Institute News
Dr. Anthony Setiadi, Chief Consultant/
Associate Director Wood Thilsted.
www.woodthilsted.com
Offshore wind industry growth is accelerating as the world is pushing towards renewable energy sources. These wind turbines would need to be installed on foundations which are in aggressive environments and would be prone to corrosion if not protected and / or designed with corrosion in mind. There are various offshore wind foundation types, such as, monopiles, jackets tetrabases, gravity bases and floating structures.
The presentation will discuss what level of protection is needed, what are the options and how would all of this impact to the structural integrity throughout the design life, also how fabrication, transport and installation limitations would affect the corrosion protection design. But equally important would be the environmental considerations that would need to be taken into account with respect to carbon equivalent in producing and protecting these foundations, as well as the potential by-products expected.
Biography
Anthony Setiadi is Chief Consultant /Associate Director with Wood Thilsted. He is an experienced materials specialist having held positions with such notable companies as INTECSEA, Saipem, Intertek CAPCIS and AMEC Nuclear. Anthony is a Chartered Engineer and holds a PhD and Bachelors degree in Material Engineering both from The University of Sheffield. He is actively involved in the design and material selection for the offshore wind industry. Additionally, Anthony is a member of ICorr’s London Branch committee, a regular speak at ICorr events and is actively involved in the Young ICorr initiative.
Institute News
The 65th Corrosion Science Symposium (CSS) was again held jointly with Electrochem2024 at Manchester Metropolitan University between the 11th
and 13th September 2024.
The symposium is always an opportunity for students and early career researchers in corrosion science from across the UK and Europe to congregate, discuss their work, share ideas and, above all enjoy themselves in a stimulating/friendly environment. This year there were 19 talks and thirteen posters, and the UR Evans award plenary talk given by Prof David Shoesmith (University of Western Ontario, Canada).
Prof Shoesmith’s research has focused on the application of electrochemical techniques, oxide/sulphide film properties, microscopic examination of the evolution and spatial
distribution of corrosion damage on a wide range of materials including copper, steels, and titanium and nickel alloys, and
the development of computational models for corrosion processes with a special emphasis on the corrosion of uranium dioxide (nuclear fuel) and nuclear waste container materials (copper, titanium and nickel alloys) under permanent waste
disposal conditions.
This year marks the centenary for the first publication of Corrosion of Metals by Ulick Richardson Evans in 1924. UR Evans is described as the father of the modern science of corrosion and protection of metals. His major contribution to the subject involved placing on a firm foundation the electrochemical nature of corrosion. As such, Prof Shoesmith’s plenary entitled Corrosion of the Spent Fuel Waste-form and Engineered Barriers in a High-Level Nuclear Waste Repository was a very fitting commemoration. He described the various intricate electrochemical investigations into the possible long-term corrosion processes within Canadian/Swedish/Finnish a deep, geological repositories. A number of key processes were addressed: (i) the evolution of exposure conditions and its effect on corrosion of the copper/steel (or iron) container corrosion barrier: (ii) the potential for hydrogen absorption by the already hydrided Zircaloy fuel cladding, and whether this rendered it an unacceptable barrier to radionuclide release if container failure occurs: (iii) the corrosion response of the spent fuel (uranium dioxide containing fission products and actinides produced in-reactor) to the evolving redox conditions inside a failed container, which will be determined by the conflicting influences of water radiolysis and the products of steel (or iron) corrosion.
This year the Shreir prize, for the best student presentation at the CSS, went to Amber Sykes (University of Leeds) for her talk entitled investigating the Influence of Porous FeCO3 Layers on the CO2 Corrosion Rate of Carbon Steel. Amber’s talk superbly described, with high level critical insights, the influence of high temperature and pressure carbon dioxide saturated environments and the of FeCO3 corrosion products on pipe walls that form dense protective layers. Utilising both experimental and numerical studies Amber assessed influence of the FeCO3 layer’s porosity and thickness on the predicted corrosion rate of the underlying carbon steel surface. A key finding was the relationship between the physical properties of FeCO3 and the protectiveness of the layer, which were also investigated using a variety of ex situ analysis techniques.
Other symposium highlights included: Alyshia Keogh (University of Manchester) gave an interesting overview of her work on the effect of aging temperature and chloride concentration on the atmospheric stress corrosion cracking of 15-5PH stainless steel. She reported that cracks found in samples aged at 450°C were intergranular whilst in samples aged at 540°C a mixed mode intergranular and transgranular mechanism was predominant. It was shown that aged 15-5PH at lower temperatures may be more susceptible to hydrogen embrittlement or that inherent mechanical properties make them more susceptible to cracking once pitting initiated.
Also, Ethan Proudlove’s (University of Leeds) presentation on the Application of Machine Learning to the Prediction of CO2 Corrosion Rates in Geothermal Systems is another honourable mention. He presented an investigation into machine learning as a tool to combat these limitations, with the aim of developing a model to emulate and improve industry applications of the existing COMSOL modelling undertaken at Leeds.
Please contact Julian Wharton should you wish to be involved in any future Corrosion Science Symposium activities: j.a.wharton@soton.ac.uk
Other symposium highlights included: Alyshia Keogh (University of Manchester) gave an interesting overview of her work on the effect of aging temperature and chloride concentration on the atmospheric stress corrosion cracking of 15-5PH stainless steel. She reported that cracks found in samples aged at 450°C were intergranular whilst in samples aged at 540°C a mixed mode intergranular and transgranular mechanism was predominant. It was shown that aged 15-5PH at lower temperatures may be more susceptible to hydrogen embrittlement or that inherent mechanical properties make them more susceptible to cracking once pitting initiated.
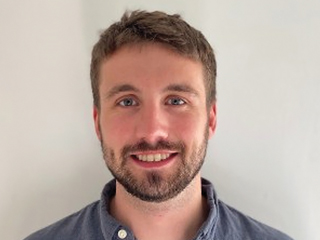
Also, Ethan Proudlove’s (University of Leeds) presentation on the Application of Machine Learning to the Prediction of CO2 Corrosion Rates in Geothermal Systems is another honourable mention. He presented an investigation into machine learning as a tool to combat these limitations, with the aim of developing a model to emulate and improve industry applications of the existing COMSOL modelling undertaken at Leeds.
Please contact Julian Wharton should you wish to be involved in any future Corrosion Science Symposium activities: j.a.wharton@soton.ac.uk
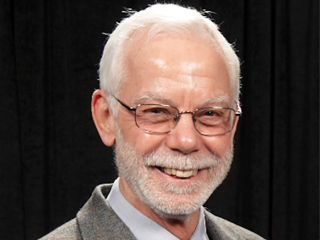
Presentation of an Engraved Sword was Made to Prof. David Shoesmith by ICorr President
Stephen Tate.
Amber Sykes
PhD Student – University of Leeds.
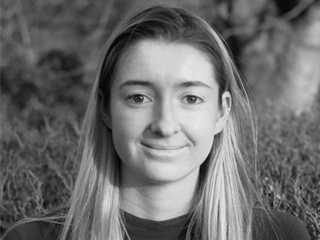
Amber Sykes
PhD Student – University of Leeds.
Ethan Proudlove
MSc in Aerospace Engineering at University of Leeds.
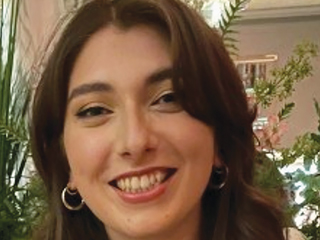
Alyshia Keogh PhD Student with Airbus at
The University of Manchester.
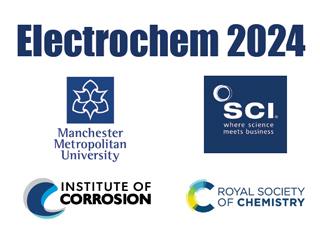
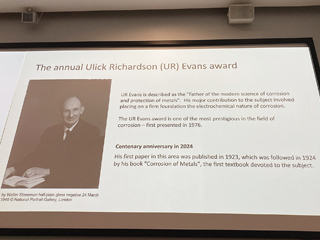
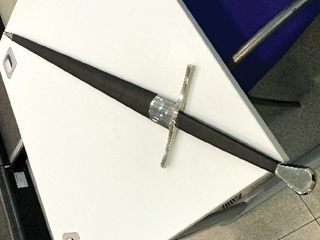
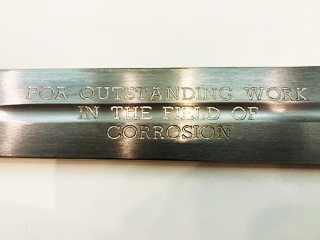
Institute News
By Prof Gareth Hinds, FREng, FIMMM, FICorr, FNACE, Senior NPL Fellow and Science Area Leader, Electrochemistry Group, National Physical Laboratory
The 2024 edition of the annual EuroCorr conference took place in Paris in the first week of September. The atmosphere in the city was unique even by Paris standards, with the Olympics having just ended and the Paralympics going on at the same time as the conference.
The streets were extraordinarily clean, the transport network was running like clockwork and service was delivered with a smile – not things one necessarily associates with the French capital! There was a real buzz around the city, which really put on a show of all that it has to offer, and the good vibes seemed to be absorbed by the conference delegates.
The theme of the conference was ‘A step forward in societal awareness of material degradation issues’. I am not sure this rather bold statement was actually achieved, as there was little interaction with anyone outside of the traditional corrosion community, but it was at least a laudable sentiment. It is encouraging to see that attendance at the conference continues to grow following its post-Covid dip; 1244 delegates were present (including 183 exhibitors), an increase of 35% on last year’s event in Brussels. It’s also worth noting that, for the first time, China provided the third highest number of delegates behind the host country and Germany, with the UK the fourth most represented country at the conference.
The venue was the Palais des Congrès, a large conference centre on the Place de la Porte Maillot, just a short walk from the Champs Elysées and the Arc de Triomphe. This excellent location was within walking distance of a range of quality hotels at reasonable prices. Any fears prior to the event that the presence of the Olympics
would drive up accommodation costs thankfully proved to be completely unfounded.
As usual, a vast array of technical topics was covered during the week, with 24 parallel sessions organised by each of the European Federation of Corrosion (EFC) Working Parties, 15 joint sessions on topics including hydrogen, electric vehicles, and medical implants, and 6 workshops covering everything from sustainability in the chemical process industry to certification in corrosion protection. It is always impossible to attend every talk that’s of interest, so navigating the programme is important. The printed version was comprehensive, but grouping the talks by room rather than in chronological order was not particularly helpful. The absence of an online conference app also appeared to be a backward step.
In general, the quality of the technical presentations was excellent. throughout the week, and there was plenty of respectful yet robust discussion in the Q&A sessions, which often extended to the coffee/lunch breaks and even on to local bars and restaurants. A new feature at this year’s conference was the introduction of short talks of 5 minutes in duration, rather than the conventional 20 minutes. These proved extremely popular with attendees (which perhaps says something about dwindling attention spans!), although there were challenges for some session chairs in keeping speakers to time.
50 exhibitor booths were on display, with occupants ranging from instrumentation suppliers to consultancy firms and research institutes, and including two UK companies (Duvine and 3SCI).
A decent footfall of delegates was maintained by dispersing the coffee and lunch throughout the exhibition. The quality of the food was high, although small portion sizes and the absence of plates meant that people had to keep coming back for more, which led to frequent blockages!
A well-attended summer school on Corrosion in Green Energy Technologies was held over the weekend before the conference at the Institut Photovoltaïque d’Île-de-France (IPVF). Here, the attendees learned about corrosion in a range of low carbon energy applications, including photovoltaics, wind, thermal solar, batteries and power electronics. There were also lectures on accelerated testing, surface analysis and atmospheric corrosion, in addition to practical demonstrations at the nearby Horiba laboratories and a discussion session on job opportunities in green energy applications.
The conference kicked off on Monday morning with a plenary session in the main lecture theatre. It is testament to the increasing popularity of the conference and the quality of the plenary speakers that some delegates had to stand, despite the vast size of the lecture theatre! After some words of welcome from the conference chair, Prof. Philippe Marcus (CEFRACORR), the traditional EFC awards ceremony took place, with the presentation of the Cavallaro Medal, the Corrosion Awareness Honour, and three EFC Honorary Fellowships.
The Cavallaro Medal was inaugurated by the University of Ferrara in 1965 and is awarded every two years under the auspices of the EFC in memory of Prof. Leo Cavallaro, one of the founders of the university’s corrosion research laboratory.
The 2024 recipient was Prof. Mikhail Zheludkevich (Helmholtz-Zentrum Hereon, Germany) for his outstanding contributions to the field of corrosion and protection of metallic materials. Prof. Zheludkevich was presented with the medal by Prof. Andrea Balbo of the University
of Ferrara, following
which he gave a talk on sustainability of material systems in complex environments through the design of functional surfaces.
The Corrosion Awareness Honour is awarded annually by the EFC, the Chinese Society for Corrosion and Protection (CSCP) and the World Corrosion Organization (WCO) in recognition of individuals who have made a significant contribution to raising awareness of the importance of corrosion and corrosion protection among the general public. This year the award was presented to Dr Jörg Vogelsang (Sika Technology, Switzerland) for sustained achievements in this area through his extensive industrial and professional society networks.
EFC Honorary Fellowships were presented to Theo Hack (TJoH Consulting, Germany), Dr François Ropital (IFPEN, France) and Dr Jörg Vogelsang (Sika Technology, Switzerland) for their significant contributions to the EFC over many years.
There followed excellent plenary lectures from Prof. John Scully (University of Virginia) on design of corrosion-resistant high entropy alloys, Prof. Nick Birbilis (Deakin University) on corrosion of additively manufactured alloys, Prof. Arjan Mol (TU Delft) on corrosion inhibitor optimisation via machine learning and Prof. Xiaogang Li (University of Science and Technology, Beijing) on the use of artificial intelligence in analysis of corrosion data. It must be acknowledged that this was not the most diverse group of plenary speakers that had ever been assembled, but the scientific quality of the talks was extremely high.
The UK was well represented at the conference, both in terms of number of delegates and representation from ICorr and IOM3. ICorr President Stephen Tate was present for the entire week and had several useful meetings and interactions with officials from the EFC, CSCP, WCO, AMPP and EFC member societies. Other conference highlights from a UK perspective were as follows:
Dr Beatriz Mingo (University
of Manchester) received the 2024 Kurt Schwabe Prize, which is awarded every three years by the Hungarian Federation of Corrosion (HUNKOR) to an outstanding early career corrosion scientist. Following the award presentation, Beatriz gave a very interesting talk on her work on smart ceramic coatings for corrosion protection of lightweight alloys.
Prof. Emilio Martínez-Pañeda (University of Oxford) was selected to give the Young EFC plenary talk, which took place in the main plenary session on the opening morning of the conference. Emilio presented a highly informative overview of the virtual corrosion lab he is
developing, which seeks to use modelling tools to predict the likelihood of pitting and stress on cracking in a range of applications.
Amber Sykes (University of Leeds) was presented with the award for best oral presentation by an early career author for her talk on characterisation of corrosion products in geothermal environments. This was a highly successful period for Amber, who had been awarded an EFC Young Scientist grant to attend the conference and also followed this up by winning the Lionel Shreir Prize for best student presentation at the ICorr Corrosion Science Symposium in Manchester the following week!
EuroCorr 2025 will take place in Stavanger, Norway, from 7-11th September 2025, and it promises to be another memorable experience. As has become traditional during the closing ceremony, the symbolic conference trophy was passed from the current conference chair (Prof. Philippe Marcus, CEFRACORR) to the next (Prof. Torfinn Havn, Norwegian Corrosion Society). Prof. Havn invited those present to come to Stavanger next year – perhaps you will join us there!
Members of the Institute are reminded that ICorr and IOM3 will jointly host the EuroCorr 2026 conference in Dublin, Ireland, from 6-10th September 2026. This will be the first time that the conference has been held in Ireland and the local organising committee is already meeting regularly to make the necessary arrangements. The venue will be the Convention Centre Dublin, a world-class conference facility in the heart of the city, and the conference dinner will be held in the Guinness Storehouse, which features a panoramic view of the city and, more importantly, the highest quality pint of Guinness in the world! Please mark the dates in your calendars.Amber Sykes (University of Leeds) was presented with the award for best oral presentation by an early career author for her talk on characterisation of corrosion products in geothermal environments. This was a highly successful period for Amber, who had been awarded an EFC Young Scientist grant to attend the conference and also followed this up by winning the Lionel Shreir Prize for best student presentation at the ICorr Corrosion Science Symposium in Manchester the following week!
EuroCorr 2025 will take place in Stavanger, Norway, from 7-11th September 2025, and it promises to be another memorable experience. As has become traditional during the closing ceremony, the symbolic conference trophy was passed from the current conference chair (Prof. Philippe Marcus, CEFRACORR) to the next (Prof. Torfinn Havn, Norwegian Corrosion Society). Prof. Havn invited those present to come to Stavanger next year – perhaps you will join us there!
Members of the Institute are reminded that ICorr and IOM3 will jointly host the EuroCorr 2026 conference in Dublin, Ireland, from 6-10th September 2026. This will be the first time that the conference has been held in Ireland and the local organising committee is already meeting regularly to make the necessary arrangements. The venue will be the Convention Centre Dublin, a world-class conference facility in the heart of the city, and the conference dinner will be held in the Guinness Storehouse, which features a panoramic view of the city and, more importantly, the highest quality pint of Guinness in the world! Please mark the dates in your calendars.
ICorr is a founding member of the European Federation of Corrosion (EFC), a federation of national member societies and affiliate members with an interest in corrosion, which operates the EuroCorr conference series. In addition to being eligible for reduced registration fees at every EuroCorr conference (typically a discount of €100), ICorr members benefit from free access to EuroCorr conference papers and presentations through the members area of the ICorr website, the opportunity to join EFC Working Parties, discounts on EFC publications, e.g. the Green Book series, and reduced registration fees for other EFC events.
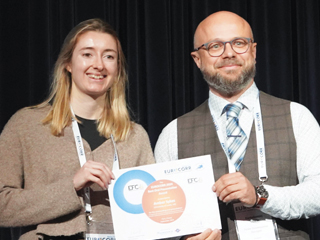
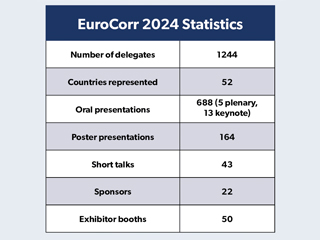
Photo: A Vibrant Poster Session Took Place in the Main Horseshoe-Shaped Corridor Leading to the Rooms Where the Oral Sessions Were Held.
Photo: A Vibrant Poster Session Took Place in the Main Horseshoe-Shaped Corridor Leading to the Rooms Where the Oral Sessions Were Held.
Photo: Prof. Mikhail Zheludkevich (Helmholtz-Zentrum Hereon, Germany) Receives the 2024 Cavallaro Medal from Prof. Andrea Balbo of the University of Ferrara.
Photo: Prof. Nick Birbilis (Deakin University, Australia) Presenting his Plenary Talk on Corrosion in Additively Manufactured Alloys.
Photo: Dr Beatriz Mingo (University of Manchester), Recipient of the 2024 Kurt Schwabe Prize, with Prof. Phillipe Marcus (EuroCorr 2024 Conference Chair).
Photo: Prof. Emilio Martínez-Pañeda (University of Oxford) Presenting the Young EFC Plenary Talk on the Topic of his Virtual Corrosion Lab.
Photo: Amber Sykes (University of Leeds) Receives the Award for Best Oral Presentation by an Early Career Author from Bartłomiej Guzik of Young EFC.
Photo: Prof. Philippe Marcus (Chair, EuroCorr 2024) Passes the Conference Trophy to Prof. Torfinn Havn (Chair, EuroCorr 2025) During the Closing Ceremony.
Institute News
IMechE Argyll Ruane (IAR) have recently announced a successful management acquisition, marking a significant milestone in the organisation, which is a world leader in Coatings and Non-Destructive Testing (NDT) and Coatings training, examinations and NDT consultancy services.
Building on its strong brand and heritage, the company will reinstate its former name Argyll Ruane Limited (ARL), which it used from 1998 – 2016. Members of the management team, proudly led by Managing Director Bryan Ravenshear, bought the two trading entities IMechE Argyll Ruane and IMechE Fife NDT Limited, from the Institution of Mechanical Engineers (IMechE).
The new owners, Bryan Ravenshear (Managing Director), Sally Taylor (Finance Business Partner) and Kristian Hampson (Group Technical Manager) are excited to advance the organisation’s legacy of success. Bryan Ravenshear, Managing Director, commented:
“Kristian, Sally and I have dedicated many years to working in various roles and departments within the organisation. We possess a deep understanding of its operations, the industries
we engage with, and the clients we support, positioning us well for future success. With our team’s ongoing support, we firmly believe that Argyll Ruane Limited will continue to be a trusted partner in the NDT and Coatings industries and providing support to ICorr for many years to come.”
As the Institution of Mechanical Engineers (IMechE) embraced a revised strategic direction, an extensive review was conducted of the enterprises within Professional Engineering Projects Limited, the Institution’s commercial arm. The goal was to ensure that these enterprises aligned with the Institution’s updated vision and strategic objectives and to assess whether the current ownership is conducive to fostering continued growth and success. The review concluded that, through having greater autonomy and adopting a more commercially focused ownership, IMechE Argyll Ruane (IAR) would be able to better leverage its strong market position and the many opportunities available
operating as Argyll Ruane (ARL) globally. If you have any questions about the acquisition, please contact the team:
enquiries@argyllruane.com
Contact Details:
Argyll Ruane Limited,
4 Europa View, Sheffield Business Park,
Sheffield, S9 1XH Tel: (+44) 114 399 5720
Source:argyllruane.com
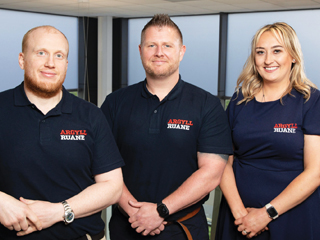
Photo: New proud owners of Argyll Ruane Limited: Kristian Hampson
(Group Technical Manager), Bryan Ravenshear, (Managing Director) and
Sally Taylor (Finance Business Partner).