The cart is empty!
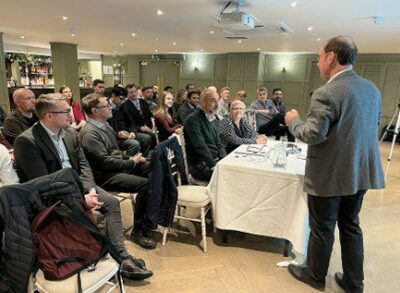
Young Engineer Programme 2022 – Who Won?
Could It Be You Flying to the AMPP Conference in the USA Next Time?
Conceived 10 years ago, and sponsored by BP throughout its history, the Young Engineer Programme (YEP) 2022 was held in Scotland for the first time. The final was in November 2022 and was attended by more than 40 people at the Palm Court Hotel, with another 15 online ─ the Aberdeen branch of the Institute of Corrosion put on a tremendous event.
Here’s the story of this latest YEP chapter, and details of how you could participate in the next YEP.
Why the Young Engineer Programme?
The aim of the Young Engineer Programme is simple, though extensive. The brainchild of our London branch, it is devised to:
- Help tackle skills shortages in the industry
- Prepare graduates for entry into the industry by helping to develop enhanced skillsets
- Be the first stage to achieving MICorr/Ceng status
This was the fourth YEP in the history of a programme that has been interrupted by the Covid pandemic. With 24 candidates selected from more than 50 applicants, it proved to be not only as popular as ever, but equally challenging to name a winning team.
In each YEP, the candidates are divided into teams and set the task of developing solutions to a real-world corrosion case study.
Candidate selection criteria
Each year, selection criteria are determined. The 2022 criteria covered five elements:
- Students in the early stage of their corrosion-related career
- Two to six years of relevant experience
- Aged 35 or under
- Relevant academic background
- Based in Aberdeen or willing to travel at their own expense
Creating the YEP teams
It was no easy task for the YEP committee to select students to take forward. The committee deserve special praise for the work they put into this and throughout the programme, especially Hooman Takhtechian (2021-2022 session chair) and Steve Paterson (YEP mentor supervisor/Case study organiser).
Six teams of four students were created, with team members chosen based upon:
- Experience
- Academic background
- Employer
The challenge here was to ensure that all teams had an average experience of between four and four-and-a-half years of experience per team member and that no team had two or more members from the same company or from the same company as the team mentor.
The 2022 case study and the challenge set
The Young Engineer Program teams were faced with a highly complex and challenging case study with the following brief:
“A 15-year-old offshore platform in sweet service that had a record of poor corrosion management with the possibility of a new owner for another 10 years of service. The potential new owner is both difficult and demanding, and a subsidiary of an international operator. With the possibility of a tie-in of a new field with slightly sour fluids, it would be necessary to deal with an intermediary integrity services contractor.”
Based upon an actual platform in the North Sea, the teams were tasked to:
- Assess and rank the key Integrity Management threats
- Provide mitigation measures and a suitable corrosion management system
- Deliver materials options for the required new pipeline
- Management and impact of change in operations
- Identify all other relevant factors to deal with the client effectively
To complete all of this, teams needed to:
- Analyse and discuss the information and data provided
- Identify any gaps in information and any assumptions that may need to be made
- Perform a high-level risk assessment to identify key threats to the mechanical integrity of the pressurised systems (structural integrity was excluded)
- Identify what further information or data was required for the other tasks in the exercise
- Propose a systematic approach to manage the key threats including mitigation measures, corrosion control requirements, performance monitoring, and the resources required to manage the process
- Propose materials of construction for a pipeline, including welding consumables, and any testing requirements to tie back the new reservoir to the platform, and explain the basis for the materials selection and how any corrosion threats will be mitigated
- Identify what changes, if any, to the existing facilities would be required should the new sour reservoir be tied back to the platform
- Propose a strategy for convincing the integrity management contractor that the approach is the optimal solution and that you are the right team to do the job
Oh, and present all the above in 20 minutes on the presentation night! And any team that overshot its 20 minutes were deducted points.
The quality of work completed and presentations made were so high that the judging panel of Chris Williams (BP, Sunbury), Susan Cushnaghan (formerly Shell Aberdeen), and Stephen Tate (2022 to 2024 ICorr President) certainly had their work cut out.
All teams were deserving of the huge praise they received for the diversity of their solutions, the professionalism of their presentations, and their enthusiasm for the task in hand. We should also mention that this is a testament to the incredible effort and contribution of all the YEP 2022 lecturers and course mentors.
The 10 lectures (and lecturers) that were delivered during the course of the YEP 2022 programme were:
Lecture | Lecturer |
Fundamentals of Corrosion | Steve Paterson |
Asset Integrity Management | Stephen Tate |
Coatings and Linings | Michael Young |
Case Study | Steve Paterson |
Presentation Skills | Olubayo Latinwo |
Materials Selection/Welding | Martin Mweemba |
Corrosion Under Insulation and Fire Management | Clare Watt |
NDT Appreciation | Jim McNab |
Introduction to Fitness for Service Assessments | Pieter Van Der Vyer |
Corrosion Aspects of O&G Production Chemistry | George Winning |
Introduction to Cathodic Protection | Brian Wyatt |
Team mentors were:
- Steve Plant
- Alistair Crichton
- Bruce McKenzie
- David Hills
- Alireza Aghasadeghi
- Muhammad Ejaz
And the winners are…
One team had to win, of course, and only by strict application of the marking criteria could the teams be separated. The criteria for the presentation were:
- Analysis of the scenario and current integrity status of the pressurised systems of the platform (20 marks).
- Application of a systematic methodology to manage corrosion and surveillance activities (20 marks).
- Viability of the proposed approach to prolong service life (10 marks).
- Assessment of material options for the new pipeline (10 marks).
- Assessment of the impact of change in operation with H2S (10 marks).
- Identification and assessment of factors in dealing with the client (10 marks).
- Overall quality and balance of the presentation, plus team coordination as demonstrated by the presentation (20 marks).
Time for the drumroll…
Congratulations to the winning team who were mentored by Alireza Aghasadeghi and who were:
- Rosie Bird (PIM)
- Jamie Hillier (Xodus)
- Lee Hunter (PBS Offshore)
- Christopher Slater (Stork)
The judges also awarded a Leadership Prize, based upon feedback about performance during the whole programme from mentors, judges, and committee members for teamwork and presentation skills. This was awarded to Eilidh Macdonald (Subsea 7).
All the winners won an all-expenses paid trip to the AMPP Annual Conference & Expo 2023 in March, courtesy of key sponsor BP.
Could you be a Young Engineer Program winner?
We are already planning YEP 2024, to be managed by Young ICorr and pencilled in to take place in London. To register your interest in becoming a team member for the next YEP, please email our Young ICorr Chair James McGladdery. It’s the first step to becoming one of the next winners of this prestigious programme.