The cart is empty!
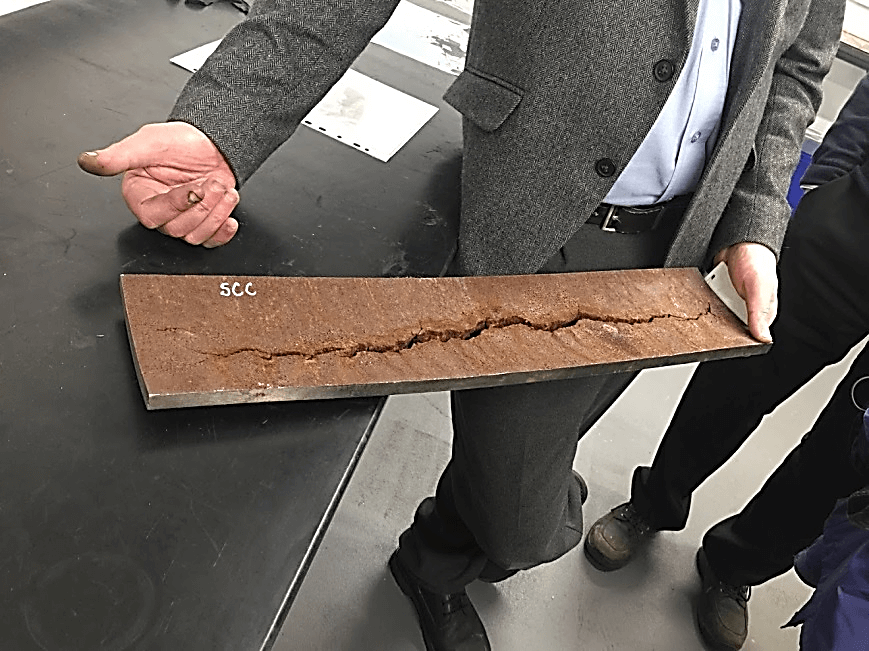
ISO 12944-9: Defining Laboratory Test Methods for Offshore and Related Structures
Improving the Quality of Protective Coating Systems in the CX Environment
In this article, we conclude our series examining ISO 12944 by describing ISO 12944-9, which was introduced to the standard in the 2017/18 revision to improve the quality of protective coating systems in extremely corrosive environments.
ISO 12944-9: A brief history
In the previous version of the standard, the corrosive category C5 (very high corrosivity) had been sub-divided into C5-I (industrial environment) and C5-M (marine environment).
In some cases, the descriptive ‘marine’ was taken to include offshore structures such as oil and gas rigs. However, the coating specifications for such offshore structures are specifically addressed in ISO 20340 (Performance requirements for protective paint systems for offshore and related structures). The differences between the two standards were marked, and created confusion and potential risk.
Specifically, there was an anomaly between the laboratory testing standards for coatings systems for offshore structures. While both ISO 12944 and ISO 20340 included a series of laboratory accelerated tests to verify the performance of candidate systems, the tests required under each standard were incompatible:
- For ISO 12944 C5-M the test regime was relatively benign (1,440 hour hot salt spray and condensation test).
- For ISO 20340, there was a much more onerous test. This included a week-long cyclic test of three days hot salt spray, one day in a deep freeze (-20 degrees Celsius), and three days in a QUVA accelerated weathering machine. This one-week cycle was repeated 25 times.
The repeated changes of hot/cold and wet/dry conditions place much more stress on a coating system compared to the static conditions of continuous salt spray. Consequently, only the very best performing paint systems would pass the cyclic test regime, whereas it would be relatively easy to get a ‘standard’ coating system to pass the ISO 12944 C5-M test.
The result?
Coatings were potentially being specified for severe offshore marine environments that weren’t fit for such purpose, and several product failures ensued under these conditions.
The ISO working group TC35/SC14 agreed that the C5-M corrosivity category should be abolished, with the C5 category that covers very high corrosivity limited to onshore structures. In addition, ISO 12944 would incorporate ISO 12340 as the new Part 9 category of CX (extreme corrosivity), covering offshore steelwork.
Coatings recommendations categories in the CX environment
And so to the coatings recommendations within ISO 12944-9, which are divided into the following three categories:
1. Atmospheric Exposure Areas
For general atmospheric exposure, it is expected that most coating systems will be based on zinc-rich primers. The very stringent pre-qualification accelerated cyclic test referred to above, with extremely low allowance for coating disbondment and corrosion from the scribe, means that non-zinc primers are unlikely (but not impossible) to pass.
The only exception to the very strict test parameters is for coatings that will be used on areas that may be subject to a high probability of mechanical impact and damage such as decks and lay-down areas. Here, zinc-rich coatings may fracture and disbond with the impact. Therefore, coating systems for such areas may utilize more traditional high-build coatings which have an allowance for slightly higher disbondment on the test schedule.
2. Immersed Areas (with cathodic protection)
These areas (classified as Im4 in ISO 12944-2) are tested for cathodic disbondment to ISO 15711 – Method A, plus a seawater immersion test to ISO 2812-2. They are not tested using the cyclic ageing test.
3. Splash/Tidal Zone Areas (with cathodic protection)
The splash zone is the portion of an offshore structure that suffers the highest level of corrosion stress. These areas will be subject to constant wet/dry cycling due to tidal movement and wave splashing with highly oxygenated sea water, and coupled with intense UV reflection off the water’s surface and the possibility of mechanical impact from flotsam or boat contact.
Splash zone areas have a significantly thicker coating specification and must pass the combined suite of laboratory tests of cyclic ageing plus immersion and cathodic disbondment tests.
‘Fingerprinting’ of coatings
It is mandatory that all coatings tested to the requirements of ISO 12944-9 are ‘fingerprinted’ by laboratory analysis.
This is done by taking paint samples from test batches and combusting them to ash. This is then analysed using Fourier Transform Infrared (FTIR) spectroscopy. This gives a detailed chemical profile of the coatings that can be used to compare against production batches to ensure that formulations are not changed post-test by the manufacturer. Routine batch checks are required to be undertaken during a project.
Thickness – a key difference in ISO 12944-9
ISO 12944-9 is extremely detailed with regards to surface preparation and quality control requirements that are commensurate with the need for the best possible coating practice to withstand the most corrosive environments. Hence, there are some differences between this part of the standard that covers CX environments and the rest of ISO 12944.
A key difference is that in Part 9, all specified coating thicknesses are minimum requirements. No dry film thickness readings are permitted below the specified level.
This is not the case for C1 to C5 specifications for dry film thickness, for which thickness values are nominal as defined by ISO 19840. This standard allows a small percentage (usually 10% or 20%) of dry film thickness readings to dip down below the nominal value, though no individual reading can be below 80% of the nominal value, and the overall average reading must be above the nominal value.
Piece-meal introduction of ISO 20340 into ISO 12944
The intention is to blend the CX specification requirements and testing schedules into ISO 12944 so that they are more aligned with other corrosivity categories as detailed in ISO 12944-5 and ISO 12944-6. However, in the 2018 iteration, this was not possible.
Therefore, as a first step, ISO 20340 was ‘bolted onto’ ISO 12944 as Part 9 of the standard. This bolt-on was added largely unchanged from the original, though with some tightening of the accelerated testing requirements that forced the use of zinc-based primers for general atmospheric exposure. Thus, there is some repetition from other parts of ISO 12944.
Further discussion of ISO 12944 is due to commence this summer, with a deadline of 2025 for the next issue of the standard – so watch this space!
The Institute of Corrosion Coating and Inspection Training Courses will help ensure your painters and inspectors work to the latest industry standards and benefit from new technology and innovative approaches. For more information, contact us today.
Other articles in our ISO 12944 series:
- ISO 12944-1: Durability Requirements
- ISO 12944-2: The Corrosive Environment
- Part 3: Design Considerations
- Part 4: Types of Surface and Surface Preparation Standards
- ISO 12944-5: Protective Paint Systems (Coating Thickness)
- ISO 12944-6: Laboratory Test Methods
- Part 7: Execution and Supervision of Paint Work
- Part 8: Development of Specifications for New Work and Maintenance