Institute News
On 1st November 2023 the Institute held its first in-person AGM since 2021, due to the prevailing COVID pandemic. We were hosted by the Birmingham Science Museum (Thinktank). ICorr greatly appreciates all those who travelled to help make the event a success and, of course, offers its thanks to the staff of Thinktank, that provided some magnificent catering on the day.
In support of the AGM, the Midlands Branch organised a very well received, multi-subject corrosion awareness event covering automated CUI monitoring case studies, corrosion control solutions for reinforced concrete and steel, holistic corrosion data management and recent advances in NDT and corrosion training by our key training partners Corrodere and IMechE. This followed on from a similar successful mini-conference held by the Midlands Branch in February 2023 at the Birmingham Council Chambers.
Our keynote speaker was Ryan Finlayson, discussing Holistic Data Management. The founder of Rysco Corrosion Services Inc. and the Rysco Group of Companies, a corrosion-focused set of businesses with international operations, services, and manufacturing. From their humble beginnings, working from his garage in 2007, Ryan and his growing team have continued to pursue technical innovation and value-added solutions for all their worldwide clients. Prior to Rysco Corrosion, Ryan worked for 7 years with Baker Hughes in their production chemistry division, learning about applied field techniques for many applications, including corrosion prevention. These experiences helped him prepare the solid foundations of Rysco by placing an emphasis on the importance of continuing education, knowledge sharing, and employee development.
Rysco are a long-time contributor to international corrosion associations, and champions these to evolve and improve the corrosion industry. With a formal education in engineering and business, Ryan is a promoter of skill acquisition within his companies and a firm believer that supporting educational initiatives build strength. The company recently hosted the Aberdeen Corrosion Awareness Event in August 2023, attended by more than 50 delegates.
Prafull Sharma then spoke to us on Automated CUI Monitoring Case Studies with examples from around the Globe, including UK upstream and downstream applications. Prafull is an inventor and the Chief Technology Officer of Corrosion Radar, with core expertise in Industry 4.0, Industrial IOT, Predictive Analytics and Sensing Technologies. Prafull obtained his PhD from Cranfield University UK. He has over fifteen years’ experience in industrial automation and sensing technology development, particularly for the Energy, Aviation and Chemical industry. He is also credited with over fifteen international patents and innovations. Corrosion Radar’s sensor technologies are now being widely adopted with support funding from Saudi Aramco Energy Ventures (SAEV) and NZTC (formerly OGTC – Oil and Gas Technology Centre) in the UK.
Christian Stone later joined us from Concrete Preservation Technologies (CP Tech).
Christian’s time has focused on the research and development of Corrosion Management Systems, working on surveying and corrosion in RAAC as a part of the University of Loughborough RAAC Research Team, and supporting teams all over the world to manage the corrosion risks of their structures. Christian has published on many aspects of corrosion and leads research to support the NHS in their issues with corrosion in RAAC.
His most informative talk focused on concrete repairs using galvanic anodes, consideration of their performance, and acceptance in reference to MCHW 5700 (Specification for Highway Works), and in particular, understanding the science around patch repairs.
In the afternoon, it was the turn of our two key external training partners – Corrodere and IMechE to update us on their recent activities. Both organisations have long-term relationships with ICorr and provide training to many hundreds of applicants every year, leading to formal certification by ICorr assessors following periods of industrial experience.
Lucy gave a great insight into the world of a training partner and how it interfaces with industry, the community, prospective course attendees, and its relationship with ICorr, particularly with regard to online training provision, which has grown enormously with the COVID pandemic. Lucy has worked with the Corrodere Academy for many years and is involved with its daily operations, development, and global growth.
She was instrumental in the expansion of the Train the Painter’ programme around the world.
Dale from IMechE then closed our AGM technical programme with a very informative talk on recent advances in corrosion and NDT training, describing their excellent classroom teaching facilities at their Sheffield and Fife operations. IMechE now provides NDT and coatings training, examinations, and NDT consultancy services around the world.
As ICorr Manager, he now supports all ICorr-related training development, providing secure IT systems for their new online training options and their day-to-day training centre operations. Dale is a driven and passionate individual who is keen to ensure training-related projects are delivered on schedule and within agreed budgets. He has been working closely with ICorr since 2020, with his involvement ramping up in 2021 and 2022, leading to him taking on the ICorr Manager role earlier this year from Chris Kirby, (now a Business Coach and Strategic Business Developer at REBLADE of Denmark).
Each year, the Institute of Corrosion bestows a range of internationally renowned awards in recognition of excellence in corrosion science and engineering and to reward outstanding service to the Institute and the wider corrosion community. Our Institute was extremely proud to announce the selection of Trevor Osborne FICorr (Hon), NACE Corrosion Specialist, for this year’s H.G. Cole Award and presented at the AGM. The most prestigious award is made in recognition of exceptional services to the development of the institute.
It is only awarded on an occasional basis, reflecting the highest possible level of commitment of the recipient to the activities of the institute. The inaugural H.G. Cole Award (in the form of a poignard) was presented to Charles Booker in 1997 by Gwen Cole (wife of the late Henry Cole) in recognition of his many years of service as Honorary Secretary of the Institute. The modern form of the award is a plaque whose design captures the essence of the original poignard. Trevor is a Past President of the Institute of Corrosion and long-standing Chair of the Board of its commercial arm, Correx Ltd. He is Managing Director of Deepwater Corrosion Services (UK) Ltd and has worked in the Energy Industry for over 43 years, with very wide experience of corrosion control and project execution.The institute offers its sincere congratulations to Trevor on this magnificent achievement.
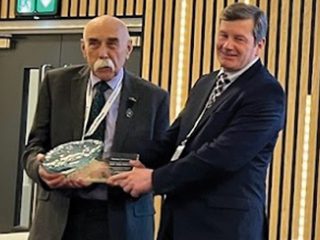
Following some excellent presentations and the awards ceremony, the day’s events closed with our formal institute AGM presented by current President Stephen Tate along with George Winning, our new ICorr Treasurer.
This part of the days programme included a detailed update of our account’s status, along with the latest updates to our re-organisation and growth plans, to be presented formally to ICorr Council in February 2024.
Our congratulations were also offered to our Lionel Shreir, Paul McIntyre and U. R. Evans Award winners for 2023, along with our thanks for special contributions made to the Institute by: Bill Hedges, Brian Goldie, David Harvey, Gareth Hinds and Tony Collins – Council Members who have all offered exceptional service and helped make it an outstanding year in terms of taking the Institute forward to the next phase of its development both internationally and within the UK.
Full details of all proceedings, discussions, and votes taken may be found in the ICorr Website Members Area at: www.icorr.org/members-area/
Thanks to all for supporting this unique event in the institute’s calendar. The relaunched Midlands Branch is planning further technical meetings for later in the session. We are pleased to welcome Prafull Sharma to this committee. For other general inquiries about events or supporting the branch, please feel free to get in touch with Bill Whittaker, Midlands Chair, at midlandschair@icorr.org
All the AGM + Feb. 23 Mini-Conference technical presentations may be found at: www.icorr.org/midlands/ please scroll down to Local Technical Programme – 2023 Presentations.
CAPTIONS:
Midlands Chair Bill Whittaker and CPSM introducing the Conference and ICorr AGM.
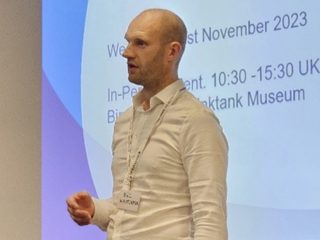
Speaker 1 – Ryan Finlayson, CEO & President, Rysco Corrosion Services, Alberta, Canada.

Speaker 2 – Prafull Sharma Inventor and the Chief Technology Officer of Corrosion Radar.
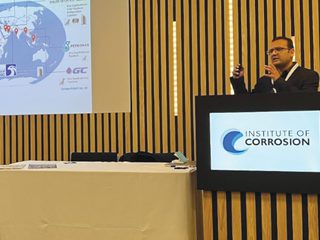
Speaker 3 – Christian Stone, technical consultant, Concrete Preservation Technologies.
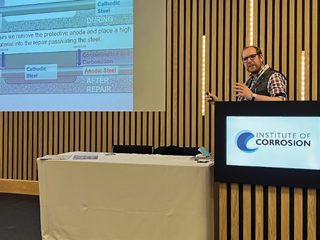
Speaker 4 – Lucy Pavia, Commercial Director of Corrodere.
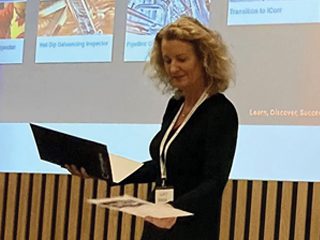
Speaker 5 – Dale O’Reilly, ICorr Manager & Business Systems Manager of IMechE.
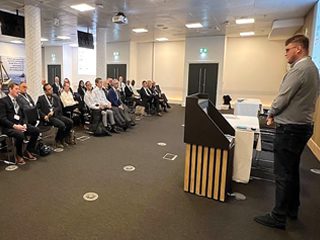
Speaker 6 – Stephen Tate, ICorr President.
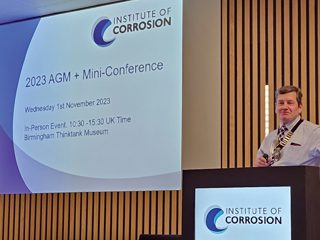
Speaker 7 – George Winning, new ICorr treasurer.
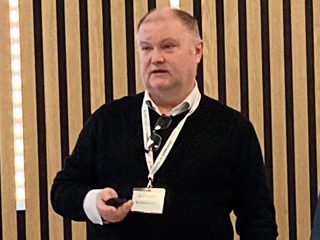
H. G. Cole Award to Trevor Osborne at AGM with President Stephen Tate.
Latest News
Join PRCI and ETH Zurich as they present: A Critical Review of the Science and Engineering of Cathodic Protection of Steel in Soil and Concrete.
Presenter: Ueli Angst, ETH Zurich
Presenter: Markus Buchler, Schweizerische Gesellschaft fur Korrosionsschutz (SGK)
Host: Gary Choquette, PRCI
This webinar will cover the following:
• The underlying chemical and physical processes that are responsible for cathodic protection.
• The implication of AC, DC was well as combined interference conditions.
• A new procedure for assessing effectiveness of CP of pipelines under time variant interference.
Not able to attend? Register anyway to automatically receive a link to the webinar recording to view on-demand at your convenience.
Attendance is limited to the first 500 registrants to join the webinar. All remaining registrants will receive a link to view the webinar recording.
After registering, you will receive a confirmation email containing information about joining the webinar.
Institute News
The North West Branch held an online event on 11th October 2023 covering reinforced autoclaved aerated concrete (RAAC) – a material currently very much in the news. The talk was led by Chris Atkins of Mott MacDonald and approximately 50 people logged in and participated with a number of questions.
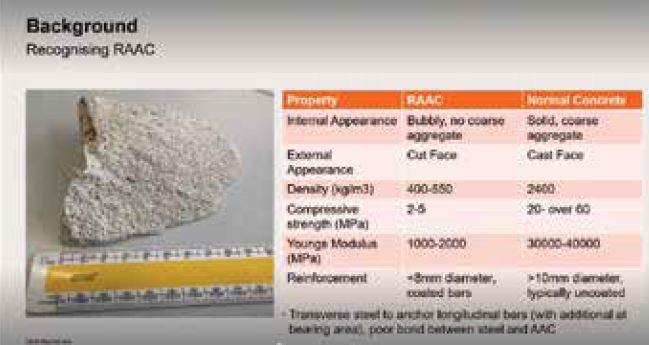
Chris Atkins is Technical Principal at Mott MacDonald where he has worked for over twenty years. Chris is part of a team dealing with all aspects of materials and corrosion work for clients in a range of sectors. He is a Chartered Engineer, a Fellow of the Institution of Civil Engineers, a Fellow of the Institute of Corrosion and an ISO 15257 Level 4 cathodic protection specialist.
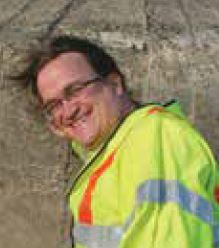
The Branch also held an event at the University of Manchester School of Materials on 29 November focusing on ICorr career development and building a student / Young ICorr chapter.
The event also included the ICorr NW Branch end of year social event. Watch the ICorr NW Branch page for more details
https://www.icorr.org/northwest/ and get in touch with Greg.Brown@mottmac.com if you require further information.
CAPTION:
Identification of RAAC.
Institute News
The branch held its final webinar of the summer on 14th September, when Esteban Amiranti, Business Development Manager at CM BEASY Ltd., presented “Corrosion Data Management, 3D Digitalisation and Digital Twin.”
The first technical session of the 23/24 season was held on 12th October at branch’s usual venue, the Lancaster Hall Hotel, Bayswater, when Simon Daly, a consultant with Safinah Group in Gateshead, gave a presentation on “Increasing the use of sensor technology to monitor coating performance.”
Simon’s current role involves providing consulting services to clients, ranging from specification writing assistance through failure investigations and root cause analysis to providing expert opinions to their energy and infrastructure clients. He has a B. Eng. (Hons.) degree from the University of Leeds as well as qualifications in marketing and international sales management. He is an AMPP-certified Senior Corrosion Technologist and a professional member of ICorr, with over 30 years’ experience in the protective coatings field.
Simon explained that recent years have seen significant improvements in the use of remote sensors for the measurement of corrosion, and also for categorising the corrosive environments in which facilities operate. Access to remote sensing has never been more important since the restrictions imposed on many assets during the COVID 19 pandemic, but with the benefits come challenges. The paint industry has been brought up with the human eye as the primary means of condition surveying. Simon posed the question “Will sensors ever be able to replace the flexibility and detail this ultimate sensor technology can provide?”
His presentation focused on the use of sensor technology to remotely determine coating performance in service. The topic of Corrosion Under Insulation (CUI) was used to highlight some of the features and benefits of coating performance sensors, compared to other types of sensors focusing on the presence of moisture or the loss of wall thickness.
Sensor technology is ideally suited for areas where the paint condition/level of corrosion cannot be seen. Examples of this includes immersed areas, inaccessible internal surfaces, inaccessible external surfaces such as beneath insulation, and areas where the risk to humans of surveying is too high.
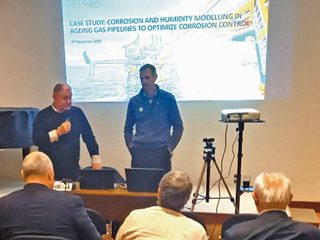
Simon Daly presenting his talk on ”increasing the use of sensor technology
to monitor coating performance.”
Using CUI as an example we can see that we can continuously measure:
• The driver – the presence of moisture in the insulation which may ultimately give rise to a corrosive environment which causes the issue.
• The cause – the time of wetness and the coating condition are both critical in contributing to ultimate failure.
• The consequence – a loss of wall thickness resulting in reduction in fitness for service.
Historically, measurement of different parameters to determine the integrity of the paint film has required visual observations and/or direct contact, but in the case of insulated service this is not possible, so we must rely on the sensor technology alone to tell us what is going on beneath the insulation and cladding, this presents a specific challenge in terms of introducing such a technology to the marketplace in terms of establishing the necessary high degree of confidence in the technology.
Simon then considered what a potential validation of such systems could look like to address the issue of confidence required to replace historic visual inspection much favoured by safety practitioners and regulators, and what might be some of the challenges encountered along the way?
There was a lively discussion on the floor, Simon was thanked for his talk, and presented with an ICorr pen.
At the November technical meeting, Steve Hodges, Intertek, gave a presentation on “The application of CO2 corrosivity, and humidity, modelling to gas pipeline internal corrosion management.”
Steve is a Chartered Engineer and a member of the Institute of Materials Minerals and Mining. He has a B.Eng. (Hons.), Materials Science and Engineering, University of Wales, Swansea, and an MSc in Corrosion Science and Engineering, from UMIST. He started his corrosion career in NZ undertaking corrosion consultancy and contract research before joining CAPCIS (now Intertek CAPIS), in Manchester. Over a 20-year period Steve has consulted to the oil and gas, petrochemical, mining, and power generation industries in some 18 countries, and was a guest lecturer on Corrosion Management and RBI on the University of Manchester’s MSc course for 8 years. He works predominantly in the areas of: corrosion modelling, corrosion/integrity management, materials selection, and fitness for service.
Steve Hodges presenting on “the application of CO2 corrosivity, and humidity, modelling to gas pipeline internal corrosion management.”
Steve’s presentation was essentially a case study of the assessment of a selection of pipelines that formed part of a network of 1000’s of km of gas and gas condensate pipelines, and some lessons learned from this.
While there were many similarities to the pipelines in the field network, the ‘one size fits all’ corrosion management approach in place had not been adequately controlling internal corrosion, as evidenced by historical in-line inspection data. A series of studies were undertaken combining both CO2 corrosion rate modelling (including basic flow modelling) and humidity modelling, along with analysis of historical operational and intelligent pig data.
In some instances, there were cost savings to be made with the cessation of batch corrosion inhibitors, in others, more onerous controls were required. However, the main takeaway from this series of studies was that the pipelines, though notionally the same, could not be considered as one in terms of degradation or corrosion management.
After the Q and A session, Steve was thanked for his talk, and given an ICorr pen as is usual for London Branch speakers.
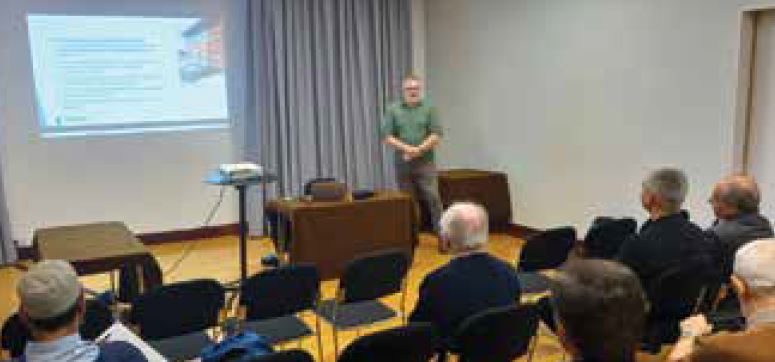