Industry News
Gecko Robotics, a leader in using advanced robotics and enterprise software to help ensure the availability, reliability, and sustainability of critical infrastructure, has announced a three-year collaboration with Siemens Energy’s European Field Service organisation to market and perform advanced ultrasonic robotic inspection services across Europe.
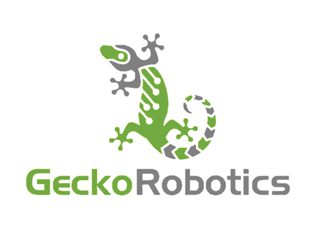
According to the company, these advanced robotic inspections are poised to strengthen critical infrastructure and transform how installed equipment is inspected and maintained. Together, the two companies will develop new technologies and services to better serve customers across several industries, including pulp & paper, power generation (conventional and renewable), and oil & gas. Siemens Energy’s European Field Service organisation and Gecko Robotics have already completed inspections in Europe, in Poland (pulp/paper), Belgium (waste to energy), the Netherlands (food processing), and the UK (power generation). In support of the collaboration, Siemens Energy has established a new Product Competence Centre in the Netherlands, with expansion plans underway.
Gecko Robotics’ robots are remote controlled and equipped with ultrasonic transducers, localisation sensors, lasers, and HD cameras. They climb vertically and horizontally, adhering magnetically to an extensive range of equipment types to scan for changes in thickness, cracks, corrosion, blistering, and other forms of degradation. The robots also include localisation technology to pinpoint exact locations on an asset, allowing for truly accurate inspections that enable inspectors to examine corrosion trends over time, predict when failures will occur, and estimate when repairs will be necessary. Data captured by Gecko’s robots and its software platform can then produce a validated report within 24 hours, allowing inspectors to quickly assess and make informed decisions about ongoing maintenance or repairs. This process and quick turnaround also enable inspectors to reduce asset downtime and lost production while ensuring critical repairs are conducted with high confidence, concluded the company.
Institute News
Sadly, Lee Wilson, who was the chair of the re-formed branch, passed away suddenly in October. Lee was passionate about the Industry, and in particular the Institute of Corrosion, and was the driving force behind the regeneration of the ICorr NE Branch. He used all his contacts and managed to put a technical programme together starting with a joint presentation at the Institute of Mining and Mechanical Engineering in Newcastle, to be given by Britt Gavaert of ACOTEC.
Lee had a wide range of experience with coating inspection techniques and methods. This experience began when he was a blaster and coating applicator in the NE, before moving into supervision and inspection. He was keen to pass on his experience to others in the protective coatings industry, and has published two editions of a book for inspectors – The Paint Inspector’s Field Guide. He is recognised as an expert on fabric maintenance and corrosion control in the Oil and Gas industry, and recently was becoming involved in the offshore wind industry. He had just finished another book aimed at this industry, “The guide to corrosion protection of offshore wind turbine towers”, but sadly his untimely death occurred before he could see this published.
The Institute of Corrosion would like to express their condolences to Lee’s family, friends, and colleagues around the world.
The new chair of the branch will be Matt Fletcher, International Paint Ltd.
Institute News
The October presentation was given by Anthony Setiadi, Wood Thilsted Partners, on the ongoing challenges in corrosion protection of foundations for offshore wind technologies. This was a well-attended hybrid event, joint with LMS had approximately 60 attendees, split 2/3rds in person and 1/3rd online.
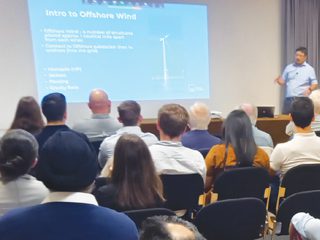
Anthony Setiadi
The offshore wind industry growth is rapidly accelerating as the world is pushing towards renewable energy sources. Wind turbines often need to be installed on foundations which are in aggressive environments that are prone to corrosion if not protected and / or designed with corrosion in mind. There are various offshore wind foundation types, such as, monopiles, jackets, tetrabases, gravity bases and floating structures, often grouped in vast arrays for reasons of economy.
The presentation was primarily focused on monopile foundations and the design considerations that would need to be taken onboard. Monopiles have both internal and external surfaces needing protection. Coating requirements and different cathodic protection systems (i.e. galvanic and ICCP) were discussed for the internal and external of the MP. Anthony stressed that there were challenges regarding positioning of the CP system and installation concerns which needed to be considered along with any simultaneous operations that need to happen offshore during the installation phases, e.g. piling operations that limit placement of anodes on the primary structure.
The main consideration is how the structure would behave with and without corrosion protection, especially the fatigue critical components such as the girth welds. The other consideration would be the site condition which will vary across the different wind farm locations and in some cases, a clustering strategy for varying sets of marine and geological conditions may be needed.
In addition, a corrosion protection plan must be developed and agreed well in advance, which then needs to be followed through to completion, including input to operation and maintenance strategies to ensure that the structure integrity is not compromised throughout design life.
This very interesting presentation was followed by a comprehensive Q&A session. Anthony was then presented with an ICorr pen by Paul Brooks.
The November meeting had unfortunately to be held online only, due to the TFL tube strike. The presentation was given by Roland Anderson of Axess-Corrosion Inc., about new solutions to problems related to intrusive corrosion monitoring systems, and learn about, and evaluate, innovations relating to the safety of these monitoring devices. Roland Anderson has over 20 years’ experience in the Oil & Gas industry focused on internal corrosion monitoring programmes globally, and has developed and established businesses in many locations including the UK, Middle East, Australia, China, and the USA.
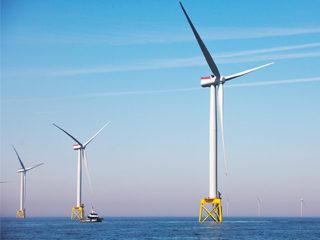
Typical offshore wind monopile foundation (Wood Thilsted).
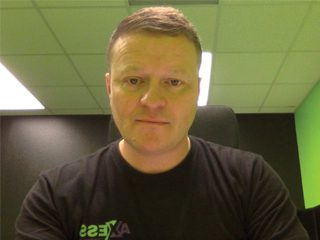
Roland Anderson
Roland first looked at some examples of incidents ranging in severity from loss of containment to fatality, in particular a fatality in 2012 which sent shockwaves throughout the industry, and the many operators who had not serviced access systems under line pressure due to risk management concerns, and which was highlighted in an ‘Learning from Incidents Action Alert’ published by Shell in 2012.
Corrosion monitoring devices are designed to be changed out under live process pressure, negating the need for the process to be shutdown, utilising an access system and specialised retrieval equipment. The access systems can be either mechanical or hydraulic, and the systems are also used for the installation of erosion, scale, hydrogen monitoring devices, and chemical injection and sampling hardware.
There was a trend, sparked by the 2012 incident, and fueled by technology companies, to move towards non-intrusive monitors. His company supply, install, and data manage these systems, which provide good value, but when talking about corrosion monitoring, it’s often actually chemical performance monitoring, and this cannot achieve the level of insights required to optimise chemical performance with ultrasonics. Intrusive and non-intrusive sensors are complementary, and the trend towards non-intrusive is driven by the need to convert inspection to monitoring, opposed to replacing one system with another.
Corrosion coupons, the backbone of traditional monitoring systems, at low to moderate corrosion rates, can detect the performance of chemical injection programmes 2 years before inspections. Electrical Resistance (ER) probes are complementary to coupons, and are used to obtain very accurate data over short periods of time to enable chemical injection optimisation. ER probes can also be designed for erosion monitoring.
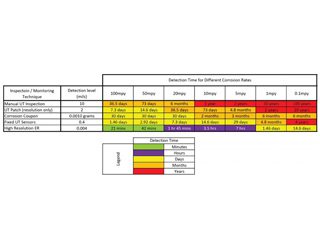
This table provides examples of the time it takes to detect metal loss.
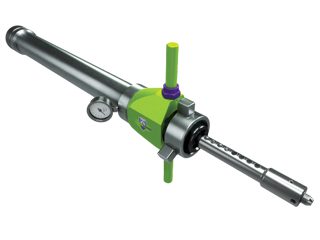
Institute News
Thank you. It feels appropriate that I start my final article as president with a thank you to all of you as ICorr members. In my two years as president, I have seen what all past presidents say – that the strength of ICorr is its people. Leaders can help shape direction but it is our members that make things happen, and so many of you give your time and resources that prove that. In todays very busy world where so many things compete for our time, I have not ceased to be amazed by the generosity of so many
of you.
As I said in my first president writes article two years ago, it is an honour to be the ICorr president, and my time in the role has made me more conscious of that. Our Institute is a phenomenal organisation where we work hard to fulfil our mission to “Advance Science and Engineering in the Prevention of Corrosion”.
Over the last few years ,we have had our challenges – most notably the Covid pandemic and the global economic downturn. Despite these we have continued to perform well and found new ways of working to mitigate them. I would point to the use of digital tools such as virtual meetings and social media that have helped us.
At our recent Annual General Meeting, which was held virtually, we had very positive reports. Our membership is growing, our training courses are in high demand and our finances are in a very strong place. If you were not able to attend the meeting, I’d recommend looking at the annual report or presentation that can be found in the members area of the ICorr website. It is very encouraging.
Thus, I feel I’m handing over the Institute in good shape and, more importantly, into the excellent hands of Stephen Tate, who was unanimously voted in as our new president at the AGM. Stephen will bring fresh ideas and initiatives to us and I know you will all support him as you have me. Congratulations Stephen, I know you will enjoy the role as much as I have.
Before I close, I’d like to express my gratitude to my fellow trustees and council members who work really hard and have given me so much support, guidance and wise council. My presidency has been much the better for that – thank you.
As ever, your ideas and feedback are important to us so please continue to let Stephen know what you like and where you think we can improve, using the president@icorr.org email. More importantly, if you’re not actively engaged and would like to be please let us know – we have lots of opportunities!
Kindest Regards,
Bill Hedges
Institute of Corrosion: Immediate Past President
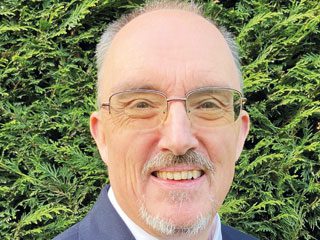