The cart is empty!
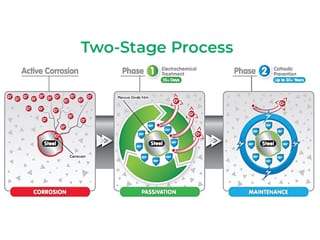
Aberdeen Branch – mitigation techniques for the civil engineering and construction industries
During March, the branch welcomed Dr George Sergi R&D Technical Director at Vector Corrosion Technologies, which, provides corrosion mitigation techniques for the civil engineering and construction industries. He is the author of several international patents for corrosion protection of steel reinforcement and these were discussed in a talk entitled “Galvanic Corrosion / CP Control of Reinforced Concrete; Lessons learnt from 20 years of Site Trials”.
Sacrificial anodes have been used in reinforced concrete structures for up to 20 years. These prototype anodes, designed for a 10-year life, have continued to deliver a reduced but significant current, complying with presently accepted CP criteria. However, there are still issues with patch repair of concrete with the condition of the re-bars not being fully understood, and corrosion re-occurring at the periphery of the repairs termed ‘ring effects’. Studying long term installed conventional sacrificial anodes and identifying the issues, has led to the development of a new Fusion™Anode, which seems to solve the issue of recurring corrosion
at repairs.
In order to prevent the initiation of corrosion in a chloride contaminated environment, the current density needs to be 0.4 to 2 mA/m2, much lower than the amount necessary to stop on-going corrosion activity which is 2 – 20 mA/m2. The zinc anodes used for this new technology are encased in a high porosity mortar (to accommodate migration of corrosion products), and also saturated with lithium hydroxide.
Site trials on a bridge in Leicester 20 years ago involved the removal of concrete to reveal the re-bar area, and attachment of anode discs at the peripheral areas of the patch, but, rather than wiring to the rebar, the anodes were wired back to a junction box wired to the steel reinforcement, which meant the anodes could be turned off and on, current could be measured, and the polarisation could be monitored. The zinc consumption could also be monitored and calculated from the Faraday Equation.
Monitoring showed that the cumulative charge from the anodes is linear w.r.t. time for first 5 years then the charge started to fall, perhaps due to the saturation of the Li hydroxide mortar. Tests showed that by disconnecting the anode for 24 hrs then reconnecting, the mean ‘instant on’ current could be established for the anodes within 5secs of reconnection. This represents the power which remains within the anodes – which was 1-1.5mA. After 14 days the current dropped to 0.5mA; this coincided
with LiOH saturation witnessed in the sections.
Looking at the current density (CD) over the 20 years and plotting on a log scale it was seen that the decline of CD was actually exponential. From this study, an ‘ageing factor’ could be determined as to how quickly the protective current halved; this was ~7 years, it then halved again after 14. The study of many other sites enabled ageing factors from sites to be compared, and by reducing the anode spacing by ~1/2 the ageing factor achieved could almost be doubled. It was concluded that the service life of existing standard galvanic anodes used in concrete repair is expected to be between 15 years and 30 years.
As a result of these long-term studies of standard galvanic disc anodes, the New Fusion™ Technology was further developed to have an anode with two stage protection using a battery which first delivers impressed current to arrest corrosion and passivate the steel and then a galvanic anode using a small ’cathodic prevention’ current to maintain the passive state for the remaining life expectancy. This product is an ICCP element and galvanic element with electronics, encased in a stainless steel can and surrounded by alkaline mortar. In laboratory tests, the installed anodes were switched on and off in the ICCP stage to check the polarisation level and the effect of wetting the slab, seen as an increase in the current density. Similar confirmations can be obtained during the galvanic protection phase. Site tests were also conducted to optimise and monitor the spacing, current levels and configuration of the anodes.
From the development work it was established that the key factors were:
- An initial charge at the top end of CP current densities that can arrest corrosion of steel.
- The level of applied charge to achieve corrosion arrest depends on the corrosivity of the concrete environment and the level of applied current density.
- Confirmation that passivation of steel can be maintained long-term with galvanic anodes.
During polarisation of re-bar in concrete it was witnessed that the chloride ions started to move away from the steel and hydroxyl ions are produced at the steel. This led to a reduced Cl_/ OH_ ratio and a reduced corrosion risk with high alkaline levels at the steel interface and low chloride, increasing with distance from the steel. It was also determined that with higher current densities such as can be produced by impressed current technology, highly alkaline areas, above that of base concrete alkaline levels, can be created at the steel which contributes to reversing the corrosion process. Lab tests using between 1% and 3% chloride showed that it took longer to passivate the steel the more residual chloride in the mix at a current density = 30mA / m2 to the steel reinforcement. By extending the experiments, the charge required to passivate the steel
and arrest corrosion at various chloride levels was established.
In summary, George highlighted the benefits from higher levels of current possible by ICCP in the initial years of installation in order to passivate the steel and create more favourable alkaline conditions at the reinforcement for forward protection by GACP.
Again, due to COVID restrictions, the annual joint conference with the Marine Corrosion Forum (MCF) was reformatted as a lunchtime webinar week, held with great success between 26-30 April 2021. Attendances averaged 77 per day and exceeded all expectations, which suggests that the way forward will most definitely be that of blended learning, possibly with live streaming of ‘face to face’ events to our international audience (ICorr itself having nearly 600 overseas members}.
Day 1 featured, Ray Sivarajan, Senior Integrity Engineer and Bill Hedges. Corrosion & Integrity Management Consultant for ICR – OMNI, presenting their “Novel integrity operating system” which uses machine learning to give integrity engineers a continuous and holistic understanding of their business assets in real time. Organisations today face increasing challenges in the changing geopolitical and industry dynamics, which can have huge impacts on the overall success of the business. Constraints such as resource and experience shortages make it ever more difficult for organisations to achieve the efficiency levels required to maintain profitability, whilst maintaining safety and environmental levels. The software boasts built-in automation between modules, workflow tracking and notifications – a first of its kind for integrity software solutions taking visibility and control of integrity activities to a new level. Each module can be used alone to integrate with existing integrity systems, or seamlessly used together as a complete solution – to support organisations in their efforts of digitising their full integrity lifecycle. Further information is available at, https://icr-world.com/omni
Day 2 saw Michael Smith, Senior Engineer Data Scientist with ROSEN UK discuss “Virtual in-line inspection for corrosion management in un-piggable pipelines”. Over the past 30 years, vast amounts of ILI data have been collected all around the world. Although pipelines are diverse in their characteristics, many share similar risk profiles for common pipeline threats such as external and internal corrosion. This has led the industry naturally towards machine learning as a complementary corrosion monitoring solution for pipelines that cannot be inspected using ILI. The results of a “Virtual ILI” create clear justification for planning actual inspections or maintenance in challenging pipelines and for a given uninspected pipeline, it is possible to now source data for similar inspected pipelines and use machine learning algorithms to generate predictive models.
Day 3 profiled Ross Hubble, Applications Engineer with COMSOL, who gave a very modern insight into “Modelling Corrosion and Corrosion Protection”, and discussed some of the benefits of corrosion modelling and what kind of simulations can be performed, starting out with a brief introduction to corrosion simulations and how the theory can be applied to a simulation in the proprietary Multiphysics® software. After the introduction, several modelling examples within the corrosion and corrosion protection field were presented. Modelling allows engineers and scientists to investigate these processes and gain a better understanding of the extent to which corrosion could occur over the lifetime of a structure, and implement preventative measures to inhibit this.
Day 4 had Hamed Habibi, Lead Engineer with Spier Hunter, deliver a most interesting presentation on “Developments in remote magnetic monitoring of carbon steel pipelines to locate and measure abnormal stress”, highlighting recent developments in an emerging non-intrusive sensing technique developed to detect localised abnormal pipe wall stress, such as corrosion and metallurgical defects by mapping variations in the earth’s magnetic field around pipelines. This presentation explored how measurements of remote magnetic field can be applied to define the location of defects in operational pipelines, quantify the associated abnormal stress, report the position of girth welds and to concurrently report a 3-dimensional map of the pipeline route.
Day 5 concluded with Daniel Sandana, Principal Engineer of ROSEN UK, presenting “Addressing the risk of Hydrogen-Induced Stress Cracking on Pipelines”. The role that hydrogen could play in the transition to low-carbon economy has refuelled the emphasis on hydrogen-related cracking mechanisms, and how these could affect the integrity of the energy infrastructure. Hydrogen-cracking mechanisms can nonetheless occur on our existing pipelines, when the effect of CP or H2S is considered. Such mechanisms will actually occur at a greater scale than what would be considered when looking at the sole effect of gaseous hydrogen. The purpose here was to get a better understanding of the problem of HISC due to CP on materials, used onshore and subsea, and how to address it.
Dr Yunnan Gao (Aberdeen’s Digital Strategy and Communications Officer) kindly compiled an all-encompassing Playlist called “ICorr / MCF Webinar Videos in April 2021”. This may be found on: https://youtube.com/playlist?list=PL-Hz5BsB9C8JB5fGT6Ubsy-rK0ITrYlU2
Looking ahead, the branch is very pleased to announce the return of its annual corrosion forum on 31 August 2021 at TRAC (The Rope Access Company),
an enthusiastic supporter and branch sponsor of Aberdeen for many years. The day will comprise a full range of corrosion awareness talks in the morning and many interesting demos in the afternoon. To register advance interest in this event please contact the ABZ events officer, Amir Attarchi, at amirattarchi@gmail.com, giving your full name and company.
Before that, members of the branch will be supporting the SPE virtual oilfield corrosion conference and exhibition, where industry leaders discuss recent innovations, trends, and concerns as well as practical challenges encountered within the oilfield corrosion community. See http://go.spe.org/lic6268, and for which registrations are now open at: https://www.spe.org/events/en/2021/conference/21ofcs/register.html
Finally, and certainly not least, we are very pleased to welcome our new branch chair, Hooman Takhtechian, who takes up his new role after several years as a committee member, and to thank Dr Muhammad Ejaz for a very successful 2020-2021 season.