Institute News
Each year, the Institute of Corrosion bestows a range of internationally renowned awards in recognition of excellence in corrosion science and engineering, and to reward outstanding service to the Institute and the wider corrosion community.
The institute is extremely proud to announce the selection of Trevor Osborne, FICorr (Hon), NACE Corrosion Specialist, for the H.G. Cole Award.
This award is made in recognition of exceptional services to the development of the Institute. It is only awarded on an occasional basis, reflecting the highest possible level of commitment of the recipient to the activities of the Institute. The inaugural H.G. Cole Award (in the form of a poignard) was presented to Charles Booker in 1997 by Gwen Cole (wife of the late Henry Cole), in recognition of his many years of service as Honorary Secretary of the Institute. The modern form of the award is a plaque whose design captures the essence of the original poignard.
Trevor is a past president of the Institute of Corrosion and a long-standing chair of the board of its commercial arm, Correx Ltd. He is managing director of Deepwater Corrosion Services (UK) Ltd., and has worked in the energy industry for over 43 years, with very wide experience in corrosion control and project execution. He will be presented with the award at the Institute AGM to be held on November 8, 2023, in Birmingham.
We offer our sincere congratulations to Trevor on this magnificent achievement.
Background to the H.G. Cole Award
Henry George Cole was the chief materials engineer at the UK Ministry of Defence. He was based in London and Farnborough, and was a hugely respected coordinator and sponsor of research, an elegant and influential ‘Whitehall Mandarin’, and a man of spectacular vision and determination. He was Secretary to the Hoar Committee, a ground-breaking development for the recognition of corrosion costs in the early 1970s that was the mainspring for corrosion interest in UK government circles for the next twenty years. Henry Cole was also hugely committed to the Institute of Corrosion. He became the part-time administrative officer for the institute when it shared accommodation with the SCI at Belgrave Square. He oversaw the Institute’s move to the IMF offices in Birmingham and he was one of the guiding lights of the Institute until his untimely death on 14th May 1987.
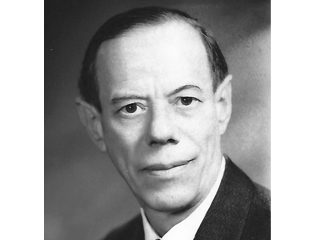
Trevor’s Legacy
Trevor has made an outstanding contribution to the long-term financial sustainability of the institute in a variety of roles over many years. He has guided the Institute financially by overseeing the continued success of our ICATS training scheme in his role as Chair of the Correx Board, and by coordinating sound investments on our behalf. In addition, before retiring from Council in 2022, Trevor spearheaded the purchase and refurbishment of a new headquarters for the Institute – ‘Corrosion House’ in Northampton.
This is a ‘state of the art’ 3-storey building, with the ground floor dedicated to the HQ administration team, the middle floor for training, and the top floor as a conference room. Each floor has its own kitchen, and the corrosion training centre has a breakout facility for delegates.
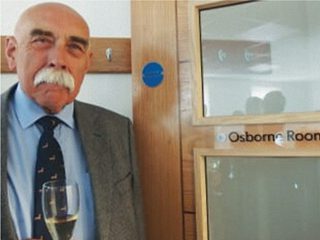
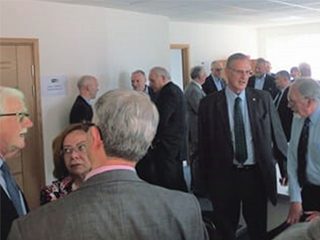
Corrosion House is undoubtedly a world class facility, totally fitting for the Institute of Corrosion, and based in a location in easy reach for both national and global customers, that today welcomes customers and members from all over the world.
More information on the H.G. Cole Award can be found on the Awards page of the ICorr Website:
https://www.icorr.org/icorr-awards/
Institute News
On 13th April, the branch heard a presentation from US based APS (of Malvern, PA), at Metec in South Shields.
During this informative presentation, the non-thermal plasma technology was presented by Andy Kintz, focusing on the key benefits of low temperatures maintained during the application and the minimal waste produced. When applied to a coating on a metal substrate, the reaction with the organic matter in the coating removes the coating creating by-products of water vapour, CO2 along with any inorganic particles, and does not change the metal substrate underneath, so revealing the roughened substrate from when the coating was applied.
If applied to an uncoated metal substrate the plasma can produce a temporary low level of surface energy which can improve the adhesion of linings.
Currently the system has a small application nozzle and is designed for small applications such as bolt and weld cleaning, rather than large areas of surface preparation. Peter Yancey of APS then carried out practical demonstrations of the cold plasma technology, removing both aged coatings and rust from steel panels, and reinforcing the claims made in the preceding presentation.
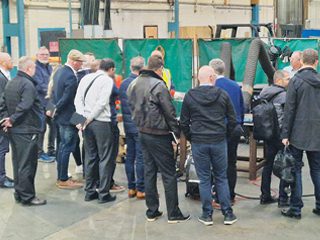
Institute News
On Tuesday 28th March 2023, the
branch meeting welcomed Dr Kevin McDonald – Sonomatic, with a talk entitled ‘Effective pipework analysis and inspection planning using Digital Twins’.
Kevin is a principal integrity engineer within Sonomatic’s integrity team in Aberdeen. He is a mathematician with a PhD in computing science. He has extensive experience in data analytics and inspection planning for pipework, pressure vessels and pipelines, co-authoring the recommended practice for Non-Intrusive Inspection (NII) as applied to pressure vessels. As well as integrity consulting, he is involved in the technical capability development for Sonomatic’s integrity team with a focus on statistical approaches. Recently, he has been involved in developing a statistics-based method of inspection planning and evaluation applied to subsea pipelines for a major operator.
Effective pipework analysis and inspection planning using digital twins
The integrity of pipework is essential for the safe and reliable operation of process plants. Inspections are traditionally performed at large numbers of individual test points, with results recorded in an inspection database. In general, this data is subject to relatively simple analysis, with the results used in integrity management decisions. However, this traditional approach can be heavily influenced by poor processes, outliers, or errors for example: incorrect entry of results, not recording higher thickness readings than those obtained previously, and inconsistencies in inspection location, are some examples of how error can be introduced into this process. This could lead to poor integrity decisions and misinterpretation of wall thickness trends. Analysis of pipework data, which is in general restricted to the difference between two thickness readings relative to the dates the readings were taken, can then be driven by measurement error.
Kevin proposed a novel alternative is to consider historic datasets as a whole and look at long-term statistical behaviour to consider how corrosion could be affecting pipework. This approach looks at whole datasets to determine behaviour before considering any sub-groupings of data points that are showing similar behaviour. The Sonomatic developed SPiDARS software accommodates many data formats. Boxplots can be used to display the whole of an inspection history in one view. In this example a normalised view allows all schedules of pipe to be compared. Boxplots can also be used to provide a quick overview of long-term trends (up or down) and can show stability over several years or highlight changes graphically that cannot be seen from data alone, due to spreads and errors affecting judgement.
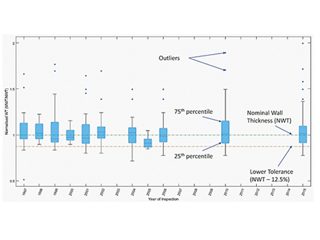
The illustrated example shows a downward long-term trend indicative of increased corrosion activity. It provides context and a jump in the final result, indicating replacement of the pipe. Data can also be grouped for pipes by diameter which can show that larger pipes seem to have more corrosion issues than smaller ones, or by pipe configuration feature type such as bends, caps, reducers, or straight sections to search for trends.
Corrosion rates determined from Non Destructive Testing ( NDT) generally trend toward wall loss percentile values as the principal criteria. Looking at group trends mitigates measurement error and gives more accurate short and long-term corrosion rate estimates. Any point showing a concerning trend can be extrapolated to predict when an alarm limit may be reached. Corrosion rate data can be plotted in different ways to try and identify issues such as localised and unusual corrosion rates. Lots of data on wall thickness measurement may just behave in a linear sense such as presented here for selected years and locations – nothing unusual is shown and general corrosion is happening at expected rates.
Sonomatic have developed 3 different inspection planning methodologies. The Type 2 methodology was further discussed with steps detailed below:
• Define corrosion state (is it what we expect to find)
• Define a corrosion coverage from previous results
• Define extent of corroded material
• Define thresholds of concern (based on historic results)
• Consider points flagged as over/under inspected
• Consider expected corrosion mechanisms that have a bearing on applied technique
• Define detection threshold
• Define probability of detection (POD)
This approach is underpinned by simple and effective access to the data, which is linked to a 3D mini digital twin.
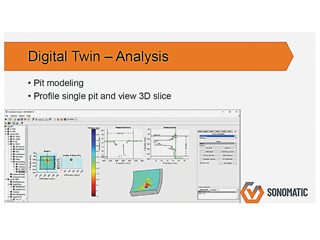
The mini-Twin also hosts a variety of data, as well as individual test points, corrosion maps, and can house inspection histories, photographs, and further data analysis of corrosion rates, fitness for service etc. 3D is used to present data in efficient ways to quickly provide an overview of the health of the pipework circuit, for example inspection frequency, inspection count, corrosion rates, all of which is valuable information for engineers and asset stakeholders.
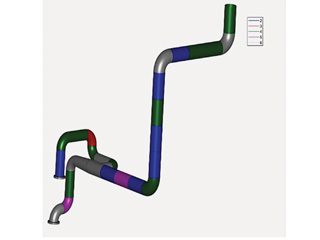
Considering sub-groupings of features within a pipework circuit has several benefits – a more representative statistical corrosion rate can be calculated per sub-group that will yield better insight into corrosion behaviour, and an illustration of points that could have been over inspected or under inspected, and information on features that may be of concern on other circuits. This methodology can deliver more efficient and targeted inspections, which represents significant cost savings in the form of lower inspection costs, and better planning of when repair or replacement may be necessary.
• Data is screened on upload for spurious points and has automated and electronic reporting. New inspection data can be uploaded to it to refine analysis and it links to mini-Twin.
• Inspection recommendations from SPiDARS are fed into the digital twin for ease of issue. Data extrapolation can be done within the digital twin, and also by SPiDARS – as they talk to each other. This will flag when repair or maintenance is required.
This was a fascinating and very worthwhile presentation from Kevin, that generated much interest from the online audience.
During April, the branch held two events, firstly, a joint hybrid event with the Marine Corrosion Forum, on the 25th April at the Palm Court Hotel. This was followed by an industrial visit to ICR’s premises at the Bridge of Don, to which MCF members were invited, with several demonstrations of ICR’s technology initiatives.
The industrial visit was split into group presentations in rotation for 6 demonstrations, which showed examples of ICR’s core business activities:
• Chemical Injection / Corrosion Monitoring
• OMNI Integrity Management Software.
• QuickFlange™ Weldless Connectors
• Sky-Futures™ Unmanned Aircraft Systems (UAS) Inspection
• Technowrap ™ Engineered Composite Repairs
• INSONO Composite Wrap Integrity Inspection
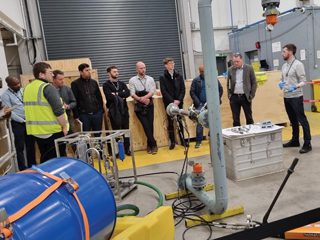
Chemical injection / corrosion monitoring services are provided throughout the energy sector by ICR who have specialist tooling and trained engineers for retrieving corrosion monitoring coupons, probes, and quills into live pipeline valve stations. The pre-installed fittings on the pipes allow threaded plugs, which carry the mounted coupons, to be inserted into the pipe. This is carried out using either mechanical or hydraulic, telescopic portable tooling, which, through the valve gate, can introduce fresh coupons of pipe grade material which sit within the line for the study period and suffer metal loss through corrosion in the fluid stream. Recovery of the coupons allows weight loss assessment and corrosion pattern study, which can be used to evaluate the
corrosive nature of the fluid and help provide remedial measures such as chemical injection solutions, for which ICR supplies a range of pumping equipment.
OMNI is a cloud-based integrity management software that enables full-lifecycle digitalisation to be tailored and implemented in line with organisational requirements and can connect directly to the latest advancements in technology, such as digital twins (as described above), robotics, and corrosion sensors. OMNI is configured as an ‘all in one’ platform, able to capture all integrity and inspection data formats, compare and provide real-time defect detection and enable the close-out through anomaly and repair –- offering improvements to operational safety and reliability. Organisations can communicate and manage operational workflows more effectively using OMNI’s innovative features such as process automation, tracking and online collaboration, allowing for better safety and operational risk management and supporting legislative compliance.
ICR also offers on-site weldless, flange to pipe connections (Quickflange TM), which are effected using a hydraulic, colleted ram system. The flanges to be fitted to the pipe have an annular groove in the inside of the flange into which the wall of the pipe can be expanded using tooling inserted inside the pipe end. The hydraulic ram contains a split collet which expands inside the pipe and forces a ring of the pipe wall into the flange grove. This provides a weldless metal to metal gas tight seal which is dressed each end with Belzona sealant to prevent water ingress to the junction. This can be performed on pipe to flange connections in any remote situation for 3” up to 15” connections. A full demonstration of the operation was performed on 10” pipe using a hydraulic compressor and ram, and sectioned flanges were offered to the audience as proof of the integrity and bond.
ICR also offers on-site weldless, flange to pipe connections (Quickflange TM) which is affected using a hydraulic, colleted ram system. The flanges to be fitted to the pipe have an annular groove in the inside of the flange
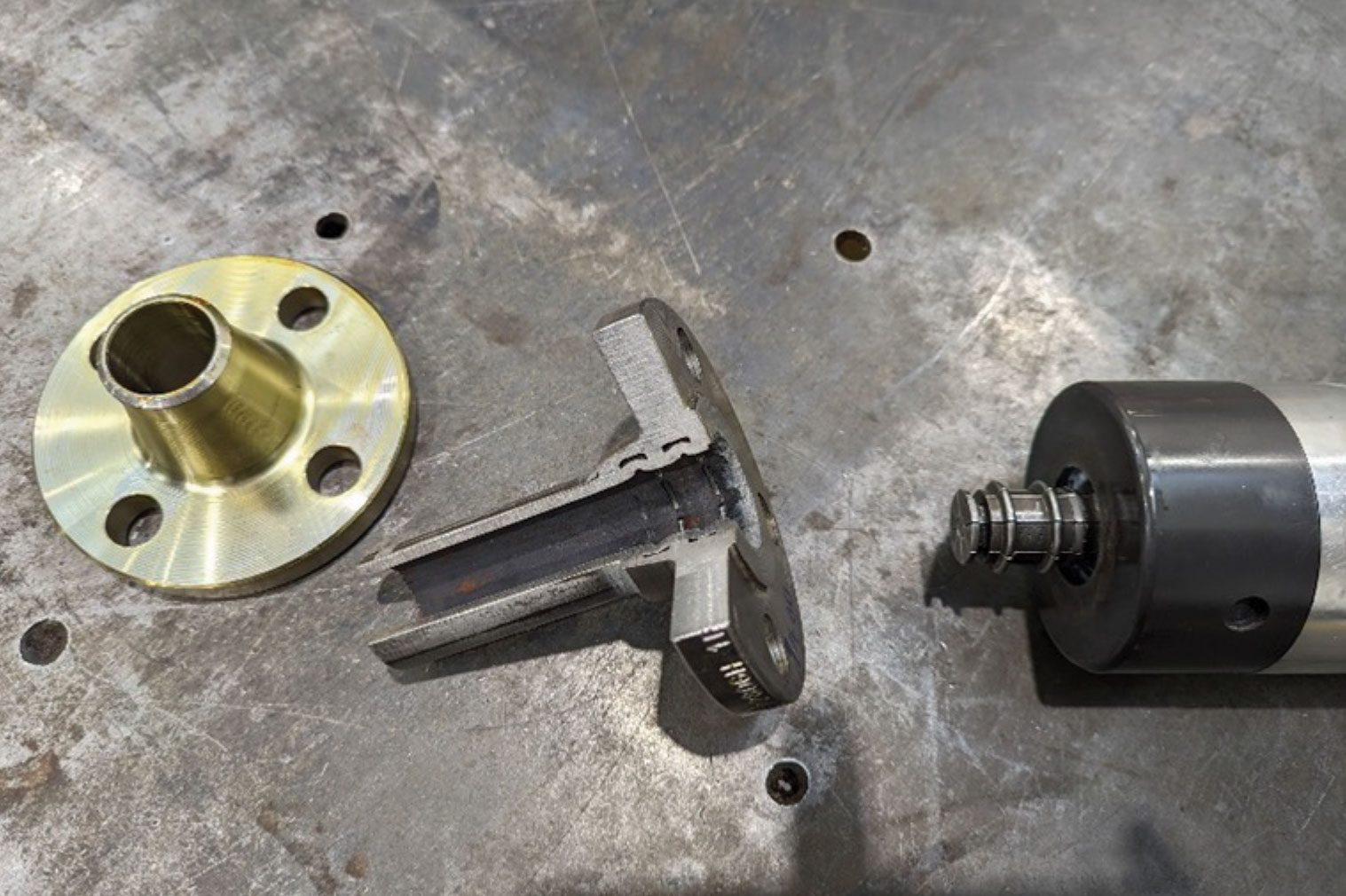
Sky-Futures™ UAS drone inspection devices are a relatively new addition to ICR’s services, and these are widely used across the energy sector including more recently for integrity assessment in the Beatrice wind farm in Scotland’s Moray Firth, as was further discussed at the event.
The turbine’s support structure and blades had exhibited various forms of damage and irregularities, including cracks and compromised safety components, previously identified by rope access personnel. Furthermore, as the turbines were due to reach the end of their service life in the next five years, it was crucial to visually confirm the structures’ overall condition and ensure their continued functionality. This method has reduced the exposure of personnel to working at height and enabled a swift and thorough inspection deploying ultra-high-resolution imagery, to evaluate identified anomalies. The following component areas of the two turbines were successfully inspected to identify any potential dropped objects, or other conditions which could impact the safe decommissioning of the turbines later including:
• Access platforms
• Jackets
• Nacelles
• Support towers
• Turbine blades
The detailed reports and accompanying imagery later provided the client with a comprehensive understanding of the condition of the turbines and their support structures, serving as a crucial component of their future decommissioning strategy.
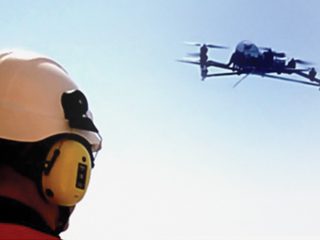
Technowrap ™ Engineered Composite repair solutions widely used in the North Sea were presented for pipework and structural beam strengthening. These repairs use glass and carbon fibre cloth, which is soaked in epoxy and then systematically wrapped around surface prepared pipes, T-junctions, elbows or structural beam sections, to cover and reinforce damaged or thinned areas of pipe or steelwork. The wrapping fibre used has a woven nature and anisotropic strength. Once wrapped, a compression bandage is added, and within 24 hours, the epoxy laden fibre will reach full cured strength.
The wrap system is ideal for situations where emergency or temporary repair is required but is often suitable (when fully engineered at the outset) for a longer-term fix until major maintenance programmes are permissible. ICR is also able to wrap/resolve low pressure pipes that are leaking under service. A flanged threaded plate is fitted into the leak, and a hose is added to divert the leaking fluid while the pipe and edge of the plate are wrapped in the composite. Once the wrap has cured, the threaded plate can be fitted with a blanking plug to reseal the pipe!
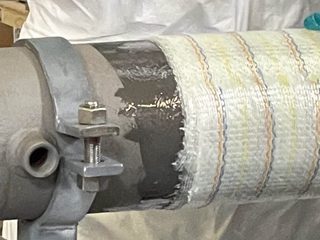
INSONO is an innovative NDT technique for the inspection of engineered composite repairs that is now widely used across the energy sector. This system can validate the condition and integrity of composite repairs, providing operators with assurance of their application and long-term performance. INSONO detected defects fall within three main areas: the composite laminate, the bond line, and the substrate. Based on the principles of the acoustic inspection method with pitch and catch, resonance and mechanical impedance analysis can detect and size the defects. A scanner provides 3D models and a visual representation of the composite repair, allowing for precise dimensions to be used in the assessment. ICR’s manually operated, angled probes are designed to access all geometries and system configurations, detect defects in the composite material, the bond line, and the steel substrate and provides a user-friendly automated inspection report.
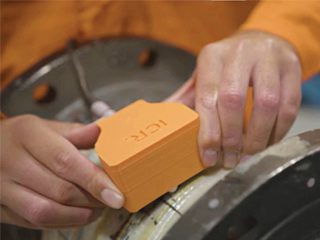
The ICR event was a fantastic opportunity to witness one of Aberdeen’s long-standing ICorr sponsors in action and proved to be a most enjoyable evening.
ICorr Aberdeen welcomes suggestions for further industrial visits.
Abstracts of potential papers for the branch technical programme are always welcome, and anyone wishing to join the committee should correspond with the 2023/2024 Technical Programme Co-ordinator: Adesiji Anjorin, anjorin@gmail.com
Further information about the branch, and past presentations, may be found on their website page: Aberdeen Branch – Institute of Corrosion (icorr.org), and to join the Aberdeen Branch mailing list, please contact: icorrabz@gmail.com
Dr Kevin McDonald, Sonomatic.
Boxplots, Sonomatic
Digital Twin – Analysis, Sonomatic.
3D Data Profiling, Sonomatic.
ICR Chemical Injection and Corrosion Monitoring.
ck Flange™ Weldless Connectors.
ICR-Sky Futures, Drone Inspection.
Technowrap ™ Engineered Composite Wrap, ICR.
Technowrap ™ Engineered Composite Wrap, ICR.