The cart is empty!
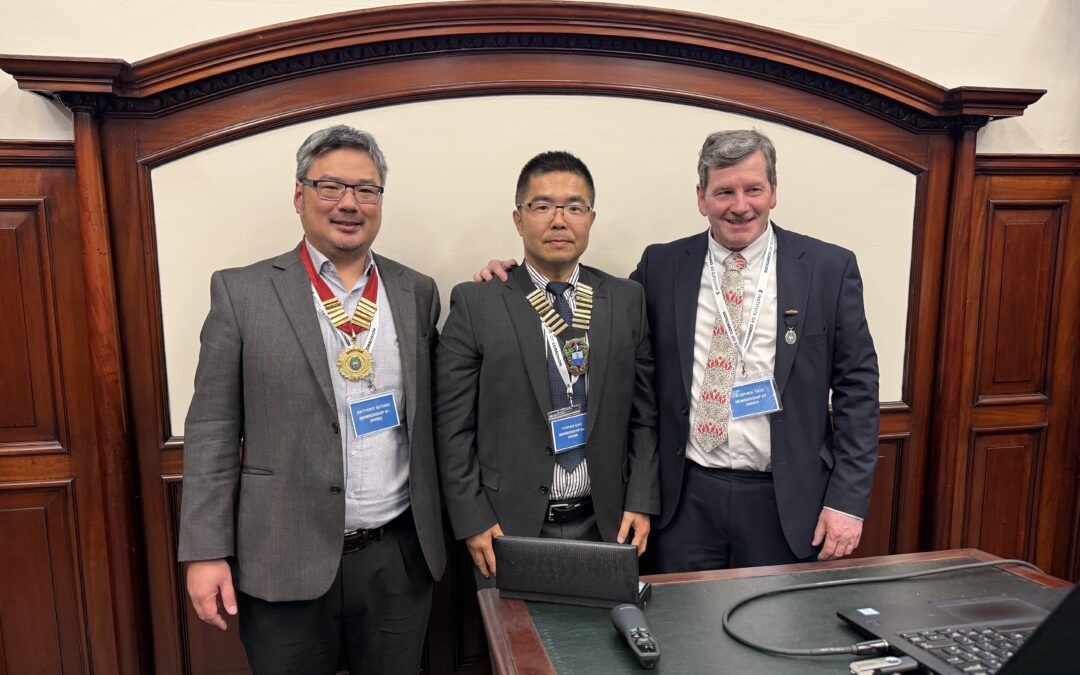
Institute of Corrosion 2024 AGM at Neville Hall
Photo 1 The Historic Lecture Theatre at Neville Hall
On Wednesday 13th November the North-East Branch of the Institute of Corrosion hosted the Institute of Corrosion 2024 AGM at Neville Hall in Newcastle upon Tyne.
The day commenced with a Technical Offshore Wind Program, followed by the AGM and concluding with an evening dinner. Almost 70 people from all over the UK attended the Technical Program and 60 attended the evening dinner, attendees included the ICorr Council, Sustaining Members, Professional members, general members and potential future members. The day was a great success with the variety of engaging content keeping the attendees entertained for almost 9 hours from start to finish.
Photo 2 The Lord Mayor of Newcastle upon Tyne Opening the Technical Program
Matt Fletcher, Chair of the North-East Branch of ICorr, opened proceedings and who was followed by the formal opening of the Technical Program by the Lord Mayor of Newcastle, who welcomed everyone to Newcastle and described how offshore wind and the project to re-paint the Tyne Bridge brought valuable jobs to the region. Lord Mayor also explained that as he did not have his “driver” available he was unable to wear his full collection of Mayoral Medals as they were too valuable to be worn in public without the extra security of his “driver”!
The Offshore Wind Technical Program then opened, consisting of 4 presentations:
Environmental considerations for offshore wind foundations corrosion protection.
Dr. Anthony Setiadi Chief Consultant / Associate Director Wood Thilsted
Photo 3 Dr Anthony Setiadi of Wood Thilsted presenting
Anthony described how the offshore wind industry growth is accelerating as the world is pushing towards renewable energy sources. These wind turbines need to be installed on foundations located in aggressive environments and are prone to corrosion if not protected and / or designed with corrosion in mind. There are various offshore wind foundation types, such as, monopiles, jackets tetrabases, gravity bases and floating structures. The presentation discussed what level of protection is required, what the options are and how would all of this impact the structural integrity throughout the design life, also how fabrication, transport and installation limitations would affect the corrosion protection design. Anthony explained how equally important, the environmental considerations need to be taken into account with respect to carbon equivalent in producing and protecting these foundations, as well as the potential byproducts expected. In discussing the creation of habitats for nature, Anthony made an interesting point, that if habitats are created on the foundations, what happens to these environments when the foundation is decommissioned in the future?
Assessment of Thermal Spray Aluminium Coating in Synthetic Seawater By Using Complementary Techniques
Dr. (candidate) Adriana Castro Vargas Research Associated – Materials Innovation Centre University of Leicester and NSIRC
Photo 4 Dr Adriana Vargas of the Materials Innovation Centre University of Leicester presenting
Adriana presented the results of her PhD that used complementary techniques, such as in-situ imaging and an analytical rotator, to understand the performance of thermally sprayed aluminum (TSA) coating in simulated marine immersion service. The experimental work involved evaluating TSA in quiescent and flowing synthetic seawater at room temperature. The coating (300µm thick) was obtained by twin-wire arc spraying of 1050 aluminium alloy on an S355 carbon steel substrate. In quiescent condition, TSA-coated steel samples were evaluated by the optical analysis of sequential images captured in-situ: (i) with defects machined before immersion (5% of exposed steel surface); and (ii) with a defect machined after 35 days of immersion (10% of exposed steel surface). When the defect is machined before the immersion, initial dissolution of iron occurs until the air-formed oxide layer degrades, the electrolyte penetrates the coating, and the aluminium surface is activated. Conversely, when the defect is created after immersion, the aluminium activates rapidly, and the system reaches the range of protective potentials (according to DNV-P-B401) providing immediate protection to the exposed steel. In flowing synthetic seawater, cylindrical coupons were tested in an analytical rotator at 50 rpm and 600 rpm for 10 days. Open Circuit Potential (OCP) and Linear Polarisation Resistance (LPR) measurements were carried out to assess the flow velocity effect and calculate the corrosion rate.
An introduction to the Offshore Renewable Energy (ORE) Catapult and its key role in advancing and derisking technology in offshore wind.
Mr. Tom Chaplin Marketing Manager Offshore Renewable Energy Catapult
Tom Chaplin provided an introduction to the Offshore Renewable Energy Catapult and described the key role it plays in advancing and derisking technology in offshore wind. ORE Catapult is one of the world’s leading offshore renewables technology centres, with an unrivalled set of test assets that aim to accelerate the creation and growth of UK companies in the offshore renewable energy sector. Established in 2013, ORE exists to accelerate the development of offshore wind, wave and tidal energy technologies in the UK. Through its world-class testing and research programmes and its unique centres of excellence, ORE works with industry, academia and government to improve technology reliability and enhance knowledge, directly impacting the cost of offshore renewable energy. ORE delivers products and services in four main areas: research, engineering, testing and validation, and supply chain growth.
Photo 5 Tom Chaplin of ORE Catapult presenting
Tom showed the scale of the ORE Catapult testing facilities showing a video of testing a 107m blade (which needed to be cut down to 100m to fit in the test facility) and the 14GW powertrain, which as a result of the testing, had its capacity increased. Tom also revealed plans to increase the capacity at ORE Catapult to be able to handle wind turbines well into the future with capability to test blades up to 150m long (and expansion potential to 180m) and a significant increase in drive train capacity to 23MW (with potential expansion to 28MW). After the presentation Tom was asked about catastrophic failure during testing, although unable to share images, Tom said it had happened and was quite dramatic. All was not lost as the fractured blade provided insightful data on blade failure to the owners
Development of ISO 25249 – Corrosion protection of offshore wind structures
Mr. Simon Daly Consultant – Energy & Infrastructure Safinah Limited
Photo 6 Questions following Simon Daly’s (Safinah) presentation
Simon described how a series of parts of a new international standard, ISO 25249, are currently being worked upon. The standard will address the issues of developing a corrosion protection approach for the protection of offshore wind farms. With the growth in offshore wind will come the need for large scale construction of assets which will be placed in a corrosive offshore environment. Whilst the corrosion of steel structures offshore is well documented through experiences in the oil and gas industry the offshore wind energy has encountered its own challenges when it comes to providing corrosion protection. The ISO 25249 standard will address key issues and develop a framework for a more standardised approach to the selection, execution and operation of a variety of different corrosion protection methods. Simon presented on behalf of the program managers for the first 5 parts of this new standard the development of which will shortly commence within the International Standards Organisation (ISO) framework. During the questions after the presentation the sharing of experiences gained in the Oil and Gas industry was discussed, it was generally agreed that to prevent mistakes from 30 years ago being repeated, experiences should be reviewed and shared. It was hoped that with more of the traditional Oil and Gas companies entering the offshore wind market that this will be more likely to take place.
Following the Technical Program the ICorr AGM took place, details of the AGM can be found in the AGM minutes. At the AGM Stephen Tate passed on the Presidency of ICorr to Yunnan Gao and Yunnan passed on the Vice-Presidency to Anthony Setiadi.
Photo 7 New Vice President – Dr Anthony Setiadi, New President – Dr Yunnan Gao, Past President – Stephen Tate
The evening saw a three-course dinner, enjoyed in the library at Neville Hall. As can be seen in the photographs, the library is a beautiful wooden clad room, with many original features such as elevated bookshelves, bookshelves hidden behind wooden doors and stained-glass windows. A jazz band played throughout the evening and the dinner was opened by the new president of ICorr – Dr Yunnan Gao.
Photo 8 Dinner in the impressive Library at Neville Hall
Feedback following the event was overwhelmingly positive:
• “NE Hospitality is famous and you certainly lived up to that.” – Stephen Tate: outgoing ICorr President.
• “Please accept my thanks for the superb organisation and excellent day yesterday.” – Brian Wyatt of CPGB and Council.
The Chair of the NE Branch of ICorr grateful thanks the NE Branch Committee for all their hard work in creating a most successful day, all are volunteers and worked tirelessly to make the event a success – Simon Daly, Patrick Johnson, David Mobbs, Bruno Ravel, Barry Turner and Josie Watson
Future Meetings
Due to a date clash with London Branch Dinner, NE Branch will now hold its Xmas (Branch) event at the end of January 2025.
There will be a tour of the Newcastle Castle Keep – the cost for which will be £20 a head.
Please contact nechair@icorr.org for further details.