barge during laying.
Traditional engineering principles for the cathodic protection of pipelines are therefore a compromise between protection requirements and installation requirements. Future developments are likely to focus on the balance of this compromise in favour of the protection requirements ever recognising that the political, environmental and economic results of getting it wrong are usually disastrous.
• Current density for protection
In almost all cases the cathodic current density to initiate polarisation is substantially greater than that required to maintain it, exceptions being where there is a substantial water velocity past the structure or some other depolarising effect such as frequent storms. Protection system specifications are now recognising this and require an initial polarising current density and (much) lower maintenance current density. This will generate considerable rewards and impact substantially on design philosophy in the future. The selective use of coatings on parts of a fixed structure can lead to reduced anode requirements and greatly assist with the initial polarisation current issue. Any reduction in float-out weight can yield significant cost savings and will be relentlessly pursued although the risks make such progress slow.
The design of protection systems for coated structures requires an estimate of the levels of coating break down over the life of the structure to be made. The CP system is then designed to cater for this. In the future this combination of coatings and cathodic protection will merit increased attention, as even a low-grade coating with a relatively short life would address the initial polarisation current.
Offshore pipelines unlike platforms are almost invariably provided with a very heavy-duty anticorrosion coating, and reinforced concrete weight coatings on top are common. Pipeline coating breakdown levels used in CP design are typically 2.5% over the design life of the line or less. The future may well include superior anticorrosion coatings to those used at present. Cathodic protection designs could therefore have fewer unit anode installations, however distribution of protection along the length of the line will be a serious consideration, and anodes may be installed only at the ends of relatively short lines, or even fewer anodes added after the line has been laid in the case of longer lines.
• Quality control and quality assurance
The importance of effective QC & QA cannot be overstressed. Anode producers use instrumented analytical techniques such as infrared spectrophotometry, spark emission spectroscopy, atomic absorption spectroscopy, and plasma emission spectroscopy, to control alloy chemistry. When undertaken by properly trained technicians with access to traceable standards these methods provide rapid and reliable compositional data.
The use of steels with appropriate certification and welding to coded practices can give suitable assurance in respect of inserts.
The use of electrochemical testing as a quality control procedure has become mandatory on alloys, and a whole industry has grown up around such testing both by producing foundries and independent test houses. The testing procedures now used involve small samples of anode alloy often prepared in such a manner as to remove the entire ‘as cast’ surface. Great store is placed on the absolute values of current capacity per unit weight obtained.
In more than 40 years of practice in the use and manufacture of aluminium alloy sacrificial anodes, the author has never heard of a report of the failure of an anode whose chemical composition was within specified tolerance, to operate as expected. Thousands of electrochemical tests have been undertaken at great expense for no benefit whatsoever. It is to be hoped that the future will see realism and this waste of effort and resource consigned to history.
• System design
The calculation of the weight of anode alloy required to protect a structure is given by a simple calculation using area to be protected, current density, required life, and anode capacity. It is a brave designer that claims to know the true surface area of the structure. Dimensional tolerances of rolled sections of the sizes from which offshore structures are made are known quite accurately but it is surprising what bits get left out of the calculation let alone any correction for surface irregularity. Maintenance current density is variously quoted at figures between 0.140 A/m2 and 0.040 A/m2
for the same location, a factor of almost 4 times.
Anode current capacities for Al-Zn-In alloys are variously quoted between 2550 Ahrs/kg and 2750 Ahrs/kg. In general, the lower figure is on the basis of long term field tests, and the higher figure is on the basis of those short term lab tests mentioned previously.
Future design of sacrificial anode systems should focus on true surface areas and the current density required to polarise them, rather than squeezing the last drop of performance out of the anode alloy, and then justifying it with spurious testing.
Dr Bob Crundwell
Institute News
Aberdeen held its first YEP session online, on 27 January 2022, chaired by Hooman Takhtechian. There are 24 participants in the scheme selected from over 50 applicants meeting the YEP criteria. These come from a diverse range of disciplines, CP, CUI, FM, Materials, Process Engineering, Reliability / Maintenance, RBI, Subsea and Welding, thus bringing a wide cross-section of experience, cultural and networking opportunities for this year’s programme.
The chair congratulated all the successful candidates and encouraged them to also participate also in the branch technical meetings and ICorr events nationally, as far as possible. All YEP participants also have the opportunity to attend the branch ACF – Annual Corrosion Forum on Tuesday 30th August 2022, with this year’s theme being the “Role of materials selection, corrosion management and asset integrity/management in the Energy Transition and Net Zero Target industry sectors.
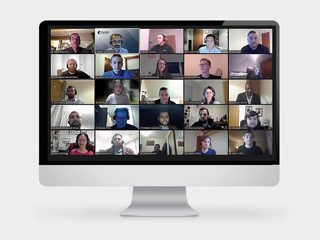
YEP Candidates and Course Organisers.
Steve Paterson, formerly Principal Technical Expert Upstream Materials for Shell Projects & Technology, got things off to an excellent start with a very comprehensive presentation covering corrosion control fundamentals and all aspects of corrosion management including, the impacts of corrosion, deterioration mechanisms, electrochemistry, materials, mitigation, modelling, passivity, kinetics and thermodynamics, along with several examples of corrosion failures. This generated many interesting questions and requests for further reading material.
The branch continued with its YEP on 8 March with an in-person meeting when Stephen Tate (ICorr Vice Chair) presented Integrity Management, and provided many experienced based examples of loss of integrity due to corrosion and erosion in, offshore fixed and floating facilities, oil and gas process systems, land-based structures and pipelines, stressing the need to ensure that all production facilities remain safe and legally compliant. A range of in-service failure specimens were made available to attendees, including removed flowline sections, choke valve sections and other piping specimens.
Subsea 7 have kindly loaned their Westhill training facilities for the YEP in-person events and the Aberdeen committee is extremely grateful to Brian Welsh – Subsea 7 Training Coordinator, for making this possible along with Amir Attarchi who managed all the catering on the night. David Mobbs has also been regularly supporting the Aberdeen YEP for us, which is very much appreciated.
YEP Session 1 presenter Steve Paterson -YEP Mentor and Case Study Leader.
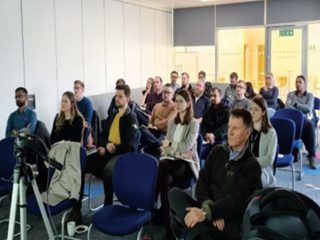
YEP Session 3 – Integrity Management with Stephen Tate at Subsea
7 Training Centre.
Institute News
The Journey described by Isaac Catran, Florentina Melo (ABRACO) and Lucia Fullalove (ICorr).
As ABRACO, the Brazilian Association of Corrosion, becomes nearer to getting ICATS, and the ICorr Paint Inspector Conversion course, we would like to take readers on the journey travelled so far.
It was in May 2018, during the INTERCORR (International Corrosion Congress) in São Paulo, Brazil, that ABRACO’s technical staff, Florentina (Flor) Melo and Isaac Catran met with Lucia Fullalove. Flor and Isaac were responsible for the training and qualification of corrosion professionals for ABRACO, and Lucia was in Brazil to deliver a ‘plenary talk’ on the “Application of Lean Principles in Corrosion Protection”, as a guest of INTERCORR.
As brief introduction, ABRACO is the Brazilian association which has represented the corrosion professionals in Brazil for over 50 years, it promotes and disseminates knowledge about corrosion and corrosion protection, and qualifies professionals in industrial paint application, industrial paint inspection, and cathodic protection. In addition to the above, ABRACO also delivers courses in the areas of pipeline protection and hot dip galvanising, for those professionals wanting to expand their knowledge.
Following the introductions, we (Lucia, Isaac and Flor) started to discuss the professional courses on corrosion protection from both our organisations, and we identified a great synergy between ourselves and the courses, and the possibility of closer co-operations between the organisations became our main target.
At ABRACO head office in Rio de Janeiro, the three of us made a presentation to the President of ABRACO at the time, Prof Laerce de Paula Nunes. The objective of the presentation was to propose a partnership which would allow for the promotion of ICorr in Brazil, as well as promoting ABRACO internationally. In addition, we wanted to get an agreement and recognition by ICorr for the paint inspectors trained and qualified in Brazil. Thus, providing the ABRACO paint inspectors with an internationally recognised qualification.
The collaboration project, “ICorr- ABRACO”, was immediately welcomed by the ABRACO President who under the advice of Lucia Fullalove, sent a message to the then President of ICorr, Sarah Vasey, introducing ABRACO and explaining the intention of creating a partnership between the two organisations. The positive response from ICorr was swift, and ‘we’ started to outline the co-operation project whilst still in May 2018.
Initially it appeared that the best way to progress would be with a direct comparison between the qualifications of both organisations in the areas of paint Inspection, paint application and cathodic protection. Therefore, a Memorandum of Understanding (MoU) between ABRACO and ICorr to show the intentions was created, the terms agreed, and finally signed by the then current Presidents of
the respective organisations in June 202,
Dr Olga Ferraz (ABRACO) and Dr Gareth Hinds (ICorr).
This partnership between ICorr and ABRACO was anticipated to go beyond the technical recognition, but also allow for further exposure and recognition of ICorr in Brazil where there is a huge potential for training development due to the country’s size, and the recognition by major players across several market sectors that corrosion protection is paramount, and of great benefit to asset owners.
On the other hand, ABRACO is well recognised in Brazil for the high standards of its qualification and quality of the training of corrosion professionals, therefore the partnership with ICorr will keep these high standards, and will give the Brazilian professionals the opportunity to also have international recognition.
As soon as the MoU was signed, we (Isaac, Flor and Lucia) started to work in earnest to focus on the equivalence for the certification of paint inspectors. From the very beginning the difference between the levels of qualifications was identified.
In Brazil, the paint inspectors’ certification is divided into 2 levels, whereas in the UK it is in 3 levels. Therefore, the first step was to see how the equivalence could be achieve, and the way forward was chosen to be to analyse and compare the course syllabuses. The idea was these would be assessed and a proposal made as to how this equivalence could be achieved, decided.
In March 2019, the contents of the ABRACO Paint Inspectors levels 1 and 2 courses were sent to be appraised and evaluated by ICorr. John Fletcher of ICorr was appointed to carry out this work, and in December 2019 following a GAP Analysis, he identified that the ABRACO Level 1 course content addressed most of the content of the ICorr Paint Inspectors levels 1 and 2, however there was a shortfall in the areas of H&S and the International Maritime Organisation ballast tank coating regulations. In the initial GAP Analysis, John also proposed options for the equivalence and a conversion module for this recognition has been proposed.
In March 2020, on the return to the UK, Lucia made a presentation to ICorr PDTC, which described the excitement and expectation created by the Brazilian paint inspectors for this ‘conversion’ from ABRACO to ICorr. Isaac, Flor and Lucia then carried out a mapping exercise between the Brazilian and the International Standards, so that ICorr could become acquainted with the Brazilian Standards and understand that the Brazilian paint inspector, although working under local standards, do have the level of work practice equivalent to their international counterparts.
The remaining differences were identified as relating to Brazilian legislation. Unlike in the UK, in Brazil, H&S activities on site are carried out by a Safety Medical professional, and by a Health & Safety qualified engineer. In addition, Brazilian technical standards are supported in law, therefore some of the activities of a corrosion protection professional must follow these. In Brazil, the standard even determines how the paint containers are stacked in storage.
The conversion module and exam questions have been written by Kevin Harold on behalf of ICorr, and the course translated, and reviewed. will be translated into Portuguese to be delivered in Brazil. The conversion course has now been uploaded to the IMechE Learning Management System. It is anticipated that once the Brazilian paint inspector takes the conversion module they will sit and online examination and the successful candidates will have their ABRACO L1 paint inspector certification, confirmed as an ICorr L2 paint inspector.
We would like to point out our certainty regarding the success of this project. This was one of the reasons Lucia was invited to deliver a presentation about the “ABRACO – ICorr” project at the Brazilian seminar of Anti- corrosive painting (SBPA) in Brazil in December 2019. The main attendees to the event were paint Inspectors and the project was well received by the audience.
The conversion module for L1 ABRACO Inspector was launched in Brazil on the 28th March, and the the next natural step is to get a similar process for the recognition of the L2 ABRACO paint inspectors as ICorr L3. Whilst a lot of training activities came to a halt as consequence of the COVID 19 pandemic, Isaac, Flor and Lucia started to work on the paint applicators course, and how to get the ICATS to Brazil.
ABRACO also wanted to have the ICATS in Brazil ‘online’ and Lucia has translated the modules and has been working with Isaac Catran to ensure the correct ‘ site jargon’ . as well as the Brazilian working practices are incorporated into the course. The translated ICATS modules have also been uploaded to the IMechE LMS system for ‘online’ access. This is now being tested , and although no definite date has been agreed for the launch, a trial is due to start soon.
As in the UK, in Brazil the training of paint applicators is carried out in parts. The ICorr Industrial Coating Applicator Scheme (ICATS) starts with a module on understanding the principles of corrosion protection, the importance of a good surface preparation before treatment, and the role of paint. And at this fudamental level the ICA is trained on the use of the paint brush and roller. It is ABRACO’s intention to follow thus training sequence. In 2020 this project was also introduced to Kevin Harold (MD of Correx) who was excited about the prospect, and proposed the setting up of the online Industrial Paint Applicators course (ICATS) in Portuguese to provide training to paint applicators in Brazil. The practical part of the course as well as the technical evaluation of the students (candidates) will be done by ABRACO.
The initial course (brush and roller) is currently being translated into Portuguese and the course contents adapted to the Brazilian legal requirements, environment, and work procedures.
For the practical assessment, Flor and Isaac had already developed a form to evaluate the students. which covers all the activities carried out by an industrial painter. This was shared with Kevin Harold to be assessed, and a modified version produced, which will be discussed and agreed by all (Kevin, Isaac and Lucia) as the new evaluation form for the ICATS Brazilian Industrial Paint Applicators.
In December 2020, there was another virtual SBPA (seminar on anticorrosion paints) meeting, which had 130 attendees, and at which Lucia was invited to, and delivered a presentation on the progress of the cooperation between ICorr and ABRACO. At this, there was great interest from both paint inspectors and paint applicators waiting to be able to take the ICATS conversion course.
The ICorr – ABRACO partnership is now being recognised and awaited by several sectors of the Brazilian Industry, such as Oil and Gas, steel producers, mining, petrochemicals, and others. There are still other areas for growth in Brazil where the strength of this partnership will be well received.
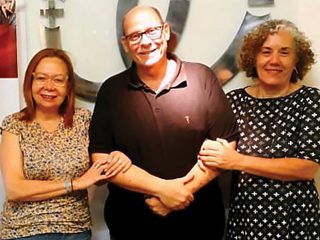
Above: Lucia, Isaac and Florentina
Institute News
At the recent AMPP 2022 Corrosion Conference and Exhibition, the first in-person event since the merger of NACE and SSPC, an event was held to celebrate our industry’s next generation of talented leaders.
On the evening of the EMERGing Leaders party, a number of different categories were presented during a ceremony at the historic Aztec Theatre near the San Antonio Riverwalk, to recognise the hard work and achievements of the younger professionals of the industry. Among them, our ICorr Young Engineer Programme (YEP) 2020 cohort winners, who were recognised for their achievements and presented with their winners’ certificates, by Bill Hedges (ICorr President) and Bob Chalker (AMPP CEO).
The winning team, mentored by Tasos Kostrivas (Mott MacDonald), was Team 4, made up of Ryan Cobbs (Civil Engineer at Mott MacDonald), Izabela Gajewska (Corrosion Engineer at Intertek), Vincent Lemoine (Welding Engineer at Saipem), Praveena Nanthakumaran (Mechanical Engineer at Worley Parsons) and Harry Wright (Corrosion Engineer at Element). The YEP 2020 case study, was a real-life corrosion problem and this particular case was based on an onshore glycol desalination plant failure. The prize for the winning team was a fully expensed trip to the AMPP 2022 Corrosion Conference and Expo.
In addition to the prize for the winning team, the YEP panel and mentors selected 2 participants to join the AMPP Leadership course (also held at the AMPP 2022 conference) for their performance during the programme. The winners for were James McGladdery (National Nuclear Laboratory) and Benjamin Lee (SGN).
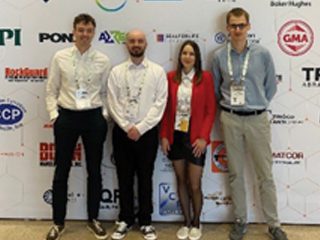
Above: Ryan Cobbs (Left), Harry Wright (Left Centre), Izabela Gajweska (Right Centre) and Vincent Lemoine (Right).
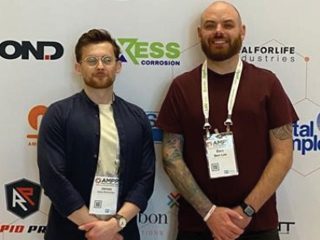
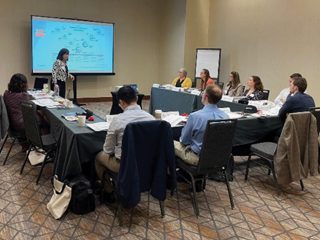
Above: James and Benjamin, and at a session of the Leadership course.
Young ICorr
To find out more contact Danny Burkle
(info.youngicorr@gmail.com)
Follow Young ICorr on LinkedIn to ensure you do not miss out on future events: