The cart is empty!
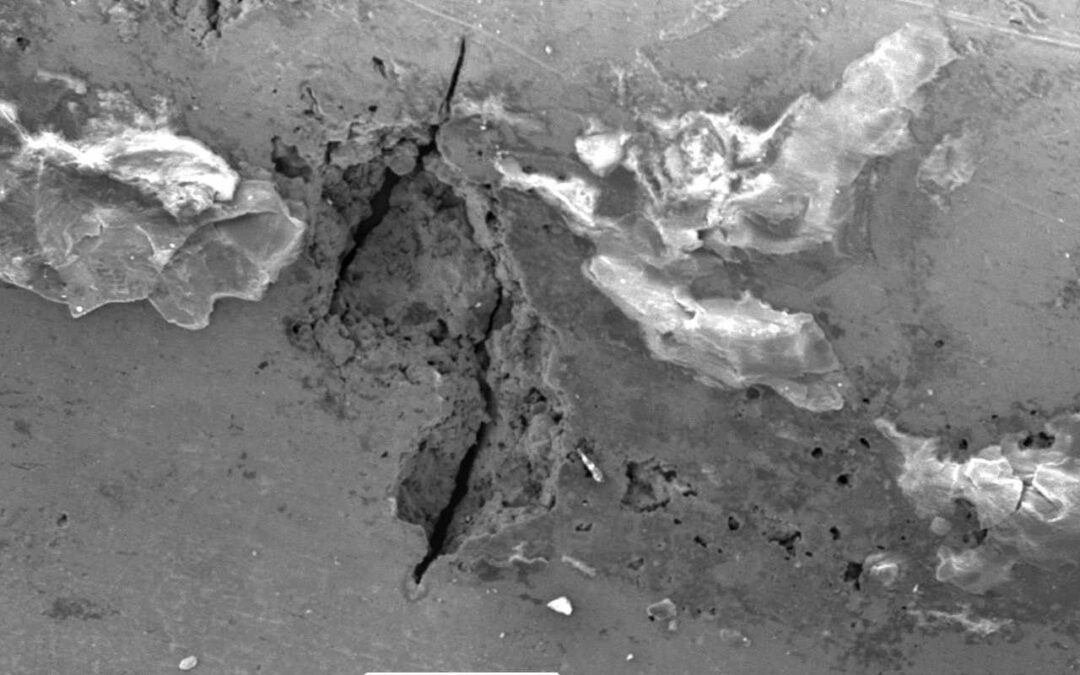
The Unique Challenges of Managing Microbiological Corrosion
5 Obstacles Corrosion Professionals Must Navigate in MIC Prevention
Microbiological corrosion (MIC) is a significant threat in many industries. The consequences of failing to effectively manage MIC range from reduced structural integrity to catastrophic failures, extensive damage, financial losses, and loss of life. (We discussed seven such failures in our recent article, ‘Real Life Impacts of Microbiologically-Influenced Corrosion‘.
However, the management of MIC is not without unique challenges. The corrosion-causing microorganisms are diverse and thrive in some of the harshest environments. These include oil and gas pipelines, cooling systems, marine structures, and even household plumbing. MIC exhibits distinctive characteristics that distinguish it from other types of corrosion mechanisms, too.
In this article, we’ll take you on a journey that explores the challenges of managing MIC. It will highlight some essential knowledge that is required if we are to mitigate the detrimental effects of microbiological corrosion to enhance safety or working environments and increase the longevity of our industrial (and public) infrastructure.
The 5 Challenges of Managing Microbiological Corrosion
The unique challenges of managing MIC demand attention and proactive measures from corrosion professionals and the industries in which they operate. We see these challenges falling under five distinct categories:
- Standards: challenges in establishing guidelines, regulations, professional codes and risk assessment
- Identification of microbiological corrosion
- Assessment of severity and risk
- Treatment of MIC
- Monitoring of MIC
MIC is shrouded in mystery because it’s not as well understood as other corroiosn mechanisms. Yet to prevent it from causing the structural corrosion that leads to significant failures, and environmental and financial losses, we must address these challenges. To achieve this a proactive management approach is the key to ensure the safety and sustainability of critical infrastructure.
Let’s delve a little deeper into the understanding of these MIC management challenges.
Standards: Challenges in Establishing Guidelines and Regulations
The landscape of standards in the management of MIC is fractured. There is an absence of universally accepted standards, and this often leads to a lack of consistency in the approach to tackling MIC. This makes it difficult for corrosion professionals to establish and adopt comprehensive strategies.
Where guidelines exist, there is a considerable variation between different industries. Of course, some of this variation is due to the unique nature of each environment – and this also poses challenges for those who work within multiple industries. Navigating through a maze of divergent guidelines can be like walking through a minefield.
Any standardisation of guidelines and regulations would necessarily require personalisation to suit different sectors. We would need to consider a myriad of factors, including material compatibility, operational constraints, selection of fit-for-purpose materials, and environmental considerations for effective implementation of MIC management strategies.
Challenges in the Identification of Microbiological Corrosion
The microorganisms involved in MIC, and their ability to form biofilms, are complex and diverse, making it challenging to identify the exact MIC mechanisms in play. The analytical techniques to detect and identify microorganisms require specialist knowledge and tools.
“Different systems require different sampling procedures and planktonic sampling can be used to estimate the density and diversity of colonising microbe,” says Tony Rizk, CEO of Halo Sealing Systems Limited, and Course Lead for ICorr’s new MIC Training Courses. “In all cases, samples should be collected as close as possible to their source. The best representative samples are collected using online coupons, pigging sludge, surface scrapings, and sediment. Samples should be collected during normal operation and free of contamination. Collected samples should be preserved, transported and, if needed, stored at 4oC.”
Though we have witnessed significant progress in MIC science, very few have the required knowledge of the interplay between microorganisms, metallic surfaces, and environmental factors involved in the process. Such limited understanding is an obstacle to the development of effective MIC prevention and management strategies. Clearly, the way forward here is to aggressively share knowledge, and empower scientists and engineers to collaborate more effectively with a shared objective of unravelling the intricacies of MIC mechanisms and management.
A further complication that clouds the identification of microbiological corrosion is the overlap with other forms of corrosion. It is also common for MIC to co-exist with other corrosion mechanisms. Yet, to develop and implement effective prevention strategies, identification of MIC is critical. Not only is knowledge crucial here, but also the use of specific diagnostic tools and techniques.
Challenges in the Assessment of Severity and Risk
The third significant challenge is quantifying the extent of MIC damage. As MIC is often localised corrosion, assessing overall severity can be difficult – traditional techniques for assessing the extent of MIC damage may not be enough.
There is also a lack of predictive models to accurately forecast the progression of MIC and its effects on a structure or system – another reason we must collaborate in our research efforts to better understand unique MIC mechanisms. If corrosion scientists can develop data-led predictive models, corrosion engineers can use these to develop proactive MIC prevention strategies.
Finally, we must factor in the cost of MIC prevention and management. This means assessing its value to combat the economic impact of MIC. There is always a balance between the costs of impact and the costs of mitigation to be struck. Just how do we assess the long-term financial impact of microbiological corrosion?
Challenges in the Treatment of MIC
When considering treating MIC, we are faced with three challenges:
- Deeper knowledge is needed to select effective treatment options based on factors such as the specific environment, microorganisms involved, the severity of the corrosion, and the impact of treatment on the environment and infrastructure itself.
- Selecting suitable inhibitors and biocides requires an understanding of specific microbial species, operating conditions and geochemical composition, as well as understanding how the treatment will affect the structure over time.
- Implementing treatment in piping, confined and concealed spaces and large infrastructure is a complex process, and suitable application techniques must be selected and executed. Corrosion engineers and industrial microbiologists must also consider the long-term maintenance requirements post-treatment.
Challenges in Continuous Monitoring of MIC
If we are to instigate effective and timely mitigation and intervention for MIC, continuous monitoring is crucial. DNA technologies have improved MIC monitoring processes, yet their adaptation is still, relatively speaking, in its infancy. Sporadic inspections are unlikely to capture the rapid progression of MIC – reliable, real-time monitoring techniques are needed.
It’s also true to say that monitoring MIC is challenging because MIC often occurs in highly inaccessible locations, including offshore structures, underground pipelines, or submerged equipment. Not only might accessibility be limited, but we must also consider safety when conducting routine inspection of installing monitoring equipment.
The data collected can also be complex. It requires expertise to translate into meaningful conclusions about microbial activity, corrosion rates, and other relevant parameters. Incomplete or misinterpreted data can lead to ineffectual MIC management.
Overcoming the Challenges of MIC Management Starts with Understanding MIC
The challenges associated with managing microbiological corrosion are multifaceted. The lack of universally accepted standards, difficulties in identifying and assessing MIC, selecting suitable treatment strategies, and implementing continuous monitoring are hurdles that require dedicated effort to overcome.
It’s crucial that we invest in research, collaboration, and professional development. Enhancing our knowledge will help us to manage MIC more effectively. This will enable us to embrace the proactive approach that will safeguard our critical infrastructure for the future.
ICorr’s MIC Training Courses are designed to provide you with the detailed knowledge required to manage MIC.
- The one-day MIC Awareness Course delivers an overview of MIC phenomenon including corrosion-influencing microorganism groups, monitoring techniques, control methodologies, affected materials and identification, and managing MIC. It also discusses some of the MIC high-profile failures.
- The four-day Microbiologically-Influenced Corrosion (MIC) Course incorporates theoretical and practical sessions with a focus on providing detailed knowledge on managing and conducting an MIC control program. It includes sampling and monitoring strategies, data interpretation and presentation, and identification of potential risks. On completion of the entire course an ICorr ‘MIC Technologist’ certificate of attendance is awarded. For attendees who also take and pass the additional examination, an ICorr ‘Certified MIC Technologist’ certificate is awarded.
To learn more, please email the Institute of Corrosion for information about our new MIC Training Course.
Articles in This MIC Corrosion Series:
Bio-Corrosion Basics: What Is MIC Corrosion?
Real Life Impacts of Microbiologically Influenced Corrosion
The Unique Challenges of Managing Microbiological Corrosion
Introducing ICorr’s Microbiologically-Influenced Corrosion Courses