The cart is empty!
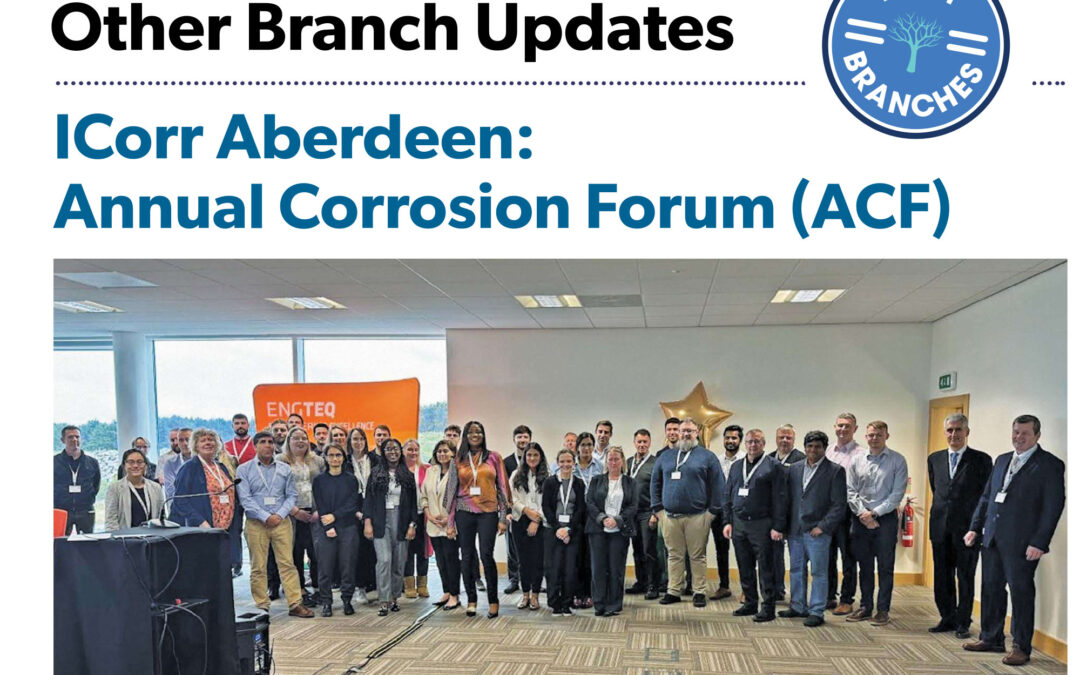
On Tuesday 22nd August 2023 the Aberdeen Branch held its annual fund-raising Corrosion awareness Day (CAD) and welcomed eight corrosion industry speakers along with multiple equipment demonstrations from Rysco, who were ICorr’s host for this one special event. CAD is designed to assist the development of those unfamiliar with Corrosion & it’s prevention and provides and understanding of the corrosion processes and causes which are specific to a range of common industries.
Delegates learnt the basics of the role of the corrosion engineer; including materials selections, corrosion mitigations; failure investigation; testing and design issues.
Delegates – Group Photo
The Welcome was provided by the Aberdeen Branch Chair, Siji Anjorin supported by Dean Smith, Bridge of Don Operations Manager for Rysco U.K for the Safety Moment.
Rysco are headquartered in Calgary and are a global provider of Corrosion Management Solutions. They are both an ICorr Gold Sustaining Member and Aberdeen Local Branch Sponsor.
Compiled: Nigel Owen and Stephen Tate
Dean Smith, Operations Manager for Rysco U.K
A comprehensive series of Talks and Demonstrations followed the Introductions, designed to cover all they key Corrosion Topics.
1. Principles and Costs of Corrosion
Steve Paterson, Ph.D, C.Eng, Arbeadie Consultants provided the opening presentation running through the fundamentals of corrosion and electrochemistry with emphasis on what drives corrosion and the corrosion process of metals. He then outlined the different types of corrosion and common corrosion mechanisms and how these related to the Oil & Gas industry. Internal Corrosion mechanisms discussed were: Acid gas corrosion (CO2/H2S) consisting: CO2 (sweet) corrosion, Preferential weld corrosion, H2S (sour corrosion, Mixed sweet & sour corrosion), Sulphide stress cracking (SSC), Hydrogen induced corrosion (HIC), Hydrogen embrittlement, Chloride pitting/crevice corrosion, Oxygen corrosion, Microbial induced corrosion (MIC) and Sand erosion.
Several methods of corrosion control and management were outlined including:
• Materials selection: The most effective solution that can remove the corrosion threat completely (e.g. CRA/Non-metallic material).
• Water removal by dehydration.
• Chemical treatments (e.g. corrosion inhibitor, biocide or oxygen scavenger) a common mitigation method for internal protection of carbon steels.
• Use of Coatings and linings.
• Anodic/Cathodic protection used to limit and control Corrosion in both internal and external situations.
• Control of process parameters/environment, e.g. by limiting temperature and chloride content can reduce the risk of SCC.
Steve then highlighted the costs and significance of corrosion and demonstrated how implementing corrosion prevention best practices could result in savings of between 15% and 35% with the NACE 2016 study quoting savings of 3.4% of global GDP (Gross Domestic Product), giving immense motivation for corrosion engineers to contribute in achieving such savings and associated improvements in integrity of infrastructure and protection of the environment
2. Materials Selection
Rob Howard, PhD, of Lloyd’s Register discussed materials selection critical to the Oil & Gas processing industry making reference to a process diagram from well to final product, he looked at the common types of corrosion witnessed in the process equipment: A selection of materials for corrosion resistance was reviewed showing how we can move from Martensitic and Austenitic Stainless steels up to Duplex and onto Ni and Titanium alloys to get sufficient resilience, albeit with some heavy cost implications.
Rob Howard graduated with a in Materials Engineering from the University of Cape Town in 1995. and worked as a post-doctoral researcher at the Corrosion and Protection Centre, University of Manchester. He joined Lloyd’s Register in 1998 and at present he is the team leader for the Offshore Materials team in LR, whose main function is to provide technical support to surveyors and clients and to review design specifications for oil and gas and offshore wind projects.
He explained how the choice of equipment materials is influenced by parameters such as corrosivity, flowrates and chloride and hydrogen sulphide levels. However, equally important are the heat treatment condition and mechanical properties required, the corrosion resistance and issues such as weldability and ongoing costs for inspection maintenance and repair of materials selected. Rob referenced a number of international sources which are particularly useful for materials selection and stressed the need to examine Manufacturer capability and quality control of the product:
• Norsok M-001 (edition 5, Sept 2014)
• ISO 21457
• ISO 15156 (NACE MR-0175)
3. Oilfield Microbiology Analysis and Data Trending
Carol Devine, PhD, BSc (Hons) of NICMB has over twenty-five years’ experience in oilfield microbiology. She has a particular interest in microbiologically influenced corrosion (MIC), sulphate-reducing bacteria (SRB), seawater injection systems and molecular microbial ecology in general. NCIMB preserve, store and supply a collection of cultures to industry and universities with the largest collection of industrial, marine and food bacteria in the UK and have approx. 10,000 strains; 300 genera; 2000 species – and still growing.
Oilfield equipment is commonly damaged by the presence and activity of micro-organisms in systems for Production, Seawater Cooling, Water Injection, Cooling/Heating and in handling of Produced Water, Firewater, reinjection (PWRI), Diesel Storage & Ballast Water. The Organisms are either Planktonic from bulk water phases or Sessile biofilms on surfaces.
Carol explained the role of the oilfield microbiologist in generating useful and appropriate data in order to:
• Predict which particular systems, vessels, pipelines, locations are under threat from microbiologically influenced corrosion (MIC)
• Prioritise areas for treatment according to budget and time available
• Apply and monitor appropriate strategies to mitigate against the effects of MIC or biofouling
Techniques for analysis where explained: Triplicate MPN’s, qPCR and Metagenomic Analysis (NGS) to assess the threat of MIC and to quantify, identify and assess the activity which needs to be monitored on a continuous basis to see trends from production changes and implement actions to control and prevent system infestation which affects flow and efficiency in the process.
4. Corrosion Mitigation by Cathodic Protection
Dr. Nigel Owen, B.Sc., D.I.C, Ph.D., MIMMM, MICorr, Aberdeen Foundries has worked in the Aluminium Industry for over 35 years on alloy development and manufacturing processes, spending his later years at Aberdeen Foundries as Sales, Technical and Plant Manager, manufacturing Sacrificial Anodes He now oversees manufacturing, testing and design of all subsea and marine sacrificial anode systems.
Nigel explained how the Galvanic table shows naturally what materials are suitable as bases for sacrificial anodes. Aluminium, Zinc and Magnesium being the primary common bases for development of the alloys. With a sufficiently electronegative potential the base material can be alloyed with other elements to make it more electronegative and efficient as an anode. Aluminium has a high current output per Kg consumed and therefore has become the material of choice for anodes, particularly on large structures.
His presentation covered:
• Alloys for Sacrificial Anodes
• Design of a CP system to protect a structure
• Applications of Anodes
• The selection of the CP system:
• The pro’s and con’s of Sacrificial and Impressed systems and their applications.
The process of designing of a sacrificial anode system was explained from assessment of (cathode) material areas and the effect of coating to the calculation of anode mass and current output for a structure in an immersed environment.
Comparison was made between Sacrificial and impressed current systems in terms of their benefits or advantages in given current demand situations and maintenance requirements. Performance being determined by the conductivity (salinity) and the temperature (water depth/ geographic region) of deployment.
5. Corrosion Mitigation by Coatings
Colin Thomson HND, FM Lead at Bilfinger Salamis, has over 20years experience working in oil and gas fabric maintenance after serving in the Merchant Navy. He has supported various clients FM requirements including, BP, and Conoco Phillips, ExxonMobil and Petrofac. He skilfully explained how Fabric Maintenance prevents corrosion, degradation and wear which could otherwise lead to safety and or operational issues. Coatings acts as a barrier to the environment therefore all locations where coatings are damaged must be maintained to prevent metal loss. Colin also brought everyone up to date with modern FM strategies and also instantaneous barrier methods such as anti-corrosion tapes (ACTs) and Corrosion Inhibiting Waxes.
Various key properties of coatings were highlighted including:
• Anti-Fouling
• Environmental Protection
• Fire Protection
• Process Flow aids.
• Safety
• Thermal protection / insulation
The complete range of surface preparation techniques were evaluated along with all factors affecting coating ‘Life Expectancy’ for example:
• Anchor Pattern (too rough or too smooth)
• Chemical Salts
• Condensation
• Existing Coatings
• Fabrication Defects (weld spatter, sharp edges)
• Mill Scale
• Oil, grease and soil
• Surface Corrosion
6. Corrosion and Chemicals Management
Jennifer Watson HNC, Senior Account Manager/Production Chemist at Champion X is currently based within the BP office supporting Glen Lyon FPSO and has over 20 years experience in Oil & Gas operations offshore and onshore. She enthusiastically described all the key chemical mitigations deployed within the energy sector including:
• Biocides for preventing MIC
• Corrosion inhibitors for internal corrosion
• Drag reduction
• Oxygen and H2S scavengers pH stabilization
Jen also discussed all commonly used monitoring processes and analysis methods for rates, chemical residuals and other dosing checks. Most importantly she emphasised the need for having appropriate Chemical & Corrosion Control Matrices (CCCM) in place. These are the basis for understanding individual threats and how they should be mitigated by applied chemical application or other barriers.
A magnificent Lunch followed with an opportunity for all to network.
One of many Networking Opportunities.
7. Integrity Management and Risk Based Inspection.
Simon Hurst, BSc, MSc has been with CAN since 2008 and is currently the Engineering Director where he is responsible for the ENGTEQ business stream and is the nominated Technical Manager under their UKAS Accreditation for Integrity Management and Pressure Systems Inspection. He commenced his talk by defining Integrity Management – BS ISO 55000:2014 states that it enables an organization to achieve its objectives through the effective and efficient management of its assets. The application of an asset management system provides assurance that those objectives can be achieved consistently and sustainably over time.
Simon went on to define some of the key components of Asset Integrity Management including the following:
• Ageing and Life Extension
• Anomaly Management
• Corrosion Control Matrices
• Failure Investigations
• Integrity Operating Windows
• Risk Based Assessments leading to Risk Based Inspection
He then defined with good detail the nature of risk and the various different methodologies for Risk Based Assessment. In relation to CRA’s Simon usefully highlighted that:
• Although the use of corrosion resistant alloys generally leads to an increase in the time between inspections, the subsequent inspection of those CRAs is normally significantly more problematic than say on Carbon Steel.
• The use of CRAs (v CS) doesn’t normally lead to a significant increase in the periodicity for the first in-service inspection as this is more about identifying fabrication type defects than in-service damage.
In closing he reminded Delegates that it is best practice to create a “Written Scheme of Examination” (WSE) that details the applicable degradation mechanisms, and the precise location and inspection technique that will be used in order to try and either find the mechanism or confirm its absence.
8. Corrosion and Erosion Monitoring
Dean Smith is an experienced Operations Manager in the Corrosion Monitoring industry, having started his career as a Retrievals Technician in 2007 and worked his way up to field services management and eventually operations management. He emphasised that erosion and corrosion pose significant challenges to oil and gas production, impacting safety, efficiency, and profitability and effective monitoring techniques, combined with ongoing innovation and investment, are essential to mitigate these challenges and ensure the sustainability of the industry.
Prior to the practical demonstrations, Dean gave a run-through of the key services of Rysco UK which cover the following:
Design & Supply of Internal Corrosion Monitoring Systems including: High & Low Pressure Access Systems:
• Custom Equipment Design & Manufacturing
• Electronic Monitoring, e.g., Electrical Resistance Instruments
• Injection & Sampling Systems
• Mechanical Monitoring, e.g., Corrosion Coupons
Field Services including: High and Low Pressure Monitoring Device Retrieval.
• Hot Tapping
• Monitoring Data Analysis and Reporting
• Monitoring System Audits
• Sampling and Lab Analysis
Online Reporting including: Custom Reporting Dashboards via Business intelligence Software and Interactive Mapping
Sponsor’s Process Equipment Demonstrations
Three separate demonstrations followed for which the 52 strong gathering was split into 3 rotating groups.
Richard Rae of Rysco U.K explains Integrated Corrosion Data Management
Retrieval Tool Demonstration
Corrosion Coupon Review
A Corrosion Quiz covering multiple aspects of the Speaker Presentations followed by a vote of thanks from the President and CPD awards closed this very successful event attended by over 50 delegates.
Delegates enjoying the Corrosion Quiz
ICorr Aberdeen welcomes suggestions for further Industrial visits.
Abstracts of potential papers for the Aberdeen Technical Programme are always welcome, and anyone wishing to join committee should correspond with the 2023/2024 Technical Programme Co-ordinator: Adesiji Anjorin anjorin@gmail.com
Further Information about the Aberdeen Branch, and past presentations, may be found on their website page: Aberdeen Branch – Institute of Corrosion (icorr.org), and to join the Aberdeen Branch mailing list, please contact: icorrabz@gmail.com
ICorr join forces with IMechE for a special Pre-Christmas Celebration.
On 20th December 2023, the Aberdeen ICorr Branch were guests of IMechE for a Joint Event at the Sandman Hotel in Aberdeen. This end of year Celebration that was very well attended with around 60 guests and was chaired by Steve Cromar CEng, FIMechE, IMechE Aberdeen Chair. The evening commenced with a welcome Hot Buffet Dinner, which was an excellent choice for a cold Winter night.
Tom Baxter a Chemical Engineering Consultant and founding member of the Hydrogen Science Coalition spoke on ‘Future Energies and Greenhouse Gas Reduction’.
Tom Baxter BSc (Hons), FIChemE
Tom graduated from Strathclyde University in 1975 with a B.Sc. in Chemical Engineering (first class honours) and is a Fellow of the IChemE. He started his career with ICI Petrochemicals, moved to fine chemicals with the Swiss company Ciba-Geigy before taking a position as a Process Engineer in 1980 with BNOC (British National Oil Corporation). Through privatisation and acquisitions BNOC became Britoil, then BP. Here he worked as an Operations Engineer, Development Engineer and Research Manager. In 1991 he left BP subsequently held positions with Altra Consultants as Technical Manager, as Technical Director with Genesis in 1998 and became the Aberdeen Business Unit Director in 2005. From 2010 together with became a Senior Fellow in the Chemical Engineering Department at Aberdeen University, which he helped establish and since 2003 he has been a visiting Professor of Chemical Engineering at Strathclyde University.
This coming decade is extremely important for achieving reductions and Individual impacts are great. During his most interesting talk key themes discussed were ways to use less energy and an eye-opening debate on the misconceptions about renewable alternatives, (in terms of actual energy efficiency breakdown from production through to final distribution) which was considered in great detail. Overall electrification came out as a very safe and efficient energy source.
Industrial Hydrogen Use
Hydrogen (H2) does have some favourable characteristics – particularly buoyancy and no carbon monoxide but has low caloric value. Generally, Hydrogen compares unfavourably overall with Methane properties and has limited applications presently. For example, it requires three times the amount of compression power to move it along pipelines and much talked of blending Hydrogen was not seen as a good idea although a 20% blend has much promoted of late by others presenting to the Institute.
H2 is considered applicable for Transport (although passenger car-dominated) and for some specialised industries e.g. steel making. There have been recent question marks over some H2 driven projects. Pau (in France) cancelled its H2 buses and the Redcar hydrogen project was recently cancelled.
Full electric vehicles are seen as most energy efficient, for trains only low train passenger routes in the UK (8ookms out of 15000 kms) but there are lots of Hydrogen miscellaneous uses, but batteries are the key to the future progression of renewables. Presently the accurate Hydrogen retail cost is not clearly defined.
Tom Baxter (seated) Chemical Engineering Consultant and Hydrogen Expert presented.
Tom also spoke of https://www.h100fife.co.uk/ a parliamentary party group with interests including Cadent / Shell / others – Projected costs to 2050 however are not considered reliable.
Domestic Hydrogen Use
Vested interests e.g. Catapult and EUA have recently promoted Hydrogen for heating. Tom reviewed the outcomes of hy4heat – Hy4Heat Its mission was to establish if it was technically possible, safe and convenient to replace natural gas (methane) with hydrogen in residential and commercial buildings.
Through a QRA study, they found that Hydrogen was inherently less safe than Methane QRA with three times as many potential events. Hydrogen usage requires more safety features and is 40% less energy efficient overall. Electric energy provides greater wattage.
Summary
Generally, with renewables, more government support is needed, so as to give more headroom / opportunity to recover capital cost over a longer period.
Tom Baxter was extremely knowledgeable and provided a most interesting talk.
Refer www.h2sciencecoalition.com
Members of the Aberdeen ICorr Committee, with new member Stephanie Okoye 2nd from Left, with guest Shukun Liu (Oceaneering) far right.
Q&A
A lively Q&A followed:
Future Meetings
The Aberdeen Branch of ICorr hopes to continue its relationship with IMechE during the next Technical Session 2024-2025
IMechE Aberdeen meet on the third Wednesday of each month and may be contacted at:
Contact the Aberdeen Area – Institution of Mechanical Engineers (imeche.org)
ICorr Aberdeen meet on the last Tuesday of each month and may be contacted at:
Initiated by Council and CP Governing Board member Bryan Wyatt, the Institute exhibited at Floating Offshore Wind (FOW) Expo 2023 (Conference & Exhibition) on the 4th and 5th of October 2023.
This unique operator and service provider event comprised around 100 Speakers, 200 Exhibitors and 2000+ high level attendees from around the globe.
ICorr Council and CP Governing Board member Bryan Wyatt (seen presenting at CEOCOR)
FOW is the meeting place for all the current and future players in the global floating wind industry. Providing an unrivalled opportunity to meet and network with all the key players as well as discuss the key technical challenges and solutions surrounding the industrialisation and commercialisation of floating wind.
ICorr’s participation was very successfully handled by the Aberdeen Branch and attracted a wide range of stand visitors. The key focus for this Event was our Training Services – Industrial Coating Applicator Scheme (ICATS) and ICorr’s Cathodic Protection and Coating Inspector courses that promote independent reporting to Facility Owners, (as now required in DNV-RP-B401 for their Cat IV coating). The highest levels of Competency, Specification and Performance Assessment at all stages from Design onwards are essential to maximise FOW Equipment life with Operators now seeking up to 35yr lifespans.
In the Cathodic Protection World, initial FOW structures were designed to RP-B401 which provides good guidance for conventional fixed jackets but is considered inadequate for monopiles or floating turbines. Latest available standards however, (the improved) RP-B401 and (the new) ISO 24656 require design by a competent, experienced CP Engineer/Expert (and Level 4 certification is the best measure, noted on both DNV and ISO).
One of the Key Objectives of our participation was to help drive Quality throughout the FOW Industry.
ICATS and ICorr’s presence at the Expo resulted in more than 60 high quality leads and around half of these were enquiries related to our existing –‘Training Services’ and others requesting new courses specifically covering the updated RP-B401 – 2021 and (the new) ISO 24656 – 2022 standards.
The Event provided excellent FOW Industry engagement and neatly followed our very well attended North-East branch sustainability conference. North East Branch – Institute of Corrosion (icorr.org) refer Local Technical Programme – 2023 Presentations.
On 17th November 2023 the Aberdeen Committee, as close partners of the North Scottish Branch of The Welding Institute (TWI) were invited to attend their 38th Annual Dinner, held at the Aberdeen Altens Hotel. This year the TWI are celebrating their 100th Anniversary.
Aberdeen Branch Committee Members – L to R, Mei Ling Cheah (former YICorr Officer and now Vice Chair), Steve Paterson (YEP Mentor’s and Case Study Co-ordinator), Lian Ling Beh (Secretary Internal), Nigel Owen (Secretary External), Eilidh Macdonald (2022 YEP Winner and now Events Co-ordinator) and Leela Ramachandran (University Liaison & CPD Officer).
There were some truly excellent presentations by Brian Bell (TWI Chairman), Katy Heidenreich (OEUK – Offshore Energies UK, Supply Chair and People Director) and Stephen Anarach (TWI- Oil and Gas Energy Transition Manager).
Later guests from across Energy companies in Aberdeenshire, were greatly entertained by Gordon Smith, former CEO of the Scottish Football Association and professional footballer who made 490 league appearances, six international appearances and scored 117 goals for teams including Brighton, Kilmarnock, Manchester City, Oldham Athletic, Rangers and Stirling Albion.
With some hilarious storytelling, Gordon told us what really goes on behind the scenes in the football world and some key life lessons from his own experiences.
The Aberdeen Branch expresses its sincere thanks to the committee of the TWI North Scottish Branch for making this all possible.
Details of their current officers may be found at: www.theweldinginstitute.com/member-benefits/branches/north-scottish-branch
Corrosion rates determined from Non Destructive Testing ( NDT) generally trend toward wall loss percentile values as the principal criteria. Looking at group trends mitigates measurement error and gives more accurate short and long-term corrosion rate estimates. Any point showing a concerning trend can be extrapolated to predict when an alarm limit may be reached. Corrosion rate data can be plotted in different ways to try and identify issues such as localised and unusual corrosion rates. Lots of data on wall thickness measurement may just behave in a linear sense such as presented here for selected years and locations – nothing unusual is shown and general corrosion is happening at expected rates.
Sonomatic have developed 3 different inspection planning methodologies. The Type 2 methodology was further discussed with steps detailed below:
Notifications