The cart is empty!
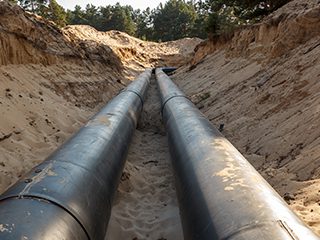
Pipeline Corrosion Detection and Management – An Essential Overview
Innovation, Integrity, and Expertise in Pipeline Sustainability
Pipeline corrosion is a and inescapable phenomenon that represents one of the most significant challenges for many industries. Manifesting in a variety of forms, it impacts longevity and integrity of liquid and gas transportation systems. Consequently, significant investment is made in the detection and identification of pipeline corrosion and its management.
In this article, we provide an overview of what is – and will continue to be – a critical field in pipeline management.
Why Is Management of Pipeline Corrosion So Important?
When poorly managed, the ramifications of pipeline corrosion can be extensive and influence safety, environmental, and economic aspects of an operation.
Economically, pipeline corrosion leads to immense costs related to maintenance, repairs, and lost efficiency. For example, there are estimated to be around 2.15 million kilometres of oil and gas pipelines around the world, and corrosion is the most important factor in pipeline integrity. In the United States alone, the annual yearly cost of pipeline corrosion is estimated at $7 billion.
A real-life example of the potential economic impact of pipeline corrosion was demonstrated in the Alaska Pipeline system where, in 2011, severe corrosion led to a spill of approximately 200,000 gallons of oil – despite pipeline corrosion caused by faulty coating having been identified 20 years earlier.
From a safety perspective, the stakes are incredibly high. Corrosion can compromise the structural integrity of pipelines, leading to failures that might cause explosions, fires, and oil spills. These incidents not only endanger human lives, but also have devastating effects on the environment. In a study of 1,063 pipeline accidents, 21% were found to have been caused by corrosion.
Effective detection and management of pipeline corrosion is not simply a case of technical and regulatory compliance. Fundamentally, it is an ethical imperative regarding the safeguarding and wellbeing of employees, surrounding environments, and local communities. Consequently, regulatory bodies across the globe impose stringent requirements for corrosion management to mitigate these risks.
Key Methods for Detecting Pipeline Corrosion
Detecting, measuring, and monitoring pipeline corrosion involves a multifaceted approach that includes non-destructive testing, electrochemical probes and sacrificial coupons
Corrosion coupons – sacrificial metal strips exposed to pipeline conditions – are analysed to determine corrosion rate within the pipeline.
· Non-Destructive Testing (NDT) Methods
NDT methods help to provide a more comprehensive view of pipeline corrosion. Techniques such as acoustic emission (AE), magnetic flux leakage (MFL), and liquid penetrant inspection enable early detection without damaging pipelines. Advanced NDT methods include:
- Visual Inspection, despite being the most basic form of corrosion detection is a very valuable inspection tool. It involves regular surveys and manual inspections of accessible pipeline sections. Of course this can only be used on the external surfaces of pipelines.
Techniques that allow both internal and external inspection:
- Radiographic Testing (RT), is an extension of visual testing involving the use of X-rays or gamma rays to capture sub-surface images that reveal corrosive damage.
- Ultrasonic Testing (UT), which employs high-frequency sound waves to detect imperfections or changes in material properties similar to the use of UT in medical applications.
- Electromagnetic Testing (ET), which utilises electromagnetic induction to detect surface and sub-surface irregularities
In addition, Intelligent pigs – often referred to as ‘Smart Pigs’ – can travel internally along pipelines to detect anomalies using methods like ultrasonic testing and magnetic sensors, providing comprehensive data regarding the condition of the pipeline. They can often provide inspection of almost 100% of both the internal and external surfaces of a pipeline.
Other forms of robots such as drones and crawlers can also be fitted with the above technologies to carry out inspections in locations that are difficult to reach.
The integration of modern technologies such as the Internet of Things (IoT) and predictive analytics represent a revolutionary step in corrosion management. Data is continuously transmitted in real time to be analysed so that potential failure points can be identified. This will allow pre-emptive repairs and significantly reduce downtime.
Corrosion coupons – sacrificial metal strips exposed to the internal pipeline conditions – are analysed to determine corrosion rate within the pipeline.
Electrochemical Probes can be inserted into a pipeline to measure the corrosivity of the fluid inside it. They can provide a continuous output of corrosion rates that can be fed to a pipeline control room and corrosion engineers.
Pipeline Corrosion Prevention Techniques
When taking action to prevent corrosion of pipelines, utilising a combination of techniques and methods is crucial. Such methods include:
· Cathodic Protection
An electrochemical process that reduces the oxidation within metal pipelines by making them the cathode of an electrochemical cell. The main cathodic protection techniques are to use sacrificial anodes or impressed current cathodic protection. This technique is primarily used to protect the external surface of a pipeline – usually in combination with coatings and linings.
· Coatings and Linings
Coatings and linings can be be made from organic, metallic and inorganic materials. They provide an anti-corrosive layer that acts as a barrier between the pipe material and the corrosive environment. When designing pipelines to minimise the risks of corrosion, it’s crucial to select materials that are inherently resistant to corrosion. They can be used on both internal and external surfaces of pipelines.
· Corrosion Inhibitors
Corrosion inhibitors are the most widely used method for protecting the internal surfaces of pipelines. They are added to the pipeline fluids and absorb onto the metal surface to provide a barrier to corrosion.
Future Trends in Corrosion Management of Pipelines
Corrosion detection and management of pipelines has evolved rapidly in recent years, and will have to continue to do so – to tackle new corrosion threats such as the transportation of hydrogen and carbon dioxide from carbon capture plants. From regulatory frameworks to materials science to sensing technologies, corrosion science and corrosion engineering continue to advance.
· Advances in Material Science
The development of new alloys and composite materials is pivotal in combatting pipeline corrosion. These materials are engineered to endure harsh environments and aggressive chemicals that accelerate corrosion in conventional materials.
Additionally, the incorporation of nanotechnology into material fabrication has given birth to nano-coatings and nanocomposites that enhance durability and resilience by improving barrier properties and reducing molecular wear and tear.
A key breakthrough has been in the use of graphene, which acts as an impermeable barrier to gases and liquids, minimising oxidation, which is a key factor in corrosion.
· Enhanced Sensing Technologies
Technological innovations in sensing technologies are revolutionising corrosion management by enabling more precise and comprehensive monitoring capabilities. Modern sensors now incorporate features like higher resolution, greater coverage areas, and advanced data analytics to detect and predict corrosion sites before they manifest into larger issues.
For example, fibre optic sensors provide real-time data on pipeline integrity by detecting changes in temperature, pressure, and structure. These sensors are immune to electromagnetic interference, making them versatile for diverse environments. Moreover, drones equipped with hyperspectral imaging sensors can perform aerial surveys to detect corrosion under insulation or in inaccessible areas.
· Regulatory and Standards Evolution
The evolution of international standards and regulatory requirements is crucial in pushing the envelope of what is technologically feasible and economically viable in corrosion management. Updating of standards ensures that the newest technological advances and best practices are implemented to safeguard public and environmental health.
Advancing Knowledge and Expertise in Corrosion Management
As the complexities of pipeline corrosion evolve, so too must the expertise of those tasked with managing it. The Institute of Corrosion (ICorr) plays a crucial role in this dynamic landscape. By sharing knowledge, expertise, and best practices, ICorr ensures that corrosion professionals are well-prepared to tackle current and future challenges. We are also at the forefront of policy discussion, giving our members a voice in the future regulation of the industries in which they operate (as demonstrated by our sponsorship of the Reuse, Repair, Replace Conference).
Our commitment to education and continuous professional development is evident through our industry-leading training programs. These are designed and delivered to elevate the technical competence of personnel across the corrosion industry. Through initiatives such as our membership pages, social media, Corrosion Management magazine and more, we provide a collaborative environment in which all our members (and the wider corrosion community) can benefit from insight and innovation in corrosion science and corrosion engineering.
In an era where technological advancements are critical to economic viability and environmental stewardship, the role of institutions like the Institute of Corrosion is indispensable. Through its efforts, ICorr not only contributes to the global economy but also fortifies the industry’s capacity to manage corrosion effectively, safeguarding infrastructure and ecosystems alike.
To learn more about the Institute of Corrosion, our membership schemes, and our comprehensive training packages, email admin at ICorr.