The cart is empty!
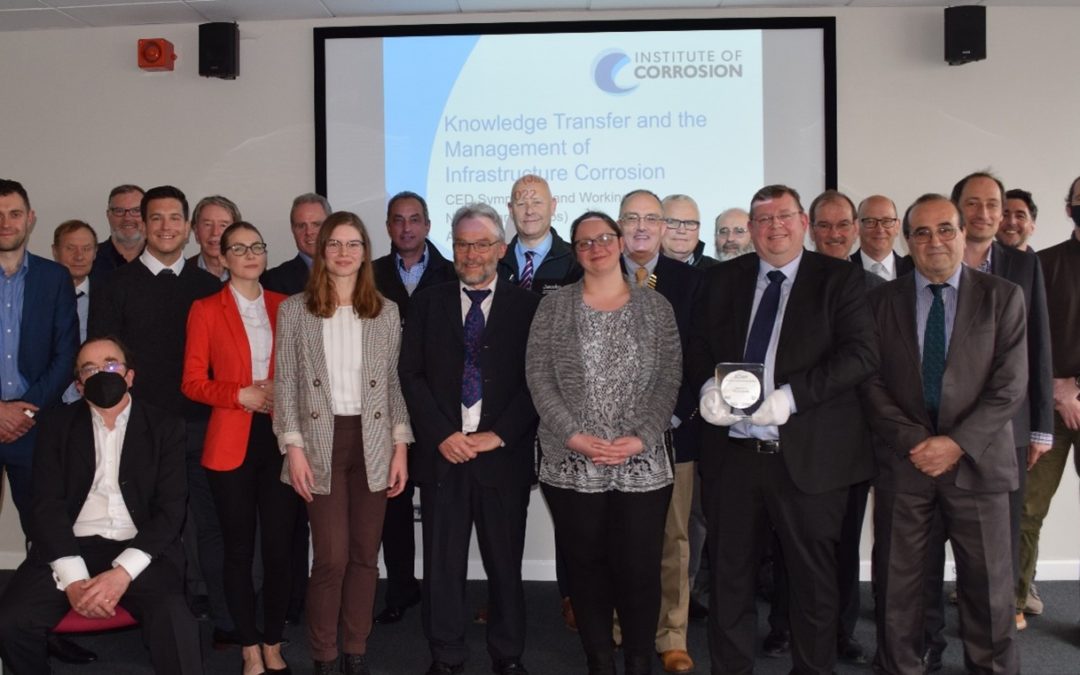
Corrosion Engineering: A Working Day to Remember
5 Talks, 4 Working Group Sessions, 1 Prestigious Award, and a New Chair… Phew!
The corrosion engineering community was able to get together and do what they do best at the Institute of Corrosion’s Corrosion Engineering Division (CED) Working Day and Symposium in April. Discuss latest trends, share knowledge, and brainstorm ideas and concepts.
Held at the magnificent National Railway Museum in York, this was the latest in a series of CED Working Days that offer delegates exceptional networking opportunities – as well as a chance to visit the museum.
A welcome to introduce a sad farewell
Nick Smart, Chair of CED, welcomed the delegates to the event and introduced the speakers. This was the last Working Day and Symposium that Nick has introduced, as, after 15 years of excellent service as the CED Chair, he is stepping down.
Nick’s shoes will be challenging to fill, and the meeting showed their appreciation for his unstinting efforts and contribution throughout his years at the helm. A sad but celebratory farewell, and a warm welcome to the incoming Chair.
Introducing the Corrosion Engineering Division’s new Chair
Before the main proceedings began, Nick Smart introduced the delegates to the CED’s new Chair, Danny Burkle.
While Nick will be a hard act to follow, we’re incredibly lucky to have Danny taking over the steering of the CED.
A business development engineer, Danny’s prime responsibilities in his role at LBBC Baskerville include developing business strategy, business, and product range for innovative corrosion testing autoclaves to simulate realistic field environments within several high-pressure and high-temperature applications and industries.
His Doctorate in mechanical engineering, which he completed at the University of Leeds, focused on corrosion mechanisms involved in carbon dioxide corrosion, and protecting carbon steel assets against corrosion by forming natural corrosion products. The industry-focused research, sponsored by BP, was based on real-life engineering problems.
With both academic and industry experience, Danny’s role as CED Chair could help to forge closer relationships between research and industry.
Knowledge transfer in five presentations
Through the day, delegates were treated to five presentations around this year’s theme of ‘Knowledge Transfer and the Management of Infrastructure Corrosion and Management’:
1. Hot dip galvanizing for specification and use in infrastructure projects
Presented by Desmond Makepeace of the Galvanisers Association, this talk began by describing the galvanising process, with reference to the appropriate standard EN ISO 1461.
Desmond discussed a variety of defects, which of these can be tolerated, and factors affecting the quality of galvanising, including coating thickness, renovation, adhesion, joining-bolting, duplex systems, maintenance, venting of hollow sections, and overlapping sections. He also discussed how the atmosphere affects corrosion of galvanised structures.
2. Best management practices to transfer knowledge to ensure integrity assurance optimisation for oil and gas production
One of the highlights of the Working Day, this Young ICorr talk was given by Izabela Gajewska. Izabela was a member of the winning team of the 2020 cohort of the Institute of Corrosion’s Young Engineer Programme (YEP) (which you can read about in our article ‘A case study for all young corrosion engineers – it could be you’).
Izabela discussed the nature of knowledge transfer, and the best practices to ensure this happens effectively and successfully – such as planning, work experience, mentoring, specialised training, attending conferences, and so on. She spoke about creating an effective mentoring strategy, delivery of training, and the value of external training courses in areas including coating, passive fire protection, cathodic protection, and risk assessments.
3. The consequences of climate change for corrosion
Chris Atkins of Mott MacDonald gave a thought leadership talk, discussing his ideas around climate change and corrosion. For example, can we rely on historically established corrosion rates as emissions of carbon dioxide are increasing? An ensuing reduction in the pH of natural waters could make them more aggressive to concrete, though it may reduce the corrosion rate of galvanised steel.
Temperature increases reduce the dissolved oxygen content in water, but Chris demonstrated how this temperature increase does not automatically produce an increase in corrosion rates – and a reduction in carbon dioxide levels from today’s elevated levels is likely to reduce atmospheric corrosivity.
The real issue? As far as Chris is aware, no one is taking a global view of the effect of climate change on corrosion, and this leads Chris to ask one last question: is this an opportunity for the Institute of Corrosion to take a leading role?
4. Academia and industry: How can we advance corrosion science and engineering together?
“Academics want to publish. Companies want to make money.”
Old thinking.
Richard Barker of Leeds University addressed this in a thought-provoking talk that pointed to research around this topic, as well as opportunities and challenges that exist for academia and commercial operations to collaborate more effectively.
While academia has the time and resource to produce new knowledge which can be used commercially, barriers that exist include complexity of communication to share knowledge and the complexity of initiating and continuing collaboration.
Perhaps the biggest challenge is trust. Industry must trust scientists, but the complex and ever-changing nature of large bodies of academic research makes this challenging for many businesses. However, we are seeing that some companies are developing strategies to identify and reach out to research groups for collaborative projects – and creating collaborative success.
The conclusion? Yes, there are challenges that exist, but these can be overcome with the correct approach from both sides. If we can do this, then there are significant benefits to be accessed from greater collaboration between academia and industry.
5. Radioactive waste disposal – where corrosion science meets corrosion engineering
In the first presentation of the afternoon session, Nick Smart gave his last CED Working Day and Symposium presentation as Chair.
Nick discussed the three levels of radioactive waste, and discussed the various research that supports the corrosion engineering and safety assessment aspects of radioactive waste management.
Describing corrosion issues that exist (such as atmospheric external corrosion of stainless steel waste containers during interim storage, the corrosion behaviour of waste uranium, aluminium and Magnox after encapsulation in cement, and the long-term corrosion of waste containers after disposal in deep geological repositories), he pointed out that the UK’s total nuclear waste inventory would fill Wembley Stadium.
Nick discussed the two main concepts for geological disposal of high-level waste, and the challenges that exist within diverse global geological environments – key environmental considerations when disposing of radioactive waste underground include oxygen concentration, chloride and sulphide concentrations, radiation levels and microbial activity.
Nick outlined the analytical techniques that are used to characterise the corrosion behaviour and corrosion rates of candidate waste container materials in long-term in situ experiments conducted under representative conditions, and how such studies can be supported by comparison with the corrosion of natural analogues, such as archaeological artefacts like the Anglo-Saxon Coppergate Helmet currently exhibited in the Yorkshire Museum.
The session concluded with a short talk by Stuart Bond from AMPP. He discussed the development of revised standards being conducted by AMPP (a merger between SSPC/NACE was rolled out in January 2021).
The Working Group Meetings
At the end of the talks, delegates had an opportunity to visit the National Railway Museum and attend Working Group Meetings. This year the following groups held sessions:
· Nuclear Corrosion Group
Chaired by Nick Smart, the Nuclear Corrosion Group met to discuss a wide range of corrosion issues arising during the storage of nuclear waste. These included assessment of pitting corrosion in stainless steel during storage in atmospheric conditions, the effects of microbial corrosion on cast iron under damp conditions, and the potential for galvanic corrosion of stainless steel in contact with graphite in cementitious environments.
· Coatings Group
There was plenty to discuss in this group, chaired by Phillip Watkinson. This included:
- The impending review of the Coatings Technical Information Documents (CTID), created in 2016-17
- The transfer of NACE Coatings Standards to AMPP
- A suggestion by Douglas Mills that EIS measurements (ISO 12944) be reviewed
- Phillip Watkinson tabled that two Paints and Varnishes Standards (BS EN ISO 4628-1:2003 and 4628-2:2003) should also be reviewed
It was agreed that an interim meeting would be held ahead of next year’s CED Working Day.
· Cathodic Protection Group
Acting Chair Chris Lynch directed discussion around subsea CP systems and performance of flush fit aluminium deep sea anodes on complex piping systems. This included current distribution, current density, anode installation methodology and expected performance along with coatings, anode corrosion products, and calcareous deposits.
· All Energy Group
Chaired by Steve Paterson, all those present contributed to a positive discussion about the purpose of the group, which has been formed by adding renewables to the previous Oil and Gas Group. Items covered included:
- Production of documents
- Mentoring of Young ICorr members
- Information exchange via networking
- Engagement with other organisations like AMPP
After an update with regards to standards, it was agreed that another meeting would be held in October.
The Paul McIntyre Award
As is customary at the CED Working Day and Symposium, before the group broke for lunch, the President presented the Paul McIntyre Award.
This year’s recipient of this prestigious award, the premier engineering award of the Institute of Corrosion, was Chris Lynch, who has worked tirelessly for many years and made many outstanding contributions to many aspects of corrosion engineering. You can read more about the award and Chris’s contributions in our article ‘Chris Lynch – Recipient of the Paul McIntyre Award 2022’.
Don’t miss out on the benefits of the CED
The CED is a driving force within the corrosion industry. It shares news, views, and learning to the Institute’s membership, via several channels, including:
- Access to PDF versions of all the talks outlined above in the Members Area of the ICorr website
- Corrosion Management Magazine
- The Institute’s Members Area on its website
- Its various Working Groups
- Informal and internal communication and networking
- Working Days and Working Group meetings
Chairs of individual Working Groups liaise with counterparts at other corresponding Working Groups in international bodies. The Working Groups also provide a mechanism for members to collaborate effectively; for example, by jointly preparing documents that are of immediate and practical use to them in their field of activity. Such documents are downloadable within the Members Area of the ICorr website.
If you are not already a member of the Institute of Corrosion, check out our membership page to learn how to become a member and immediately begin to enjoy the many benefits of membership of the Institute of Corrosion.