The cart is empty!
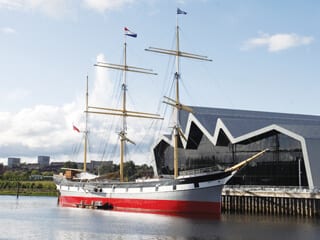
Enhancing Corrosion Resistance: The Synergy of Coatings and Cathodic Protection
The Benefits of Combining Coatings with Cathodic Protection
Coatings and cathodic protection are often used in conjunction with each other when designing and implementing corrosion protection systems. But why?
Corrosion is one of the most significant challenges in maintaining the integrity of structures, installations, components, and mechanical systems. It involves the deterioration of materials (primarily metals) through chemical reactions with their environment, leading to the formation of oxides, hydroxides, or sulphides. The result is compromised structural integrity and functionality of critical systems.
The factors that influence corrosion include environmental conditions, material properties, and electrochemical activity, with the presence of an active metal surface being a crucial element in the corrosion process.
Mechanisms of Corrosion Protection
To combat corrosion, it is essential to transform active metal surfaces into passive ones. This process can be achieved by reducing the potential of the metal surface through the application of a protective current, a technique known as cathodic protection.
Cathodic protection effectively halts or significantly slows down electrochemical changes, preventing corrosive attacks. How does cathodic protection work? There are two primary methods of implementing cathodic protection:
1. Sacrificial Anode Cathodic Protection (SACP)
This method involves attaching a more easily corroded ‘sacrificial’ metal to the protected metal. The sacrificial anode corrodes in place of the protected metal.
2. Impressed Current Cathodic Protection (ICCP)
In this method, an external power source supplies a current to the protected metal, countering the corrosive current and thus preventing corrosion.
The Role of Coatings in Corrosion Prevention
Coatings serve as another effective strategy for mitigating corrosion. They function as a protective layer, barrier, or sacrificial layer over the metal surface. These coatings enhance the material’s surface characteristics, protect against corrosive environments, and reduce the risk of failure.
Coatings are particularly beneficial in environments where structures are exposed to dynamic loads, such as marine structures, where they help prevent corrosion fatigue and stress corrosion cracking. However, in extremely aggressive environments, the use of coatings alone might not be sufficient.
The Synergy of Coatings and Cathodic Protection
Combining coatings with cathodic protection offers a robust solution for enhancing metal resistance against corrosion. This dual approach provides several benefits, including:
· Increased Durability
The combination extends the operational life of structures and components by providing multiple layers of defence against corrosion.
· Cost-Efficiency
It reduces the need for frequent maintenance and repairs, thus lowering overall lifecycle costs.
· Design Optimisation
By mitigating corrosion risks, it allows for the use of lighter materials, reducing fabrication and transport costs, and contributing to sustainability goals.
Advanced Coating Technologies
Recent advances in coating technologies have led to the development of nanocoatings and nanocomposite coatings, which offer superior protection in harsh and complex environments. Examples of these advanced coatings include Nickel-Alumina (Ni/Al2O3), Nickel-Silicon Carbide (Ni/SiC), Nickel-Zirconia (Ni/ZrO2), and Ni-Graphene (GPL). These nanocomposite coatings are designed to withstand both mechanical wear and chemical corrosion, providing enhanced protection for components in demanding applications.
These advanced coatings have been subjected to rigorous testing, including ASTM B117 salt spray testing, to validate their performance under corrosive conditions.
The Bottom Line
In summary, the primary objective of industrial coatings is to prevent corrosion and withstand hazardous chemicals. Selecting the right coating and supplementing it with cathodic protection can significantly enhance the durability and reliability of structures.
Advanced coating technologies and remote monitoring systems further improve corrosion resistance, offering bespoke solutions for specific applications.
By integrating these strategies, industries can achieve cost-effective, efficient, and reliable protection against corrosion, ensuring the longevity and safety of critical infrastructure, and achieving significant cost savings and environmental benefits.
What Do You Want to Ask an Expert?
This article has been adapted from a question that was sent to the Institute of Corrosion and answered by Professor Zulfiqar Khan. The question was, “Why are coatings often supplemented with cathodic protection to protect against corrosion?”, and we first published Professor Khan’s answer in our exclusive Corrosion Management magazine.
If you have a question to pose to our experts, please feel free to send it to us by email, and we’ll do our best to have the answer published for you.