Branch News Aberdeen Branch
Following on from the success of its week long April joint webinar event with MCF, ICorr Aberdeen held its 8th event of the 2019/2020 session during 6-10 July 2020 with a very comprehensive marine focussed ‘Webinar Week’ comprising of some excellently delivered papers by:
• Roger Francis, (RF Materials – Improving the Corrosion Resistance of Duplex Stainless Steel Welds).
• Adnan Syed, (Cranfield University – Hot Corrosion Mechanisms for Gas Turbines).
• Lars Lichtenstein, (DNV GL – Improvements of the DNVGL-RP-0416 and DNVGL-RP-B401 – Upcoming Revisions).
• Brian Wyatt, (Corrosion Control Ltd – Cathodic Protection of Offshore Renewable Energy Infrastructure).
• Andrew Woodward and Chris Matthews, (Connector Subsea Solutions Ltd – Use of CRA’s in Mechanical Connectors for CRA Clad or Lined Pipe Repairs).
The heavily over-subscribed webinars, which had more than 500 attendees, were jointly chaired by Phil Dent (MCF) and Stephen Tate (ICorr-ABZ), with Lewis Barton (MCF) as webinar facilitator.
This time around, a very effective 4-pronged promotional attack was deployed, with excellent Social Media blogs provided by Michael Barton for the HQ website, Dr Yunnan Gao promoting at the Aberdeen end, Lewis Barton via the MCF website and LINKEDIN pages, and further additional support provided by Gareth Hinds and Brian Wyatt of ICorr Council.
There was excellent participation by the attendees via Web Chat for all the Q&A Sessions, and all the presenters’ responses are also now loaded onto the ICorr/MCF websites.
All the webinar presentations had excellent technical content that highlighted the particular challenges of the marine environment, in terms of correct materials selection, correct application of corrosion control methods, the importance of good quality control at fabrication, and having appropriate inspection and maintenance regimes.
Roger Francis discussed in great detail the development of modern Duplex stainless steels from the early 1980’s onwards, with particular emphasis on the jointing processes / joint design and how to avoid corrosion failures of welds resulting from disturbed metallurgy, the importance of having adequate post-weld treatments / checks, (such as post-weld pickling / use of shielding welding gases during fabrication and the use of Feritscope checks on the HAZ of production welds that can be used to measure the ferrite content through magnetic induction), and in also having suitable weld testing programmes in place at fabrication stage, over and above that of ASME IX, and he proposed some suitable tests. Roger also emphasised the need to perform corrosion tests not just on the PQR (Procedure Qualification Record), but also based on the individual welder qualifications, in order to ensure that each welder fully understands what is necessary to produce an acceptable’ weld quality.
Adnan Syed described a very interesting journey through hot corrosion mechanisms of jet engines and industrial gas turbine components, (this being a well-known issue for the aviation and power generation industries). The talk included the possible hot corrosion mechanisms occurring in the gas turbine combustion environment, and some of the challenges industry is facing in their understanding and managing of turbine component degradation. He discussed the two main types of attack: Type I (high temperature corrosion) attack, in the range of 750 to 900 C, mainly due internal sulphidisation, and Type II (low temperature hot corrosion) attack, at temperatures in the range of 600 to 750 C (maximum rate of attack in the range of 675–730 C) and associated with pitting type attack. The importance of good alloy quality and the prevention of corrosion damage related to salt deposit chemistries was emphasised, along with ongoing Cranfield laboratory corrosion experiments and the use of thermodynamic software to help identify the phases formed, which in turn enables a better understanding of the mechanisms involved
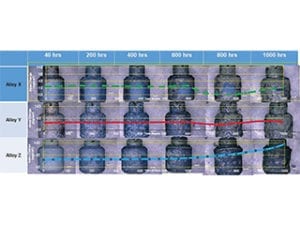
Cranfield University – Adnan Syed. Examples of macrographs and mass change data for high temperature corrosion testing.
Lars Lichtenstein then considered the harsh operating environment for Marine Wind Turbines being increasingly deployed in our coastal waters, bringing us up to date on ongoing revisions to DNV GL documents on corrosion protection for wind turbines (which are under internal revision), DNVGL-RP-0416 and DNVGL-RP-B401. Changes highlighted included more guidance on the useful coating lifetime as introduced in DNV-OS-J101:2011 for the first time, and the relation with fatigue calculation and surface preparation, including the need for weld grinding. In particular the level of coating quality required at the end of the lifetime, and the degree of effort needed to be put into inspection and repair of 15+ year old coating systems, so as to ensure ongoing integrity. Lars also discussed the issue of coating breakdown factors with regards to CP system calculation and on current drain of buried structures. He further highlighted new information on material selection for bolts and stainless steel, and what boundary conditions should be considered.
Brian Wyatt nicely linked into the previous day’s discussion on standards and recommended practices and emphasised the multiple zones / environments requiring many different corrosion control considerations / solutions within the Wind Energy Sector.
He highlighted the lack of competency seen in some projects performed to date and gaps in guidance that urgently require to be addressed as the renewables industry accelerates in scale. Velocity effects are a particular consideration resulting in increased levels of oxygenation at the steel/water interface which demand more robust CP designs, both in mechanical and electrochemical terms. The nature of the support structures, and limited scope for lower cost onshore anode installation, also lead to challenges to uniform anode distribution, particularly on Monopile type structures that replaced the earlier jacket type wind farm structures, that were more similar to the established requirements and practices of the Oil and Gas Industry, for which earlier DNV Codes were intended to cater for (editor, see technical article later in this magazine).
Andrew Woodward and Chris Matthews wrapped up the week with a great talk on outcomes from their recent joint industry project (JIP) with Chevron and Woodside Petroleum, as part of a new technology development programme in line with DNVGL-RP-A203. They have recently developed a new patented method of sealing on the inside of a CRA clad or lined pipe, thus enabling a permanent subsea repair solution. The new seal in the “CLiP” Connector takes advantage of the corrosion resistant and ductile properties of Alloy 625 (UNS N06625) and experience gained through extensive testing of graphite in order to create a seal that conforms to NACE MR0175 / ISO15156-3. The seal forms around all pipeline manufacturing tolerances and even localised irregularities such as internal weld seams. The seal can be easily integrated into existing mechanical connector configurations and is able to be adapted for both diver installed and remote repairs. The technology qualification was completed through a combination of analysis (including development of a parametric FEA model to cover all future design scenarios), 3rd party material testing, and component testing in specialised test rigs; all culminating in full scale testing within a mechanical connector. The presentation focussed on the analysis and testing aspects of the technology qualification process which highlighted all key failure modes that had to be addressed.
There has been much debate of late concerning the impacts of the coronavirus outbreak, but the success of these recent Joint and Online Events has proven beyond doubt that such obstacles can be overcome and that the thirst for corrosion learning remains as strong as ever.
As usual, full details of future branch events can be found on the ICorr Website, or by contacting: ICorrABZ@gmail.com, and copies of the majority of past branch presentations can be found at: https://www.icorr.org/aberdeen/ and a photo gallery for all Aberdeen events may be found at: https://sites.google.com/site/icorrabz/event-gallery. See also ICorr Aberdeen on LinkedIn at https://www.linkedin.com/in/aberdeen-icorr/.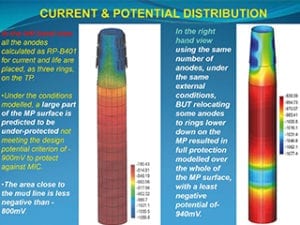
It should be noted that the planned ‘Industrial visit (Oceaneering), an “Alternative / Interactive Industrial Event’, will now take place on 25th August 2020, and readers should also be aware of the upcoming Aberdeen joint event with TWI on 24th September 2020 covering Environmental Corrosion of Fasteners. More details of both events will follow soon on the ICorr website and social media. All of Aberdeen’s remaining 2020 events will be Online.
Brian Wyatt – Corrosion Control Ltd. Example of Advanced CP Modelling used to optimise Galvanic Anode Positioning.
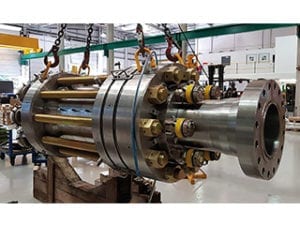
Connector Subsea Solutions Ltd – Andrew Woodward and Chris Matthews. An assembly showing the use of CRA’s in subsea clad pipelines and repair of connections. DNV GL approval was awarded to the CRA clad and lined pipe end seal in December 2019.