The cart is empty!
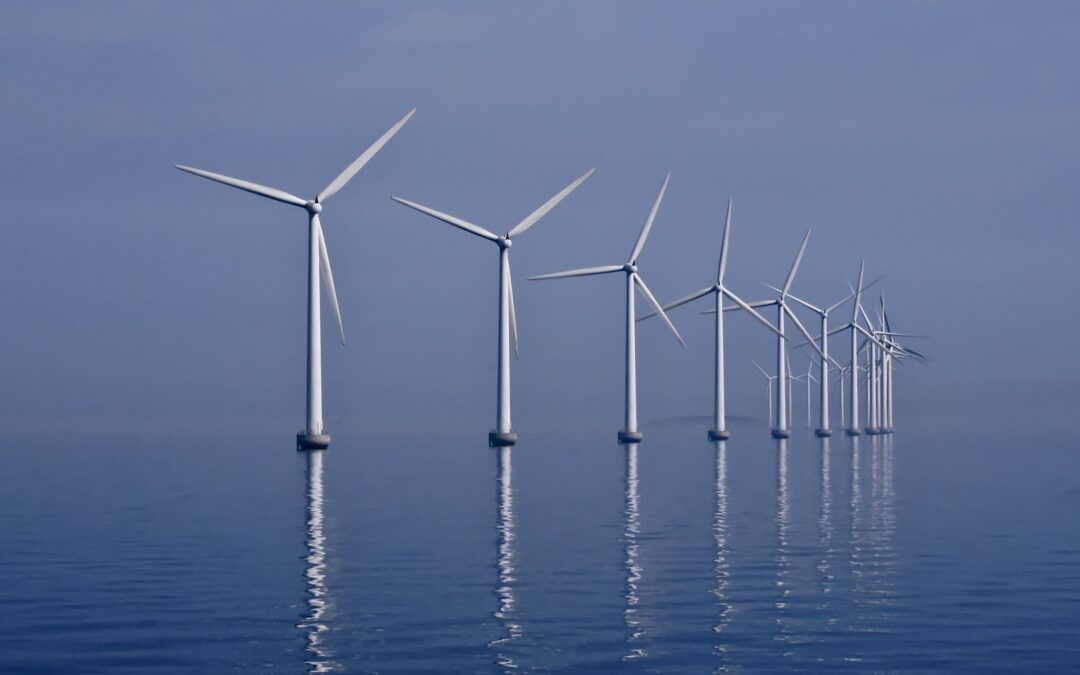
The Role That Corrosion Management Plays in Sustainability of Wind Turbines
Corrosion Is Key to the World’s Net Zero Goals
The world is waking up to the need for sustainability, but is struggling with how to achieve it. How can we meet our current energy needs without compromising the ability of future generations to meet their own needs?
Sustainability is a concept that’s essential to our survival as a species, as we face increasing pressure on our natural resources due to population growth, urbanisation, and climate change. A key piece of the puzzle is to transition to renewable energy sources, and wind turbines are a prime example of this. But their viability is impacted by corrosion.
By understanding the challenges and opportunities presented by corrosion in wind turbine structures, we can work towards a more sustainable and resilient future.
In this article, we delve into the topic of wind turbines and sustainability, focusing on corrosion:
- We explore how wind turbines are affected by corrosion, and the impact that it has on their lifespan and efficiency.
- We also look at current methods for preventing and mitigating corrosion in wind turbines, and discuss potential future developments in the field.
Just how important are wind turbines?
The amount of energy produced by wind turbines is rocketing. According to the International Energy Agency, wind electricity generation increased by 17% in 2021 ─ that’s 55% faster growth than in 2020. The majority of this growth (perhaps surprising to most) came in China.
In the coming years, there are ambitious plans to increase the amount of electricity produced by wind even further. China plans to generate a third of its energy from renewables by 2025, with 18% from wind and solar. The EU is targeting 40% renewables by 2030.
The UK is already a world leader in wind power. It produces over 75 million MWh per year from wind. That’s enough to power 20 million homes. It has more offshore wind capacity than any other country in the world. In the second quarter of 2022, the UK’s wind farms produced almost 40% of the energy generated across the UK.
If the UK is to meet its target of net zero by 2050, and the world to meet its longer-dated targets, wind turbines are crucial. But there is a problem looming: corrosion.
How wind turbines are affected by corrosion
Wind turbines work by harnessing the kinetic energy of wind and converting it into electricity:
- They consist of a rotor with blades that rotate when the wind blows.
- In turn, this spins a shaft connected to a generator.
- The electricity generated by the turbine is then transmitted to the grid and distributed to homes and businesses.
The vast majority of wind turbines are horizontal-axis turbines, which have blades that rotate around a horizontal axis, and they can be found in various sizes and configurations. It’s a lot of moving parts.
Of course, wind turbines are built to withstand the harsh conditions of the natural environment, but even the most robust structures can be affected by corrosion. In the case of wind turbines, corrosion can occur on various components, such as the blades, the tower, and electrical components. This corrosion happens in several ways.
Wind turbines are affected by corrosion through exposure to the elements. A turbine’s components are constantly exposed to wind, rain, snow, and other weather conditions which can cause a variety of forms of corrosion. For example:
- The blades of a wind turbine are exposed to UV radiation, which can cause UV degradation, leading to cracks and delamination.
- The tower and other components can be affected by corrosion due to exposure to saltwater, which is commonly found near coastal areas.
- Another common form of corrosion that affects wind turbines is galvanic corrosion. This is a particularly challenging form of corrosion to prevent, as it often occurs in hard-to-reach areas of the turbine.
- Ultra violet (UV) degradation from sunlight and blade erosion, which degrades the coating on the blade as the tips of the blade can reach speeds of 300km/h.
The impact of corrosion on wind turbines
Corrosion can have a significant impact on a wind turbine:
- It can lead to a reduction in the efficiency of the turbine, which can result in a decrease in the amount of electricity generated.
- It can also lead to structural damage, reducing the lifespan of the turbine and increasing the need for maintenance and repairs.
According to the National Renewable Energy Laboratory, the lifetime of wind turbines is around 20 years. It’s a big, expensive piece of equipment to manufacture and install. If corrosion is not addressed on time, the turbine lifespan can be reduced. And good corrosion practice prolongs both reliability and turbine life.
In other words, by taking steps to protect wind turbines from corrosion, we can ensure that they continue to generate clean, renewable energy for much longer. This reduces costs and environmental impact (wind turbine blades cannot, yet, be recycled effectively).
Prevention and mitigation of corrosion in wind turbines
Clearly, preventing and mitigating corrosion in wind turbines is crucial for ensuring their longevity and efficiency.
There are a number of methods currently used to protect wind turbines from corrosion, and these can be divided into two main categories: passive and active corrosion prevention.
· Passive corrosion prevention methods
These include the use of coatings, such as paint and galvanizing, and the use of corrosion-resistant materials, such as stainless steel and aluminum.
Coatings work by creating a barrier between the metal and the environment, which slows down the corrosion process. For example, coatings like paint and galvanizing provide a physical barrier that protects the metal from exposure to the elements. However, coatings can wear off over time, and they may not be effective in areas that are difficult to reach.
· Active corrosion prevention methods
These include the use of cathodic protection and corrosion inhibitors, and the use of monitoring systems to detect and track the progression of corrosion.
These methods actively control the corrosion process, rather than merely slowing it down. For example, cathodic protection systems use electrical current to prevent corrosion from occurring, while inhibitors are chemical compounds that can be added to the environment to slow down the corrosion process.
The effectiveness of corrosion prevention methods depends on various factors, such as the environment in which the turbine is located, the type of corrosion that is occurring, and the type of material that is being protected.
Looking ahead, there are several potential developments in the field of corrosion prevention for wind turbines that show promise.
For example, the use of advanced materials (such as nanocomposites, which have superior corrosion resistance properties) could greatly improve the durability of wind turbine components.
Additionally, the use of advanced monitoring systems (such as ultrasonic and infrared imaging) could help detect corrosion at an early stage, allowing for timely repairs and maintenance.
The field of corrosion prevention for wind turbines is constantly evolving, and new technologies and materials are being developed to improve the durability of wind turbine components. By continuing to invest in research and development in this area, we can work towards creating wind turbines that are more sustainable and resilient.
The bottom line
Wind turbines are a vital tool in the transition to a more sustainable and resilient future. As renewable energy sources, they play a crucial role in reducing our dependence on fossil fuels and fighting climate change.
Indeed, Greater Gabbard, off the northeast coast of England, will become the largest offshore windfarm in the world. Blades will exceed 100 metres in length, and each turbine will be capable of producing 14MW of electricity. You’ll have a chance to see these being tested at the Ore Catapult during our conference ‘Integrity Engineering for a Sustainable Future’ in June 2023.
However, like any machine, wind turbines are not immune to the effects of corrosion. This can have a significant impact on lifespan and efficiency, reducing overall effectiveness as a renewable energy source.
Preventing and mitigating corrosion in wind turbines is crucial. A variety of methods are currently used to protect wind turbines from corrosion, and these methods have different levels of effectiveness depending on many factors.
The field of corrosion prevention for wind turbines is constantly evolving, and new technologies and materials are being developed to improve the durability of wind turbine components. It’s crucial that we continue to invest in research and development in the field of corrosion prevention for wind turbines. By doing so, we can work towards creating wind turbines that are more sustainable, resilient, and efficient.
To learn more about the sustainability initiatives developed and promoted by the Institute of Corrosion (like the conference on Integrity Engineering for a Sustainable Future), please email us.