Ask the Expert
The question in this issue features the type of coating needed for the internal protection of an above ground storage tank.
Question:
What type of generic coating is required to protect the inside of a tank containing a liquid with pH ranging from 2-13, and operating at between 65-80 C? PS PS
Answer:
The range of possible conditions covered make this a fairly difficult question to answer. When responding to queries where all the information required has not been provided, the specifier will need to err on the side of caution and generally ends up in the proposal being over specified in an attempt to cover the unknowns, in this case, in the tank. Over-specified linings generally increase cost and complicate application requirements. It is also the case that the more expensive a system is, does not necessarily make it a more suitable solution, as every lining has its own strengths and weaknesses.
The first question should always be what is the existing coating solution? If this is maintenance, what was previously used and was it successful? If it failed, do we know how and why?
Details of the chemicals involved, and their concentrations are required before a specification can be given, including durations in the different states (acidic and alkaline). Is the temperature a genuine continuous service temperature or are there short-term spikes to these maximums, or is the higher a design temperature (if achieved the lining is the least of the operator’s worries) and the lower the actual service temperature? What is the tank substrate, steel or concrete? All these will affect the lining selection.
With the wide range of pH quoted, this could be a neutralisation tank or pit and this type of aggressive service conditions often require a high build reinforced vinyl ester system. These systems are made up of a number of layers, including a trowel applied screed and glass fibre reinforcement mat to create a robust chemical resistant system, but the system cannot be confirmed until full details are known.
Matthew Fletcher, International Paint Ltd
Industry News
This series of articles is intended to highlight industry wide engineering experiences, practical opinions, guidance, and focused advice to practising technologists. The series is written by experts who have made significant contributions to the field of corrosion management. The article in this issue features a contribution from Alan Denney, who discusses weld corrosion problems.
Preferential corrosion of welds – an introduction
Welding of a metal results in a range of different metallurgical structures in the heat affected zone (HAZ); that part of the parent material adjacent to the weld which has not been melted and fused into the weld itself. Where a filler metal is used in welding (in the form of a welding rod or wire), such as in manual metal arc welding (MMAW), metal inert gas/metal active gas welding (MIG/MAG welding), flux cored arc welding (FCAW) or submerged arc welding (SAW) the weld metal will have an inherently different chemical analysis to the parent metal. This is because the parent metal has a wrought structure, with properties coming from mechanical working and heat treatment whereas the weld metal has a cast structure which achieves its strength mainly due to its additions of alloying elements.
When a weldment is exposed to an electrolyte (a conductive corrosive medium) one part of the weldment may corrode preferentially over another part, resulting in the weld being preferentially attacked. In real life situations the preferential attack may be in another discrete area such as the heat affected zone or even some distinct part of the heat affected zone which has a particular metallurgical structure. Where preferential attack occurs it can be rapid, difficult to detect by conventional monitoring methods, and potentially dangerous.
Galvanic corrosion
The corrosion may be caused or enhanced by galvanic action, galvanic corrosion being the electrochemical process where there is a different natural electrical potential between two metals or two different metallurgical structures, resulting in one part of the weldment being the cathode and another the anode of a corrosion cell. It is the anodic area which corrodes, but the cathodic reaction drives the corrosion process. The potential difference may be relatively small but if the parent metal is the cathode and the weld is the anode then there is a large cathodic area to drive the corrosion reactions and rapid weld metal dissolution can result.
Galvanic corrosion is a clear risk where a weld is made between significantly different metals, such as in welds between carbon-manganese steels and duplex stainless steel when exposed to a corrosive environment, but problems can also occur where there is less obvious difference in materials.
Preferential corrosion of welds in seawater lines
One well-known example of preferential corrosion is internal corrosion of pipelines transporting seawater. These are commonly used for water injection into oil wells. The corrosion occurs within the welds at the pipe joints made of carbon-manganese steel welded using welding consumables which would be considered as ‘matching’ in properties (albeit there are the wrought/cast structural differences mentioned above). One means of avoiding the corrosion is to reduce the oxygen level of the seawater to low levels of parts per million (which is extremely challenging) and/or to control the as-deposited composition of the weld metal to increase its cathodic potential thus minimising galvanic potential differences. This involves careful selection of the welding consumables, based on consideration of composition, but also the results of sophisticated corrosion testing of trial welds. A further solution is to install the line with a continuous internal plastic liner in the pipe, thus preventing seawater contact with the pipe or welds surfaces.
Preferential attack in welds in stainless steel
Stainless steels are cathodic when in combination with other metals such as carbon steels or aluminium alloys and hence unaffected by corrosion when in combination in a corrosive environment, but they are not immune to preferential corrosion effects. One example is when austenitic stainless steels are welded (to themselves), and exposed in a corrosive environment. They may then suffer from what is commonly termed ‘weld decay’. If this occurs in current times it is a consequence of an error in not selecting a modern resistant grade of stainless steel.
Stainless steels owe their corrosion resistance to a layer of chromium oxide a few microns thick which forms a passive protection layer. If breached and in a corrosive environment this layer does not repair itself and localised corrosion will occur. In their original form the austenitic stainless steels (the familiar 300 series of stainless steels) contained carbon up at levels of up to 0.08%. This carbon content and its distribution in the matrix becomes significant in welding the steel when ‘sensitisation’ can occur.
Sensitisation is due to the carbon preferentially combining with the all-important chromium to form chromium carbide which forms along the grain boundaries. This depletes the areas adjacent to the grain boundary of the chromium and this is no longer available to form the passive protection layer. In a corrosive environment, local corrosion cells will form, corrosion occurs around the grains and they can detach from the surface (Figure 3). This situation occurs within a range of temperatures experienced in the heat affected zone of the weldment.
This problem is readily avoided by selecting the low carbon stainless steels denoted by the L designation (e.g. 304L or 316L) which use modern steelmaking techniques to achieve carbon contents of less than 0.03%. There is a further material selection option which is to use the so-called stabilised grades of stainless steel, such as type 347, in which the carbon is ‘stabilised’ (i.e. chemically combined) by the addition of niobium.
In a component already fabricated from the higher carbon (unstabilised) grades it can be prevented by suitable post weld heat treatment.
In conclusion, there are numerous other examples of preferential corrosion of welds and this topic is well covered in web articles and technical papers which the reader can discover by performing online searches.
Welcome to the world of the welding engineer who has to select the welding and heat treatment parameters based on the materials and their application.
Alan Denney, Consultant.
References
1. Corrosion of welded components in marine environments (April 2003). Stuart Bond, TWI Ltd. Prevention and Management of Marine Corrosion, London, 2-3 April 2003. Lloyds List Events. (available on the TWI website https://www.twi-global.com/technical-knowledge/published-papers/)
2. Good welding practices for stainless steel. Presentation by Glenn Allen, TWI Ltd. Available to members on the TWI website.
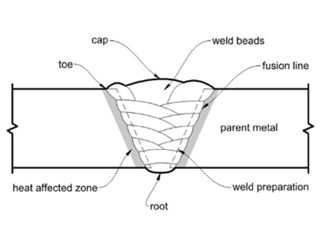
Figure 1: An example fusion weld showing the heat affected zone.
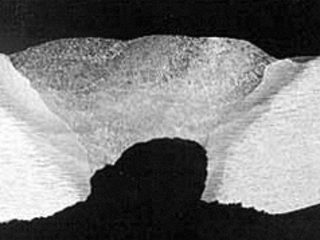
Figure 2: Preferential weld metal corrosion in carbon steel (copyright TWI Ltd reproduced with permission). Source: Reference 1.
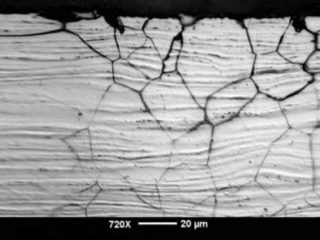
Figure 3: (copyright TWI Ltd reproduced with permission).
Source: Reference 2.
Industry News
Ten leading paint manufacturers in the Middle East, Akzo Nobel, Altakamol, Asian Paints, Axalta, Caparol Paints, Hempel, Jotun, National Paints, PPG and RAR Holding, have agreed to launch the Middle East Paints & Coatings Association (MEPCA), with the backing and support from the World Coatings Council and
Vincentz Network.
Abukaker Sheibani, Group CEO, Sheibini Group/ Altakamol International commented “At long last, we have a joint platform for our industry in the region. We will collaborate for the benefit of all members and the coatings sector in general. Over time, we strive to grow our membership to include all relevant paints and coatings manufacturers in the Middle East”, and who was elected Chairman at the launch meeting held in Dubai on September 13th . He will be supported by Vice Chairman Martin Rosocha, Managing Director ME & Africa, Caparol Paints, and Treasurer Jasbir Gill, Regional Director Middle East and Africa, Akzo Nobel.
According to the report, the formation of MEPCA, made up of the most senior leaders in each company, was prepared and driven by the World Coatings Council (WCC) and Vincentz Network. President, Tom Bowtell, and global business director coatings, Jürgen Nowak, had held exploratory meetings in February, which were followed by a formal joint meeting with the group of companies in May and the launch meeting in September. Both
Vincentz Network as a company and Tom Bowtell as WCC President have been made Honorary Members of MEPCA.
The founding members of the new Middle East Paint and Coatings Association, after signing the launch document in Dubai on September 13. From left to right, Joseph Eapen (inset) (Asian Paints), Franck Derouen (Axalta), Jasbir Gill (Akzo Nobel), Martin Rosocha (Caparol Paints), Laurence Brown (Hempel), Tom Bowtell (World Coatings Council), Abubaker Sheibani (Al Takamol International), Jürgen Nowak (Vincentz Network), Anthony Reaidy (RAR Holding), Olga Kolevatova (PPG), Samer Sayegh (National Paints) and Esben Hersve (Jotun).
Uncategorized
Future climate policy looks to hydrogen and its synthesis products with great importance, but how could the demand for hydrogen develop globally? According to a report, a new meta-study coordinated by Fraunhofer ISI addresses this question and re-evaluates more than 40 energy system and hydrogen scenarios within the HyPat research project. The study provides statements on the range of possible future developments of hydrogen demand, globally, in the EU, and China until 2050, and differentiates between various demand sectors. The focus is on scenarios with ambitious greenhouse gas reduction targets.
Hydrogen and its synthesis products are globally regarded as important future energy sources that could be used in many different sectors. For example, there is an ongoing controversial debate about the role hydrogen will play in transport in the future, and specifically its use for passenger cars and trucks. There are also potential applications with demand for hydrogen in other sectors, such as industry and buildings.
As far as specific applications are concerned, the biggest demand for hydrogen is expected in the transport sector, according to the study, in both absolute terms and relative to total energy demand. The meta-study calculated an average hydrogen share of 28% for the EU’s transport sector in 2050 – based on the total energy demand of the sector – compared to 14% for China and 16% worldwide. However, transport is also the sector with the widest range, and therefore the highest degree of uncertainty concerning future hydrogen use. H2 synthesis products will be used in areas such as international shipping and aviation, but the possible future use of hydrogen is less clear in other large fields
of application such as passenger cars and trucks.
Prof. Martin Wietschel, who coordinates the research work of the HyPat consortium, estimates the future global significance of hydrogen as follows: “Our evaluations underscore that hydrogen will play an important role in future global climate policy – but will not be the dominant final energy carrier of the future. In order to reduce greenhouse gas emissions globally, measures to save energy and direct electrification based on renewable power, for example, in heat pumps, electric vehicles or heating networks, are seen as the most important levers. On the other hand, hydrogen does play a relevant role in specific applications where other technologies are either technically or economically not feasible.”
Latest News, Uncategorized
ICorr Microbiologically Influenced Corrosion (MIC) Training Course
Plan for 2023
The Institute of Corrosion (ICorr) is pleased to announce the plan for the MIC training course for 2023. Both the Awareness and Certified MIC Technologist proficiency levels are offered, at ICorr headquarter, twice next year as follows;
April 2023:
- Awareness (one day course) on the 12 April 2023
- Certified MIC Technologist (5-day course) from the 17 April to the 21 April 2023
October 2023:
- Awareness (one day course) on the 4 October 2023
- Certified MIC Technologist (5-day course) from the 23 October 2023 to the 27 October 2023.
An MIC Technologist attendance certificate is available for attending the 4-day course without taking the certification exam.
Please contact admin@icorr.org for registration.
There are a number of hotels within a walking distance to ICorr offices including Ibis and Park Inn. It is recommended to make provisional booking as early as possible to secure a competitive rate.
We look forward to seeing you.
The Institute of Corrosion