Ask the Expert
The Significance of PREN for the Corrosion
Resistance of Stainless Steel by Sarah Bagnall
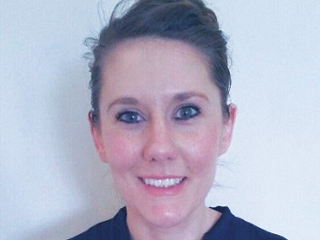
Sarah Bagnall, Director Consultancy Services at R-TECH Materials, CEng. MSc, BSc
Sarah is a materials engineer specialising in failure analysis, for the petrochemical, process, and power generation industries. Currently, she is Director of Consultancy Services at R-TECH Materials. With over 600 failure investigations conducted to date, Sarah has broad experience with a wide range of engineering components, metallic and non-metallic materials, and industries. Sarah has extensive expertise in the corrosion of a wide range of materials, particularly for the chemical processing and petrochemical industries.
- What is the Significance of PREN for the Corrosion Resistance of Stainless Steel?
Calculating PREN and How to Apply it
Stainless steels are well known for their superior corrosion resistance, which is primarily a consequence of the significant chromium addition. When exposed to oxygen, stainless steel forms a passive film due to its 10.5% (or more) chromium content. This film protects the material from rusting and even has self-healing properties. Other elements can be added to further improve the corrosion performance, such as Nickel, Molybdenum, and Nitrogen.
Not all stainless steels are created equal. Different grades exist, and their corrosion resistance can vary significantly. The corrosion resistance between grades can be compared by using the Pitting Resistance Equivalent Number (PREN). The calculation used for PREN is as follows:
PREN = Cr% + 3.3 x (Mo% + 0.5 x W%) + 16 x N%
Examples of stainless steel grades and the calculated PREN numbers are given in Table 1 and Figure 1 below.
Performance in Service
While the PREN is useful for ranking and comparing the different grades for relative resistance to corrosion, it cannot be used to predict whether a particular grade will be suitable for a specific application, where pitting corrosion may be a hazard. All environmental and operating conditions must be taken into consideration.In some industries, notably the oil and gas sector, specifications may place tighter restrictions on the PREN for specific grades than that implied by the minimum composition of the grade defined in EN or ASTM Standards.
In practice, the vast majority of stainless steels deployed across industry are of the 300 series type with lower PREN values, where external pitting is actually quite common in service at ambient temperatures.
Corrosion resistance is not only affected by the chemical composition of the material but also by the heat treatment condition. If the material is heat treated incorrectly during manufacture or welding, microstructural changes can occur which effectively means that
the material is no longer a stainless steel in a localised area. Exposure to temperatures in the range 370-815oC allows the precipitation of chromium rich carbides/nitrides along the grain boundaries. These precipitates are rich in chromium and deplete the area directly adjacent to the boundary of chromium, thereby increasing the likelihood of localised corrosion in the form of intergranular attack, pitting or stress corrosion cracking in a corrosive environment.
Further Guidance
The British Stainless Steel Association (BSSA) exists to promote and develop the manufacture and use of stainless steel across the UK and Ireland. Based in Sheffield, the Association provides technical advice, information, training, and education in all aspects of stainless-steel
usage. They may be contacted at: www.bssa.org.uk
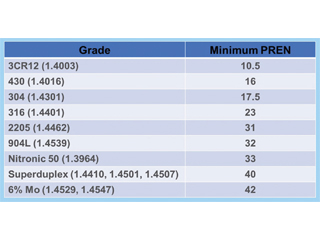
Table 1: Comparison of Stainless-Steel Grades Based on the PREN.
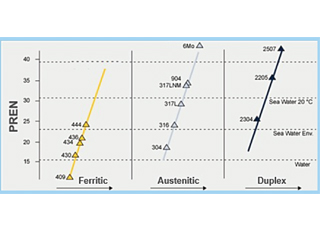
Figure 1. Comparison of Stainless-Steel Grades Based on the PREN
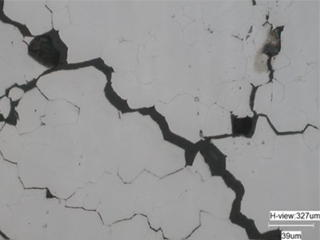
Figure 2. Cracking of a Sensitised Stainless Steel Bolt Which Had Been Heat Treated Incorrectly During Manufacture.
Ask the Expert
Why Do Bronze Medals Tarnish So Quickly?
By Roger Francis, RF Materials
Meet the Author
Dr. Roger Francis
Dr Francis has been a corrosion engineer for over 45 years. He has wide experience in the fields of marine corrosion, desalination, sour oil and gas corrosion, mineral processing, and the chemical and process industries. He has published over 100 technical papers in all these areas, particularly on copper alloys and duplex stainless steels. Roger has written seven books on various aspects of corrosion and has jointly edited three other books. The most recent was on corrosion in desalination plants. Dr. Francis has served on several standards committees working on corrosion testing of both copper alloys and stainless steels. In particular he was involved with the committee turning NACE MR0175 into ISO 15156.The author has served as chair of NACE Europe, two terms as the NACE (now AMPP) European Area Director and also as Chair of NACE STG 32 (Oil and Gas; metals). He was made a NACE Fellow in 2005 for his work in marine corrosion. In 2014 he received the T J Hull Award for his work in publications. In 2012 he set up his own corrosion consultancy business, RF Materials. In 2023, he received the Institute of Corrosion Paul McIntyre award presented to a senior corrosion engineer who, as well as being a leading practitioner in his field, has advanced European collaboration and international standards development.
Bronze has been used for a variety of medals for over two hundred years and given sufficient time without cleaning, they will all tarnish. Figure 1 shows an old coin with different degrees of tarnish on the two sides. Figure 2 is a bronze medal that also shows tarnishing.
There is a wide range of bronze alloys, where the chief alloying element is tin, aluminium, or silicon. The majority of bronze medals used to be made of LG2 gunmetal (Cu/5Sn/5Zn/5Pb) or something very similar. Tin bronzes are reddish, but not as strongly red as pure copper. Other elements may be added to modify the colour, for example, to make it more yellow. However, to cut costs, many modern “bronze” medals are actually brass (Cu/5Zn), which has a similar appearance to tin bronze but is not as corrosion resistant.
When a “bronze” medal is polished and shiny, the metal surface is very active and reacts readily in the air to form a very thin layer of cuprous oxide. This slightly dulls the appearance, but continued exposure to air will enable corrosion to continue, and a thicker layer of reddish brown cuprous oxide gradually forms. Although both alloys form cuprous oxide as the main corrosion product, the zinc or tin substitutes at some of the copper sites in the oxide matrix. Zinc makes the oxide layer less protective, while tin makes it more protective1. If the tin content is high enough, a separate layer of stannous oxide can form, but this is unlikely at 5% tin1. If a medal is exposed to an aggressive atmosphere for long enough, then a second corrosion product can form on top of the oxide layer, as shown in Figure 3. This is a basic copper carbonate, and it is less protective than the cuprous oxide layer.
Bronze has been used for a variety of medals for over two hundred years and given sufficient time without cleaning, they will all tarnish. Figure 1 shows an old coin with different degrees of tarnish on the two sides. Figure 2 is a bronze medal that also shows tarnishing.
There is a wide range of bronze alloys, where the chief alloying element is tin, aluminium, or silicon. The majority of bronze medals used to be made of LG2 gunmetal (Cu/5Sn/5Zn/5Pb) or something very similar. Tin bronzes are reddish, but not as strongly red as pure copper. Other elements may be added to modify the colour, for example, to make it more yellow. However, to cut costs, many modern “bronze” medals are actually brass (Cu/5Zn), which has a similar appearance to tin bronze but is not as corrosion resistant.
When a “bronze” medal is polished and shiny, the metal surface is very active and reacts readily in the air to form a very thin layer of cuprous oxide. This slightly dulls the appearance, but continued exposure to air will enable corrosion to continue, and a thicker layer of reddish brown cuprous oxide gradually forms. Although both alloys form cuprous oxide as the main corrosion product, the zinc or tin substitutes at some of the copper sites in the oxide matrix. Zinc makes the oxide layer less protective, while tin makes it more protective1. If the tin content is high enough, a separate layer of stannous oxide can form, but this is unlikely at 5% tin1. If a medal is exposed to an aggressive atmosphere for long enough, then a second corrosion product can form on top of the oxide layer, as shown in Figure 3. This is a basic copper carbonate, and it is less protective than the cuprous oxide layer.
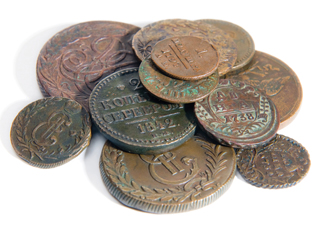
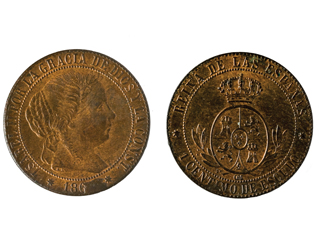
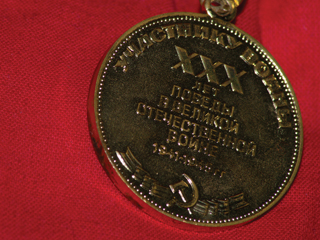
Figure 1: 19th Century Coin Showing Different Degrees of Tarnish on the Two Sides.
Figure 2: Tarnished Medal.
Figure 3:
Old Russian Coins from The Early 19th Century Showing Green Carbonate Corrosion Product.
Ask the Expert
Preventing Chloride Stress Corrosion Cracking (CSCC) and Degradation in Austenitic Stainless Steels
Dr Shagufta Khan, Ph.D., FICorr
- How can we prevent chloride stress corrosion cracking
(CSCC) in austenitic stainless steels?
Chloride stress corrosion cracking (CSCC) is one of the most common reasons why austenitic stainless-steel pipework and vessels fail under service in the chemical processing and petrochemical industries however these lower stainless grades can be subject to a wide range of deterioration modes as detailed below.
Stainless steels (SS) must contain a minimum of 11 Wt % chromium, and this level of chromium allows formation of a passive surface oxide that prevents surface corrosion in an unpolluted atmosphere. Increasing Cr content to 17 to 20 %, as typical of the austenitic SS, or to 26 to 29 % as possible in newer ferritic SS, greatly increases the stability of the passive film. Examples of common grade modifications for different applications are given below in Table 1.
AISI Euronor11z DIN British
Description
Standard
304 1.4301 X5CrNil 8-10 304S31
The general-purpose grade, widely used where good formability and corrosion resistance are required.
304L 1.4306 X2CrNi l 9-11 304Sl 1
As 304 but with lower
carbon content to Minimize carbide precipitation during welding.
301 and 1.4310 Xl 2CrNi l 8-10 301S21
Higher strength versions of 304 that are often cold worked to give higher strength.
303 1.4305 XlOCrNiS18-9 303S31
General purpose grades with sulphur or Selenium added
to improve machinability.
321 1.4541 XlOCrNiS18-9 321Sl2
321S31
As 304 with an addition of titanium to prevent carbide precipitation during welding.
347 1.4450 X6CrNiNbl8 -10 347S3l
As 304 with addition of niobium and or tantalum to prevent carbide precipitation during welding.
316 1.4401 X5CrNiMol7-12-2 316S31
As 304 but with molybdenum
added to increase resistance to localised corrosion in marine and chemical environments.
316L 1.4404 X2CrNiMol7-13-2 316Sl 1
As 316 but with lower carbon content to minimise carbide precipitation during welding.
Austenitic SS can have an excellent combination of mechanical strength, corrosion resistance, ease of fabrication, and cost effectiveness. The most widely used stainless steel grades are austenitic, with 74% production of total world SS production. Various grades of austenitic steels have excellent corrosion resistance in many environments, resisting attack by the atmosphere and by many industrial gases and chemicals.
The pitting and crevice corrosion resistance of stainless steel is primarily determined by the content of chromium, molybdenum and nitrogen. Manufacturing and fabrication practices, e.g. welding, are also of vital importance for the actual performance in service. A parameter for comparing the resistance to pitting in chloride environments is the
PRE number (Pitting Resistance Equivalent).
The PRE is defined as, in weight-%
PRE = %Cr + 3.3 x %Mo + 16 x %N
Many of these stainless steels have good strength at high temperatures which accounts for their wide use at elevated temperatures. They are also among the primary materials selected for use at extremely low temperatures, since they do not become brittle compared to other types of steel. AISI 304 and 304L are the most popular grade of austenitic SS. Although austenitic SS are used as corrosion resistance alloys for many applications, there are many cases of failure in aggressive environments. Some of the corrosion failure types that stainless steel remains susceptible to include:
-
Crevice corrosion (common, often seen at piping flanges and under identification labels).
-
Galvanic/bimetallic corrosion (common, must have compatible fixings/fasteners).
-
Pitting corrosion (very common especially under labels, can occur in storage or at fabrication site prior to service).
-
Stress corrosion cracking (common at more elevated temperatures and where there are residual stresses).
-
Weld decay (less common, varies with process chemistry and applied chemical treatments).
SCC
Stress corrosion cracking is a time-dependent phenomenon that occurs in a metal when certain metallurgical, mechanical, and environmental, conditions are present at the same time. SCC is a somewhat sneaky type of degradation because it occurs at stress levels within the design stress range. The cracking can be:
- Intergranular (IG): passing through the grain boundaries.
- Trans granular (TG): passing through the grain matrix.
- A mixed mode (TG and IG) of SCC,
Depending on the microstructure of the material exposed to the atmosphere and the nature of the environment. SCC is caused by weak tensile stresses, typically below the macroscopic yield stress. Figure 3 describes the necessary conditions for SCC to occur. Austenitic stainless steels may undergo SCC in hot, concentrated chloride solutions, chloride-contaminated steam, and in HTHP (high temperature and high pressure) demineralised water in presence of oxygen.
Among all types of environmentally assisted cracking of austenitic stainless steel, CSCC is perhaps the most common. Many
incidences of failure have been reported due to CSCC, e.g.
condenser tubes in heat exchangers, swimming pool components,
parts used in marine applications, under insulation of external piping
in a refinery, and medical devices. Chloride stress corrosion
cracking of patch repaired elbow in hydrocarbon service is shown
in Figure 4.
API 571 defines chloride stress corrosion cracking as follows: “Surface initiated cracking of 300 series SS and some nickel-based alloys under the combined action of tensile stress, temperature, and an aqueous chloride environment. It is also referred to as chloride cracking”. All 300 series SS are highly susceptible to pitting and CSCC where additional stresses exist. Welds in 300 series SS normally contain some ferrite, producing a duplex structure that is usually more resistant to CSCC than the base
metal though.
Factors Affecting CSCC: Several environmental factors, like chloride concentration, temperature, pH, dissolved oxygen can have profound effect on CSCC. Nickel content of alloy and applied or residual tensile stresses can also affect CSCC.
Chloride Concentration: CSCC is caused by inorganic chloride ions. It is known that organic chlorides do not directly cause CSCC. In industrial processes, hydrolysis or thermal decomposition of organic chlorides may produce ionic, inorganic chlorides. Therefore, organic chlorides can also cause CSCC. The components experiencing higher tensile stresses require lower Cl- concentration for initiation of SCC. There is no lower limit of Cl- concentration for crack initiation. A few ppm Cl- in the process stream can concentrate to hundreds of ppm where evaporation takes place. Cl- can further concentrate at the base of pits when pitting corrosion starts. Increasing levels of chloride will increase the likelihood of cracking and greater than 50g/L of chloride in process fluids would certainly give cause for concern for 300 series SS.
Temperature: Increasing temperatures increase the cracking probability if tensile stress and an aqueous chloride solution and/or external chloride build-up are present. Although exceptional cases have been reported. Highly cold worked or sensitised materials may undergo cracking at lower temperature or even at ambient temperature. Usually cracking occurs at metal temperatures above about 50 °C and this temperature limit is considered the guideline for fixed equipment in the refining industry.
Tensile Stresses: Tensile stress may be applied or residual. Crack initiation and propagation are guided by the aggregate of both external (i.e. applied) and internal residual stresses. Residual stress by definition is the tensile, or compressive force, that exists in the bulk of a material without application of an external load. The bending of steel plates during pipe construction, localised plastic deformation during handling, and differential cooling through the wall thickness and along the surface during rolling, are all potential sources of residual stresses in pipeline steels. Regions with different microstructures and chemical segregation at the grain boundary may also generate residual stresses in metallic components. In the absence of proper control measures, residual stresses produced during the fabrication phase can significantly contribute to SCC. Non-stress-relieved welds, highly stressed, or cold worked components, such as expansion bellows, are highly susceptible to cracking.
pH of Environment: Cracking is more likely to occur at lower pH. However, SCC usually does not occur at pH values below 2. Uniform corrosion generally predominates at such highly acidic range. CSCC tendency decreases toward the alkaline pH region.
Dissolved Oxygen: It is observed that oxygen dissolved in the water increases tendency to SCC. Other oxidisers in addition to oxygen (e.g., CO and CO2) can also enhance CSCC. It is unclear what oxygen concentration must be reached before CSCC starts.
Nickel Content: Alloys tendency to SCC is affected by nickel content in a profound way. Stainless steels with a nickel content of 8 % to 12 % have greatest susceptibility toward SCC. Alloys with nickel contents above 35 % are highly resistant, and alloys above 45 % show near immunity in refining applications, but severe conditions may lead to cracking in these alloys.
Prevention of CSCC: Prevention of CSCC by applied coatings is common in the energy sector although can be more difficult to achieve with smaller diameter piping. Reduction of tensile stress can be used to avoid CSCC. This can be achieved by applying compressive stress by shot peening. A suitable high-temperature stress relief heat treatment of 300 series SS after fabrication will reduce residual stresses. Care should be taken that stress relief heat treatment should not result in sensitisation.
Changing process conditions is the best approach for minimizing CSCC. The acidity and corrosiveness of the process fluids can be controlled by addition of chemicals such as acid neutralizer and corrosion inhibitors. Effectiveness of corrosion inhibitors must be assured before use through laboratory test. Upgrading the metallurgy may also be opted to avoid SCC. A duplex SS might be considered for this purpose. Duplex SS has almost equal ratio of austenitic and ferritic grains in its microstructure. Duplex SS have very good corrosion resistance and they can withstand higher tensile stresses. Their resistance to pitting corrosion is also very good. Super austenitic SS have higher content of Ni so they show good resistance to cracking in chloride environments.
Low chloride-content water should be used during hydrotesting, followed quickly by thorough dry out. Designs that create stagnant regions should be avoided as chlorides can concentrate in such region. An effective external coating (e.g. epoxy phenolic coatings up to 120 oC and TSA above this temperature limit) should be applied to SS piping and equipment prior to insulating or adding piping identification. Shrink-wrapped PVC labels, coatings, or label adhesives with high levels of chlorides or other halogen ions should be avoided.
References
- J. F. Grubb, T. DeBold, J. D. Fritz, Corrosion of Wrought Stainless Steels, in: S. D. Cramer, B. S. Covino (Eds), Corrosion: Materials, Vol 13B, ASM Handbook (tenth edition), ASM International, Ohio, 2005, p. 54-77.
- A. J. Sedriks, Corrosion of stainless steels, second ed., John Wiley and Sons, New York, NY, 1996.
- ANSI/API Recommended Practice 571 Third Edition, March 2020, Damage mechanisms affecting fixed equipment in the refining industry.
- M. Hussain, T Zhang, S Khan, N Hassan, Stress corrosion cracking is a threat to pipeline integrity management, Corrosion and prevention 2020, Perth Australia organised by Australian corrosion association.
- S. Khan, Doctoral thesis “Corrosion of austenitic stainless steels in nitric acid at trans passive potentials: effect of material and process parameters, 2016, Homi Bhabha National Institute, India.
- Chidambaram Subramanian, chloride induced stress corrosion cracking of repaired pipe elbow from an oil refinery: forensic analysis.
CAPTIONS:
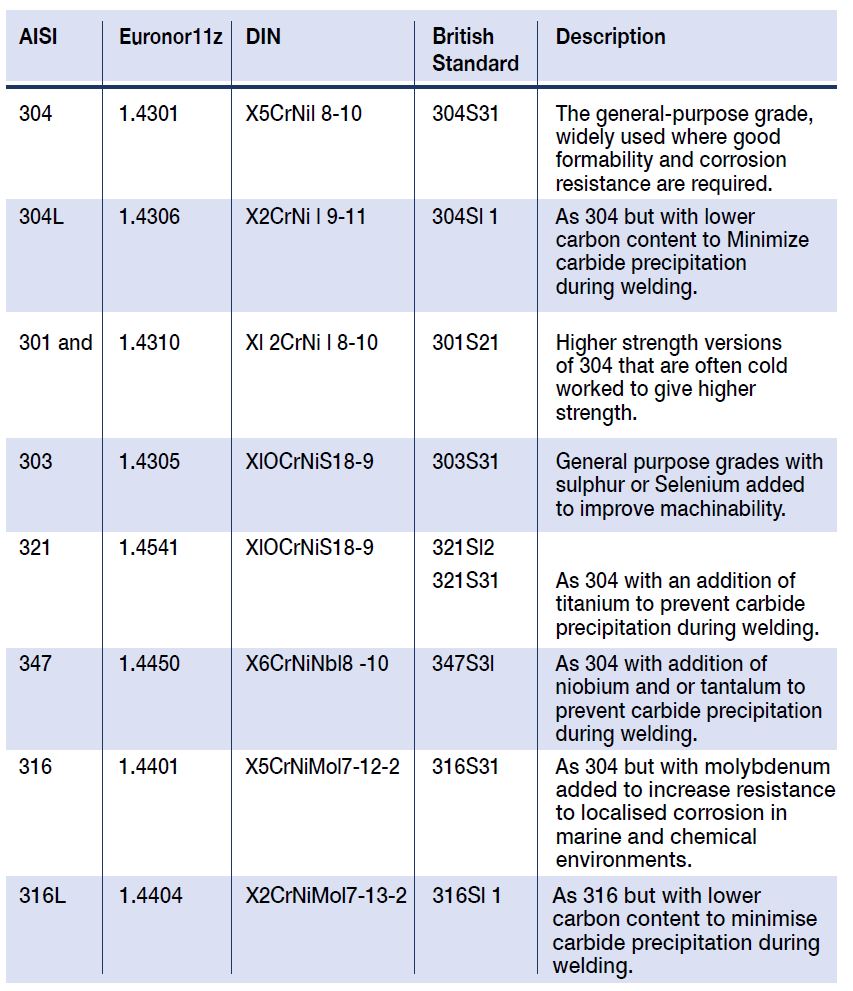
Table 1: Widely Used Grades of Austenitic Stainless Steel
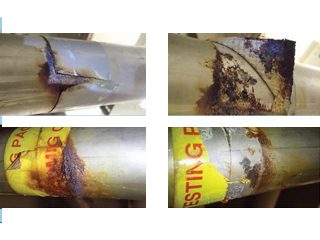
Above: Figure 1: Commonly Observed 316L Grade Stainless Pitting Under Labels.
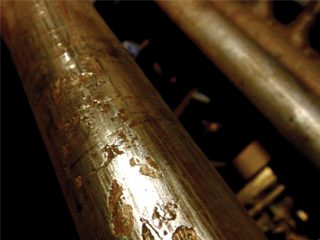
Left: Figure 2: Photo of Corrosion Under Labels (CUL) Seen After Label Removal.
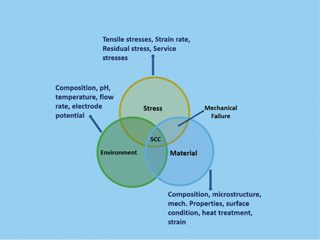
Figure 3: The Necessary Conditions for SCC to Occur in Austenitic Stainless Steel.
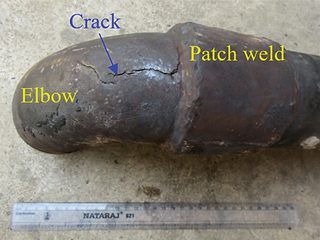
Figure 4: Photo of Patch Repaired Piping Elbow from Hydro Cracking Plant (Corrosion Management, Issue 174).
Ask the Expert
What Stops the Reinforcing Steel in Damp, Porous Concrete from Corroding (Usually)?
John Broomfield, Corrosion Engineering Solutions Ltd.
Meet the Author
John Broomfield
John Broomfield is a Fellow of ICorr, AMPP, and the Concrete Society. He is a Chartered Materials Engineer and Chartered Scientist. He is also a Level IV Senior Cathodic Protection Engineer and an AMPP/NACE International Corrosion Specialist. He has over 40 years of experience in dealing with deterioration and durability problems in the built infrastructure, specialising in reinforced concrete, corrosion of steel-framed structures, and conservation of historic buildings and monuments. He has worked on projects all over the
world and undertaken condition surveys, repair feasibility studies, life cycle
cost analysis, corrosion risk analysis, repair specification, and repair design.
He specialises in the application of electrochemical techniques for the investigation, rehabilitation, and design of durable new construction.
Concrete
Concrete has been used for millennia in various forms, principally as unreinforced mass concrete. The Romans used a form based on volcanic ash extensively, one of the finest remaining examples being the Pantheon in Rome.
The development of Portland cement by Joseph Aspdin in the early 1800s using simple, widely available materials and then the development of reinforced concrete by François Hennebique in the late 1800s led to the development and use of reinforced concrete for buildings, bridges, and other major structures. There had been attempts to use other metals to reinforce concrete, but iron and steel turned out to be the most compatible due to the similarity of their thermal expansion coefficients [1].
Concrete is a composite of cement powder and water mixed with coarse and fine aggregates. It is the cement that binds the aggregates together as it hydrates. The most common binder is Portland cement, made from limestone and clay roasted and ground in a kiln. It is a complex mixture of calcium compounds such as silicates, aluminates, and iron oxides that, when combined with water, form a calcium silicate hydrate gel that binds the concrete mix together. The hydration process, when completed, leaves a level of porosity in the hardened concrete of the order of 10%. These pores contain calcium hydroxide both in solution and as a precipitate, along with some sodium and potassium oxides/hydroxides.
While strong in compression, concrete is weak in tension, requiring reinforcement in many applications. Steel exposed to water and oxygen will oxidise unless effectively starved of oxygen or completely dried out. Absence of water in concrete can occur in indoor environments or behind external cladding. Absence of oxygen can occur in submerged concrete. For normal outdoor exposure, the steel would be subject to corrosion at a rate that would be harmful over the lifetime of a structure due to the ingress of water and oxygen through the pore system unless otherwise protected.
Corrosion Resistance of Reinforcement
Fortunately, the excess calcium hydroxide in the concrete pores, combined with some sodium and potassium hydroxides, elevates the alkalinity at the steel surface to around pH 12.5 to pH13. At this point in the Pourbaix diagram [2], iron is passivated, forming a thin, protective, self-sustaining oxide layer with a very low corrosion rate. As long as the concrete cover to the steel remains intact, sufficiently alkaline, and uncontaminated, the steel will remain in good condition despite the presence of oxygen and water at the concrete and steel surfaces, or perhaps we should say that the protection of the steel is because of
the presence of oxygen and water to maintain the protective passive oxide film. We therefore have reinforced concrete structures that
can last 100 years or more without showing any signs of
reinforcement corrosion.
A true passive layer is a very dense, thin layer of oxide that leads to a very slow rate of oxidation (corrosion). There is some discussion as to whether or not the layer on the steel is a true passive layer. It seems to be thick compared with other passive layers and it consists of more than just metal oxides but, as it behaves like a passive layer, it is generally referred to as such.
Corrosion scientists and engineers spend much of their time trying to find ways of stopping the corrosion of steel by applying protective coatings to steel. Metals such as zinc and polymers such as acrylics or epoxies are used to stop corrosive conditions from forming on steel surfaces. The passive layer is the corrosion engineer’s dream coating, as it forms itself and will maintain and repair itself as long as the passivating (alkaline) environment is maintained.
Factors that Accelerate Corrosion in Reinforcement
However, the passivating environment is not always maintained. For reinforced concrete in normal atmospheric exposure, two conditions can break down the passivating environment without attacking and destroying the concrete itself. One process is carbonation, and the other is chloride attack.
Carbonation occurs when the naturally occurring carbon dioxide (CO2) in the air reacts with the alkaline oxides/hydroxides in the concrete pore water. The dissolution of CO2 in water forms carbonic acid, a weak acid that does not attack the cement paste or the aggregates in the concrete but reduces the pore water pH below 10. At that point, the passive layer on the steel breaks down, and the steel is vulnerable to corrosion. Carbonation moves as a front through the concrete cover. The rate of progress of the carbonation front is approximated by a simple diffusion equation where the depth of carbonation x at time t after construction is given by:
x = kt1⁄2
Where k is a constant. The carbonation front is a transition in pH from about 12.5 to 8.5 and is a few millimetres wide. The depth of carbonation can be measured using an indicator solution, sprayed on to a freshly exposed profile through the cover concrete. An example is shown in Figure 1.
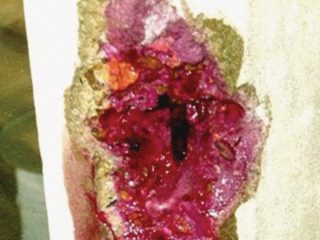
Right: Figure1: Phenolphthalein
Indicator Applied to Freshly Broken
Concrete to Measure the Carbonation
Depth on a Reinforced Concrete
Window Mullion.
The other condition leading to the de-passivation of steel is exposure to chloride ions (Cl-), generally from sea salt or de-icing salts. In this case, the chlorides diffuse into the concrete and build up in the concrete cover until there is sufficient concentration at the steel surface to break down the passive layer. There is no moving front, but there is a threshold for corrosion at the steel surface when the chloride ions successfully compete with the hydroxyl ions and break down the passive layer. The threshold is generally taken as being in the range of 0.2 to 0.4% chloride by mass of cement for low-alloy carbon steels in Portland cement- based concretes. It should be noted that for the newer “low carbon concretes,” the threshold has yet to be confirmed and may reduce with age [3].
Once the steel is de-passivated by carbonation or by chlorides, reinforcement in atmospherically exposed concrete will start to corrode. The most common corrosion process forms porous iron oxides with a volume several times that of the steel consumed. This leads to tensile forces which will crack and delaminate the concrete cover [4]. There are field techniques for measuring the carbonation depth in concrete and for sampling for chlorides. There are also non-destructive techniques for estimating the corrosion condition. Reference electrode potential measurements can identify areas of actively corroding steel and a polarisation resistance kit can estimate the corrosion rate [4,5].
Remedial Measures for Corrosion in Concrete
There are a range of techniques for preserving and restoring the passive layer on steel. These include the application of coatings, physical repair of the concrete, and a range of electrochemical techniques. Coatings are preferred for preventing the ingress of chlorides and CO2. BSEN 1504-2 [6] gives details on the selection and performance of anti-carbonation coatings and of penetrating sealers that resist chloride ingress. It has been found that anti- carbonation coatings are effective in controlling the corrosion rate in carbonated concrete by controlling moisture ingress as well as CO2 [7]. However, penetrating sealers applied to chloride contaminated concrete are less effective in slowing corrosion once the corrosion threshold chloride concentration has been exceeded at the steel surface.Electrochemical techniques such as re-alkalisation, chloride extraction, impressed current and galvanic cathodic protection are all effective in preventing corrosion of the steel, regardless of the extent of de-passivation if used appropriately [4].
Corrosion in Alternative Types of Concrete
It is important to recognise that the concrete cover to the steel must sustain the passive layer throughout the life of the structure if there is a corrosion risk. The performance of Portland cement concrete, and concretes with blended cements is well understood. However, there is now a new range of low-carbon cements being made available to the construction industry. In a recent article in CM [3], I expressed concern about the long-term corrosion protection afforded to low-alloy steel reinforcement by novel cement materials. Are there sufficient alkali reserves available over 50 to 100 year design lives to ensure the steel cannot corrode? Is anyone testing them? The recent problems with reinforced autoclaved aerated concrete (RAAC) are also interesting. RAAC is a very low-density concrete with minimal resistance to the ingress of water and CO2. It was designed for ease of handling and low cost. Much of the press-coverage around this issue is confused. RAAC has many problems and failure mechanisms and many are not corrosion related. These problems include poor placement of reinforcement, poor placement of units [bearing shelves], deterioration through wetting & drying cycles and negligible to zero cover to the reinforcement. However, RAAC was supposed to be used in a dry, indoor environment where the corrosion risk to the reinforcement is minimal. RAAC beams were often installed under flat roofing. Any leaks would expose the concrete to wetting and drying, which would allow rapid carbonation and rapid breakdown of the passive layer with subsequent reinforcement corrosion. Flat roofs have a limited life, and identifying leakage can be difficult, especially above false ceilings. The problems were foreseeable and were foreseen by many, but not necessarily always by those with the responsibility and budgets for keeping the buildings safe. Moreover, this is not just a corrosion issue or a failing of the material – if your roof is leaking, you have bigger problems than just how it might affect any RAAC that might be present.
Summary
We can therefore see that the alkaline reserves in the concrete pore water leads to the formation and maintenance of the protective passive layer on the reinforcing steel. This is crucial to the durability of steel-reinforced concrete exposed to normal atmospheric conditions. Those responsible for the maintenance of reinforced concrete structures need to understand how and why reinforcing steel is protected from corrosion. If corrosion occurs, the correct techniques must be used to assess the cause and extent of the problem and the correct treatment applied to control corrosion and maintain the asset for the required life.
References
-
Paul Lambert Reinforced Concrete: The History, Properties and Durability of Reinforced Concrete , Technical Note 1 Corrosion Prevention Association, Bordon Hants, 2018.
-
Pourbaix, M. (1974). “Applications of Electrochemistry in Corrosion Science and in Practice.” Corrosion Science Vol. 14: p. 25-82.
-
Broomfield, J.P The Corrosion Resistant Properties of Novel Cements, Concretes, and Reinforcement, Corrosion |Management July/Aug 2023 pp 22-23.
-
John Broomfield, Corrosion of steel in concrete, 3rd edition Publ. CRC Press, London, 2023.
-
Concrete Society Technical Report 60, Electrochemical Tests for Reinforced Concrete. Concrete Society, Camberley, 2004.
-
BS EN 1504-2 (2004) Products and Systems for the Protection and Repair of Concrete Structures – Definitions, Requirements, Quality Control and Evaluation of Conformity: Part 2: Surface Protection Systems for Concrete.
-
Seneviratne, A. M. G., Sergi, G. Page, C.L. (2000). “Performance characteristics of surface coatings applied to concrete for
control of reinforcement corrosion.” Construction and Building Materials 14: 55-59.
Ask the Expert
Question:
Why are coatings often supplemented with cathodic protection to protect against corrosion?
Answer:
Corrosion is one of the most critical failure mechanisms in structures, installations, components, and mechanical systems, in which materials go through decay or deterioration, which in turn compromises the integrity of these structures or systems. Deterioration is the cause of the formation of oxides, hydroxides, or sulphides, which are naturally more stable forms of any refined material. There are several reasons for corrosion to initiate and propagate, these include environmental and operational conditions, material properties, and electrochemical activation. Although several factors are involved in initiating and propagating corrosion, a key factor is the availability of an active metal surface, which incubates electrochemical changes leading to corrosion.
Therefore, the primary focus, as a cost effective, efficient, and reliable technique, is to convert the active metal surface areas into passive surface areas. This helps stop or decelerate corrosion, and can be done by providing a protective current, which in turn reduces the potential of a metal surface. This results in cathodic protection, hence stopping or significantly reducing electrochemical changes, in other words, any corrosive attack is halted. There are two conventional methods by which passivation of metal surfaces is achieved. These are commonly known as (i) sacrificial anode cathodic protection, and (ii) impressed current cathodic protection. The above methods have been widely used in several industrial applications, such as petrochemical, marine, and infrastructure. Another effective technique for mitigating corrosion is to use a coating. The coating acts as an anti-corrosive protective layer, a barrier, or a sacrificial layer over the metal. Coatings offer several benefits by protecting materials, enhancing surface characteristics, and avoiding or reducing the risks of failure. Corrosion, however, becomes more complex in terms of its failure mechanisms when structures and components are dynamically loaded as in marine structures. This will cause failures such as corrosion fatigue and stress corrosion cracking.
Or when static structures are exposed to more aggressive environments, corrosion and corrosion failures will significantly accelerate. The combination of both coatings and cathodic protection will enhance metal resistance against corrosion. Therefore, a combination of both is widely used. These preventative methods also assist at the design stage in reducing the required weight of material for required operating lifetime and can thus significantly reduce fabrication and later transport costs with net-zero type benefits.
A more complex corrosion mechanism will occur when components are dynamically loaded and are subject to relative motion. This adds more complexity to attempts at stopping or controlling corrosion, because other mechanical and physical factors are now combined and are contributing to a more complex form of deterioration. In such instances, the use or application of cathodic protection becomes complicated, challenging, and in some cases, it becomes almost impossible to meet specified CP criteria. Therefore, more robust methods of enhancing corrosion resistance through material development, advanced coatings and coating techniques, corrosion monitoring, and prognostic measures, have been developed over the past several years. It is more pragmatic to provide bespoke solutions for specific applications.
If the components are interacting, then surface wear will occur. In a scenario where corrosion is absent, the wear purely results from mechanical loading and surface deterioration. However, in the presence of corrosive species, corrosion will also occur. This leads to a wear-corrosion mechanism.
Recent Coating Developments
Researchers have been developing advanced coatings to withstand both corrosion and wear in challenging and harsh environmental and operational conditions subject to design life requirements. Recent developments in nanocoatings and nanocomposite coatings [5], have shown that more attractive coating solutions are available for applications in more complex mechanical and chemical conditions. These nanocomposite coatings are, for example, Ni/Al2O3, Ni/SiC, Ni/ZrO2, Ni/Graphene (GPL), and several others. Such coatings have been developed in order to be subjected to corrosion while incorporating the effects of key mechanical properties. These newly developed nanocomposite coatings have been tested according to ASTM B117,
salt spray testing [1].
Further study of the above nanocomposite coatings has been conducted within the wear context [2].
A comprehensive study of the above nanocoatings at atomic surface layers, incorporating corrosive fluids, and using a numerical approach, was conducted [3].
It is well known that the durability and reliability of complex interacting systems are very important from a cost viewpoint and within a wider sustainability context. These interacting systems are subject to corrosion failures and are therefore a major concern for industry professionals. It is important to fully diversify design parameters.
Remote Monitoring
Further work has been performed to predict corrosion in dynamically corrosive environments by considering physical and mechanical characteristics. Researchers have recently developed and patented a new corrosion sensor that could improve the safety and reliability of large structures such as bridges, aircraft, military vehicles, and gas pipelines. The device can detect defects and risks in major infrastructure at a much earlier stage than the methods that are currently used. As well as improving safety, it could reduce the need for time consuming repairs, which can come at a significant cost and inconvenience to industries and the public.
In summary, it evident that the primary objective of an industrial coating is to prevent corrosion, and to withstand a variety of hazardous chemicals. Choosing the right coating is just as important as choosing the coating itself, a wrongly specified coating can lead to a wide range of problems, from maintenance to premature failure. No coating is completely free of defects, even when freshly applied. Faults can occur during the production of the coating as well as during handling and improper application of the coating. A defect may also arise during the course of service. The most common causes of coating failures include inadequate surface preparation, a non-friendly environment, poor formulation, and an inefficient application technique. Coatings with high efficiency are more expensive. Thicker coatings, the use of sophisticated inspection methods, and fixing specific defects, all result in higher cost and critically weight. Sometimes it is advantageous to use another protection method to supplement coatings, which is why we use cathodic protection and especially in marine situations. There is an overall benefit when a good coating application is combined with cathodic protection [4].
Prof. Zulfiqar Khan, Bournemouth University NanoCorr, Energy & Modelling (NCEM) Research Group.
References
1. Nazir, M.H., Khan, Z.A., Saeed, A., Bakolas, V., Braun, W., Bajwa, R. and Rafique, S., 2017. Analyzing and modelling the corrosion behavior of Ni/Al2O3, Ni/SiC, Ni/ZrO2 and Ni/graphene nanocomposite coatings. Materials, 10 (11).
2. Nazir, M.H., Khan, Z.A., Saeed, A., Bakolas, V., Braun, W. and Bajwa, R., 2018. Experimental analysis and modelling for reciprocating wear behaviour of nanocomposite coatings. Wear, 416-417, 89-102.
3. Nazir, M.H., Khan, Z.A., Saeed, A., Siddaiah, A. and Menezes, P.L., 2018. Synergistic wear-corrosion analysis and modelling of nanocomposite coatings. Tribology International, 121, 30-44.
4. L.L. Sheir, R.A. Jarman, and G.T. Burstein; “Corrosion”, Volume 2: “Corrosion Control”, 3rd edition, Butterworth Heinemann, ISBN 0-7506-1077-8.
5. https://www.digitaljournal.com/pr/news/theexpresswire/nano-coating-market-by-2031
Continuity Straps across Flanges for providing Cathodic Protection.
Ask the Expert
The question in this issue looks at the role of an inspector.
Question:
What makes a good coating inspector? CM
Answer:
This is an interesting question and has numerous answers in my opinion. Having worked in industry for some 40 odd years, and been on all sides of the fence including sitting on it, I feel I am able to give the following judgements.
The first and foremost criterion to be met is that an inspector needs to be completely independent and must not have their judgement swayed by allegiances or obligations. Until the advent of the ISO 9001, inspectors were employed by clients to provide objective and impartial viewpoints from an unbiased stand point, providing accurate and valid reports on the performance of a contractor’s work. They were generally put on site to act as a ‘Jiminy Cricket’ to witness, observe, and report back, as to what was going on, this, if done well would ensure that the contractor would be less likely to cut corners and use improper practices.
Up until 1987, BS5750 had been the governing system in the UK for business management but the arrival of ISO 9001 saw this coming to an end and the introduction of self-certification for contractors, this effectively destroyed the impartial third party inspection in the UK with an overnight hammer blow. Inspection in an instant became the domain of the contractor and many unscrupulous contractors immediately saw this as a license to print money as the poacher became both poacher and gamekeeper overnight. This led to the demise of many of the highly reputable inspection companies over the next few years.
It wasn’t until several years later when the clients started to actually look at, and audit, the works being undertaken under the ISO 9001 banner did they start to realise that things were not all that they seemed. From this a drive started to push forwards to try to put in place mitigation to prevent this from happening again.
The other major stumbling block that has often prevailed is the attitude of individuals who see inspection as unnecessary and a cost best avoided, how often do we hear the fateful words ’how difficult is it to paint a bit of steel? My wife manages to paint the house so it can’t be difficult at all!’ WRONG! Our business is highly technical and calling it painting is a huge mistake, paint is cosmetic and decorative! What we are involved in is the application of high-performance protective coatings and so we need people with a high level of technical knowledge to administer, as well as a well-trained and understanding workforce.
A properly constructed specification and contract is now seen as the best way forward to ensure contractor inspection is fit for purpose and that the personnel are properly trained and certified via a recognised body as competent.
From this we need to look at what the inspector’s role should be today, and what makes a good inspector. Inspection needs to be stand alone, you cannot blast or coat a piece of steel then inspect it and certify it yourself, as unfortunately still so often happens.
Many coating inspectors have worked their way up through the ranks and prove to be highly suitable and capable to undertake the coal face inspections. With the aid of quality training and access to all the right equipment, these people provide a solid and reliable backbone to the industry. What they do need is a proper and competent system of support, both from more highly qualified and experienced inspectors controlling and monitoring them, and with a management team that appreciates the true ramifications and the importance of inspection.
A good basic inspector should therefore be someone who is truly enthusiastic about his role and understands that he must at all times be an observer and not try to run the job, his role is the duty to collect and collate information, and report back to line management with his findings, and not get involved in front line confrontation. That does not mean to say that he cannot be authorised to discuss what he finds with the foreman or other management on the project but telling a worker what to do by bypassing the chain of command generally
ends up badly.
A basic inspector is not a basic person, he needs to have a large amount of experience and understanding of how the jobs are undertaken and the limitations of what is trying to be achieved. A good technical grounding is essential as well as the ability to communicate clearly, concisely, and correctly. One of the absolute essentials is training by a recognised training body with certification stating that the inspector has been trained and assessed to a given level and what they are competent to undertake and what level of supervision they require. For example the ICorr Coating Inspector training courses delivered by IMechE Argyll Ruane.
The knowledge required as an inspector moves further up the hierarchy, and becomes more varied and more technical. Ideally when the levels of dealing with contracts, documentation, auditing and failure analysis are reached, very comprehensive inspection training is needed as well as other technical qualifications such as degrees in chemistry, organic chemistry, metallurgy and materials, or process engineering. This gives the necessary level of understanding and authority to state the case when decisions need to be made and if necessary enforced.
An inspector’s life is not a simple one, and having an open mind, unbiased view point, an inquisitive nature, a strong, unwavering sense of right and wrong, a good sound training background along with something resembling a sense of humour and the hide of a rhinoceros, all go a long way to making a good inspector.
Simon Hope
Auquharney Associated Ltd.