Ask the Expert
The Significance of PREN for the Corrosion
Resistance of Stainless Steel by Sarah Bagnall
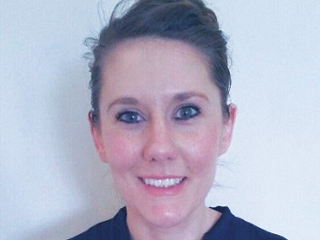
Sarah Bagnall, Director Consultancy Services at R-TECH Materials, CEng. MSc, BSc
Sarah is a materials engineer specialising in failure analysis, for the petrochemical, process, and power generation industries. Currently, she is Director of Consultancy Services at R-TECH Materials. With over 600 failure investigations conducted to date, Sarah has broad experience with a wide range of engineering components, metallic and non-metallic materials, and industries. Sarah has extensive expertise in the corrosion of a wide range of materials, particularly for the chemical processing and petrochemical industries.
- What is the Significance of PREN for the Corrosion Resistance of Stainless Steel?
Calculating PREN and How to Apply it
Stainless steels are well known for their superior corrosion resistance, which is primarily a consequence of the significant chromium addition. When exposed to oxygen, stainless steel forms a passive film due to its 10.5% (or more) chromium content. This film protects the material from rusting and even has self-healing properties. Other elements can be added to further improve the corrosion performance, such as Nickel, Molybdenum, and Nitrogen.
Not all stainless steels are created equal. Different grades exist, and their corrosion resistance can vary significantly. The corrosion resistance between grades can be compared by using the Pitting Resistance Equivalent Number (PREN). The calculation used for PREN is as follows:
PREN = Cr% + 3.3 x (Mo% + 0.5 x W%) + 16 x N%
Examples of stainless steel grades and the calculated PREN numbers are given in Table 1 and Figure 1 below.
Performance in Service
While the PREN is useful for ranking and comparing the different grades for relative resistance to corrosion, it cannot be used to predict whether a particular grade will be suitable for a specific application, where pitting corrosion may be a hazard. All environmental and operating conditions must be taken into consideration.In some industries, notably the oil and gas sector, specifications may place tighter restrictions on the PREN for specific grades than that implied by the minimum composition of the grade defined in EN or ASTM Standards.
In practice, the vast majority of stainless steels deployed across industry are of the 300 series type with lower PREN values, where external pitting is actually quite common in service at ambient temperatures.
Corrosion resistance is not only affected by the chemical composition of the material but also by the heat treatment condition. If the material is heat treated incorrectly during manufacture or welding, microstructural changes can occur which effectively means that
the material is no longer a stainless steel in a localised area. Exposure to temperatures in the range 370-815oC allows the precipitation of chromium rich carbides/nitrides along the grain boundaries. These precipitates are rich in chromium and deplete the area directly adjacent to the boundary of chromium, thereby increasing the likelihood of localised corrosion in the form of intergranular attack, pitting or stress corrosion cracking in a corrosive environment.
Further Guidance
The British Stainless Steel Association (BSSA) exists to promote and develop the manufacture and use of stainless steel across the UK and Ireland. Based in Sheffield, the Association provides technical advice, information, training, and education in all aspects of stainless-steel
usage. They may be contacted at: www.bssa.org.uk
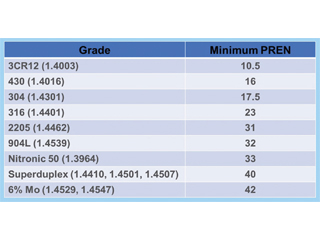
Table 1: Comparison of Stainless-Steel Grades Based on the PREN.
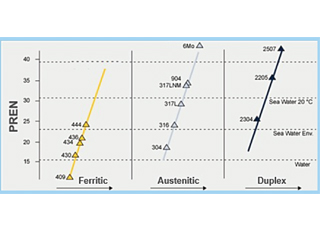
Figure 1. Comparison of Stainless-Steel Grades Based on the PREN
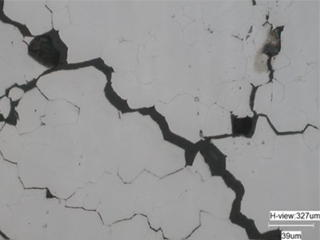
Figure 2. Cracking of a Sensitised Stainless Steel Bolt Which Had Been Heat Treated Incorrectly During Manufacture.
Industry News
This year marks a momentous milestone for the corrosion science community—the centenary of the publication of The Corrosion of Metals by Ulick Richardson Evans in 1924. This pioneering work laid the foundation for modern corrosion science, transforming it from a fragmented collection of empirical observations into a rigorous, quantitative discipline. As we celebrate this historic achievement, it is fitting to reflect on Evans’ profound contributions and the enduring impact of his groundbreaking research.
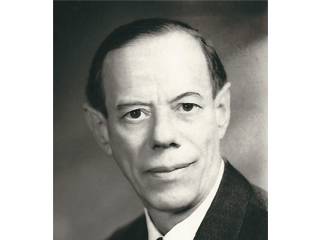
U.R. Evans: A Visionary in Corrosion Science
Ulick Richardson Evans was described in the Biographical Memoirs of Fellows of the Royal Society as the “Father of the modern science of corrosion and protection of metals”. Evans was born in Wimbledon and received his education at Marlborough College (1902–1907) and King’s College, Cambridge (1907–1911), where he pursued the Natural Sciences Tripos, specializing in chemistry in Part II. Following his studies, he began research on electrochemistry in Wiesbaden and London, but his work was interrupted by the outbreak of the First World War.
He served in the army from August 1914 until 1919. After the war, he returned to Cambridge, where he dedicated the remainder of his life to research and prolific writing on the corrosion and oxidation of metals.
His keen intellect, innovative experiments, and commitment to advancing the field quickly earned him international recognition.
Published at a time when the scientific understanding of corrosion was in its infancy, The Corrosion of Metals was revolutionary. It was the first textbook to comprehensively explain the mechanisms of corrosion, with a particular focus on the electrochemical nature of metal deterioration. Evans’ insights provided engineers and scientists with the tools to address real-world corrosion challenges systematically, heralding a new era of research and practical applications.
The Impact of The Corrosion of Metals
Evans’ book was not only an academic milestone but also a practical guide that addressed the pressing needs of industries reliant on metals. Its immediate translation into German, French, and Russian underscored its global importance. The book introduced concepts such as passivity, electrochemical corrosion mechanisms, and methods of protection that remain central to the field today.
Over the next five decades, Evans continued to expand and refine his work, publishing additional seminal texts, including Metallic Corrosion, Passivity, and Protection (1937) and An Introduction to Metallic Corrosion (1948). His ability to elucidate complex scientific principles with clarity and rigor inspired generations of corrosion scientists and engineers.
A Legacy that Lives On
Evans’ contributions extended beyond his publications. He was an influential mentor, guiding researchers from around the world in their pursuit of corrosion science. His work provided the foundation for many of the engineering advancements that now enable us to protect critical infrastructure, transportation systems, and industrial equipment from the damaging effects of corrosion.
His legacy is perpetuated through the U.R. Evans Award, established by the Institute of Corrosion in 1976. This prestigious award, symbolized by an engraved sword, honors outstanding achievements in corrosion science, continuing Evans’ mission to foster collaboration and innovation in the field.
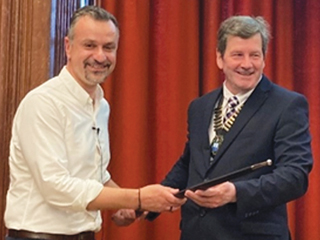
Photo: Professor Nick Birbilis UR Evans Award Presentation on 11th September 2023.
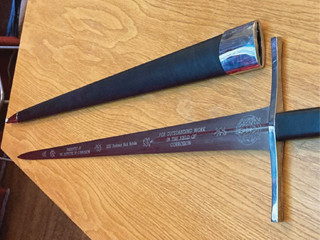
Photo: Engraved Sword.
Industry News
Cortec® Corporation is pleased to announce a new addition to its line of concrete surface treatments. MCI®-2019 X is a 40% silane penetrating water repellent minus the typical Migrating Corrosion Inhibitors of MCI®-2019. The reason for not including MCI® is the same reason that Cortec® released MCI®-2018 X without MCI® in early 2024: some contractors need more options to adapt to specific project budgets and parameters. Here is a closer look at how MCI®-2019 X might fit into the picture.
Redundant or Complementary Protection
MCI®-2019 X provides water repellency by chemically reacting with the alkaline environment of concrete and creating a hydrophobic layer to reduce the ingress of water and other corrosives. This water repellency offers standalone benefit and is even better paired with a penetrating surface applied corrosion inhibitor (SACI). Historically, this combination has been available with MCI®-2018 and MCI®-2019, two silane water repellents that contain Migrating Corrosion Inhibitors. However, to get the highest concentration of SACIs on the market, users must opt for MCI®-2020, which contains a higher dose of MCI® without water repellent. While applying MCI®-2020 with either MCI®-2018 or MCI®-2019 on top would provide enhanced protection due to the presence of MCI® in both products, some contractors may prefer to apply just a water repellent on top of MCI®-2020 due to budget limitations or other project parameters. For cases like these, MCI®-2018 X and MCI®-2019 X are excellent alternatives to adapt to project needs.
Is 100% or 40% Silane Better?
But why would someone choose MCI®-2019 X over MCI®-2018 X? The answer, again, goes back to project and budget needs. Using a 40% silane water repellent is naturally more budget friendly than a 100% silane water repellent because of the lower concentration of a commodity in high demand. Yet that is not the only advantage. Contractors applying water repellent to previously treated concrete surfaces must think about ensuring good penetration and compatibility. This usually requires the thorough removal of water repellent residue before another product can be applied. However, MCI®-2019 X is one water repellent that may be applied over residue from previously worn-off treatments, thus replenishing the water repellency that the concrete has lost. This low-labor benefit is especially helpful in maintenance applications where a water repellent is reapplied every 5 to 10 years.
Slippage and Appearance
As a silane water repellent, MCI®-2019 X is a good choice for concrete structures where slippage is a concern. Since silane molecules are so small, they tend to penetrate deeper than other types of water repellents, making them less likely to cause water puddling or slippage. They also do not darken or change the appearance of concrete, an ideal characteristic for protecting historical structures.
More Flexibility for Contractors
With this new addition to Cortec’s MCI® portfolio, contractors have greater flexibility to tailor a surface protection system to their concrete repair or maintenance project. Whether they want a two-in-one MCI® water repellent (MCI®-2019), a doubled-up protection system of SACI + SACI water repellent (MCI®-2020 plus MCI®-2019), a simple water repellent (MCI®-2019 X) on top of high concentration SACI (MCI®-2020), or a 40% silane water repellent (MCI®-2019 X) alone, contractors can make their pick on what seems to be the best choice for their jobs.
Julie Holmquist
email: jholmquist@cortecvci.com
Industry News
By Birit Buhr, FICorr, Chief Corrosion Engineer, Europeanenergy
A new Joint working group (JWG6) have been created between two technical committees (TC) of ISO.
The two technical committees are:
ISO TC 107: Metallisation and inorganic coatings (project lead)
ISO TC 35—organic coating, but also
ISO TC 156 WG10 (cathodic protection) as a liaison partner to
the JWG6
Five projects have been approved, and five draft documents circulated:
25249-1 Corrosion protection of offshore wind structures, design considerations
25249-2 Corrosion protection of offshore wind structures, primary steel components—general requirements for thermal spraying and painting
25249-3 Corrosion protection of offshore wind structures, primary steel components—supplementary requirements for foundations
25249-4 Corrosion protection of offshore wind structures, primary steel components—supplementary requirements for towers
25249-5 Corrosion protection of offshore wind structures, Supplementary requirements for primary structural steel components—structural steel and cast components for nacelles
They are planning for 5 more for secondary steel components, qualification of metallisation and paint systems, repair of surface protection systems, composite structures, and last but not least, environmental impact considerations, including life cycle
assessment (LCA).
Offshore wind was born in Denmark in 1992 with the project Vindeby, and therefore it has only been natural that the project initiative comes from Danish Standards and the offshore wind industry here.
ISO support industrial needs and offshore wind is a global industry. The standardisation works will be truly international, with already the following countries supporting the work and the joint working group: Australia, China, Czech Republic, Denmark, Ethiopia, Finland, France, Germany, Ghana, Iran, Italy, Japan, Jordan, Korea, Netherlands, Norway, Poland, Portugal, Russian federation, Spain, Sweden, Switzerland, United Kingdom.
The purpose of the NWIPs is to have overall industry-based ISO standard for the corrosion protection of offshore wind turbine structures to enable these structures to reach their intended
service life.
Industry News
Houston, Texas – Oceaneering International, Inc. announces today that its Subsea Robotics and Aerospace and Defense Technologies segments were awarded a multi-million-dollar contract by the Defense Innovation Unit (DIU) of the U.S. Department of Defense to build a Freedom™ Autonomous Underwater Vehicle (AUV) and establish an Onshore Remote Operations Center (OROC) for the U.S. Navy.
The award highlights Oceaneering’s ability to leverage technology originally developed to support the offshore energy industry into other markets.The vehicle will be manufactured at Oceaneering’s Morgan City, Louisiana facility.
Oceaneering has conducted remote operations of commercial subsea robotic systems from OROCs since 2015 and has performed over 120,000 hours of remote operations to date.
Source: Oceaneering News Release