The cart is empty!
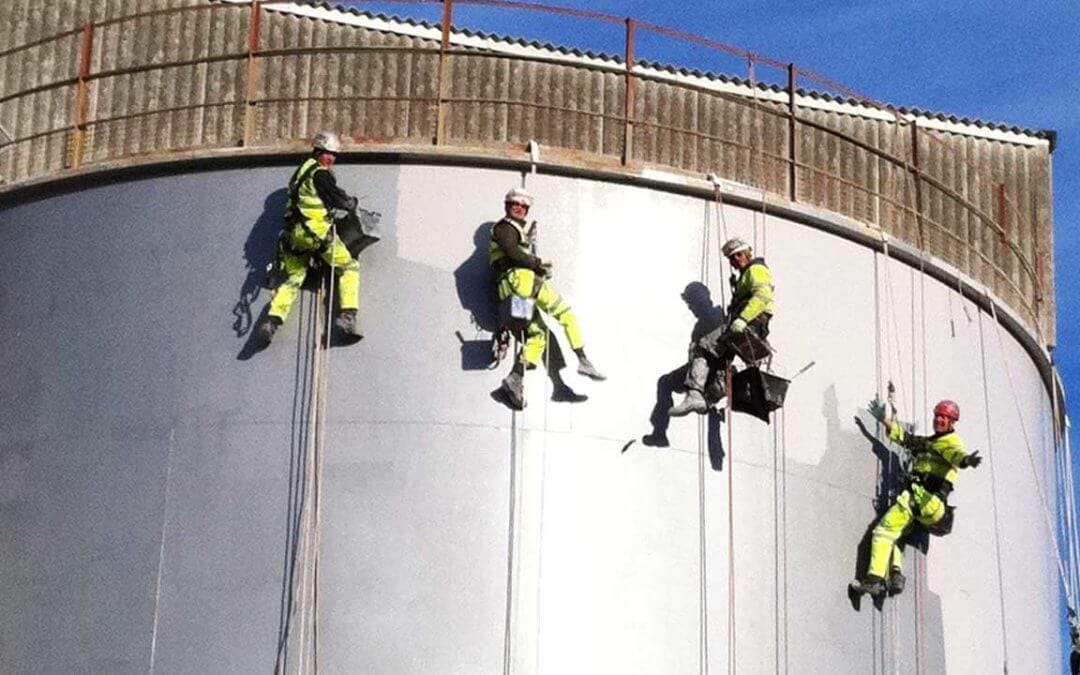
ICATS and Correx ─ All You Need to Know
Introducing the Industrial Coatings Applicator Scheme
ICATS may sound like a fancy slang word, but it stands for ‘Industrial Coatings Applicator Training Scheme’. It’s a scheme that has been designed specifically to meet industry demand for formally accredited training for applicators of coatings in the UK, and now around the globe. One of the primary functions of Correx Limited is to administer the ICAT scheme.
What is ICATS?
ICATS is a training and certification programme designed to provide standardised training and qualifications for industrial coating applicators. Those who have ICATS certification possess the knowledge and skills to carry out work as an applicator in a safe and planned manner.
The aim of the course is to improve safety and quality of industrial coating application. It is mandated by National Highways (formerly known as The Highways Agency), but is relevant across all sectors in which corrosion plays a role. These include construction, oil and gas, petrochemicals, nuclear and marine industries.
How does ICATS work?
ICATS is a comprehensive, structured training scheme covering various elements of coating applications, including:
- Surface preparation
- Coating techniques
- Equipment usage
- Health and safety
- Environmental considerations
The Industrial Applicator section also includes:
- Corrosion protection
- Paint types
- Painting inspection (QA and QC)
The framework of the programme allows individuals to progress from foundation skills to advanced techniques, gaining different qualifications and certifications on the way. Courses contain theoretical and practical learning. Newly qualified ICATS industrial coatings applicators receive an ICATS card according to the course the module they have passed. The scheme contains Industrial Coatings Applicator, Specialist Blast and Spray modules, and Supervisor and Technical Manager courses.
What are the benefits to individuals and companies?
The ICAT scheme delivers a host of benefits to individuals and employers who register to have their workforce certified.
Benefits for individuals include:
- Enhanced skills and knowledge, including a deep understanding of industry best practices. This helps to improve work effectiveness as well as the confidence of the individual.
- Recognition of competence delivered by gaining a recognised qualification. This demonstrates competence and expertise, enhancing credibility, employability, and career prospects.
- As a qualified ICATS operative, individuals are deemed to be up to date with the latest techniques to prepare surfaces and apply coatings in the safest way possible ─ helping them to exceed industry expectations, and ensure the quality and durability of applied coatings.
- Greater awareness of health and safety issues and practices. This includes the ability to identify potential hazards, appropriate handling of materials, and proper use of personal protective equipment.
Benefits for employers include:
- A competent workforce that can deliver high-quality coating application services, leading to improved outcomes, reduced reworks, and greater customer satisfaction.
- A workforce that delivers work of a consistent quality, operating at industry best practices and standards. This helps a company to maintain a higher level of quality assurance.
- Benefitting from greater competency across teams that have a strong foundation in surface preparation techniques, coating application methods, and equipment usage, efficiency and productivity improve.
- Incorporating relevant regulations and environmental considerations, the ICATS scheme helps to ensure that employees remain compliant with industry standards, reducing the risk of the consequences of non-compliance (such as rework, project delays, penalties or fines).
- A safer working environment, reducing the risk of potential health hazards, accidents, and litigation.
- Finally, clients are more likely to select a company with ICATS-certified staff. This demonstrates a commitment to high standards, professional development, and high-quality work. In two words: competitive advantage.
Where does Correx come into the ICATS equation?
Correx Limited is a wholly owned subsidiary of the Institute of Corrosion. First registered in 2003, its role is to organise the commercial activities of the Institute of Corrosion. Many people have asked where the name Correx came from – it is a combination of the words “Corrosion” and “Exhibition” –an early remit of Correx was to run exhibitions on behalf of ICorr. Correx has a Board of Directors made up from senior members of ICorr including several past Presidents. As already mentioned, to administer the ICATS . MD Kevin Harold explains more:
“As the MD, my roles are very varied. The work I do for Correx takes around a third of the time available to me. I juggle these responsibilities with those I have as Technical Director for Paintel Ltd.
“We’re a small core team at Correx with myself as MD and senior trainer for ICATS course. Robert Hurley is the second senior trainer and carries out ICATS audits for our 9001 certificate (he’s also senior painter and quality at Paintel Ltd.). David Mobbs assists with client communication, client visits, business development, and pretty much all things ICATS (his 40+ years of coatings experience is invaluable). At Head Office, Becky and Trish provide incredible help with admin and promotion ideas.
“I also author the ICATS courses, a job with which my wife helps me by helping guide me through online courses and transfer of information ─ as well as being a daily sounding board for me.
“This brings me to Correx board meetings, where we discuss ideas and keep everyone informed of what we are doing, who is responsible for what, and so on.”
ICATS. Not a trendy word, but certainly a trending certification in the corrosion industry. Companies that are involved in industrial painting are finding this certification, accredited by the Institute of Corrosion, is proving to be highly beneficial. It enhances skills, knowledge, and qualifications for individuals, while providing employers with a skilled workforce, quality assurance, compliance adherence, and a competitive edge in the industry.
Want to know more?
Our team is ready to answer your questions. All you need to do is email us at correx@icorr.org.