The cart is empty!
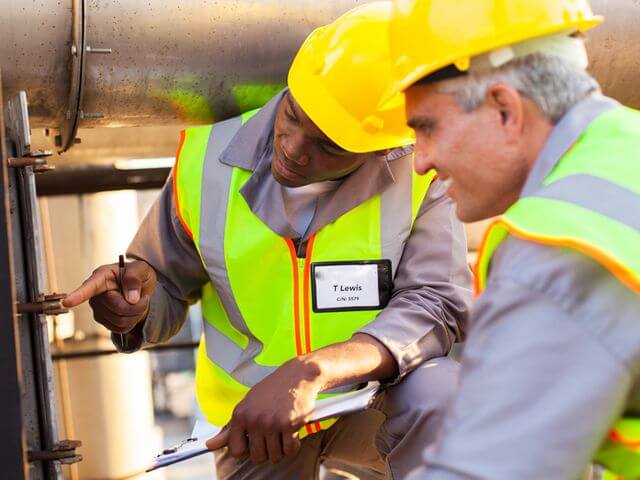
How Is a Coating Condition Survey Conducted?
The eight-step coating survey methodology
Is a full coating condition survey necessary before applying a coating system? Isn’t understanding the environmental issues and operating in line with ISO 12944 enough?
In a short answer to these questions, imagine that your car is making strange noises from under the bonnet. You take it to two mechanics.
The first opens the bonnet, looks inside, taps the engine in a couple of places with a hammer, and then diagnoses the problem.
The second mechanic opens the bonnet, connects an electronic diagnostic machine, and invites you to have a tea while you’re waiting. Having received a computer printout, the mechanic then raises the car so he can look underneath. He makes a couple of phone calls, before presenting you with a detailed appraisal of the issue you have.
The question is this: which mechanic do you believe will provide the best, safest, longest-lasting, and most cost-effective solution? The one who carried out the most extensive and structured assessment, right?
In this article, we examine how an effective coating survey should be conducted to provide the knowledge needed to ensure the correct coating system is applied most cost-effectively.
When is a coating survey used?
A coating condition survey (or ‘coating survey’) should be used as a proactive measure in the protection of any previously coated structure. For example, this may include surveying coatings in the offshore environment or on bridges that are at risk of corrosion. Such proactive surveying will help to reduce maintenance costs, increase the integrity of infrastructure, and improve safety. A win/win/win.
Steps for successful surveying of coatings
To be effective, a coating survey must be designed, carried out in line with planning, recorded and reported. It’s essential to conduct coating surveys using a methodical and structured approach. This ensures that each survey benefits from the same rigorous standards. The following eight steps form the core of a coating condition survey.
1. Planning the coating survey – what is needed?
It’s important to define the parameters of the survey before it is started. The information that is needed may depend upon factors such as:
- Age of the asset
- Time since the last coating survey
- The value of the asset
- When routine maintenance is due
- If a new coating system will add value to the asset
- Health and safety issues
2. Planning the coating survey – what is the expected output of the survey?
The detail required of the survey should also be assessed. It is possible to produce a survey in too much detail. For example, consider an example of surveying the condition of a front door. Should you survey it as a single item, or assess each element separately? If the latter, then a survey will include each hinge, the letter box, the door knocker, each pane of glass, the inside and outside handles, the inserts, the frame, and the lock mechanism. One item becomes a survey of a dozen or more items.
If a survey is too detailed, it risks information overload and crucial details could be overlooked upon review. If not detailed enough, the survey may miss crucial details altogether.
3. Planning the coating survey – how do you grade conditions?
The survey should carry out its assessment with a recognised and consistent grading system that establishes the severity of degradation of each component under the survey. The standards to which the assessment of coating/corrosion degrading must conform to are ISO 4624 parts 2-7 and the European Scale of Rusting for Anticorrosive Paint (commonly referred to as the Re Scale).
4. Conducting the coating survey – note physical details
The survey should consider all the corrosive environmental issues that may affect the coating’s current condition. The location of the structure and the environmental factors associated with the location will affect how a coating performs. Factors include climate, moisture, and UV exposure.
5. Conducting the coating survey – the original application
To better understand how the original coating has been affected by physical details, the survey should include key information about the original coating such as the date of application, the coating manufacturer, the applicator, and so on.
6. Conducting the coating survey – note extraordinary events and occurrences
Over time, a structure’s coating may be affected by many events. These may include severe weather conditions, accidents, fire, maintenance, repairs, and refurbishment. The more detail that can be compiled within this section of the survey, the more informed the survey’s results will be.
7. Conducting the coating survey – assessing the coating
The survey should move onto assessing the existing coating, considering adherence to the structure, dry film thickness, the percentage of failure across the system and its component parts, and the presence of aspects such as mill scale, chalking, pitting, etc.
8. Recording and reporting – planning the next steps
The survey should record all details required of it, as set out in the planning steps. The survey should make recommendations as to:
- Whether immediate maintenance is required
- What maintenance should be planned for the next one to three years
- The locations that are difficult to reach and which may require extra measures
- Whether coating of an area may lead to the need for adjacent areas to be recoated
Answering these points will form the basis of a full coating maintenance programme that is designed to ensure asset integrity during the expected lifetime of the asset.
In Summary
A coating condition survey should form part of the routine maintenance checks for all structures on which protective coatings are used to combat corrosion. The survey should assess all components of the structure that have been identified as required to be surveyed, and assessment should be conducted in a manner that ensures consistency and completeness.
By following a consistent survey methodology, the survey should establish the current state of the existing coating, and the reasons for any degradation.
By monitoring the performance of a structure’s coating, an asset owner can understand the action needed to reduce the effects and consequences of corrosion. To ensure this, it is imperative that surveys are carried out by those with the training, experience, and qualifications to do so.
In our next article, we examine a world first that will define the coating survey professional and how industry carries out coating condition surveys in the future. In the meantime, to find out more about the Coating Survey Course, email the Institute of Corrosion or contact Corrodere.