Ask the Expert
Preventing Chloride Stress Corrosion Cracking (CSCC) and Degradation in Austenitic Stainless Steels
Dr Shagufta Khan, Ph.D., FICorr
- How can we prevent chloride stress corrosion cracking
(CSCC) in austenitic stainless steels?
Chloride stress corrosion cracking (CSCC) is one of the most common reasons why austenitic stainless-steel pipework and vessels fail under service in the chemical processing and petrochemical industries however these lower stainless grades can be subject to a wide range of deterioration modes as detailed below.
Stainless steels (SS) must contain a minimum of 11 Wt % chromium, and this level of chromium allows formation of a passive surface oxide that prevents surface corrosion in an unpolluted atmosphere. Increasing Cr content to 17 to 20 %, as typical of the austenitic SS, or to 26 to 29 % as possible in newer ferritic SS, greatly increases the stability of the passive film. Examples of common grade modifications for different applications are given below in Table 1.
AISI Euronor11z DIN British
Description
Standard
304 1.4301 X5CrNil 8-10 304S31
The general-purpose grade, widely used where good formability and corrosion resistance are required.
304L 1.4306 X2CrNi l 9-11 304Sl 1
As 304 but with lower
carbon content to Minimize carbide precipitation during welding.
301 and 1.4310 Xl 2CrNi l 8-10 301S21
Higher strength versions of 304 that are often cold worked to give higher strength.
303 1.4305 XlOCrNiS18-9 303S31
General purpose grades with sulphur or Selenium added
to improve machinability.
321 1.4541 XlOCrNiS18-9 321Sl2
321S31
As 304 with an addition of titanium to prevent carbide precipitation during welding.
347 1.4450 X6CrNiNbl8 -10 347S3l
As 304 with addition of niobium and or tantalum to prevent carbide precipitation during welding.
316 1.4401 X5CrNiMol7-12-2 316S31
As 304 but with molybdenum
added to increase resistance to localised corrosion in marine and chemical environments.
316L 1.4404 X2CrNiMol7-13-2 316Sl 1
As 316 but with lower carbon content to minimise carbide precipitation during welding.
Austenitic SS can have an excellent combination of mechanical strength, corrosion resistance, ease of fabrication, and cost effectiveness. The most widely used stainless steel grades are austenitic, with 74% production of total world SS production. Various grades of austenitic steels have excellent corrosion resistance in many environments, resisting attack by the atmosphere and by many industrial gases and chemicals.
The pitting and crevice corrosion resistance of stainless steel is primarily determined by the content of chromium, molybdenum and nitrogen. Manufacturing and fabrication practices, e.g. welding, are also of vital importance for the actual performance in service. A parameter for comparing the resistance to pitting in chloride environments is the
PRE number (Pitting Resistance Equivalent).
The PRE is defined as, in weight-%
PRE = %Cr + 3.3 x %Mo + 16 x %N
Many of these stainless steels have good strength at high temperatures which accounts for their wide use at elevated temperatures. They are also among the primary materials selected for use at extremely low temperatures, since they do not become brittle compared to other types of steel. AISI 304 and 304L are the most popular grade of austenitic SS. Although austenitic SS are used as corrosion resistance alloys for many applications, there are many cases of failure in aggressive environments. Some of the corrosion failure types that stainless steel remains susceptible to include:
-
Crevice corrosion (common, often seen at piping flanges and under identification labels).
-
Galvanic/bimetallic corrosion (common, must have compatible fixings/fasteners).
-
Pitting corrosion (very common especially under labels, can occur in storage or at fabrication site prior to service).
-
Stress corrosion cracking (common at more elevated temperatures and where there are residual stresses).
-
Weld decay (less common, varies with process chemistry and applied chemical treatments).
SCC
Stress corrosion cracking is a time-dependent phenomenon that occurs in a metal when certain metallurgical, mechanical, and environmental, conditions are present at the same time. SCC is a somewhat sneaky type of degradation because it occurs at stress levels within the design stress range. The cracking can be:
- Intergranular (IG): passing through the grain boundaries.
- Trans granular (TG): passing through the grain matrix.
- A mixed mode (TG and IG) of SCC,
Depending on the microstructure of the material exposed to the atmosphere and the nature of the environment. SCC is caused by weak tensile stresses, typically below the macroscopic yield stress. Figure 3 describes the necessary conditions for SCC to occur. Austenitic stainless steels may undergo SCC in hot, concentrated chloride solutions, chloride-contaminated steam, and in HTHP (high temperature and high pressure) demineralised water in presence of oxygen.
Among all types of environmentally assisted cracking of austenitic stainless steel, CSCC is perhaps the most common. Many
incidences of failure have been reported due to CSCC, e.g.
condenser tubes in heat exchangers, swimming pool components,
parts used in marine applications, under insulation of external piping
in a refinery, and medical devices. Chloride stress corrosion
cracking of patch repaired elbow in hydrocarbon service is shown
in Figure 4.
API 571 defines chloride stress corrosion cracking as follows: “Surface initiated cracking of 300 series SS and some nickel-based alloys under the combined action of tensile stress, temperature, and an aqueous chloride environment. It is also referred to as chloride cracking”. All 300 series SS are highly susceptible to pitting and CSCC where additional stresses exist. Welds in 300 series SS normally contain some ferrite, producing a duplex structure that is usually more resistant to CSCC than the base
metal though.
Factors Affecting CSCC: Several environmental factors, like chloride concentration, temperature, pH, dissolved oxygen can have profound effect on CSCC. Nickel content of alloy and applied or residual tensile stresses can also affect CSCC.
Chloride Concentration: CSCC is caused by inorganic chloride ions. It is known that organic chlorides do not directly cause CSCC. In industrial processes, hydrolysis or thermal decomposition of organic chlorides may produce ionic, inorganic chlorides. Therefore, organic chlorides can also cause CSCC. The components experiencing higher tensile stresses require lower Cl- concentration for initiation of SCC. There is no lower limit of Cl- concentration for crack initiation. A few ppm Cl- in the process stream can concentrate to hundreds of ppm where evaporation takes place. Cl- can further concentrate at the base of pits when pitting corrosion starts. Increasing levels of chloride will increase the likelihood of cracking and greater than 50g/L of chloride in process fluids would certainly give cause for concern for 300 series SS.
Temperature: Increasing temperatures increase the cracking probability if tensile stress and an aqueous chloride solution and/or external chloride build-up are present. Although exceptional cases have been reported. Highly cold worked or sensitised materials may undergo cracking at lower temperature or even at ambient temperature. Usually cracking occurs at metal temperatures above about 50 °C and this temperature limit is considered the guideline for fixed equipment in the refining industry.
Tensile Stresses: Tensile stress may be applied or residual. Crack initiation and propagation are guided by the aggregate of both external (i.e. applied) and internal residual stresses. Residual stress by definition is the tensile, or compressive force, that exists in the bulk of a material without application of an external load. The bending of steel plates during pipe construction, localised plastic deformation during handling, and differential cooling through the wall thickness and along the surface during rolling, are all potential sources of residual stresses in pipeline steels. Regions with different microstructures and chemical segregation at the grain boundary may also generate residual stresses in metallic components. In the absence of proper control measures, residual stresses produced during the fabrication phase can significantly contribute to SCC. Non-stress-relieved welds, highly stressed, or cold worked components, such as expansion bellows, are highly susceptible to cracking.
pH of Environment: Cracking is more likely to occur at lower pH. However, SCC usually does not occur at pH values below 2. Uniform corrosion generally predominates at such highly acidic range. CSCC tendency decreases toward the alkaline pH region.
Dissolved Oxygen: It is observed that oxygen dissolved in the water increases tendency to SCC. Other oxidisers in addition to oxygen (e.g., CO and CO2) can also enhance CSCC. It is unclear what oxygen concentration must be reached before CSCC starts.
Nickel Content: Alloys tendency to SCC is affected by nickel content in a profound way. Stainless steels with a nickel content of 8 % to 12 % have greatest susceptibility toward SCC. Alloys with nickel contents above 35 % are highly resistant, and alloys above 45 % show near immunity in refining applications, but severe conditions may lead to cracking in these alloys.
Prevention of CSCC: Prevention of CSCC by applied coatings is common in the energy sector although can be more difficult to achieve with smaller diameter piping. Reduction of tensile stress can be used to avoid CSCC. This can be achieved by applying compressive stress by shot peening. A suitable high-temperature stress relief heat treatment of 300 series SS after fabrication will reduce residual stresses. Care should be taken that stress relief heat treatment should not result in sensitisation.
Changing process conditions is the best approach for minimizing CSCC. The acidity and corrosiveness of the process fluids can be controlled by addition of chemicals such as acid neutralizer and corrosion inhibitors. Effectiveness of corrosion inhibitors must be assured before use through laboratory test. Upgrading the metallurgy may also be opted to avoid SCC. A duplex SS might be considered for this purpose. Duplex SS has almost equal ratio of austenitic and ferritic grains in its microstructure. Duplex SS have very good corrosion resistance and they can withstand higher tensile stresses. Their resistance to pitting corrosion is also very good. Super austenitic SS have higher content of Ni so they show good resistance to cracking in chloride environments.
Low chloride-content water should be used during hydrotesting, followed quickly by thorough dry out. Designs that create stagnant regions should be avoided as chlorides can concentrate in such region. An effective external coating (e.g. epoxy phenolic coatings up to 120 oC and TSA above this temperature limit) should be applied to SS piping and equipment prior to insulating or adding piping identification. Shrink-wrapped PVC labels, coatings, or label adhesives with high levels of chlorides or other halogen ions should be avoided.
References
- J. F. Grubb, T. DeBold, J. D. Fritz, Corrosion of Wrought Stainless Steels, in: S. D. Cramer, B. S. Covino (Eds), Corrosion: Materials, Vol 13B, ASM Handbook (tenth edition), ASM International, Ohio, 2005, p. 54-77.
- A. J. Sedriks, Corrosion of stainless steels, second ed., John Wiley and Sons, New York, NY, 1996.
- ANSI/API Recommended Practice 571 Third Edition, March 2020, Damage mechanisms affecting fixed equipment in the refining industry.
- M. Hussain, T Zhang, S Khan, N Hassan, Stress corrosion cracking is a threat to pipeline integrity management, Corrosion and prevention 2020, Perth Australia organised by Australian corrosion association.
- S. Khan, Doctoral thesis “Corrosion of austenitic stainless steels in nitric acid at trans passive potentials: effect of material and process parameters, 2016, Homi Bhabha National Institute, India.
- Chidambaram Subramanian, chloride induced stress corrosion cracking of repaired pipe elbow from an oil refinery: forensic analysis.
CAPTIONS:
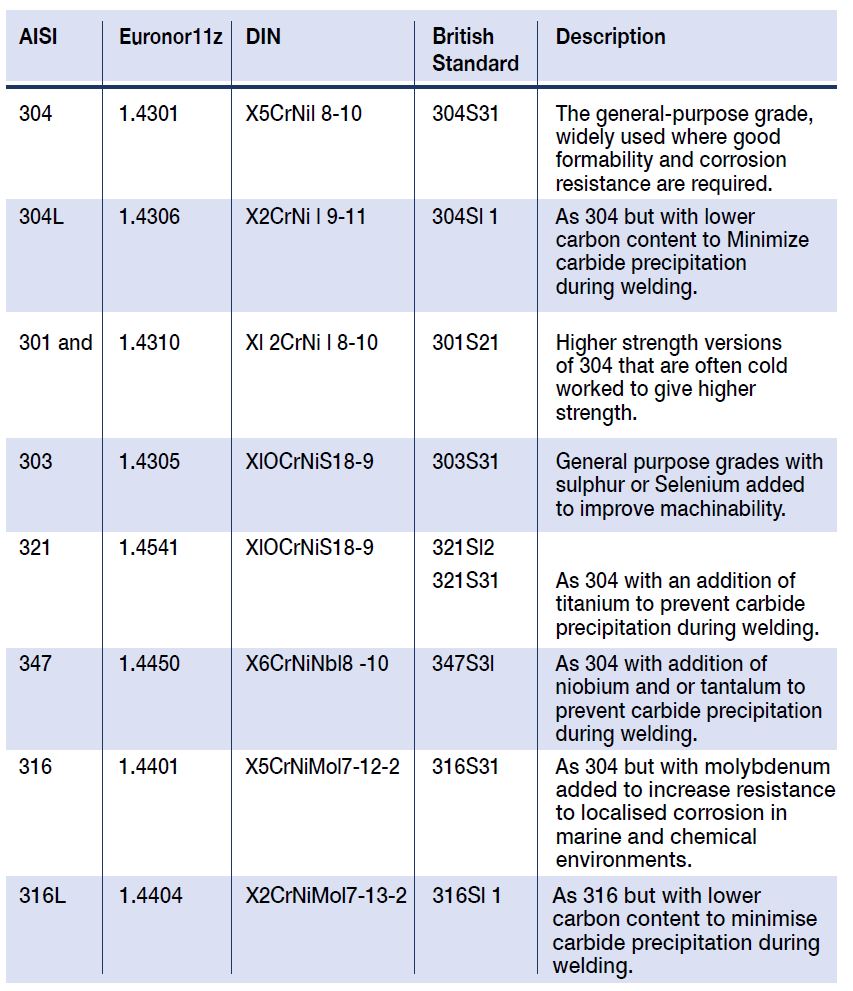
Table 1: Widely Used Grades of Austenitic Stainless Steel
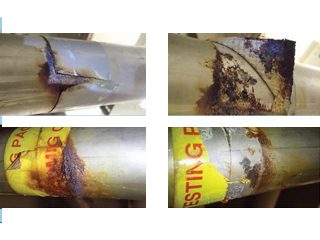
Above: Figure 1: Commonly Observed 316L Grade Stainless Pitting Under Labels.
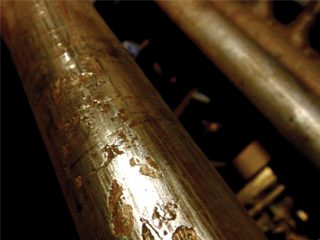
Left: Figure 2: Photo of Corrosion Under Labels (CUL) Seen After Label Removal.
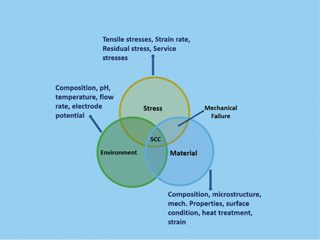
Figure 3: The Necessary Conditions for SCC to Occur in Austenitic Stainless Steel.
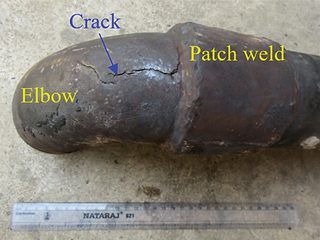
Figure 4: Photo of Patch Repaired Piping Elbow from Hydro Cracking Plant (Corrosion Management, Issue 174).
Industry News
Antonella Sardinella and Mariaenrica Frigione of University of Salento have provided an overview of the bio-based/sustainable materials proposed for the development of original coatings to protect concrete works in their recent review.
Traditional coatings involve the use of synthetic materials that are often toxic for human beings and the environment. Research is going on around the world for the development of new sustainable coatings made with bio-based or non-toxic materials using green technologies.
Following are qualities of a good coating:
- Chemical inertness against substrates.
- Good stability against acids, alkalis, UV radiations, heat, and oxidation.
- Permeability to water vapor (the underlying concrete must still “breathe”).
- Adequate adhesion to the substrate.
- Non-toxic and non-dangerous to the environment and human beings.
In the field of construction, the sustainable products proposed as potential protective coatings for concrete substrates can be divided into: (i) geopolymers and (ii) natural bio-based substances, such as agricultural waste, oil, wax, cellulose and others.
Geopolymers
The low curing temperatures of geopolymers and their ability to be produced from a wide range of raw materials, including industrial waste (also known as secondary raw materials, or SRM), make them sustainable materials. Reusing (or recycling) solid waste, such as fly ash (FA), slag, and other active byproducts, can actually produce geopolymers by the alkaline activation of aluminosilicate precursors.
Coatings Based on Agricultural Waste
Agricultural organic waste, i.e., products that are constantly generated, can be profitably exploited for different purposes, giving an economic value to the waste and reducing the costs of its disposal.
Vegetable Oil and Fatty Acids
Recently, vegetable oils have been used in technologies meant to preserve a substrate (like concrete), which can be a viable substitute for synthetic materials and a sustainable approach. The chemical structure and film-forming properties of oil and its derivatives actually make them useful in this field.
Proteins
Very recently, proteins have been proposed to develop coatings with good hydrophobic characteristics. Lysozyme, for instance, is composed of a microfiber network containing amyloid which, when applied to the surface of a metal, adheres to it and increases its resistance to corrosion.
Cellulose
Cellulose, the most abundant natural polymer on earth, is a low-cost renewable resource: it is generally recognised as a potential candidate for the production of green superhydrophobic coatings.
Plant-Based Wax Coatings
Starting from materials of vegetable origin dispersed in water, Morrissette et al. developed superhydrophobic self-cleaning coatings for different applications.
Advantages of These Coatings
These are harmless to humans and the environment. They can be applied using the same techniques and methods as for traditional coatings, without additional costs. Waste materials can be used. Additionally, the studies carried out so far have especially highlighted the excellent protective properties offered by these materials, not considering any difficulties in the production processes and possible increased costs.
Challenges in Commercial Application
Higher production costs, scale-up problems, demand for high quantities of bio-based raw materials, competition with food and feed for the supply of raw materials, technological barriers, and including industrial conversion for new productions are some of the barriers that slow down the introduction of these materials to the market.
You can refer below article for more details:
Antonella Sarcinella and Mariaenrica Frigione, Sustainable and Bio-Based Coatings as Actual or Potential Treatments to Protect and Preserve
Concrete, Coatings 2023, 13(1), 44;
https://doi.org/10.3390/coatings13010044
IMAGE FROM: The Concrete Beneath the M32 Flyover, Inset, Some of the Corrosion Found During Safety Checks.
Industry News
Under the UK’s Network Rails ‘Access for All’ programme, ongoing over the last 15-20 years, we now have step-free, accessible routes at more than 200 railway stations across Britain to provide an obstacle free, accessible route to and between railway platforms. The improvements have been funded by the Department of Transport, which also selects the stations. In Scotland, ministers recommended stations for inclusion to the Secretary of State for Transport.
In 2006, the DfT published the Railways for All Strategy, outlining the UK government’s intention to improve access to the rail network for disabled people across Britain. A key part of this strategy was the Access for All Fund. The Access for All programme was launched in 2006 to deliver accessible routes at stations. The standard design included new lift shafts and footbridges. Examples of rail inclusivity and accessibility improvements include:
-
Lifts that are automatic and give an audible tone when the doors open and close.
-
Staircases and platform edges that have tactile warning surfaces.
- New ramps and footbridges with lowered handrails.
Often, these are replacing well maintained historic railway footbridges that have been in place for over 150 years without significant corrosion issues. Dumfries Station is a fine, well-detailed example of a mid-19th century station, built in the Italianate style, a listed structure since 1981.
Refer: Access for All – Improving Accessibility at Railway Stations Nationwide – Network Rail
Unfortunately, many new structures are seen to be failing prematurely due to poor design detailing, e.g. water traps,
a lack of water drainage points, inferior coatings, and poor material selection. Winter de-icing programmes are
accelerating structural damage. The salt attracts moisture from the environment to the carbon steel substrate, which speeds
up the oxidation (rusting) process.
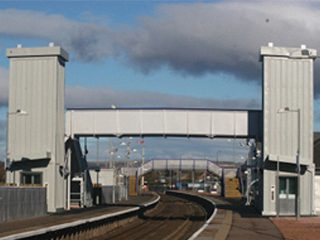
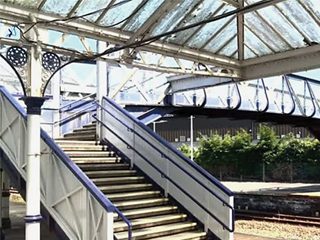
Photo 1: Typical Original Non-Accessible Footbridge without Lifts.
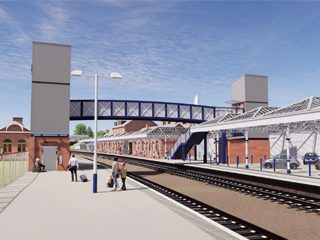
Photo 2: (a) Dumfries-Station-Original Footbridge (b) Dumfries-Station Replacement Footbridge 2024 – Credit: Network Rail.
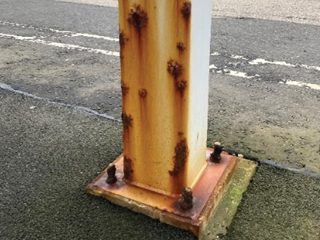
Photo 3: Corrosion Around Us – Network Rail Footbridge, Dyce, Aberdeenshire (a) Footbridge Stairs, (b) Support Stanchion and
(c) Underside of Footbridge – Credit Stephen Tate.