Aberdeen Branch, Latest News
Branch News Aberdeen Branch
Following on from the success of its week long April joint webinar event with MCF, ICorr Aberdeen held its 8th event of the 2019/2020 session during 6-10 July 2020 with a very comprehensive marine focussed ‘Webinar Week’ comprising of some excellently delivered papers by:
• Roger Francis, (RF Materials – Improving the Corrosion Resistance of Duplex Stainless Steel Welds).
• Adnan Syed, (Cranfield University – Hot Corrosion Mechanisms for Gas Turbines).
• Lars Lichtenstein, (DNV GL – Improvements of the DNVGL-RP-0416 and DNVGL-RP-B401 – Upcoming Revisions).
• Brian Wyatt, (Corrosion Control Ltd – Cathodic Protection of Offshore Renewable Energy Infrastructure).
• Andrew Woodward and Chris Matthews, (Connector Subsea Solutions Ltd – Use of CRA’s in Mechanical Connectors for CRA Clad or Lined Pipe Repairs).
The heavily over-subscribed webinars, which had more than 500 attendees, were jointly chaired by Phil Dent (MCF) and Stephen Tate (ICorr-ABZ), with Lewis Barton (MCF) as webinar facilitator.
This time around, a very effective 4-pronged promotional attack was deployed, with excellent Social Media blogs provided by Michael Barton for the HQ website, Dr Yunnan Gao promoting at the Aberdeen end, Lewis Barton via the MCF website and LINKEDIN pages, and further additional support provided by Gareth Hinds and Brian Wyatt of ICorr Council.
There was excellent participation by the attendees via Web Chat for all the Q&A Sessions, and all the presenters’ responses are also now loaded onto the ICorr/MCF websites.
All the webinar presentations had excellent technical content that highlighted the particular challenges of the marine environment, in terms of correct materials selection, correct application of corrosion control methods, the importance of good quality control at fabrication, and having appropriate inspection and maintenance regimes.
Roger Francis discussed in great detail the development of modern Duplex stainless steels from the early 1980’s onwards, with particular emphasis on the jointing processes / joint design and how to avoid corrosion failures of welds resulting from disturbed metallurgy, the importance of having adequate post-weld treatments / checks, (such as post-weld pickling / use of shielding welding gases during fabrication and the use of Feritscope checks on the HAZ of production welds that can be used to measure the ferrite content through magnetic induction), and in also having suitable weld testing programmes in place at fabrication stage, over and above that of ASME IX, and he proposed some suitable tests. Roger also emphasised the need to perform corrosion tests not just on the PQR (Procedure Qualification Record), but also based on the individual welder qualifications, in order to ensure that each welder fully understands what is necessary to produce an acceptable’ weld quality.
Adnan Syed described a very interesting journey through hot corrosion mechanisms of jet engines and industrial gas turbine components, (this being a well-known issue for the aviation and power generation industries). The talk included the possible hot corrosion mechanisms occurring in the gas turbine combustion environment, and some of the challenges industry is facing in their understanding and managing of turbine component degradation. He discussed the two main types of attack: Type I (high temperature corrosion) attack, in the range of 750 to 900 C, mainly due internal sulphidisation, and Type II (low temperature hot corrosion) attack, at temperatures in the range of 600 to 750 C (maximum rate of attack in the range of 675–730 C) and associated with pitting type attack. The importance of good alloy quality and the prevention of corrosion damage related to salt deposit chemistries was emphasised, along with ongoing Cranfield laboratory corrosion experiments and the use of thermodynamic software to help identify the phases formed, which in turn enables a better understanding of the mechanisms involved
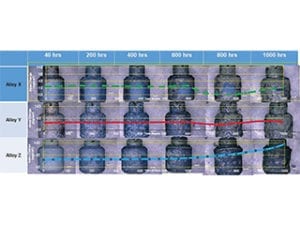
Cranfield University – Adnan Syed. Examples of macrographs and mass change data for high temperature corrosion testing.
Lars Lichtenstein then considered the harsh operating environment for Marine Wind Turbines being increasingly deployed in our coastal waters, bringing us up to date on ongoing revisions to DNV GL documents on corrosion protection for wind turbines (which are under internal revision), DNVGL-RP-0416 and DNVGL-RP-B401. Changes highlighted included more guidance on the useful coating lifetime as introduced in DNV-OS-J101:2011 for the first time, and the relation with fatigue calculation and surface preparation, including the need for weld grinding. In particular the level of coating quality required at the end of the lifetime, and the degree of effort needed to be put into inspection and repair of 15+ year old coating systems, so as to ensure ongoing integrity. Lars also discussed the issue of coating breakdown factors with regards to CP system calculation and on current drain of buried structures. He further highlighted new information on material selection for bolts and stainless steel, and what boundary conditions should be considered.
Brian Wyatt nicely linked into the previous day’s discussion on standards and recommended practices and emphasised the multiple zones / environments requiring many different corrosion control considerations / solutions within the Wind Energy Sector.
He highlighted the lack of competency seen in some projects performed to date and gaps in guidance that urgently require to be addressed as the renewables industry accelerates in scale. Velocity effects are a particular consideration resulting in increased levels of oxygenation at the steel/water interface which demand more robust CP designs, both in mechanical and electrochemical terms. The nature of the support structures, and limited scope for lower cost onshore anode installation, also lead to challenges to uniform anode distribution, particularly on Monopile type structures that replaced the earlier jacket type wind farm structures, that were more similar to the established requirements and practices of the Oil and Gas Industry, for which earlier DNV Codes were intended to cater for (editor, see technical article later in this magazine).
Andrew Woodward and Chris Matthews wrapped up the week with a great talk on outcomes from their recent joint industry project (JIP) with Chevron and Woodside Petroleum, as part of a new technology development programme in line with DNVGL-RP-A203. They have recently developed a new patented method of sealing on the inside of a CRA clad or lined pipe, thus enabling a permanent subsea repair solution. The new seal in the “CLiP” Connector takes advantage of the corrosion resistant and ductile properties of Alloy 625 (UNS N06625) and experience gained through extensive testing of graphite in order to create a seal that conforms to NACE MR0175 / ISO15156-3. The seal forms around all pipeline manufacturing tolerances and even localised irregularities such as internal weld seams. The seal can be easily integrated into existing mechanical connector configurations and is able to be adapted for both diver installed and remote repairs. The technology qualification was completed through a combination of analysis (including development of a parametric FEA model to cover all future design scenarios), 3rd party material testing, and component testing in specialised test rigs; all culminating in full scale testing within a mechanical connector. The presentation focussed on the analysis and testing aspects of the technology qualification process which highlighted all key failure modes that had to be addressed.
There has been much debate of late concerning the impacts of the coronavirus outbreak, but the success of these recent Joint and Online Events has proven beyond doubt that such obstacles can be overcome and that the thirst for corrosion learning remains as strong as ever.
As usual, full details of future branch events can be found on the ICorr Website, or by contacting: ICorrABZ@gmail.com, and copies of the majority of past branch presentations can be found at: https://www.icorr.org/aberdeen/ and a photo gallery for all Aberdeen events may be found at: https://sites.google.com/site/icorrabz/event-gallery. See also ICorr Aberdeen on LinkedIn at https://www.linkedin.com/in/aberdeen-icorr/.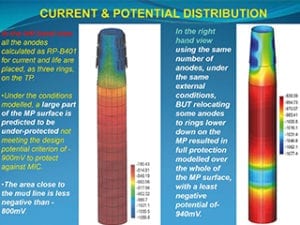
It should be noted that the planned ‘Industrial visit (Oceaneering), an “Alternative / Interactive Industrial Event’, will now take place on 25th August 2020, and readers should also be aware of the upcoming Aberdeen joint event with TWI on 24th September 2020 covering Environmental Corrosion of Fasteners. More details of both events will follow soon on the ICorr website and social media. All of Aberdeen’s remaining 2020 events will be Online.
Brian Wyatt – Corrosion Control Ltd. Example of Advanced CP Modelling used to optimise Galvanic Anode Positioning.
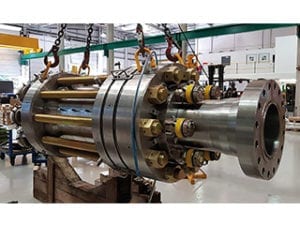
Connector Subsea Solutions Ltd – Andrew Woodward and Chris Matthews. An assembly showing the use of CRA’s in subsea clad pipelines and repair of connections. DNV GL approval was awarded to the CRA clad and lined pipe end seal in December 2019.
Aberdeen Branch, Latest News
Pictured: Adam Lea-Bischinger, CEng CMgr MEng CMRP Eur Ing, Snr. Consultant with Fokus – Reliability and a Specialist in Asset Management and Performance Improvement.
The branch held its 7th event of the 2019/2020 session, on 27 April. This was the first of 5 technical presentations of the annual joint Institute of Corrosion/MCF (Marine Corrosion Forum) programme, held Online this year over 5 days, due to the COVID crisis. The heavily over-subscribed webinar was jointly chaired by Phil Dent (MCF) and Stephen Tate (ICorr-ABZ) with Lewis Barton (MCF) as webinar manager and with Dr Yunnan Gao (ICorr-ABZ) and Institute of Corrosion HQ jointly promoting.
The branch was very pleased to host Adam Lea-Bischinger, a Snr. Consultant with Fokus – Reliability, who currently holds several roles in Aberdeen including, Branch Chair of IAM – Institute of Asset Management, online course tutor in Asset Management for the University of Aberdeen, and Snr. Advisor to the Board of Pavan Asset Value Managers.
Adam has 15 year’s experience working in maintenance, reliability, asset management and inspection covering major oil and gas, power, mining and infrastructure projects worldwide, and holds a masters degree in Engineering, Materials and Corrosion with post graduate training in Inspection and NDT.
Adam spoke enthusiastically on asset management and how it can deliver value to an organisation. He carefully described the six core elements of asset management, the work of IAM, and the development and roll-out of ISO 55000:2014 which defines terminology, requirements and guidance for implementing, maintaining and improving an effective asset management system, and gave examples of UK and overseas companies operating the ISO 55000 system, including many utilities, major transport operators and drilling companies, who all having significant investments to protect and maintain for their full life-cycle.
The now established standard has three key parts:
ISO 55000 – Asset Management – Overview, Principles and Terminology
ISO 55001 – Asset Management – Management systems – Requirements
ISO 55002 – Asset Management – Management systems – Guidelines for the application of ISO 55001
According to the IAM, “These three international standards are important not only for their content, but because they represent a global consensus on what asset management is and what it can do to increase value generated by all organizations.”
The conceptual model, developed by IAM to show the core elements of the ISO 55000 series standard containing six main groups and thirty nine subjects is detailed below:
• Strategy & Planning
• Asset Management
Policy
• Demand Analysis
• Strategic Planning
• Asset Management
Planning
• Organisation & People • Procurement & Supply
Chain Management
• Asset Management
Leadership
• Organisational
Structure
• Organisational Culture
• Competence
Management
• Asset Information
• Asset Information
Strategy
• Asset Information
Standards
• Asset Information
Systems
• Data & Information
Management
• Decision Making
• Capital Investment
Decision Making
• Operations &
Maintenance Decision
Making
• Lifecycle Value
Realisation
• Resourcing Strategy
• Shutdown/Outage
Strategy
• Lifecycle Delivery
• Technical Standards
• Asset Creation/
Acquisition
• Systems Engineering
• Configuration
Management
• Maintenance Delivery
• Reliability Engineering
• Asset Operations
• Resource
Management
• Shutdown/Outage
Management
• Fault & Incident
Response
• Asset Disposal
• Risk & Review
• Risk Management
• Contingency Planing
• Sustainable
Development
• Management of
Change
• Asset Health Monitoring
• AM System Monitoring
• Management Review
• Asset Costing &
Valuation
• Stakeholder
Engagement
The importance of team-working and good communication was heavily stressed, so as to achieve good LOF – Life of Field Design, and to avoid the too often prevailing SILO (compartmentalised) type mentality within organisations.
An extensive Q&A followed with questions on topics such as the use of ‘Hands-Free’ asset management software, conditioning monitoring, cyber security threats from wireless devices, and the management of ‘Late Life’ assets. Various aspects of implementation of ISO 55000 guidance were also discussed and highlighted global differences in asset management methods and regulation.
Following from the success of the April webinar with MCF which had an attendance exceeding 70 on all 5 days, it is now planned that the Institute of Corrosion will work together with MCF to continue the close co-operation now established, for its July meeting, in Birmingham, with webinars running between 6-10 July 2020, as the resumption of ‘Face to Face’ meetings is not being expected before that date.
On the 29th April, members of the Aberdeen Branch also participated in the online CED Working Day and Symposium on ‘Corrosion Control in Transport and Infrastructure’, with Alistair Seton of the Aberdeen Committee chairing the Oil and Gas Working Group.
There has been much debate of late concerning the impacts of the coronavirus outbreak, but both the Institute of Corrosion/MCF Webinars and the CED Online event, has proven beyond doubt that such obstacles can be overcome and that the demand for corrosion learning by whatever method, is as strong as ever.
As usual. full details of future branch events can be found on the ICorr Website, or by contacting: ICorrABZ@gmail.com. Copies of the majority of past branch presentations can be found at: https://sites.google.com/site/icorrabz/resource-center, and a photo gallery for all Aberdeen events may be found at: https://sites.google.com/site/icorrabz/event-gallery.
It should be noted that the planned Aberdeen event of Tuesday 23 June – ‘Industrial visit (Oceaneering), an Alternative / Interactive Industrial Event’, is currently postponed (awaiting Scottish Government instructions), with a new date to be advised, as soon as is possible.
Aberdeen Branch, Latest News
The branch held its 5th event of the 19/20 season at RGU Aberdeen, with a paper entitled “Structural Integrity Issues: under-deck, air-gap, splash zone assessment / deterioration / repair mechanisms, (for corroded / fatigued conductors, caissons and risers)” by Chris Tierney, SETS. This was a highly successful 1st joint presentation with EI – The Energy Institute, with
75 attendees.
The first part of the presentation considered, conductor integrity, hidden risks and corrosion mitigation, and in the second part Chris discussed new platform-launched technologies for repair of caissons and conductors subsea on ageing assets. After a decade in the subsea engineering sector with Technip, Chevron Upstream Europe, and Pro Dynamic Lifting (PDL), Chris founded SETS in 2011 as a subsea engineering and consultancy specialist. A platform splash zone is an area of multiple risks to production due to the high likelihood of mechanical damage to elements running through this area, cracking and in some geographical locations, very high corrosion rates. SETS provide innovative, engineering and tooling services to deliver efficient conductor management and repair solutions. The company have continued to innovate, learn and produce solutions for this difficult work zone and have been at the forefront of the design and development of technically advanced subsea tooling for conductor cleaning and inspection, clamp repair and shim installation. Unusually, their technology is remotely operated from topside, eliminating the requirement for diver support, and dramatically reducing time and cost. Their success in this area has resulted in the recent acquisition of the company by AquaTerra ( Kintore, Aberdeenshire).
The SETS presentation concentrated on conductors but the technology is equally applicable to caissons and risers. Conductors run from seabed to wellhead, providing environmental protection to the most vulnerable well components. A conductor should be considered a complex system, and its integrity managed accordingly, spanning wells, structural and operational functions. The condition of conductor and guide frames at the spider deck reflect the condition of these at the first elevation subsea. These are the most highly utilised areas in a conductor system, subjected to the greatest environmental loads and generally where majority of defects present themselves. The presentation discussed in detail, marine corrosion, fretting, fatigue, damage mechanisms and progression rates affecting conductors on ageing assets. Chris explained how different marine environments worldwide impact on conductor, caisson and riser integrity and following this, there were many thoughtful questions from the audience.
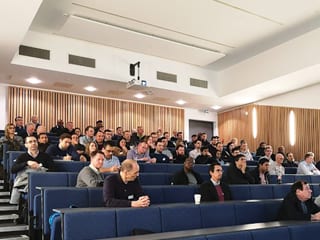
A full house, attended this first IE/ICorr joint event.
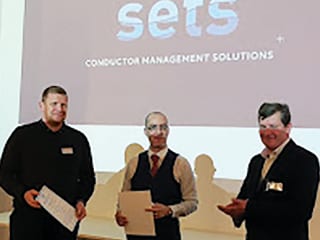
Branch chair, Stephen Tate, closes the event with Certificates of Appreciation to Roy Milne (Vice Chair of EI – Energy Institute and Chris Tierney, Managing Director of SETS.
The February 2020 evening meeting with 55 attendees opened with a discussion of the new ICorr logo and re-branding of the Institute to provide a much needed re-start and more professional focus, with the key being firmly on corrosion prevention by all available means. Following this introduction, there were very informative twin presentations by DNV-GL on risk based inspection activities, covering both PSVs (Pressure Safety Valves) and FPSO’s (Floating Production, Storage and Offloading) units.
The first presentation, by Dr Chris Bell discussed how data analysis of servicing has helped reduce cost and improve safe interval servicing of PSVs. PSVs are installed in process and utility systems to prevent build-up of internal pressure, or external effects such as fire. Over pressurisation of any vessel, or other equipment item, with energy released from the pressurised fluid, or the hazardous or flammable nature of the contents, can have significant consequences on a platform. Valves can block through build-up of wax, gunk or corrosion products within the system and the PSV will fail to lift. For this reason, PSVs are classed as safety critical when protecting hydrocarbon containing equipment and must be safety tested on a regular basis. The testing cannot generally be done in-situ, and valves most usually have to be taken onshore, tested, refurbished and refitted. Typically there are over 100 PSVs on a platform so it is worth optimising the maintenance interval. This can be done by data analysis to find the appropriate time to service the valve based on previous history and ensure a safe practice whilst minimising costs, and the inspection interval can be set so that the residual risk of failure is acceptable.
0.5 billion hours of service data for PSVs have been analysed from 10,311 tests and 544 failures by DNV-GL to allow optimisation of maintenance intervals and manage the inspection of PSVs. A methodology was developed that combined qualitative and quantitative RBI analysis. This multi-layered assessment gained the most information possible from the data, and as an outcome, the average maintenance interval was changed from 37 to 44 months and the test failure rate dropped. So, for an average PSV maintenance cost of £1000, total cost has now reduced by £ 1.1m from £6.5m to £5.4m per year.
The second presentation was by Dr Madhu Parlapalli, who presented a paper on risk based inspection (RBI) of FPSO Cargo Tanks. Risk based inspection in the oil and gas industry of piping, pressure vessels and other critical equipment has been used more recently for planning structural inspections. For floating structures like FPSOs where there are additional requirements to satisfy in the form of Classification Society rules, although risk based approaches are allowed under these rules there are relatively few examples of where this has been applied to plan structural inspections on FPSOs, for items such as cargo or ballast tanks.
It is operationally quite inconvenient to carry out inspections of these tanks on a fixed 5-year interval in line with a standard Class schedule. A risk based inspection schedule has to take account of all relevant degradation mechanisms and the corresponding means of inspection. For FPSO cargo tanks the main degradation threats are fatigue cracking and corrosion / coating degradation and of course general inaccessibility for inspection. The RBI process involves developing a structural hierarchy of ‘accessible’ elements, identifying the relevant ‘failure modes’ and damage mechanisms then evaluating the ‘probability’ ranking for the relevant mechanism. The ‘consequence’ ranking for safety, environment or business impact is then added, and the risk level is evaluated using an agreed risk matrix with the client/owner. An inspection plan can then be developed for different inspection activities to form an optimised inspection schedule. Case studies were presented for ‘hotspots’ identified on an FSPO and RBI analysis used to look at the fatigue degradation mechanism and a coating degradation mechanism. An extensive Q&A followed these 2 excellent papers.
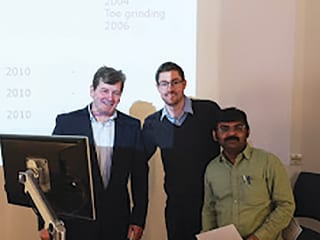
Branch chair, Stephen Tate with Dr Chris Bell and Dr Mahdu Parlapalli of DNV-GL.
Full details of future branch events can be found on the diary page of this magazine and on the website, or by contacting: ICorrABZ@gmail.com. Copies of the majority of past branch presentations can be found at: https://sites.google.com/site/icorrabz/resource-center, and a photo gallery for all Aberdeen events can be found at: https://sites.google.com/site/icorrabz/event-gallery
A special reminder is drawn to the August 2020 Annual Corrosion Forum (ACF), which unfortunately has now been cancelled owing to the Covid.19 outbreak and knock-on financial effects.
Aberdeen Branch, Latest News, London Branch, Midlands Branch, North East Branch, North West Branch
The Institute of Corrosion continues to follow the official UK government guidelines on how to mitigate the spread of coronavirus (COVID-19).
Our major priority is the safety and welfare of our members, officers and staff. Our main office at Corrosion House is open, with appropriate social distancing and safety measures in place for our staff and visitors.
Our training course providers will provide regular updates via their websites.
We appreciate the patience and support of our members in these challenging circumstances.
Aberdeen Branch, Latest News
Aberdeen Branch
The branch held its 4th event of the 2019/2020 session at its usual venue, RGU, with a presentation on “The Application of bismuth based alloys to address Oilfield challenges” by, Paul Carragher (BiSN), Lance Underwood (BiSN) and Angus MacLeod (BP).
This was a highly successful joint presentation with IOM3 – The Institute of Materials, Metals and Mining, which has recently celebrated its 150 year anniversary. The BiSN speakers discussed in detail their Wel-Lok sealing technology which utilises a unique combination of a thermite powered chemical heater and a bismuth based alloy to deliver an efficient down hole sealing capability, using standard oilfield deployment methods.
The thermite heater provides the energy to melt the bismuth alloy in situ, allowing the heavy liquid alloy to flow by gravity to the desired location. As the bismuth alloy cools, it expands on solidification to provide a seal. Paul Carragher started BiSN in 2010 with the insight to develop new and innovative sealing solutions for the oil & gas industry, and explained the use of bismuth in downhole sealing applications
Lance Underwood, Principal Engineer at BiSN Oil Tools, who has has over 30 years of experience in the industry, then provided further insights into the development of new technologies for plugs for oil wells, covering materials selection, downhole corrosion control and long-term corrosion testing programmes. He illustrated some of the rigorous testing requirements for downhole oilfield tools including bits, mud-motors, turbo-drills, under-reamers, hammers, and laser drilling.
Angus MacLeod (Senior Intervention Engineer with BP), with 22 years Oil and Gas industry experience, then followed this up with some actual case histories from BP operations worldwide, where this technology has been applied offshore, to shut off water production in open-hole gravel pack completions, as well as the work being done to qualify the alloys, as a permanent well abandonment material. In his current role, Angus is responsible for developing new well technology as part of BP’s Upstream Technology Group, primarily focussed on “Life of Well Surveillance” and “Plug & Abandonment”. The event generated a huge level of interest and many questions were asked, which can be found, together with the answers, on the branch website.
At the close of the meeting, the branch chairman, presented all speakers with a Certificate of Appreciation from the branch.
Full details of future branch events can be found on the diary page of this magazine and on the website, or by contacting: ICorrABZ@gmail.com.
Copies of the majority of past branch presentations can be found at: https://sites.google.com/site/icorrabz/resource-center and a photo gallery for these events is at, https://sites.google.com/site/icorrabz/event-gallery
Particular attention is drawn to the 2020 Corrosion Awareness Day to be held on Tuesday 25th August at, Petrofac Training Centre, Forties Road, Montrose, Angus, DD10 9ET. The day will include several practical demonstrations with teaching, this year themed on fabrication and external corrosion management. Further Details about this can be obtained from the branch Chair: Stephen Tate, email: Stephen.Tate@external.total.com
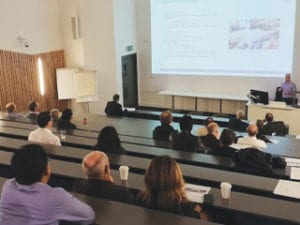
Angus MacLeod highlighted the many practical applications for this new Downhole Sealing Technology.
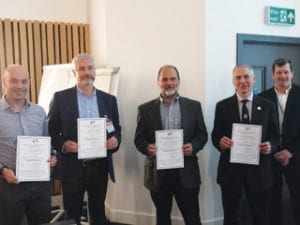
The Aberdeen Chair Stephen Tate, presented all speakers with Certificates of Appreciation.
Aberdeen Branch, Latest News
The 3rd Technical Meeting of the 2019/2020 Aberdeen Branch Session, was held on 29 October. This was a double header event with Dr Gareth Hinds, the current ICorr President speaking about “Growing the Institute Membership, and the ICorr Awards”, and later on, Matt Streets of RAWWATER: presenting “An understanding of Reservoir Souring and Mitigation”.
Dr Gareth Hinds started his presentation by posing the question: How can the Institute of Corrosion adapt to thrive in a rapidly changing world? He reminisced that he had first attended an Aberdeen Branch meeting 13 years ago and complimented the branch for being one of the strongest and most active of the regional branches. He went on to say that since then he has learned a lot about what its members can give to the Institute and what they can expect to get from it in return.
He described the history of the Institute and the benefits of Membership, and stated his belief that the more one puts in, the more one will get out of being a member.
Gareth reminded the audience of the history from when ICorr started as the British Association of Corrosion Engineers in 1959 and the many name changes and location changes that it went through up to present day, when the Institute recently purchased its own headquarters building in Northampton.
The President went on to explain the different types of ICorr Membership touching on the plans to change individual membership to “Affiliate” and other planned changes. He also touched on the challenge to get student members to stay, and by empowering younger members, for example to take part in the young engineers programme which has as a prize a free trip to the NACE conference in the USA, and free ICorr and NACE memberships.
Gareth continued by highlighting key Membership benefits which he stated were networking, career development, visibility and financial rewards. He also gave the audience an update on the situation with the Engineering Council caused by the sudden failure of the Society of Environmental Engineers (SEE) in that the Institute hopes to combine with the Society of Operational Engineers (SOE) to continue to award Chartership (CEng) status through the Engineering Council.
It is expected that a new agreement will proceed next year with SOE and ICorr head office will be in touch with all ICorr chartered engineers affected to confirm this.
He described the brand refresh which will be taking place at the start of next year 2020 when the ICorr website and all paperwork etc. will be revised to make the image of the Institute more modern. Pictures of rust and corrosion will largely be replaced by pictures of gleaming new infrastructure (of natural metallic colours / alloys) and similar modern metallic hardware. Gareth told how the Institute had undergone digital modernisation and members can now pay their subscription online on the website.
The visiting President said that the Institute of Corrosion was once again looking to influence governing bodies as they had in the 70s, when they had been very influential in getting CAPCIS in Manchester and the National Physical laboratory setup.
Gareth’s most comprehensive presentation was both enlightening and uplifting, showing his clear vision for the future of the Institute of Corrosion under his leadership.
In the second (technical) presentation of the evening Matt Streets of RAWWATER discussed to the large audience how, as all oilfield reservoirs have different souring propensities, operators must view all injector/producer (I/P) pairs as unique in regard to H2S gas production, as well as control and mitigation strategies.
The following and very detailed RAWWATER presentation by Matt Streets described how a predictive oilfield souring model can be used to help forecast if, when, and to what extent, an oilfield will sour.
He explained how the model describes the cooling of an oilfield due to water-flooding and the subsequent growth of sulphate-reducing microorganisms, resulting in sulphide production at the topsides facilities.
Outputs from the model can be used to inform and influence key operational decisions and have provided huge cost savings for operators through cost-effective material selection and chemical dosing.
Matt’s presentation included a detailed review of the science that was used to produce the model and how the output from it can be used by Oil and Gas operators to plan to minimising costly problems caused by reservoir souring and thereby maximise their operating profits
At the end of his presentation Matt answered questions from the Audience on topics such as where the model input data came from, how critical seawater breakthrough was to the modelling, how many core samples were required to confirm that they had not been contaminated, the viability of injecting alternative food stock to the reservoir and about re-educating Oil and Gas operational personnel after several recent ownership changes.
At the close of the meeting, the Aberdeen branch chairman, presented both of the speakers with a Certificate of Appreciation from ICorr Aberdeen Branch.
UK ICorr President Dr Gareth Hinds and Matt Streets (of RAWWATER) receive their Certificates of Appreciation
Activities continued afterwards at the Norwood Hall Hotel nearby, with further fruitful discussions on Aberdeen Branch Development, improved HQ integration and many other issues.
The Branch is very grateful to Gareth for making the long journey north and for his great enthusiasm and interest in our Branch Activities.
Full details of all future branch events can be found on the diary page of Corrosion Management Magazine and on the ICorr Website.
Copies of the majority of past branch presentations
Branch photo gallery for these events
Discussions with the New President continued late into the Night at Norwood Hall nearby. Seated Left to Right are: (New Committee Member), Dr Olubayo Latinwo, Hooman Takhtechian, (Internal Secretary), (Event Co-ordinator), Stephen Tate, (2019-2020 Session Chair), UK ICorr President Dr Gareth Hinds, Alistair Seton, (Past Chair / New External Secretary), Zahra Lotfi, (University Liaison and CPD Officer), Mei Ling Cheah, (New Committee Member), Dr. Yunnan Gao, (Immediate Past Chair / New Website Officer).