The cart is empty!
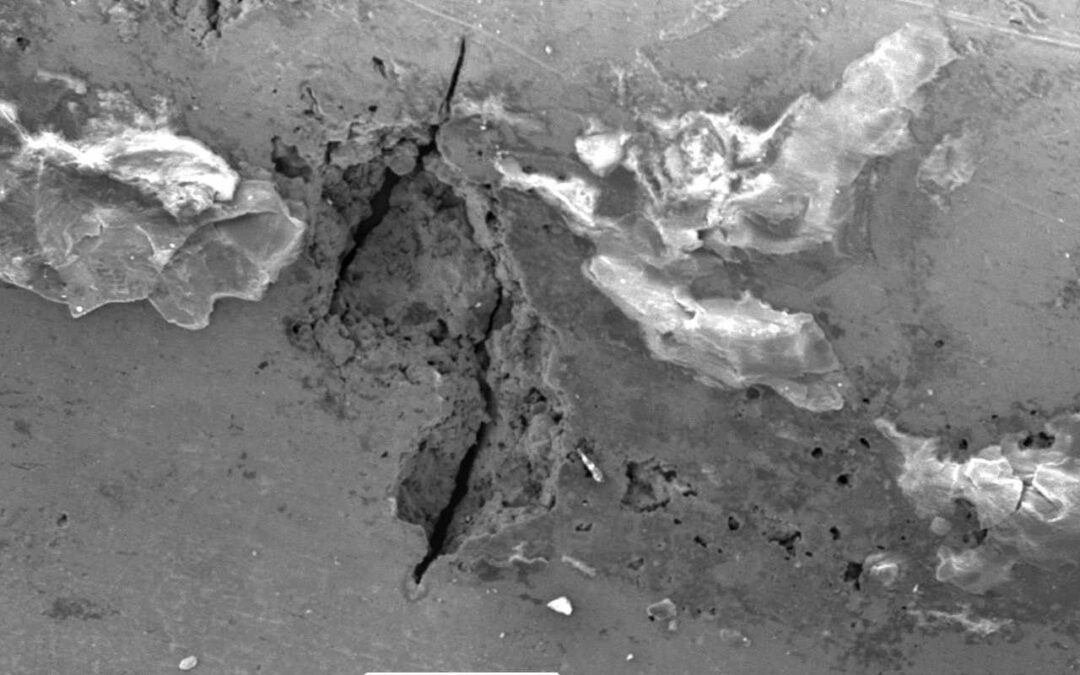
Bio-Corrosion Basics: What Is MIC Corrosion?
An Introduction to Microbiologically Influenced Corrosion
Microbiologically Influenced Corrosion (MIC) refers to the effect of metabolic activities of colonising microbial populations on the kinetics of the corrosion process. Microorganisms are ubiquitous and the phenomenon is caused by bacteria that settle and stick to the metal surface – known as sessile colonies. Zones of established biofilm are anodic with different physiochemical conditions on the metal surface.
MIC is the least understood corrosion phenomenon. It affects systems in different industries with traces of water and is predominantly manifested in the form of localised corrosion (pitting).
Corrosion is a natural process. It can’t be stopped but can be controlled. It is an electrochemical process involving the flow of electrons and ions. Microbial metabolic activities can accelerate corrosion reactions. The annual cost of corrosion in the oil and gas industry is estimated at USD 13.5 billion per annum and MIC is the cause of around 20% of all corrosion failures. Sulphate-reducing bacteria (SRB) are the best-known corrosion-causing microbes. However, there are other equally detrimental microbial groups that are responsible for premature failures.
Corrosion is a huge threat to the world’s infrastructure, at a cost estimated to be more than 3% of global GDP. It threatens the fabric upon which the human world exists. From oil and gas installations and pipelines to wind turbines, water systems, bridges, nuclear energy… the list is without end.
Most people are well versed in how the corrosion of metals is generally accepted to occur – electrochemical reactions cause metals to deteriorate.
You may also hear MIC referred to as microbial corrosion, microbial influenced corrosion, bio corrosion, or microbiological induced corrosion.
Unmasking MIC: Understanding the basics
The existence of active microorganisms and water accelerates the corrosion process, and can cause an alarming corrosion rate. It can also cause clogging as microorganisms secrete slimy waste by-products (extracellular polymeric substance – think of this like the fungus that grows on a piece of fruit after it has started to turn brown).
The science behind Microbially Influenced Corrosion
MIC is a complex process involving:
- Different types of microorganisms (bacteria, fungi, algae, and archaea);
- Construction metal; and
- Handled media
Microorganisms attach themselves to the surface of a metal to form a biofilm. This alters the chemical and physical properties on the metal’s surface and creates an environment that accelerates corrosion.
The actual processes involved in MIC include the production of corrosive metabolic by-products, the creation of localised anodic environments, and the physical disruption of protective surface layers. Biofilm can consist of both organic and inorganic materials and layers of different microbial groups. The availability of nutrients and tolerable operating conditions can lead to exponential growth of microorganisms, and therefore accelerate the effects of MIC.
It’s worth noting that in biological corrosion:
- Archaea can grow at temperatures above 80oC (‘Archaea are microorganisms that define the limits of life on Earth. They were originally discovered and described in extreme environments, such as hydrothermal vents and terrestrial hot springs. They were also found in a diverse range of highly saline, acidic, and anaerobic environments’ – Encyclopedia Britannica.)
- Bacteria can tolerate extreme conditions, including high pressure and temperature
- Algae can be problematic on a multitude of surfaces, including concrete
Microorganisms are omnipresent and accelerate corrosion in different ways including:
- Generating acids that can be utilised by other groups and lower pH leading to a fast acid-driven corrosion.
- Forming corrosion products that accelerate corrosion e.g. iron sulphide.
- Working in cyclic effect with detrimental effect on corrosion. While SRB generates the highly toxic and corrosive H2S, sulphur-oxidising bacteria convert sulphide to highly corrosive by-products including elemental sulphur or sulpheric acid.
Among the complexities of MIC is that there are several groups of bacteria involved. Two of the most common are:
- The anaerobic sulphate-reducing bacteria reduce sulphate to sulphide.
- The extremely aggressive aerobic iron-oxidising bacteria (IOB) oxidise ferrous (Fe2+) to ferric (Fe3+) and destabilise the oxide layer.
Conditions favouring Microbiologically Induced Corrosion
There are many elements that play a part in MIC. All the following can contribute to the severity of MIC and the corrosion problem:
- The type and surface finish of construction materials, operating conditions including shear stress, temperature, deposition of solids, dissolved oxygen, etc.
- The type of colonising microorganisms.
- Nutrient availability and geochemical composition.
When examining the effects of MIC, we know that certain conditions will encourage its occurrence. The microorganisms that cause MIC are often found in highest concentration in crevices, stagnant zones, sediments, and damaged protective coatings. They deposit and multiply in the presence of water, with an adequate supply of nutrients, a suitable temperature range, and a wide range of pH.
Why we should care about MIC
Reducing bacteria to mitigate MIC mechanisms may sound like a microscopic issue, but MIC failures can have huge implications. It can damage the integrity of our infrastructure, add to safety concerns, and cause financial losses. It is complex (and fascinating), and affects pretty much everything around us. In short, it is a challenge that we cannot ignore.
Tony Rizk, PhD, Ex-Honorary Reader at Manchester University, and Course Lead for ICorr’s new MIC Training Courses, says:
“Microbiologically-influenced corrosion is a major problem in industrial systems and has been responsible for a number of high-profile failures, including the Prudhoe Bay Oil Spill, Alaska in 2006 and the methane leak from a South California storage facility in 2015.
“It is estimated that around 20% of all corrosion failures are due to MIC. Despite this, MIC is not considered a major topic in corrosion training curricula.”
Understanding the causes and mechanisms of MIC helps us to mitigate its impacts, improving safety and sustainability of our infrastructure.
Our next article in this series will discuss real-life impacts of MIC. In the meantime, if you would like to up your game in the least understood phenomenon of corrosion, please email the Institute of Corrosion for information about our new MIC Training Course.
Articles in This MIC Corrosion Series:
Bio-Corrosion Basics: What Is MIC Corrosion?
Real Life Impacts of Microbiologically Influenced Corrosion
The Unique Challenges of Managing Microbiological Corrosion
Introducing ICorr’s Microbiologically-Influenced Corrosion Courses