The cart is empty!
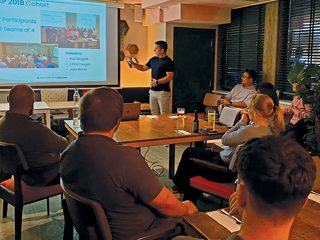
Young Engineer Programme 2024: Launched and Off to a Successful Start
YEP 2024 Sprints Out of the Blocks
Standing at the forefront of the corrosion industry, the Institute of Corrosion understands the critical nature of preparing the next generation of corrosion engineers to tackle the significant challenges and threats that corrosion poses to the world’s infrastructure and economy. Which is why we are delighted to announce the launch of the Young Engineer Programme (YEP) 2024.
In this year’s programme, we’re building on the success of previous years. Coordinated and managed by Young ICorr for the first time, YEP 2024 promises to be an even more enriching and transformative journey for aspiring corrosion professionals.
Young Engineer Programme 2024: Key Takeaways
- YEP is meticulously designed to cover the spectrum of corrosion management, from the fundamentals of corrosion to the intricacies of materials selection, integrity management, and beyond.
- The curriculum is structured to ensure participants gain not just theoretical knowledge, but also hands-on experience through real-life case studies and team projects.
- As in previous years, perhaps the most exciting aspect of this year’s YEP is the real-life case study challenge, where participants will apply their learning to solve actual corrosion problems, culminating in a presentation to a panel of judges.
- The winning team will be awarded an all-expenses-paid trip to the AMPP 2025 Conference in Nashville, USA, confirming ICorr’s commitment to rewarding excellence and innovation.
YEP 2024 – Kicking Off in London
YEP 2024 kick-started with an inaugural event in London, marking a momentous beginning to a year-long journey dedicated to nurturing tomorrow’s corrosion management experts.
This event wasn’t simply a formal introduction to the programme. It was a vibrant gathering of passionate individuals, including the selected participants, esteemed ICorr members, and distinguished speakers from the corrosion community.
Meet the Participants
This year, we’re thrilled to welcome twenty-six early-career professionals from diverse backgrounds, including engineering, science, and research, all sharing a common goal: to excel in the field of corrosion.
Representing a broad spectrum of companies and academic institutions, they bring a wealth of perspectives and a shared eagerness to dive deep into the world of corrosion. Their diversity is not just in their professional backgrounds but also in their aspirations, with each looking forward to contributing to and benefitting from this unique learning experience.
Drum roll, please, as we bring this year’s YEP participants on stage!
- Alvaro Gonzalez Fuentes, Wood Thilsted
- Alyshia Keogh, University of Manchester
- Amy Johnstone, Kent PLC
- Ben Hudson, Premtech
- Berenika Syrek-Gerstenkorn, Scottish Power
- Christina Igube, C-Probe Systems
- Clayton Bevas, Jacobs
- Dilshad Shaikhah, University of Leeds
- Ellie Lowe, DNV
- Fatima Mehnoune, Intertek CAPCIS
- Georgie Bond, Johnson Matthey
- Joe Linkson, Wood Thilsted
- Katie Atkins, Johnson Matthey
- Kevin Lam, bp
- Kishan Ramesh, Plant Integrity Management
- Lukasz Ramowski, Saipem
- Mohammed Muqueeth, Plant Integrity Management
- Muhammad Haris, Brunel University
- Noor Ghadarah, Saipem
- Roberto Alcivar, vHPM UK
- Rochelle Holness, Genesis Energies
- Roisin Harris, Ramboll
- Samuel Brown, Wood PLC
- Tom Robinson, Saith Ltd
- William Adu-Poku, Altrad Babcock
- Yulia Sergeykina, BP
YEP 2024: The Year Ahead
As the participants embark on their journey, YEP 2024 will unfold over the rest of the year with a series of evening lectures and workshops. Oh, and, of course, the eagerly anticipated case study project.
Each session is an opportunity for participants to learn from and interact with experts in the field, developing not just their technical skills but also their professional network, as YEP 2024 covers topics that include:
Date | Topic of Event / Workshop |
Jan 2024 | Fundamentals of Corrosion |
Feb 2024 | Materials / Welding |
Mar 2024 | NDT & Corrosion Monitoring |
Apr 2024 | Coatings & Linings |
May 2024 | Previous Case Study / Delivery of Case Study to the Teams |
Jun 2024 | Corrosion under Insulation / Fire Proofing |
Jul 2024 | Cathodic Protection |
Aug 2024 | Production Chemistry / Chemical Treatments |
Aug 2024 | Annual Corrosion Forum – Energy Transition (Free space for YEP) |
Sep 2024 | Integrity Management / Fitness For Service |
Oct 2024 | Presentation Skills |
Nov 2024 | Presentations of Case Study |
Let the Battle Begin!
Toward the end of the programme, a pivotal moment awaits our participants: the case study presentation. Each event, workshop, and talk is leading to this test of knowledge and chance to showcase innovation, teamwork, and the ability to apply theoretical learning to real-world corrosion challenges.
Having delved deep into the case study, each team will stand before a panel of judges to present their findings and proposed solutions. This culmination of months of hard work, learning and collaboration is a high-stakes affair – the winning team will not only earn the accolade of their peers, but also be rewarded with an all-expenses-paid trip to the AMPP 2025 Conference in Nashville, USA.
YEP 2024 Is an Event for All Corrosion Professionals
While we must strictly limit the number of participants in YEP, this doesn’t mean you can’t follow along! Indeed, we welcome the wider corrosion community to support this invaluable initiative.
Whether you’re a seasoned professional or someone with a budding interest in corrosion management, there’s much to learn and share.
Please, feel free to engage with the Institute of Corrosion and YEP 2024 through our events, as well as our updates on the ICorr blog and social media, and consider how you might contribute to or benefit from ICorr’s initiatives.
Don’t forget, if you’re interested in diving deeper into the topics covered by the YEP or learning more about corrosion management, visit the ICorr website for a wealth of resources, including publications, upcoming events, and membership information.
YEP 2024: A Final Word from Young ICorr
We couldn’t close this article without hearing from the Young ICorr committee. Izabela Gajewska, MICorr, Corrosion & Integrity Engineer at Intertek CAPCIS told us:
“It was great to finally meet the successful YEP 2024 candidates from various engineering companies across the UK in person! They all seemed to be as enthusiastic about the programme as we are!
“We’re delighted to have such a group of participants in this year’s YEP. I can’t wait to get going in earnest, and witness how the programme decreases the gap in knowledge between junior and senior engineers!”
As ever, we would like to extend special thanks to our generous YEP sponsors, AMPP: Association for Materials Protection and Performance, BP and Wood Thilsted (Anthony Setiadi), and also to the speakers at the launch event: ICorr President Stephen Tate, Dr Jane Lomas, and ICorr Corrosion Engineering Division Chair / YEP Committee Dr Danny Burkle.