The cart is empty!
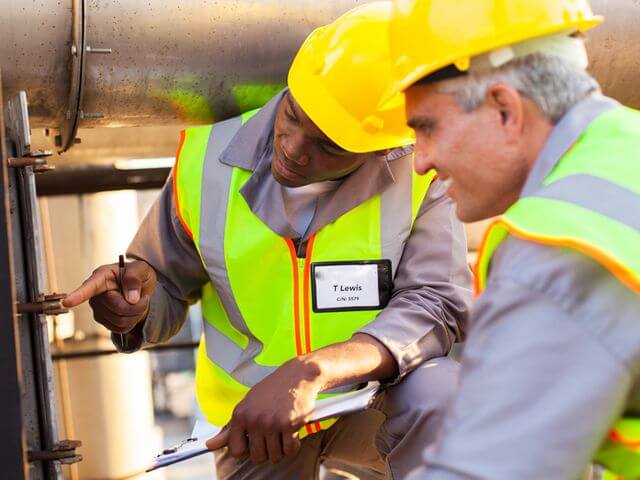
Coating Survey Training – World-Class Course Is a World First
The What and How of the Ground-Breaking Coating Survey Course
Up to now, there has been no coatung survey training available anywhere in the world specific to improving the provision and competency of coating condition surveys. Here at the Institute of Corrosion, we’re happy to say this has changed, with the arrival of a world first – the Coating Survey Course endorsed by ICorr and accredited by Lloyd’s Register and the Royal Society of Chemistry.
Such an important addition to any industry – especially an addition that promises to revolutionise standards and improve health, safety, and cost-effectiveness across multiple industries and their infrastructure – deserves a proper introduction.
Why Is Coating Survey Training Needed?
A coating survey is crucial in the maintenance cycle of structures that benefit from coating systems. When it is properly planned and conducted, a coating condition survey helps to maximise the protection offered by coating systems. This is integral to ensure that safety hazards and operational interruptions are avoided.
Because of the critical nature of a coating survey, it should be conducted only by those who can assess circumstances competently. They will need to draw sound conclusions about the condition of the existing coating and how best to manage coating systems going forward.
Corrodere’s Coating Survey Course satisfies the need to ensure that those conducting coating surveys are suitably qualified and have the knowledge and expertise to carry out costing surveys from basic walk-throughs to the most comprehensive coating condition surveys.
Written by experts with impeccable credentials
The first thing to note about this course is that it is authored by experts in the industry: Brendan Fitzsimmons and Trevor Parry.
Brendan is a Fellow of the Institute of Corrosion, a Chartered Scientist, and has a Master’s degree in Materials Engineering. He is also a NACE Corrosion Specialist, Coating Inspector, Protective Coatings Specialist, and Peer Reviewer.
Trevor is a Professional Member of the Institute of Corrosion, Fellow of the Royal Society of Chemistry, a member of NACE, and an expert on ISO committees.
Between them, Brendan and Trevor have authored many publications and papers within their fields, perhaps most notably Brendan’s authorship of Fitz’s Atlas and Fitz’s Atlas 2.
Development of the Coating Survey Course has also benefitted from the input of major paint manufacturers.
Who should attend this course?
Developed in response to industry needs, if your responsibilities and duties include inspecting or surveying coating systems you will benefit from this formal training and qualification. You’ll benefit from completing this course if you currently perform any of the following roles:
- Coating Surveyors
- Coating Inspectors
- Coating Engineers
- Material Engineers
- Mechanical Engineers
- Insurance Personnel
- Plant Managers
- Asset Integrity Personnel
- Corrosion Engineers
- Asset Owners
- Marine Engineers
- Ship Surveyors
How is the course structured?
The Coatings Course is delivered online by way of 24 hours of training divided into easy-to-manage units. These modules walk you through all the knowledge areas needed, covering:
- Coating Surveys
- Estimation of Percentages
- European Scale of Degree of Rusting of Anticorrosive Paints
- Common Defects
- Marine Fouling
- Dry Film Thickness Surveys
- Passive Fire Protection
- Adhesion Testing
- Holiday Detection
- Sampling Techniques
- Standard Test Methods, Field Tests and Laboratory Analysis
- Photography, Documentation and Reporting
- Paint Testing, Paint Constituents and Paint Chemistry
The online delivery of course materials and training make it easy to complete the course in your own time and a learning pattern that suits you. The course materials will be available to complete over a 12-month period after registration.
The culmination of the training is an online assessment and final exam. The exam is a multiple-choice-style exam with a pass mark of 70%.
Those who successfully complete the course receive the Certificate of Achievement in Coating Surveys accredited by Lloyds’ Register and the Royal Society of Chemistry, endorsed by the Institute of Corrosion.
Do you qualify for this course?
There are two levels of certification available, and which you can achieve depends on your route onto the course.
Level 1:
You don’t need any formal qualifications within the coatings industry to register for Level 1 of the Coating Survey Training Course. You won’t be required to sit the final examination, but will need to successfully complete the online assessments during the course.
Upon successful completion you will receive a Certificate of Completion.
Level 2:
Those who complete Level 2, including passing the exam and online assessment, will be rewarded with full certification and a wallet card valid for four years. To register for this level of qualification you will need to meet one of the following entry criteria:
- Qualified Coatings Inspector (ICorr Level 2, NACE Level 2, SSPC Level 2, FROSIO Level 2)
- Paint Chemist with field experience
- Coating Engineer with field experience
If you are a coating surveyor without formal qualification in coating inspection, you can still take the Level 2 qualification providing you can demonstrate a minimum of five years’ experience as a coating surveyor and provide two employer references.
Why you should take this course
This course, and the qualification it offers, will demonstrate your proficiency in coating surveys. It provides evidence that you conduct and report in-depth coating surveys and that your expertise will:
- Help asset owners accurately plan future works
- Help asset owners accurately target and plan funding for future works
- Assist with paint guarantees, warranties, and disputes
Many industries require the experience and expertise of qualified coating surveyors. These industries include:
- Road
- Rail
- Marine and Offshore
- Nuclear
- Petrochemical
- Oil and Gas
- Construction
At a time when all industries are becoming more highly regulated, with a growing need for asset owners to reduce costs and improve their health and safety, the knowledge that this course provides – including across standards NORSOK 501, ISO 12944, and ISO 4628 – is likely to become invaluable to all those who perform coating surveys and the companies that require them.
This training is currently not available anywhere else in the world. To find out more, you should contact Corrodere. Alternatively, email the admin team at the Institute of Corrosion who will be happy to help.