Fellows Corner
This series of articles is intended to highlight industry-wide engineering experience, guidance, and focussed advice to practising technologists. It is written by ICorr Fellows who have made significant contributions to the field of corrosion management. This issue features an introduction to intumescent coatings, by Brian Goldie.
Passive Fire Protection – Intumescent coatings
Today most buildings and structures have some degree of fire protection in order to protect lives, delay possible structural collapse allowing for evacuation, provide areas of temporary refuge in the case of fire, and ensure the integrity of escape routes, by preventing or delaying the escalation of a fire and protecting high-value assets.
There are two basic types of fire protection: active and passive. Active fire protection includes alarms and detection systems, sprinklers and water deluge systems, firefighting equipment and foam and powder extinguishers. Passive fire protection involves materials such as concrete, mineral fibre boards, vermiculite, cements, and intumescent coatings. This article will describe how intumescent coatings can achieve passive fire protection in many structure types including offshore platforms or floating facilities, such as FPSOs and FLNGs, and commercial buildings.
Intumescent coatings have been used to protect the steelwork in buildings and other structures from fire for approximately 40 years. These coatings work by swelling up in the event of fire and physically creating a barrier between the steel and the fire for as much as 4 hours in some cases. Steel begins to lose its structural strength at about 400 C, and these coatings can delay the time it takes to reach this temperature (Figure 1). Intumescents are often referred to as thin- film or thick-film coatings.
Thin-film intumescents are typically single component solvent or waterbased products, and have dry film thicknesses (DFTs) of less than 5 millimetres. In the last few years new technologies, such as multi-component methacrylate, or “hybrid” products, have been brought to the market, offering specific advantages over the traditional products.
Thick-film coatings are typically solvent-free, epoxy-based with DFTs of up to 25 millimetres.
The acceptance and use of intumescent coatings increased dramatically in Europe in the 1980s as the major oil companies learned of their ability to protect structural steel from the extreme heat caused by hydrocarbon fires, including jet fires caused by leaking hydrocarbons. Also, exposed steel was used more prevalently in the design of commercial structures and high-rise buildings, increasing the use of thin-film intumescents, which looked more like conventional paint and therefore could meet the aesthetic requirements of architects.
How Do Intumescent Coatings Work?
Intumescent coatings react to fire by expanding to form a carbon “char” with low thermal conductivity, which essentially forms an insulating layer reducing the rate of heat transfer and extending the time necessary to reach the critical failure temperature of the underlying steel.
It’s a complex chemistry incorporating the organic binder resin (coating) — typically an epoxy (hydrocarbon fire) or acrylic (cellulosic fire), and an acid catalyst, for example ammonium polyphosphate, which decomposes to yield a mineral acid. This acid reacts with a carbonific source, for example, pentaerythritol, to produce a carbon char. A spumific (foam-producing) agent, such as melamine, reacts with the acid source and decomposes, evolving into an inert gas which then expands the char. These are the basic reactions taking place, although more complex interactions also occur. Reinforcing mesh can be used to support the formed char.
Cellulosic vs. Hydrocarbon Fires
A cellulosic fire has a fuel source composed mainly of cellulose — for example, wood, cardboard, or paper. Hydrocarbon fires are fuelled by hydrocarbon compounds and ignite and grow exceedingly fast, achieving high temperature almost immediately after ignition, greater than 1,000C in less than five minutes (Figure 2). Cellulosic fires are slower to reach maximum temperature but may eventually reach or surpass the temperature of a hydrocarbon fire.
A hydrocarbon pool fire is defined as a turbulent diffusion fire burning above a horizontal pool of vapourising hydrocarbon fuel, where the fuel has zero or low initial momentum. A jet fire is a turbulent diffusion fire resulting from the combustion of a fuel continuously released with high pressure.
Testing Intumescent Coatings
No two fires are the same. The conditions depend on the type and quantity of fuel, the availability of oxygen and ambient conditions. For reproducible product testing. “standardised” fires have been defined, for example, BS 476 (parts 20 and 21) “Fire tests on building materials and structures” and EN 13381 (part 8), “Test methods for determining the contribution to the fire resistance of structural members” describe how intumescent coatings are tested with cellulosic fire exposure. Performance depends on coating thicknesses, the types of steel section, I-section, hollow section, and the section orientation, i.e., beam or column.
Other test standards include UL 1709, “Rapid Rise Fire Tests of Protection Materials for Structural Steel” for hydrocarbon fire exposure, ISO 22899-1, “Determination of the resistance to jet fires of passive fire protection materials”. Different standards apply to marine applications. It is not possible to test every variation, so the test results are analysed to produce an assessment of performance.
Ensuring Durability
To protect steel in a fire, a coating must be resistant to the environment and be intact at the time of the fire. Poor durability can lead to ineffective fire protection resulting in structural failure during a fire and expensive restoration afterwards. Poor durability can also lead to corrosion of the substrate, compromising structural integrity. To ensure durability of intumescent coatings the key ingredients — ammonium polyphosphate, melamine and pentaerythritol — are all sensitive to moisture, and must be formulated carefully.
Different resins are used to prepare intumescent coatings for different applications. Water-based acrylic materials are formulated for use in mainly dry, internal locations. Solvent- based acrylic materials are used to formulate intumescent coatings for use in internal or sheltered external locations.
Solvent-based or solvent-free epoxy materials are used to formulate intumescents that can be used in any location. These resins have different weathering performance, and therefore, protection capabilities.
To test the durability of an intumescent coating, standard coating test procedures are used, such as NORSOK M 501, “Surface preparation and protective coating,” Underwriters Laboratory, UL 2431, “Rapid Rise Fire Tests of Protection Materials for Structural Steel”, European Technical Approval Guidance, EAD350402-00-1106, “Reactive Coatings for Fire Protection of Steel Elements”, and/or EN16623, “Reactive coatings for fire protection of metallic substrates. Definitions, requirements, characteristics and marking.”
In addition, the intumescent coating should not spall or crack in use, be resistant to atmospheric and chemical attack and be re-coatable with itself — even after prolonged curing. There should also be excellent bonding between substrate, primers and the intumescent to combat the problems of under-film corrosion.
Specifying Fire Protection
Firstly, the item to be protected must be identified, whether it is structural steel, vessels, or divisions such as fire-resistant bulkheads, or decks, on petrochemical facilities. The general rule is, the thicker the coating, the longer the protection – up to a limit. The thickness of the intumescent used will depend on the weight and type of the steel member being protected. As the weight of steel decreases, the thickness of the intumescent should increase. Lightweight steel sections will heat up faster than heavier sections and will therefore need more protection for a given time.
Rather than just figuring the weight of the steel, specific calculations must be made in order to determine the appropriate thickness of the coating, taking into consideration the shape, or shapes, of the steel and accounting for any cut-outs or irregularities in the beams. The critical steel temperature which must be protected against should be defined — for example, structural steel between 200 and 750 C, and vessels between 200 and 350 C.
Next the section factor must be considered, as well as the fire protection period of between 30 minutes and four hours. The section factor (Hp/A) is the ratio of the fire exposed perimeter to the cross-sectional area of the steel (Table 1).
Most intumescent coating suppliers provide guidance in calculating the thickness of the coating required for a specific use and some have dedicated departments staffed with trained fire engineers who will do the calculations for you. For cellulosic fires, the products will have 3rd party certification to national or international standards (BS 5476 or EN13381). For hydrocarbon fires, the products will have certification from bodies such as Lloyd’s Register, Det Norske Veritas, or Underwriters Laboratories.
Consideration must also be given to the service environment the structure or vessel will be exposed to, as well as any special requirements such as blast resistance, high or low substrate temperature or cryogenic spill protection.
Conclusion
In addition to offering fire protection for up to four hours, intumescent coatings offer speed of application, shop or field application, aesthetic appearance and ease of inspection and maintenance.
Intumescents can protect a variety of steel surfaces from structural columns and cellular beams, to building components, vessels, and complex shapes. They can be formulated to protect against cellulosic and hydrocarbon fires including jet fires and fires resulting from explosions.
I would like to acknowledge the assistance of colleagues at JPCL, and Rick Perkins, Global Technical Manager – Fire, Sherwin-Williams Protective Marine Coatings, in compiling this article.
Brian Goldie
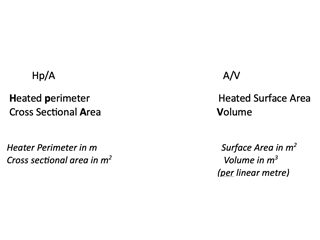
Table 1. Ratio of surface exposed to the fire, and “heat sink”.
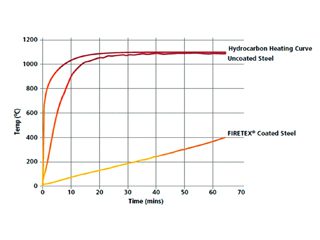
Fig. 1: This graph illustrates the effect of intumescent coating on steel temperature in a hydrocarbon fire.
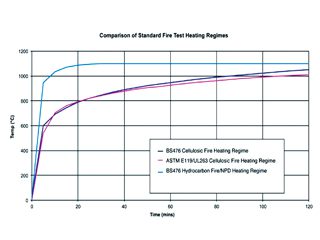
Fig. 2: This graph compares the heat-up rate of cellulosic and hydrocarbon fires.
Industry News, Latest News
The following documents have obtained substantial support during the past two months, and have been submitted to the ISO member bodies for voting, or formal approval.
ISO/FDIS 4624 Paints and varnishes — Pull-off test for adhesion (Revision of 2016 standard)
ISO/DIS 3549 Zinc dust pigments for paints —Specifications and test methods
ISO/DIS 14919 Thermal spraying — Wires, rods and cords for flame and arc spraying — Classification — Technical supply conditions (Revision of 2015 standard)
ISO/DTS 16774-2,3,4 Test methods for repair materials for water-leakage cracks in underground concrete structures — Part 2: Test method for chemical resistance, Part 3: Test method for water (wash out) resistance, Part 4: Test method for adhesion on wet concrete surface (Revision of 2016 standards)
ISO/FDIS 24131-1,2 Internal protection by polymeric lining for ductile iron pipes — Requirements and test methods — Part 1: Polyurethane lining, Part 2: epoxy lining
ISO/DIS 24489 Non-destructive testing — Acoustic emission testing — Detection of corrosion at atmospheric and low-pressure metallic storage tank floors
New International standards published in the past two months.
ISO 1518-1:2023 Paints and varnishes — Determination of scratch resistance — Part 1: Constant loading method
ISO 4212:2023 Corrosion of metals and alloys — Method of oxalic acid etching test for intergranular corrosion of austenitic stainless steel
ISO 4618:2023 Paints and varnishes — Vocabulary
ISO 4905:2023 Corrosion of metals and alloys — Electrochemical test methods for high-temperature corrosion testing of metallic materials in molten salts
ISO 7142:2023 Binders for paints and varnishes — Epoxy resins — General methods of test
ISO 7784-1,2:2023 Paints and varnishes — Determination of resistance to abrasion — Part 1: Method with abrasive-paper covered wheels and rotating test specimen, Part 2: Method with abrasive rubber wheels and rotating test specimen
ISO/TS 19392-6:2023 Paints and varnishes — Coating systems for wind-turbine rotor blades — Part 6: Determination and evaluation of ice adhesion using centrifuge
ISO 24647:2023 Non-destructive testing — Robotic ultrasonic test systems — General requirements
Institute News
Manchester remains Europe’s largest centre of corrosion education and research and that is why the Institute’s Council have recently taken the decision to support, with bursaries, MSc programme students drawn from those taking the MSc (PGT) in corrosion, and those opting for the corrosion option in the final (4th) year of the undergraduate materials engineering MEng programme. This will be ICorr’s largest ever single investment in corrosion education with a total sponsorship of £25k per year over 5 years (£125k), and is fully aligned to our memorandum of association (MOA). The timing of the announcement is linked to the 65th Jubilee Symposium and the opening of the new Corrosion Labs at Manchester, held on 3rd and 4th April 2023 to celebrate 65 years of corrosion teaching and research at The University of Manchester (UoM).
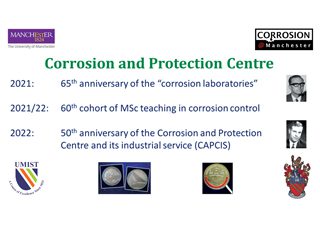
The UoM corrosion group comprises a collegiate academic team where Stuart Lyon is currently “first among equals”. Stuart was, of course, ICorr President from 2004-2006, and CEO of Correx from 2007 to 2012 when ICATS was just getting going. Stuart has always remembered his father’s despair when the beloved family car (a Rover 2000) gradually rusted away. Now, as AkzoNobel Professor of Corrosion Control, Stuart specialises in the field of protective organic coatings formulating environmentally sustainable paints, to greatly extend the useful life of materials and assets.
Corrosion education was established by Ken Ross (a Chemical Engineer) in 1957, at the former Manchester College of Science and Technology (which became UMIST in 1966). Ken had become aware of the cost of corrosion damage in chemical plants and the lack of awareness of maintenance staff and management, and was determined to do something about it. Subsequently in 1962 he established, with Graham Wood (another former ICorr President), the MSc course in Corrosion Science and Engineering which continues to this day as the MSc in Corrosion Control Engineering. The Corrosion and Protection Centre, led by Graham as Britain’s first “Professor of Rust” came about in 1972 as a consequence of the much-quoted Hoar Report on the cost of corrosion. The Corrosion Protection Centre Industrial Service (CAPCIS – now part of Intertek), which became the world’s largest corrosion consulting organisation, was also established at the same time with government pump-priming. At one time more than half the world’s corrosion engineers outside North America had been educated in Manchester.