The cart is empty!
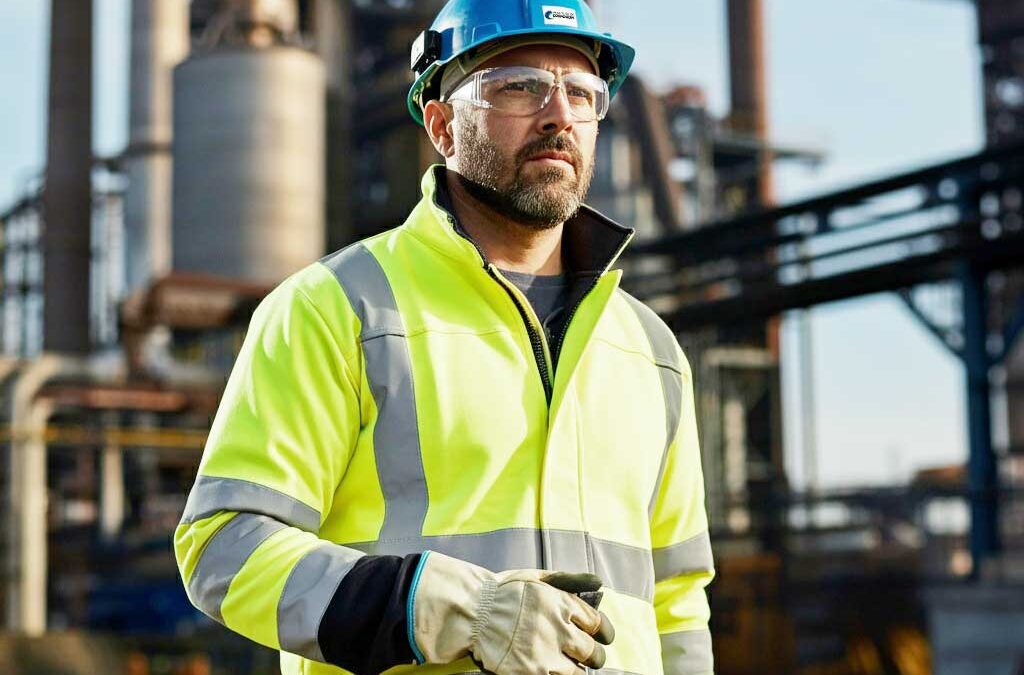
Mastering Marine and Offshore Coating Inspection: Your Guide to Qualifying at Level 1
Preparing for the Protective Coatings Inspector Level 1 Course
Protecting marine and offshore structures from corrosion is vital to the integrity of our oil and gas industry. Correctly applied and maintained coatings are a critical component in this, not only safeguarding against corrosion but also significantly extending the lifecycle of installations in harsh marine environments.
To ensure the effectiveness of coating systems, competent coating inspection is essential. Coating Inspectors are in high demand – it’s a highly rewarding role with great responsibility, and worldwide opportunities.
The Level 1 Coatings Inspection Course equips you with knowledge and skills to oversee and implement protective coatings systems. However, qualifying at Level 1 is not a cakewalk. It takes hard work and a strategic approach.
Based on feedback from previous course attendees, we’ve identified key strategies and tips to help increase your chances of success at this crucial stage of a career in coating inspection.
Preparing for the Protective Coatings Inspector Level 1 Course
You’ll be covering a lot of ground as you prepare to kickstart your career with Level 1 Coating Inspector training. Topics include:
- Protective Coating Application and Spray Painting
- Abrasive Blast Cleaning
- Coating Inspection and Inspection Equipment
- Marine Coatings
You’ll also explore QA, QC, and the basics of inspection, providing a comprehensive understanding of normative documents, corrosion of iron and steel, surface preparation for ferrous materials, and much more.
Before attending the course, we recommend that you become acquainted with its contents, and familiarise yourself with key concepts, such as tools and techniques used in the industry, how materials respond to different environmental conditions, and the protective qualities of various coatings. Having a foundational knowledge in these areas will prepare you for the deeper dive into the world of coating inspection that the Level 1 course delivers.
Best Practices for Engaging with Course Material
How you use the course materials is crucial – the right learning strategies will not only enhance your learning experience, but also make the course more enjoyable. We’ve condensed feedback into three categories:
1. Effective Notetaking and Concept Mapping
Structured note-taking methods like the Cornell Note-Taking System help you organise and summarise key information efficiently. You might also employ concept mapping by creating visual relationships between course topics – this is particularly useful when linking theory to practical applications to improve your problem-solving skills.
2. Utilising Resources Effectively
Consider the content of the course and the topics you will be covering, and supplement this with recommended reading that might include texts on materials science, corrosion protection, and coating technologies.
Don’t neglect the value of interactive tools – if you’re taking the online version of the course, these include the online modules and video tutorials, which can help to deepen your understanding of the subject matter, as well as cater for various learning styles.
3. Active Learning
Finally, participate in class discussion and workshops. Ask questions and collaborate with others – this all helps to enhance your understanding and knowledge retention.
In practical sessions, ensure that you actively seek to associate application with the foundational theories, to cement your learning and prepare you for fieldwork.
Master Your Skills During Practical Sessions
There will be opportunities to optimise your hands-on training experience in supervised practical sessions to experience the environmental and logistical challenges you’ll face in the field. You should expect structured guidance and step-by-step demonstrations in using various equipment, across realistic tasks such as evaluating surface preparations, applying coatings, and conducting post-application inspections.
To get the most from your practical sessions, you should:
- Take every opportunity to handle materials and tools; the tactile experience is invaluable
- Ask questions to clarify procedures and rationales to deepen your understanding of each task
- Collaborate with your peers to gain new insights and reinforce your knowledge
- Relate practical tasks back to the theory to help understand why certain methods are preferred
- Note how coating performance is impacted by environmental performance
Techniques for Excelling in the Exam
The exam is held on a separate day after the end of your course. However, we all know that exams can be funny things – nerves may play a part, and passing to qualify is not guaranteed. Your success depends upon preparation and exam strategy. Here are our tips to help you qualify at Level 1:
· Create a Structured Revision Plan
Allocate specific times for different topics according to their complexity and your proficiency. Stick to a consistent schedule to build a routine.
· Consolidate Revision
Break down the course content into manageable topics and review them systematically. Use summary sheets and flashcards for key terms and concepts.
· Practice Your Knowledge Recall
Test your understanding regularly by practicing with past exam questions or creating your own quizzes. This reinforces learning and identifies areas needing further review.
· Manage Your Time
Figure out how much time to spend on each question, and prioritise those that you find easiest to secure marks quickly.
· Understand Questions Before Answering
Break down complex questions to understand exactly what is asked. Only then should you tackle the answer.
Choose the Course That Suits Your Preferred Learning Style
We all have diverse preferences, schedules, and learning styles. Whether you thrive in the dynamic atmosphere of a classroom or prefer the flexibility of self-paced study, we partner with leading training providers to align with your unique educational needs and career goals:
· Classroom Learning with IMechE Argyll Ruane
Experience the immersive environment of classroom learning in Sheffield, equipped with cutting-edge facilities. IMechE Argyll Ruane offers a comprehensive five-day course that covers all aspects of Level 1 certification. This option is ideal for those who benefit from face-to-face interactions and immediate expert feedback.
· Online Learning with Corrodere Academy
Embrace the flexibility of online learning with Corrodere Academy, where you can progress at your own pace. You have 12 months to complete 40 hours of interactive, professionally curated content. This format is perfect for those who need to balance their educational pursuits with professional or personal responsibilities.
The Institute of Corrosion has chosen IMechE Argyll Ruane and Corrodere Academy as preferred training providers because they deliver the highest standards in global corrosion training.
Whether opting for classroom learning or online courses, rest assured that you are receiving top-tier training designed to equip you for the supervisory challenges of a Coating Inspector role.
Your Pass to a Successful Career as a Coating Inspector
Mastering Level 1 Coating Inspection equips you to protect marine and offshore structures from corrosion, taking a course that blends theory with practical skills. With commitment and a strategic approach, you’ll not only gain certification but also lay a strong foundation for a successful career in coating inspection.
For more information, and to discuss which course is best for you, contact ICorr’s admin team by email today.