The cart is empty!
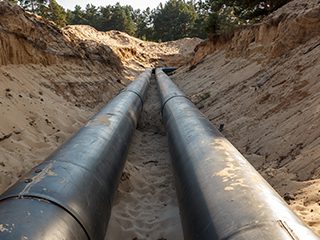
An Introduction to Top-of-Line-Corrosion (TLC)
Understanding the Mechanisms Behind Pipeline Corrosion
Top-of-Line-Corrosion (TLC) is a phenomenon characterized by localised corrosive attack at the upper internal surface of pipelines. TLC is primarily a consequence of internal condensation of water at favourable locations along a pipeline and typically occurs in untreated wet natural gas transport lines.
Here the wet natural gas phase will invariably contain the corrosive agent carbon dioxide (CO2)-resulting in conditions often referred to as ‘’sweet’’ corrosion) but may also contain hydrogen sulphide (H2S) known as ‘’sour’’ corrosion, and volatile organic acids most commonly acetic acid (HAc). However TLC can also be a credible corrosion threat in wet multiphase hydrocarbon transport lines operating under stratified flow conditions.
Understanding TLC is crucial due to its potential to severely compromise the structural integrity of pipelines if left undetected and not actively addressed. Effective management of TLC can prevent costly repairs, environmental damage, and catastrophic failures, thereby safeguarding both assets and personnel.
Mechanisms of TLC
Corrosion is the process in which oxidation caused by chemical or electrochemical reactions causes a metallic material to deteriorate. Where the corrosive phase present is electrically conductive – contains ionic species – the resulting corrosion reaction is electrochemical in nature. Anode and cathode sites form on the metal surface which is connected ionically through the conductive corrosive phase and electrically through the metal resulting in formation of active electrochemical (corrosion) cells.
In fact, all metal loss corrosion processes in the presence of an aqueous phase are electrochemical in nature and can result in general and/or localised metal loss corrosion depending on the anode-to-cathode area ratio, composition/chemistry of the aqueous environment present, the formation of corrosion product films and the level of protection they afford – as well as factors such as the properties of the metal, temperature, and presence of a static or flowing/refreshed aqueous phase.
TLC, where condensation plays a pivotal role, is a particular form of aqueous based corrosion that, if left undetected, can (in extreme cases) result in highly localised attack at the top section of the pipe. Under favourable conditions, this can lead to rapid penetration resulting in a leak, and, under certain extreme circumstances, complete failure of the pipeline material.
As warm, moisture-laden natural gas flows through cooler sections of the pipeline, water vapour droplets condense on the inner surface, creating a favourable environment for corrosion. The condensed water will rapidly dissolve corrosive gases like carbon dioxide (CO2), hydrogen sulphide (H2S) and HAc from the wet gas phase.
In the most common case of the presence of CO2 in the wet gas phase the chemical and electrochemical reactions involved in TLC are:
- Chemical Formation of Carbonic Acid – resulting from CO2 dissolving in condensed water droplets, forming carbonic acid (H2CO3).
- Dissociation of H2CO3 – to bicarbonate ions (HCO3–), carbonate ions (CO32-) and hydrogen ions (H+), the latter lowering the condensed water’s initial pH typically to <5 which determines its initial corrosivity.
- Anodic Electrochemical Reaction – where iron (Fe) from the steel pipe dissolves into the condensed water droplets to form iron ions (Fe2+).
- Cathodic Electrochemical Reaction – where hydrogen ions (H+) are reduced to hydrogen gas (H2) to complete the electrochemical corrosion cell.
- Overall Corrosion Reaction – as the concentration of Fe2+ ions increase as corrosion progresses it has an increasing buffering effect on pH to a maximum when the water phase becomes Fe2+saturated (pH >5) with subsequent supersaturation resulting in surface formation and growth of an iron carbonate (FeCO3) film/scale that, dependent on its stability and surface coverage, can provide a level of protective under favourable conditions.
The presence of HAc affects Fe2+ saturation solubility and supersaturation limits and hence interferes with the formation of a protective FeCO3 layer. The effect on FeS films formed when H2S is also present is less clear as these films are less soluble, i.e. they require a much lower concentration of dissolved Fe2+ to form and so form earlier then FeCO3 in the overall corrosion process.
Incomplete filming where FeS is present can support and accelerate highly localised corrosion (pitting) due to the electrically conductive nature of FeS compared to FeCO3. Furthermore FeS can poison the hydrogen gas (H2) cathodic reaction raising the potential for atomic hydrogen (H) – intermediate step in formation of H2 – diffusing into the steel matrix and introducing a risk of localised hydrogen embrittlement and threat of cracking if the quality/type of steel and associated welds are not cracking resistant.
Conditions Leading to TLC
Environmental factors such as temperature, rate of condensation, and the presence of corrosive agents significantly influence TLC. Fluctuating temperatures promote condensation cycles, which are highly influential for TLC initiation and progression.
Operational parameters including flow rate/regime, gas composition, and pipeline pressure affect the rate and severity of TLC. High flow rates can increase the frequency of condensation events, thereby accelerating corrosion processes.
Presence of acidic gases CO2 and H2S in the transported wet gas phase and volatile organic acids which singly and collectively contribute to TLC as they readily dissolve in the condensed water, forming weak acids that can aggressively attack the pipeline material.
Where is TLC most Common?
TLC is most prevalent in oil and gas pipelines where a wet natural gas is transported over long distances. The temperature gradients and varying flow regimes influenced by pipeline profile and surrounding topography – subsea and on land – and flow rate within a pipeline can conspire for condensation and subsequent TLC to occur.
Consequences of Top-of-the-Line Corrosion
Undermining the structural integrity of pipelines, leading to thinning of the pipe wall, leaks, and, in the extreme, catastrophic rupture especially if hydrogen embrittlement has subsequently occurred, TLC can result in significant operational downtime and maintenance costs. Direct costs such as repair and replacement, and indirect costs like production losses and environmental cleanup combine to substantial total economic impact.
Safety hazards associated with TLC include the risk of pipeline failure, which can lead to fires, explosions, and toxic gas releases. Protecting personnel and communities from these dangers is a paramount concern. In the extreme the consequences may affect continuing Licence to Operate.
Detection Methods for TLC
Given TLC only occurs and becomes established at specific locations along a pipeline where conditions favour water condensation, how and where to conduct meaningful inspection and monitoring presents a significant logistical challenge. Particularly because flow rates and operating conditions along the pipeline can alter corrosive conditions, and because detection needs to be non-intrusive to have no lasting detrimental effect on condensation.
This highlights the importance of first undertaking systematic corrosion risk assessments which need to be routinely reviewed and updated accordingly.
Direct Detection
The most detailed and assured means of detection is to undertake periodic Intelligent Pigging of the pipeline which is a key to assessing and satisfactorily establishing a pipeline’s overall continuing Fitness-For-Service (FFS). It is also a key feature of a Pipeline Integrity Management System (PIMS) with frequency of running determined by all the credible corrosion threats identified and current condition of the pipeline.
An intelligent pig commonly uses either magnetic-flux leakage (MFI) or ultrasonic (UT) on-board inspection technology via a circumferential array of sensors; but ‘combo’ MFL-UT tools are also available. Also development of secondary eddy current in-line inspection technology has proved effective at detection of shallow internal corrosion which TLC can exhibit.
It is important to note that Intelligent Pigging is a lagging indicator of the presence and rate of corrosion which may well vary over time and in response to changing operating conditions.
‘Real Time’ Monitoring
Simply relying on conventional intrusive weight loss coupon (WLC) and electrical resistance (ER) probe corrosion monitoring at the inlet and outlet of the pipeline, a common and convenient general approach, is of highly questionable value and relevance where TLC is concerned.
There are several non-intrusive and highly sensitive externally mounted Non-Destructive Testing (NDT) systems available using ultrasound or eddy current transducer technology suited to ‘real time’ pipe wall corrosion monitoring at selected locations along a pipeline. They can be retrofitted including subsea and using sensor arrays give 3600 pipe wall coverage. However, knowing where to meaningfully locate them requires very careful consideration and where correlation with Intelligent Pig inspection data is invaluable.
Prevention/Mitigation Measures Against Top-of-Line Corrosion
Key to effective prevention and mitigation is having a ‘real time’ picture of how the pipeline operating conditions affect the threat presented by TLC and its likely locations. This should be a key feature during design and supporting subsequent operation over life of the pipeline drawing on dynamic multiphase flow modelling to define flow rate of phases present, flow regime (e.g. stratified, annular, slug), temperature and condensation rates as they all vary through the length of the pipeline.
Prevention
Most likely addressed at design but could in principle be a retrofit action:
- Drying before entry into the pipeline – removal of all co-produced liquid phases and drying the associated wet gas to a water dew point temperature below the lowest operating temperature to be expected along the pipeline. This has a cost impact on upfront CAPEX and life of pipeline OPEX but if well managed is extremely effective as gas export pipelines containing very high levels of corrosive CO2 (>20%) have shown.
- Using a suitably qualified Corrosion Resistant Allow (CRA) – either fully fabricating the pipeline out of or as an inner liner in a low alloy carbon steel pipeline. This a very high CAPEX option that really receives consideration for short safety-critical sections of pipeline – e.g. export risers, pipeline entry into onshore processing facilities.
Mitigation
- Treatment with corrosion inhibitor is the most commonly employed mitigation method and invariably a first consideration over prevention options at the design stage. While having a CAPEX element associated with installation of deployment facilities, the main associated cost is life of pipeline OPEX. The active presence of corrosion inhibitor is a continuous requirement to be effective where inhibitor efficiency at best lies between 95% and 99% supported by a Corrosion Allowance built into the pipe wall thickness.
- Corrosion inhibitors have a somewhat chequered history with reliance solely on deployment by continuous injection in effectively mitigating TLC. This is due to commercially formulated inhibitor products having limited volatility to be transported for any significant distance in a wet gas phase along the length of a pipeline and so not being accessible to readily dissolve into top of line condensation where conditions are favourable pH stabilisation – promoting formation of a very protective FeCO3 surface film by directly raising the pH of an aqueous phase to pH≥ 7 – has received attention and limited use as an alternative lower recyclable OPEX approach for inhibiting corrosion in wet gas pipelines but again its ability alone to directly inhibit TLC is questionably.
Other methods of inhibitor deployment such as regular batch treat and/or use of specifically designed pigs that spray inhibitor to top-of-line may be required in support of continuous injection or even replace it for achieving overall effective corrosion control including TLC.
Mitigation of TLC by corrosion inhibitor requires rigorous prequalification testing preferably including use of large diameter flow loop testing supported by a sound and regularly reviewed corrosion management programme.
- Presence of external insulation to minimise through-wall thermal loss and rate of fall in operating temperature profile across the pipeline to limit and possibly prevent condensation accumulation, thereby mitigating TLC. External insulation is only suited for use with land-based pipelines; and care needs to be exercised to prevent ingress of moisture into/under the insulation introducing the risk of Corrosion Under Insulation (CUI) occurring which could become a comparable or more severe corrosion threat than TLC.
Upshot of Top-of-Line Corrosion
Mitigating Top of Line Corrosion in wet gas pipelines requires a multifaceted approach, including appropriate material selection, operational adjustments, and advanced monitoring and inspection technologies. Understanding the conditions that lead to TLC, such as condensation of water containing corrosive agents, and implementing effective preventative/mitigating measures can significantly enhance pipeline longevity and safety.
Integral to maintaining our infrastructure in the oil and gas and other industry primary product pipelines is effective inspection. It’s an exciting area of work, with job opportunities around the world.
If you are new to the subject of TLC and want to know more about it, then ICorr’s Fundamentals of Corrosion Engineering training course would be an excellent starting point.