On Tuesday 30th January 2024 the Aberdeen Branch meeting welcomed Dr. Steve Paterson, Arbeadie Consultants Limited for a talk entitled, “Applying materials experience from oil and gas production to carbon capture and storage in North-East Scotland.”
Steve graduated from Imperial College London with a B.Sc. (Eng.) and Ph. D. in Metallurgy. He has over 40 years’ experience in the oil and gas industry, mostly with Shell. His final position at Shell was Principal Technical Expert for Upstream Materials where he was primarily involved in materials, corrosion, welding, inspection and integrity management. He has been involved in several CCS projects during his career and has co-authored papers on materials selection for CCS. Steve is currently an independent materials and corrosion adviser with Arbeadie Consultants based in Banchory near Aberdeen, UK; and is also, an external lecturer in Materials and Corrosion Management at Robert Gordon University in Aberdeen. He was awarded the Institute of Corrosion Paul McIntyre Award in 2019 and EFC Honorary Fellowship in 2023.

Applying Materials Experience from Oil and Gas Production to Carbon Capture and Storage in North-East Scotland
Carbon Capture and Storage (CCS) is a key technology to mitigate emissions from large-scale fossil fuel use. During transport and injection of the CO2 separate liquid phases may form depending on the phase envelope and CO2 composition. These phases comprise of water or reaction products including strong acids and elemental sulphur. The type of liquids formed and shifts in the phase envelope can significantly influence materials integrity including fracture, corrosion, and degradation of polymers. CCS involves the gathering of CO2 from industrial sources, and processing the gas so that it can be transported and injected into sub-surface reservoirs. After capture, the CO2 gas is compressed into ‘Dense Phase’ which is a super-critical fluid state, where its viscosity is similar to that of a gas but its density is actually closer to that of a liquid. It is important that these conditions are achieved for pipeline transport, as this means lower drag and
operating costs.
Experience gained from the oil and gas sector can be used to facilitate materials selection and corrosion control that can address the specific integrity requirements of a CCS project. The presentation also placed in context the historical development of CCS opportunities offshore Aberdeen.
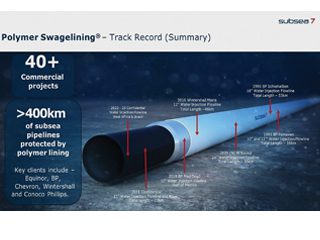
CCS in North-East Scotland has had a number of false starts, beginning with BP in 2005 with the proposed Peterhead CCS project to produce ‘carbon-free’ electricity from hydrogen and inject the CO2 into the declining Miller oil field 240 km offshore for enhanced oil recovery. This was scrapped in 2007 following the decision by the UK government to make funds available only to projects selected via a competition. This led to 3 short-listed bids by Shell, EON and RWE, including capture of CO2 at Scottish Power’s coal-fired Longannet Power Station, transporting it to St Fergus and injecting it in the depleted Goldeneye reservoir 100 km offshore. This project was cancelled in October 2011 due to its high-cost estimate. A new proposal to capture CO2 at SSE’s gas-fired Peterhead station and inject it in the Goldeneye reservoir was initiated in 2012 but cancelled in November 2015. In July 2018 UK government launched the CCUS Innovation programme to deploy CCS in a minimum of 2 industrial clusters by the mid-2020s, and 4 by 2030 at the latest. The aim was to capture and store 20-30 Mt CO2 per year by 2030. The first phase evaluation results in November 2021 confirmed HyNet and East Coast Clusters as Track-1 clusters for mid-2020s, with the Scottish Cluster (Acorn) as a reserve if backup was needed. The UK government confirmed Acorn and Viking CCS systems as Track-2 clusters in December 2023. The Track-2 Acorn project consists of 4 partners: Storegga (formerly Pale Blue Dot), Shell UK, Harbour Energy and North Sea Midstream Partners. In phase 1 the CO2 will be captured from existing St Fergus industrial emitters and transported through the existing 20” Goldeneye pipeline where it will be injected into the Acorn South (Goldeneye) reservoir. In phase 2 the options include CO2 capture and transport from industrial centres around Grangemouth to St Fergus via the National Gas Grid Feeder 10 pipeline, injection in the Acorn Central reservoir via the existing Atlantic pipeline, and a possible international interconnection utilising the Miller Gas System pipeline.
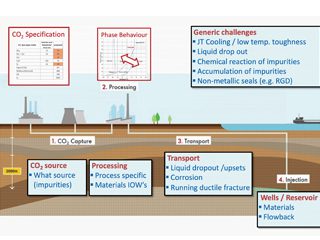
The question remains whether Acorn will actually happen. This will depend on a number of factors, including the high cost of providing the CCS infrastructure, and commitment and funding from the UK government. Only time will tell.
Materials Selection and Corrosion Control
For capture, processing transport and reservoir storage appropriate materials selection and corrosion control is critical. Control can be affected by either avoiding threats that can lead to rapid failure by selecting resistant materials, or by managing threats using a suitable mitigation strategy. Specific threats that can lead to rapid failure include, brittle fracture due to Joule-Thompson cooling, running ductile fracture, hydrogen related cracking mechanisms and stress corrosion cracking. Threats that can be controlled using suitable barriers, including CO2 corrosion and acidic corrosion from impurities. These failure mechanisms were discussed in detail in the presentation by Steve.
For CO2 corrosion there is a wealth of data and many CO2 corrosion prediction models from the oil and gas sector including some based on the traditional De Waard-Milliams relationship. When water is dissolved in dense phase CO2 there is no corrosion, but if water drops out the CO2 dissolves in the water to form carbonic acid and CO2 corrosion becomes a threat. It has been found that at higher pressures the dense phase CO2 corrosion rate is lower than that predicted by the traditional De Waard-Milliams relationship. A revised correlation has been proposed that gives a better fit between field/lab data and model calculations.
CO2 for storage can originate from different sources with a range of impurities such as water, O2, SO2, NO2 and H2S. Impurities may trigger a water phase below normal dewpoint and initiate a shift in tendency of water to condense and create conditions for CO2 corrosion. Impurities can form highly corrosive liquid phases with sulphuric acid, nitric acid and elemental sulphur. Control options for the strong acids are either preventing formation or avoiding drop-out. H2SO4 (and also elemental sulphur) has low solubility in dense phase CO2, so the preferred control option is preventing formation. HNO3 has a relatively high solubility in dense phase CO2 so the preferred option is to avoid drop out by defining strict CO2 specification limits.
The presence of water in CCS systems can lead to breakdown of passivity of low grade CRA such as 13Cr often used for well tubing. High CO2 pressure in CCS can lower pH of condensing water to create conditions where de-passivation can occur. It is well known from oil and gas experience that de-passivation can cause pitting and possible SCC. Parameters that trigger de-passivation include pH, chloride content, temperature and presence of oxygen. For tubulars at the bottom of injection wells in a reservoir with high salinity, the selection of high grade CRAs may be required. CRA materials should be selected for conditions where de-passivation does not occur under any operating scenario. Special attention is required for CRA materials in wells especially if O2 is present in the CO2.
Polymer materials that will be exposed to CO2 should be assessed for rapid gas decompression resistance and the potential impact of impurities. Steve concluded by highlighting that much data and expertise are already available from the oil and gas sector to benefit design and operation of CCS projects, although additional testing may be necessary to confirm suitability for the specific conditions of CCS.
An extensive Q&A session and discussion followed a very detailed and informative presentation.
Predictable Pipeline Performance with Polymer Liners
On Tuesday 27th February 2024 the Aberdeen Branch meeting welcomed Mark Smithson, Subsea 7 Limited with a talk entitled “Predictable Pipeline Performance with Polymer Liners.”
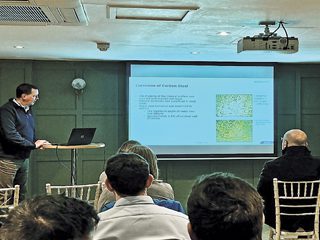
Mark is currently a senior development engineer with the Internal Corrosion Management team for Subsea7 pipeline products. An experienced engineer, he holds a Bachelor of Engineering in Mechanical engineering with industrial management from Liverpool University. Mark has been part of Subsea7’s polymer lined pipe developments and execution for more than 5 years working on a range of projects aimed at increasing the applications applicable to polymer lining. Within this role, he has been responsible for increasing the qualification limits for the new ‘Linerbridge’ connector and currently holds two patents relating to polymer liner developments with a further application pending. Prior to joining the polymer lined pipeline team at Subsea7; Mark worked for Artis, an independent polymer consultancy where he worked on projects ranging from polymer compound development, polymer characterization and product development to testing and process development or optimisation.
Polymer liners have provided a global, cost-effective solution for internal corrosion mitigation of rigid water injection flowlines for more than 25 years. The first polymer lined subsea pipeline was installed in 1994, since then more than 400 km of high-density polyethylene (HDPE) liners have been installed for subsea water injection service by Subsea7 companies. This track record includes design conditions and qualification programmes demonstrating pressures up to 1293 bar at depths greater than 1,500 m and temperatures up to 80 °C, with the potential to expand all these boundaries.
Reduced pipeline performance due to internal corrosion often leads to a reduction in field output, and an increase in maintenance activities and non-productive time. This results in reduced production and lost revenue. Furthermore, corrosion ultimately leads to pressure downrating or complete failure. The lifetime expectancy of a typical unlined carbon steel (C/S) water injection pipeline is ~ 7 years only and the global cross-industry cost of corrosion is presently estimated at $2.5 trillion annually. Appropriate corrosion mitigation could save industry ~ 35%. Subsea7 have developed innovative swage-lining products which are essentially polymer lined (C/S) subsea pipelines. These products have many advantages, and they can have greater and more predictable service life assurance. The pipeline weight can be reduced, there is increased uptime and the potential to reduce total expenditure costs. The swage-lining products can also offer reduced carbon footprint when compared to competing technologies.
In order to line a steel pipeline with a polymer the swage-lining process is used. This is a proprietary process in which a polymer liner pipe is selected which is of a slightly greater size than the pipe ID. The polymer pipe is pulled through a reduction die at entry and through the length of the pipe under tension, using a pull line threaded through the pipe. The pipe is reduced in diameter by the die and the strain enough to fit through the ID of the outer pipe and is pulled right through. Once in position the tension is released and the liner contracts in length and expands in diameter to form a snug fit inside the pipe.
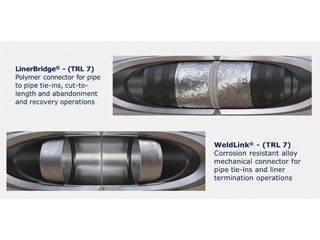
For connecting the sections of pipe together, there are a few different solutions. There is a Liner bridge and a Weld link product with ridges inside the polymer liner ends into which a compression ring can be forced to seal the polymer against the ID of the pipe.
BP Foinhaven – Lined Spool Assessment
Evidence of the efficacy of polymer lining as a corrosion protection technology was demonstrated on the recovery of a spool from a live field at BP Foinhaven F26 after 13 years in service, which demonstrated no deterioration of either polymer material or carbon steel host pipe. Autopsy on the pipe involved sectioning the pipe and machining the interfaces to study the liner condition and the performance of the weld link products.
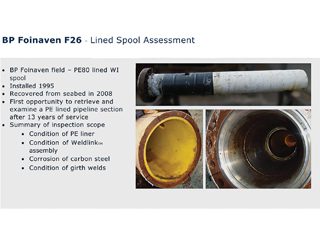
The PE liner condition was assessed by conducting tensile tests on recovered samples against the specification of 18 MPa and these were found to still be within spec on the 4 samples that were taken from different sites. The liner is also proven to have retained residual stress, indicating a tight fit. Tests were also made for environmental stress cracking and chemical stability. The material had improved stress cracking due to adsorbed service fluid. There was no change in chemical stability. The weld link and compression ring assembly remained fully intact after reeling installation, 13 years’ operating service and recovery. A pull-out test on the PE liner from the weld link joint also demonstrated that the force required to pull the liner out of the assembly exceeds the yield strength of the PE liner even after 13 years. The carbon steel pipe was sectioned, and the liner was removed from the inside of the pipe to examine for corrosion. The pipe had superficial corrosion only and was largely covered in cracked mill scale and rust blooming. The worst corrosion was examined in section and was found to be a maximum depth of 280 micron (0.28 mm) or approximately 1.6 % of wall thickness. Sections were also taken to assess the girth welds and the inner diameter of the carbon steel pipe. Girth welds within the polymer lined section were deemed acceptable, with the liner protecting the weld. Outside the lined section the weld was found compromised due to a fissure in the protective Inconel clad section near the clad flange.

These lining Products now have a significant track record and over 400 km of subsea pipelines have been installed for a number of operators worldwide.
More recently, this well-established flowline product has been supplemented by the qualification of polymer lined pipe for dynamic riser service (steel catenary riser, SCR, and Steel Lazy Wave Riser, SLWR). The qualification programmes included fatigue testing on both full-scale polymer-lined pipe sections and small-scale material coupons. Combined with an investigation of liner behaviour in the vertical orientation. The riser product obtained qualification to technology readiness level (TRL) 5 from the industry-recognised body, DNV.
A deep-water riser has since been fabricated and installed off the back of this programme and is ready to enter service.
Current developments in polymer lining technology have the potential to offer these and other benefits in alternative service environments, such as Water Alternating Gas (WAG), production lines, and new energy transition applications like Carbon Capture, Utilization and Storage (CCUS) and Hydrogen transportation. Mark’s talk was most interesting and very well received. The Aberdeen Branch provides a very full technical programme of both in-person and online events. Abstracts of potential papers for the Aberdeen Technical Programme are always welcome for consideration, and anyone wishing to present should correspond soonest with the 2024/2025 Chair and Technical Programme Co-ordinator: meilingcheah@gmail.com
Further Information about the Aberdeen Branch, and past presentations, may be found on their website page: Aberdeen Branch – Institute of Corrosion (icorr.org) and to join the Aberdeen Branch mailing list,
please contact: icorrabz@gmail.com
Dr. Steve Paterson, Arbeadie Consultants Limited.
Materials and Corrosion Challenges
Mark Smithson, Subsea 7 Limited.
Swagelining® Connectors.
Internal Section of Carbon Steel Pipe After PE Liner Removal Including Girth Weld Region.
Superficial Corrosion of Carbon Steel After Liner Removal.
Polymer Lining – Project History.