The Significance of PREN for the Corrosion
Resistance of Stainless Steel by Sarah Bagnall
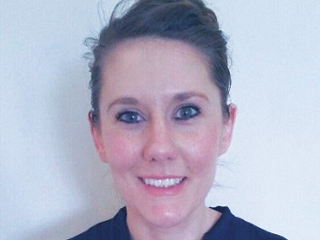
Sarah Bagnall, Director Consultancy Services at R-TECH Materials, CEng. MSc, BSc
Sarah is a materials engineer specialising in failure analysis, for the petrochemical, process, and power generation industries. Currently, she is Director of Consultancy Services at R-TECH Materials. With over 600 failure investigations conducted to date, Sarah has broad experience with a wide range of engineering components, metallic and non-metallic materials, and industries. Sarah has extensive expertise in the corrosion of a wide range of materials, particularly for the chemical processing and petrochemical industries.
- What is the Significance of PREN for the Corrosion Resistance of Stainless Steel?
Calculating PREN and How to Apply it
Stainless steels are well known for their superior corrosion resistance, which is primarily a consequence of the significant chromium addition. When exposed to oxygen, stainless steel forms a passive film due to its 10.5% (or more) chromium content. This film protects the material from rusting and even has self-healing properties. Other elements can be added to further improve the corrosion performance, such as Nickel, Molybdenum, and Nitrogen.
Not all stainless steels are created equal. Different grades exist, and their corrosion resistance can vary significantly. The corrosion resistance between grades can be compared by using the Pitting Resistance Equivalent Number (PREN). The calculation used for PREN is as follows:
PREN = Cr% + 3.3 x (Mo% + 0.5 x W%) + 16 x N%
Examples of stainless steel grades and the calculated PREN numbers are given in Table 1 and Figure 1 below.
Performance in Service
While the PREN is useful for ranking and comparing the different grades for relative resistance to corrosion, it cannot be used to predict whether a particular grade will be suitable for a specific application, where pitting corrosion may be a hazard. All environmental and operating conditions must be taken into consideration.In some industries, notably the oil and gas sector, specifications may place tighter restrictions on the PREN for specific grades than that implied by the minimum composition of the grade defined in EN or ASTM Standards.
In practice, the vast majority of stainless steels deployed across industry are of the 300 series type with lower PREN values, where external pitting is actually quite common in service at ambient temperatures.
Corrosion resistance is not only affected by the chemical composition of the material but also by the heat treatment condition. If the material is heat treated incorrectly during manufacture or welding, microstructural changes can occur which effectively means that
the material is no longer a stainless steel in a localised area. Exposure to temperatures in the range 370-815oC allows the precipitation of chromium rich carbides/nitrides along the grain boundaries. These precipitates are rich in chromium and deplete the area directly adjacent to the boundary of chromium, thereby increasing the likelihood of localised corrosion in the form of intergranular attack, pitting or stress corrosion cracking in a corrosive environment.
Further Guidance
The British Stainless Steel Association (BSSA) exists to promote and develop the manufacture and use of stainless steel across the UK and Ireland. Based in Sheffield, the Association provides technical advice, information, training, and education in all aspects of stainless-steel
usage. They may be contacted at: www.bssa.org.uk
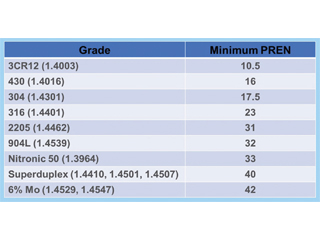
Table 1: Comparison of Stainless-Steel Grades Based on the PREN.
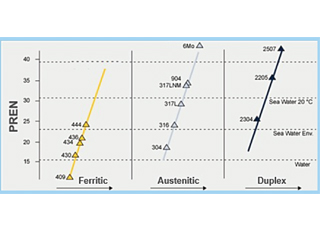
Figure 1. Comparison of Stainless-Steel Grades Based on the PREN
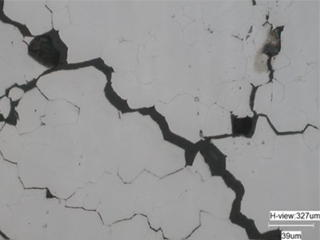
Figure 2. Cracking of a Sensitised Stainless Steel Bolt Which Had Been Heat Treated Incorrectly During Manufacture.