Why Do Bronze Medals Tarnish So Quickly?
By Roger Francis, RF Materials
Meet the Author
Dr. Roger Francis
Dr Francis has been a corrosion engineer for over 45 years. He has wide experience in the fields of marine corrosion, desalination, sour oil and gas corrosion, mineral processing, and the chemical and process industries. He has published over 100 technical papers in all these areas, particularly on copper alloys and duplex stainless steels. Roger has written seven books on various aspects of corrosion and has jointly edited three other books. The most recent was on corrosion in desalination plants. Dr. Francis has served on several standards committees working on corrosion testing of both copper alloys and stainless steels. In particular he was involved with the committee turning NACE MR0175 into ISO 15156.The author has served as chair of NACE Europe, two terms as the NACE (now AMPP) European Area Director and also as Chair of NACE STG 32 (Oil and Gas; metals). He was made a NACE Fellow in 2005 for his work in marine corrosion. In 2014 he received the T J Hull Award for his work in publications. In 2012 he set up his own corrosion consultancy business, RF Materials. In 2023, he received the Institute of Corrosion Paul McIntyre award presented to a senior corrosion engineer who, as well as being a leading practitioner in his field, has advanced European collaboration and international standards development.
Bronze has been used for a variety of medals for over two hundred years and given sufficient time without cleaning, they will all tarnish. Figure 1 shows an old coin with different degrees of tarnish on the two sides. Figure 2 is a bronze medal that also shows tarnishing.
There is a wide range of bronze alloys, where the chief alloying element is tin, aluminium, or silicon. The majority of bronze medals used to be made of LG2 gunmetal (Cu/5Sn/5Zn/5Pb) or something very similar. Tin bronzes are reddish, but not as strongly red as pure copper. Other elements may be added to modify the colour, for example, to make it more yellow. However, to cut costs, many modern “bronze” medals are actually brass (Cu/5Zn), which has a similar appearance to tin bronze but is not as corrosion resistant.
When a “bronze” medal is polished and shiny, the metal surface is very active and reacts readily in the air to form a very thin layer of cuprous oxide. This slightly dulls the appearance, but continued exposure to air will enable corrosion to continue, and a thicker layer of reddish brown cuprous oxide gradually forms. Although both alloys form cuprous oxide as the main corrosion product, the zinc or tin substitutes at some of the copper sites in the oxide matrix. Zinc makes the oxide layer less protective, while tin makes it more protective1. If the tin content is high enough, a separate layer of stannous oxide can form, but this is unlikely at 5% tin1. If a medal is exposed to an aggressive atmosphere for long enough, then a second corrosion product can form on top of the oxide layer, as shown in Figure 3. This is a basic copper carbonate, and it is less protective than the cuprous oxide layer.
Bronze has been used for a variety of medals for over two hundred years and given sufficient time without cleaning, they will all tarnish. Figure 1 shows an old coin with different degrees of tarnish on the two sides. Figure 2 is a bronze medal that also shows tarnishing.
There is a wide range of bronze alloys, where the chief alloying element is tin, aluminium, or silicon. The majority of bronze medals used to be made of LG2 gunmetal (Cu/5Sn/5Zn/5Pb) or something very similar. Tin bronzes are reddish, but not as strongly red as pure copper. Other elements may be added to modify the colour, for example, to make it more yellow. However, to cut costs, many modern “bronze” medals are actually brass (Cu/5Zn), which has a similar appearance to tin bronze but is not as corrosion resistant.
When a “bronze” medal is polished and shiny, the metal surface is very active and reacts readily in the air to form a very thin layer of cuprous oxide. This slightly dulls the appearance, but continued exposure to air will enable corrosion to continue, and a thicker layer of reddish brown cuprous oxide gradually forms. Although both alloys form cuprous oxide as the main corrosion product, the zinc or tin substitutes at some of the copper sites in the oxide matrix. Zinc makes the oxide layer less protective, while tin makes it more protective1. If the tin content is high enough, a separate layer of stannous oxide can form, but this is unlikely at 5% tin1. If a medal is exposed to an aggressive atmosphere for long enough, then a second corrosion product can form on top of the oxide layer, as shown in Figure 3. This is a basic copper carbonate, and it is less protective than the cuprous oxide layer.
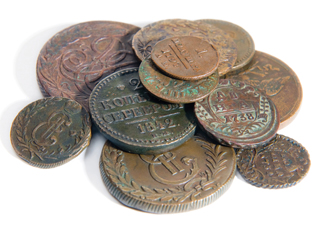
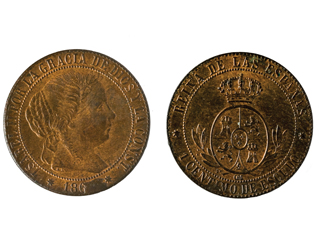
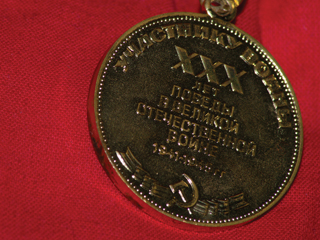
Figure 1: 19th Century Coin Showing Different Degrees of Tarnish on the Two Sides.
Figure 2: Tarnished Medal.
Figure 3:
Old Russian Coins from The Early 19th Century Showing Green Carbonate Corrosion Product.