This series of features in Corrosion Management intends to highlight industry wide engineering experiences, practical opinions, and guidance, to give improved awareness for the wider public, and focused advice to practicing technologists. The series is written by ICorr Fellows who have made significant contributions to the field of corrosion protection through past industry involvements. Corrosion Management is pleased to publish this month’s contribution by Bijan Kermani, FICorr.
Metallic Materials for Hydrocarbon Production
Several categories of alloy are used in the energy sector, and in particular, in hydrocarbon production facilities, to enable successful and trouble free operations. The majority of the components of these facilities are manufactured from metallic materials, commonly carbon and low alloy steels (CLASs), which are readily available in the volumes required and able to meet many of the mechanical, structural, fabrication and cost requirements. However, the inherent corrosion resistance of CLASs is relatively low, and their successful application requires combination with one or more whole-life forms of corrosion mitigation against both internal and external exposure conditions, and/or the use of corrosion resistant alloys (CRAs).
The main materials used in hydrocarbon production fall broadly into three categories, ferrous, non-ferrous and non-metallic materials, in which ferrous materials covers three types, carbon steels, CLASs and CRAs, broad details of which are summarised in Table 1. This article briefly addresses only the ferrous materials, which are the essential materials of construction for CAPEX intensive items (tubular and pipeline), their ranges, examples, related standards and their resistance to principal types of corrosion threat in hydrocarbon production (metal loss CO2 corrosion. and resistance to sulphide stress cracking, SSC, in the presence of H2S). These are summarised and characterised briefly in Table 2 and are as follows:
CLASs: A wide variety of CLAS grades are used across this industry sector and are the principal materials of construction and the first, optimum, and base-case choice for many applications. They normally have low metal loss corrosion resistance. The most notable categories of CLAS according to the application include, structural services and pressure containment.
Structural Services
These commonly utilise “structural” steel products in the form of rolled plate, various sectional shapes and tubular sections, although cast or forged products may also be used. Typical applications include offshore structures, sub-sea module support frames, pipe racks, process equipment saddles and, in some instances, low criticality storage tanks. They contain Mn (typically 0.5 – 1.5%) and limited quantities of other alloying elements such as Nb, Ti and V. Structural Steels generally have adequate properties over a range of temperatures lying between approximately -50°C to +50°C, depending on the local environmental conditions, e.g. in arctic, temperate or tropical conditions. They are normally weldable and have a yield strength not exceeding 350 MPa.
Pressure Containment
C/Mn or lean alloy steels may be used for process plant, vessels, pipe work, pipe fittings and valve bodies requiring pressure containment. However, steels with an increased alloy content of Cr, Ni, Mo, so called low alloy steels, are employed to give mechanical properties suitable for a temperature range lying within the limits of approximately -80°C (characteristic of Joule Thompson cooling) to approaching 600°C (characteristic of a number of refining processes). Typical applications requiring pressure containment include drill pipe, casing and tubing, linepipe, process pipework, pressure vessels and heat exchangers. Generally CLAS has low resistance to metal loss corrosion while sour service grades have good tolerance to SSC.
While metallic materials used for subsurface applications (wells) are seamless with relatively high strengths (normally yield strength >500 MPa) and have no requirement for welding (threaded connections are used), other applications including, flowlines, topside/surface facilities and pipeline/trunklines require materials with the ability to be welded and normally have lower yield strength (not exceeding 700 MPa).
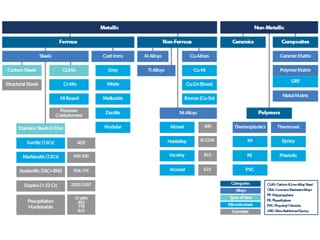
Table 1. Range of metallic and non-metallic materials used in the construction of hydrocarbon production facilities.
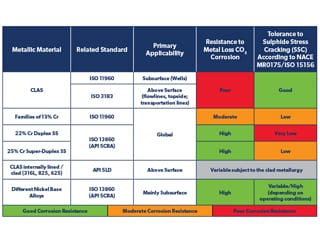
Table 2. Range of CAPEX intensive metallic materials (tubing and pipelines) and their relative corrosion performance.
The new generation of low Cr containing steels with 1 to 5%Cr offer slightly improved metal loss corrosion resistance, optimality for well completion applications.
CRAs: While CLASs, or in combination with corrosion prevention systems, may offer suitability for some applications, corrosion resistant alloys (CRAs) containing amongst other elements, Cr, Mo, N, W, Nb, Ni, Co have emerged as alternative more corrosion resistance choices. Increasing alloying elements invariably leads to increasing costs. Even though CRAs are more costly to procure in terms of CAPEX, they may offer more favourable whole life cost with lowering risk in terms of corrosion threats.
CRAs are primarily restricted for use in subsurface (well completion) and as internal cladding of manifolds and internal cladding of risers due to their relative cost. However, based on whole life cost comparison they may become economical for specific applications.
There are many categories of CRAs. These are generally divided into groups or families of alloys that have common characteristics or microstructures. These are summarised in Table 1 and include: 13Cr Steels. The family of 13Cr stainless steel (SS) exhibit good metal loss corrosion resistance with good strength. They contain 13%Cr and some other minor elements. A new generation of this family contains 15-17Cr, or alloyed 13Cr containing Ni and Mo, have improved metal loss corrosion and top temperature limit. They are primarily for subsurface applications, although weldable/lean grades are considered for infield flowline/pipeline applications. Generally, they have low resistance to sulphide stress cracking (SSC).
Duplex Stainless Steels
Duplex and super duplex SS derive their properties from the balance of phases between ferrite and austenite by the addition of Cr, Ni and Mo. They are designed to provide better corrosion resistance than the 13Cr families, particularly resistance against chloride pitting corrosion and they have higher strengths, although their tolerance to environmental cracking (EC) in the presence of H2S is low.
Other CRA
Other types of CRA include several categories of alloy containing varying amounts of Cr, Ni, Mo and other alloying elements, and also Ti alloys some of which do not fall into the ferrous category. These offer superior metal loss, corrosion, as well as tolerance to environmental cracking (EC) in the presence of H2S, chloride, and also when elemental sulphur is present. While some grades of Ti alloys have been successfully used in well completion (sub-surface), these are not covered in the present article.
Additional reading: B Kermani and D Harrop, Corrosion and Materials in Hydrocarbon Production; A Compendium of Operational and Engineering Aspects, Wiley, 2019.