The cart is empty!
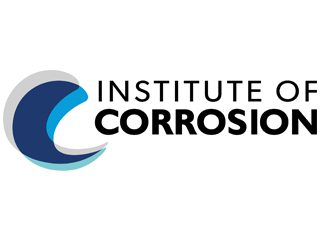
How the Institute of Corrosion operates – the Surface Treatment Governing Board and Cathodic Protection Governing Board
The Surface Treatment Governing Board (STGB) is one of two sub-committees that provide support and advice to the Professional Development and Training Committee (PDTC). The other sub-committee is the Cathodic Protection Governing Board (CPGB). STGB is specifically responsible for the Surface Treatment Training Courses, which include all the Coating Inspection courses and their content.
The main responsibility of STGB is to oversee the Requirements Documents (REQ-DOCs) for each of the Surface Treatment schemes, and which describe the training schemes for the Coating Inspection courses. There are currently three main REQ-DOCs for Surface Treatment Courses, one for courses that are normally delivered in the classroom and a separate REQ-DOC for the courses that are delivered on-line. The new Passive Fire Protection Coating Inspector Scheme has a separate REQ-DOC, as there are significant differences in this scheme, in that the Level 3 Inspectors are required to satisfy a Peer Review once they have successfully completed the examination stage. Currently, this is unique to the new PFP Coating Inspector scheme, and it also reflects that some of the training can be delivered on-line as well as in the classroom.
These REQ-DOCs contain all the guidance for operating the courses and the associated examinations and certification, and detail the syllabus for the specific courses. For example, the Protective Coating Inspector scheme, previous known as the Painting Inspector scheme, has three levels, Level 1, Level 2, and Level 3. The REQ-DOC describes the eligibility of potential candidates for the different courses and details the topics that are covered by the three levels. The Protective Coating Inspector scheme also includes the specific training required for Insulation Coating Inspectors (Level 2), Pipeline Coating Inspectors (Level 2) and Hot
Dip Galvanising Coating Inspectors (Level 2).
STGB keep the REQ-DOCs under review so that they can be updated and improved on a regular basis. Once a REQ-DOC has been edited and agreed by STGB, it is submitted to PDTC with a recommendation that the updated version of the REQ-DOC be approved
and published.
STGB is also responsible for reviewing any new Surface Treatment courses that are submitted to ICorr through PDTC, who refer such courses to STGB where a reviewer with the relevant experience is identified. The review is used to make a recommendation to PDTC with regard to the content and quality of the new course and, where appropriate, its conformance with an existing REC-DOC.
In addition to the REQ-DOCs, STGB review applications from the course providers for candidates who wish to become Course Tutors for the classroom courses, or Course Assessors for the on-line courses, and make recommendations to PDTC regarding approval or rejection of these applications. These applications mainly come from the overseas agents who market the ICorr courses in their countries or regions. In all cases Tutors and Assessors must hold the relevant ICorr certification to be eligible to be considered for these roles.
STGB is made up of about six ICorr members, who have knowledge and experience of coatings and coating related inspections, and STGB is chaired by a Level 3 Coating Inspector.
STGB is always looking for additional members and if you have an interest in joining STGB please contact Keith Wagner via the ICorr Office.
CPGB is a sub-committee of Professional Development and Training Committee (PDTC). Both CPGB and the Cathodic Protection Scheme Manager (CPSM), report to the PDTC Chairman, and work closely with one another to ensure an effective running and management of the Cathodic Protection courses and exams. These include CP levels 1 to 4. All members of CPGB are CP specialists in at least one of the four sectors of CP. The CP Scheme Manager is also a member of the CP Governing Board, which meets on a regular basis.
CPGB ensures as a minimum:
• Scheme is run in accordance with BS EN ISO 15257 – Cathodic protection. Competence levels and certification of cathodic protection personnel, and BS EN ISO/IEC 17024.
• the documents detailing the scheme, course material and exams, are up to date and fit for purpose.
• Document control to ensure latest versions are available for each course.
• Audit the syllabi, the course content, and the course delivery of CP courses.
• Audit both the technical content and process of the examinations.
The CPSM, additionally, coordinates course bookings, training centre availability and candidates, and ensures that the course work and examination material is delivered at the appropriate time and location, examinations are booked, completed, and marked, and the results are fed back to ensure that candidates then apply for their certification on time.
Nearly 20 CP courses were conducted, and 120 candidates attended these courses, in 2022.
The Scheme Manager also ensures that candidate feedback is regularly received by the CPGB as well as the tutors, as this is key to the success of CP courses.
The current CPGB Chair is Raju Narayan, and CP Scheme Managers, Eva and
Bill Whittaker.