Fellows Corner
This series of articles is intended to highlight industry-wide engineering experience, guidance and focused advice to practising technologists. It is written by ICorr Fellows who have made significant contributions to the field of corrosion management.
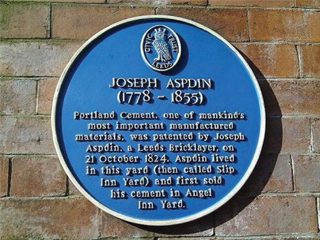
1824 and All That – A Celebration of The Bicentenaries of CP and PC
Paul Lambert, Head of Materials and Corrosion Technology at Mottmac
On January 22, 1824, the Philosophical Transactions of the Royal Society in London received a paper entitled ‘On the corrosion of copper sheeting by sea water, and on methods of preventing this effect, and on their application to ships of war and other ships’. The author was Sir Humphry Davy, and it describes a study with his colleague Michael Faraday into what we now know as cathodic protection, which celebrates its 200-year anniversary in 2024. It was many years later before the true value of cathodic protection was recognised for the protection of buried and submerged steel structures. It was championed by the formation of the Texas-based Mid-Continent Cathodic Protection Association in 1938, which by 1943 had evolved into the National Association of Corrosion Engineers (now AMPP) in the USA.
But that is only half the tale. On October 21st 1824, a bricklayer in Leeds patented a new formulation of hydraulic binder for mortar and concrete which he called Portland cement due to its similarity to the popular structural stone, especially when mixed with beach sand. Portland cement eventually dominated the manufacture of all concrete worldwide.
200 years on, the long-term durability limitations of Portland cement concrete are regularly made good by the application of cathodic protection, making 2024 a very important year for those involved in reinforced concrete and its remediation.
Happy 200th birthday to Cathodic Protection and Portland Cement.
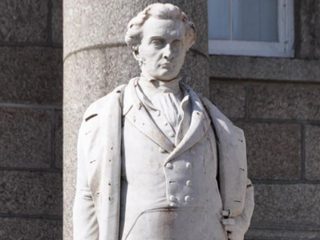
Sir Humphry Davy of Penzance (1778 – 1829).
Photo courtesy of Pen with Local History Group
https://corrosion-doctors.org/Corrosion-History/CP-History.htm
Industry News
Floating production storage and offloading (FPSO) units are on the upward trend in the oil and gas industry because of their flexibility to meet changing demands in an unpredictable market. Yet, without good preservation strategies during construction and delivery, FPSO fabricators and owners can be in for a negative surprise when they encounter corrosion problems during FPSO commissioning or thereafter. VP Technologies offer practical and effective solutions to avoid these unwanted corrosion-related downtime episodes to promote smoother commissioning and better durability.
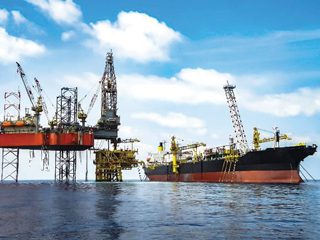
A Corrosive Environment
FPSO topside equipment is often built near ocean ports and spends the rest of its service life in a marine environment. High temperatures, humidity, and salt spray create a perfect atmosphere for corrosion propagation. To make matters worse, certain types of equipment must be flushed or hydrotested during construction and commissioning, introducing corrosives that threaten to compromise the internal integrity of the equipment. While corrosion consequences can be drastic, a few simple preservation strategies in key areas will go a long way toward preserving equipment until the time of commissioning.
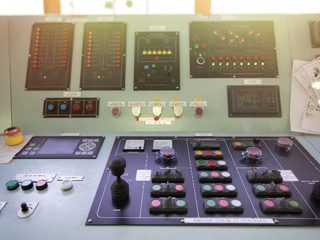
Preserving Electricals and Electronics
Electricals and electronics are the brains and nerve centres of a FPSO. Fortunately, electronics and electricals can be protected using VpCI® emitters which are available in multiple sizes—from the VpCI®-101 Device that protects 1 ft³ (28 L) of space to the VpCI®– 308 pouch that protects 35.3 ft³ (1 m³)—and release Vapor phase Corrosion Inhibitors that fill the enclosure, adsorbing on metal surfaces as a protective molecular layer.
Protection During Hydrotesting
Products such as those in the VpCI®-649 Series can be added to the hydrotest water for protection during hydrostatic testing and can be dosed at higher concentrations for extended periods of preservation. These hydrotest additives are both film-forming and vapor-phase corrosion inhibiting for protection of hard-to-reach areas inside valves or systems that are capped subsequent to hydrotesting.
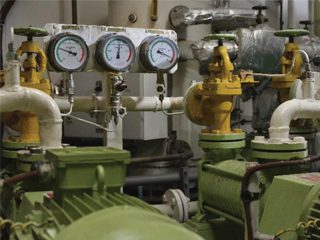
Preserving Tanks, Vessels, and Flow Paths
Another means of internal protection is to apply VpCI®-337 or CorroLogic® Fogging Fluid VpCI®-339 . Inhibitors into flow paths of gas turbines and other rotating equipment. They also work inside tanks, vessels, and other enclosed voids that could otherwise be difficult to protect.
External Protection
Turbines and other equipment fogged with VpCI® Technology are often wrapped in VpCI® Films such as VpCI®-126 HP UV Shrink Film and MilCorr® VpCI® Shrink Film—both to protect equipment externals and to trap Vapor phase Corrosion Inhibitors inside the equipment.
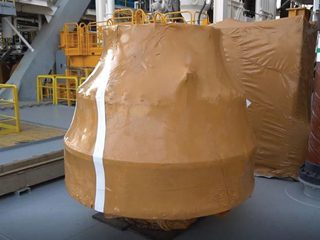
Source: cortecvci.com
Industry News
The CORINJ sidestream
system is designed to
measure corrosion and
chemical efficiency in a
continuous way, even
when inline monitoring
points are not available.
The CORINJ sidestream is
custom built based on
customer requirements
and Specifications. The
system can be integrated
into any system and devices can be serviced quickly and easily without having to conduct live breaking containment retrieval work.
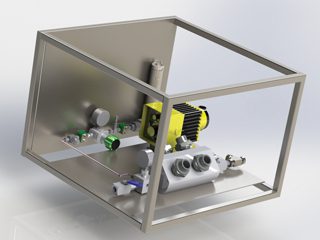
Monitoring Options
The sidestream has various options, you can choose from 2 to 10 monitoring points that include different types of probes and
corrosion coupons.
Assembly
The unit’s main block has different ports for various types of monitoring. The ports have NPT union fittings, which let you screw in and seal the devices.
H2S Monitoring
The CORINJ sidestream offers continuous ‘real-time’ H2S monitoring through a side-stream unit. If you want to monitor suspect, or known H2S issues this side-stream is ideal as it can be tied into the exact point on a specific system or wells.
ER Probes
ER probes are used to provide live corrosion rate readings or to gather and store data of corrosion rates and metal loss. The probes can collate data via logging equipment or can be connected to a transmitter which feeds back to the client DCS to provide live
data feedback.
Corrosion Coupons
The corrosion coupons are aligned with the inner wall of the sidestream. They measure corrosion rates and pit depths by metal loss over a known time period.
Bio Probes
Sessile bacteria attached to the bio studs can be collected and analysed to check the efficiency of the chemical injection systems or biocide regimes using Bio Probes in oil and gas production.
Continuous Flow
This is key to a sidestream working effectively. The outlet of the side-stream is usually routed back downstream in the system where the pressure is lower, so the flow is continuous.
Source: https://corinj.com
Industry News
Innovative Dual Sensor System:
CorrosionRADAR: LR introduces a dual sensor system- Corrosion and Moisture Sensor, offering a total range of 50 metres for each sensor. This dual-sensor approach enhances the system’s ability to detect and monitor corrosivity rate with higher accuracy than ever before.
New Features and Enhancements:
-
Battery-Powered System: CorrosionRADAR: LRoperates on a battery-powered system, providing flexibility and ease of installation in various environments.
-
LoRa Long-Range Transmission: With a data transmission range exceeding 1 km, CorrosionRADAR: LR ensures efficient and reliable data communication.
-
The system comes with a Bluetooth Low Energy (BLE) tablet option for
data retrieval and commissioning.
-
Risk Analytics Dashboard: Users can now leverage a comprehensive Risk Analytics Dashboard, available on both Cloud and On-Premises platforms, that can be connected to plant dashboards.
-
Upgraded Features: CorrosionRADAR: LRincludes upgraded features, such as the CUI Risk API 581 assessment, improved corrosivity rate models, and more sensitive early detection algorithms.
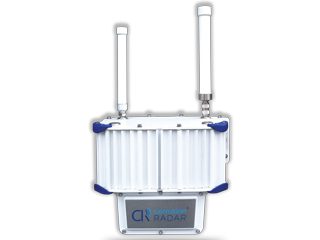
Source:
https://www.corrosionradar.com
Institute News
This industry leading course provides direct access to professional membership of ICorr, for those with relevant experience. Corrosion management, failures and remediation commonly occur throughout all branches of engineering where metals are part of the structure or process. FOCE is a corrosion course that covers the basic principles of corrosion that are needed by engineers to understand why and how failures occur, actions that can be taken to manage the ongoing corrosion and/or remediate the structure, and options to prevent further corrosion, where possible. The course is presented as a series of modules, starting with essential background information about the corrosion process and then applying the basic principles to common engineering metals, including stainless steel, aluminium, and copper alloys.
Both the general and the different types of localised corrosion such as crevices, pitting, bi-metallic corrosion, etc., is considered. Common atmospheric and immersed conditions, re-bar in concrete, high-temperature atmospheres, water treatment, buried pipes, etc are considered to understand corrosion.
Corrosion management strategies, including material selection, cathodic protection, surface preparation, coatings, chemical treatments, inhibitors, etc., are included in the course.
The role of the corrosion engineer is described and includes investigation of failed components, inspection, and testing of samples, with practical examples and case histories included in the course notes.
As a classroom-based course, FOCE is provided in English by an experienced, practicing corrosion consultant. A copy of the training material is provided to each attendee. Questions and active participation are encouraged throughout the course, as many participants enjoy learning about the additional real-life examples that are provided by fellow attendees. Fun quizzes are held each morning so both the candidates and the tutor can assess their progress during the week on an ongoing basis. One-on-one sessions can be arranged where a student has a specific module requirement.
The learning modules are given over four intensive days, and candidates for the examination on the final day are encouraged to revise the material each evening to ensure that they understand the course content.
At the end of the course, all attendees are given a Certificate of Attendance, which shows that they have been present for all
the modules.
After passing the examination, participants receive a
Certificate of Achievement, which demonstrates that they
have received sufficient corrosion training to apply directly for a Professional grade of Membership of ICorr, such as TICorr or MICorr, depending on the other requirements of
the membership grade.
Previous attendees of the course have ranged from complete beginners in corrosion (zero previous knowledge) to practicing Corrosion Consultants and some of the comments received from participants are given below.
Please note that FOCE specifically geared for professional membership is not a Cathodic Protection or Protective Coatings Inspector type course and does not provide these qualifications. Those courses are available separately through ICorr’s specialist training providers and further details are available on the
ICorr website.
ICorr also offers many other specialist courses in Microbial Corrosion, Oil and Gas related corrosion topics, intumescent coatings, etc. Details of all ICorr courses are available on the Institute website.
The next FOCE course will be held at Corrosion House in Northampton 15-19th April 2024.
FOCE course cost is currently £1650 + VAT and includes a copy of the course notes, lunch each day plus tea and coffee.
The course fee must be paid in full before the delegate can attend the course. Potential delegates can fill in the application form on the website and contact ICorr for making payments.
Additional dates in 2024 will be posted in Corrosion Management magazine and on the ICorr website:
https://www.icorr.org/fundamentals-of-corrosion-for-engineers/
Recent feedback from delegates
- Great course, which I will certainly recommend to others.
-
The (redacted) project and myself have definitely gained as a result. With the knowledge gained I have been identifying issues on site and poor practices that are now being addressed. As a result Line Managers have sent me to undertake checks of the Civil Engineering works in areas I do not normally inspect.
-
I really enjoyed the course – you have a great teaching style, very clear and logical, it made the material easy to follow.