The cart is empty!
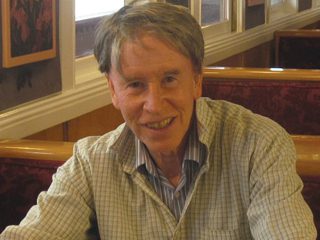
Fellow’s Corner – Douglas Mills
Douglas Mills undertook PhD research on anti-corrosive coatings at Cambridge University and has worked on and off in this field since. After spells at the BNF Metals Technology Centre and the Nuclear Power Company, in recent times he has worked in academia, and apart from teaching materials, he has continued to conduct and supervise research in the field of electrochemical methods for application to coatings, particularly studying and developing the electrochemical noise method. He was for fifteen years the Technical Secretary of the Institute of Corrosion and is also involved in standards development.
Douglas Now Lays Down His Story:
I have had an interest in archaeological corrosion ever since I did work in this area many years ago at the British Non-Ferrous (BNF) Metals Technology Centre in Wantage. This was “An examination of artefacts brought up from the seabed after 262 years”. In 1707 several ships of the line from a fleet of twenty one under the command of Sir Cloudesley Shovell, hit the rocks of the Scilly Isles during a fierce storm and sank. This included the flagship HMS Association. In 1969 a team of divers under the overall control of Roland Morris recovered many artefacts. The BNF was given a Royal Society grant to examine these, and it fell to me to carry out much of the work. Conducting chemical analysis as well as metallographic studies, enabled us to find out (and comment on) the type of corrosion, the nature of the corrosion product and the extent of corrosion. Also, the composition and metallurgical structure of the metals/alloys were compared with similar alloys used today. The items included, brass dividers a bronze cutlass handle lead musket balls and silver pieces of eight as well as lead pipe, pewter platters, a copper spike, and (bronze) ship’s bells. (There was also bronze cannon although my work did not extend to examination of these).
I did this work under the direction of Hector Campbell. one time editor of the British Corrosion Journal, with whom the 70page report was written.
Much later I became involved with the Maritime Museum in Gdansk.
I was able to pass this report over to Kasia (their corrosion expert). The museum had bits from two ships (“Copper Ship” and “Solen”) which sank in the Baltic a similar length of time ago). On the metallurgical side, the composition of many of the alloys used was surprisingly close to what might be used today and many were also reasonably pure for example.
• Lead musket balls: afforded an interesting comparison with musket balls from the Swedish warship Wasa, visible in its entirety in museum in Stockholm, which sank some 60 years earlier in the Harbour there. This was possible because the original size and weight of musket balls was known and hence (assuming linear) we could work out the corrosion rate and compare them. What was found was that sea water conditions in the Scilly Isles (clean and turbulent) afforded a less aggressive environment than Stockholm harbour (polluted) led to about half the rate of corrosion.
• Brass dividers: These had undergone hardly any corrosion; the points made of iron had rusted away completely (bimetallic corrosion), and maybe they provided galvanic protection in the early stages. But it was the fact that the brass was single phase and contained some arsenic (a useful inhibitor of dezincification) that probably saved the dividers.
• Bells: one from HMS Romney (probably!) and one from HMS Association. These, despite similar composition (two phase: one copper rich and one tin rich), had corroded in quite different ways with one phase being attacked in one bell and the other phase in the other. Interesting polarisation / potentiostatic work done in the lab revealed that the two bells had probably been subjected to different environmental conditions – half of one bell having been buried in mud while the other bell was freely exposed to sea water.
• Pieces of eight: The interest here was in developing a more efficient cleaning method compared with the normal one which was lengthy and removed significant amount of silver, achieved partly by using an electrochemical method.
Protective Coatings and Electrochemical
Assessment Methods
This kind of research i.e., towards understanding long term corrosion and its prevention, has relevance today to both the storage of nuclear waste and conservation. The afore mentioned Kasia and I have collaborated in developing an electrochemical assessment method for corrosion protective coatings. The specific interest here is in how do you keep things in the museum environment from continuing to corrode? But there are also ancient artefacts outside like statues. The most common approach is application of
thin, invisible organic coatings. Getting the right coating is quite a challenge as the appearance must not to be altered. The Museum at Gdansk had a bell and bowls which had been protected by these thin transparent coatings. How do you assess such coatings? One approach is to use Electrochemical measurement techniques like DC resistance or Electrochemical Noise. Some recent work done in Northampton University tested four such coatings and concluded that Paraloid (conservation grade acrylic lacquer) coatings were the best. But only if you applied two thin (typically
10-20mm) coats.
Other Discoveries
Moving back to the discovery phase on a more local level i.e., people discovering archaeological items in the earth, the father of a friend found a large cannon ball in the south of England which I was invited to have a look at. It had a thickish layer on the outside and this interestingly was not iron based but contained large amounts of lead.
The inside of the cannon ball was very likely cast iron, based on its hardness and the calculation of density (between 6.8 gm/cc and 7.5 gm/cc. Cast Iron has a density of 7.3 gm/cc.)
• Outer lead casing – why was the outer lead put on? Was it a corrosion protective layer? What was the environment that caused the more noble lead to corrode so extensively? (apparently faster than the musket balls in the sea, as all the lead exterior was destroyed). Was it pure lead or some lead alloy which was more corrodible? Maybe the smoother lead surface assisted in the firing (that seems very plausible). One possibility is that it was never used in anger but was lost while being transported. Such cannon balls were used on big ships (even as early as the Mary Rose, Henry VIII’s flagship, from the early 16tH century) So it could have been travelling between the Arsenal and Portsmouth when it “fell off a cart!”
In summary lots of questions raised and only speculative answers! This is the fascination with any investigation of archaeological corrosion. It leaves plenty of room for the Imagination!
References:
1. H. S. Campbell and D. J. Mills Marine Treasure Trove – A Metallurgical Examination Metallurgist & Materials Technologist October 551 (1977).
2. Mills, D.J.; Schaefer, K.; Wityk, T. In-Situ Evaluation of the Protectivity of Coatings Applied to Metal Cultural Artefacts using Non-Destructive Electrochemical Measurements. Corros. Mater. Degrad. 2021, 2, 120–132. https://doi.org/10.3390/cmd2010007.
3. Schaefer, K.; Mills, D.J. The application of organic coatings in conservation of archaeological objects excavated from the sea. Progress in Organic Coatings Volume 102, Part A, January 2017, Pages 99-106.
Brass dividers
(almost no corrosion).
Lead musket balls with varying rates of corrosion according to submersion condition.
Pieces of eight after electrochemical cleaning.
Cannon Ball (weight 4 kG (9 lbs) Diameter 11cm (density 6.8-7.5) with Corrosion Product about 1-2 mm thick.