Corrosion Engineering Division, Latest News
The Institute of Corrosion is running meetings of both the Corrosion Science Division (CSD) and the Corrosion Engineering Division (CED) as part of the Electrochem 2019 conference, which is being held from 26-28 August at Strathclyde University, as follows:
1. The Corrosion Science Symposium will include presentations on the electrochemical aspects of corrosion science and will cover state of the art developments in fundamental corrosion science. Presentations will be given in on Tuesday 27th and Wednesday 28th August. This symposium will include presentation of the U.R. Evans award to the 2019 winner, Tetsuo Shoji.
2. The Corrosion Engineering Day will take place on Wednesday 28th August only. In the morning there will be a series of invited lectures from experienced practitioners on the theme of ‘Electrochemical Corrosion Monitoring in Industrial Applications’. This symposium will include presentation of the Paul McIntyre award to the 2019 winner, Steve Paterson. In the afternoon CED working group meetings will take place (Coatings, Oil and Gas, Nuclear, CP, Corrosion in Concrete). A day rate option is available on the registration page for people attending the CED meeting only. Attendance at the working group meetings only is free of charge. Please email Nick Smart (nick.smart@woodplc.com) to indicate which working group meeting(s) you plan to attend.
Full details about registration etc. are available at https://www.strath.ac.uk/engineering/chemicalprocessengineering/electrochem2019/
Please note that the early bird registration fees expire on June 21st.
We look forward to seeing you there.
Corrosion Engineering Division, Latest News
This year the annual working day of the Corrosion Engineering Division (CED) will take place during the Electrochem 2019 meeting, being held at the University of Strathclyde’s Technology Innovation Centre in Glasgow, Monday 26th – Wednesday 28th August. The CED meeting will be held on the 28th August, and it will be integrated with the Corrosion Science Symposium, organised by the Institute’s Corrosion Science Division.
The programme for the CED part of the meeting will include invited lectures on the theme of ‘Industrial Applications of Electrochemical Corrosion Monitoring’, which will be presented during the morning. Full details of the CED lectures will be published on the conference web site in June 2019, and in the next issue of CM. The lectures will be followed by the presentation of the Paul McIntyre award
to this year’s winner, who will be announced in a few weeks’ time.
In the afternoon there will be an opportunity to join the CED working group meetings. The current working groups are:
n Cathodic protection
n Nuclear
n Coatings
n Oil and gas
n Corrosion in Concrete
The Electrochem 2019 annual meeting is organised by the Electrochemistry, and Electroanalytical and Sensors, Interest Groups of the RSC, and the Society of Chemistry and Industry (SCI). The 2019 meeting will be the 25th anniversary of Electrochem and it will include the 60th Corrosion Science Symposium. Details of the meeting and registration are available at https://www.strath.ac.uk/engineering/chemicalprocessengineering/electrochem2019/.
Attendees are welcome to join any of the parallel sessions that will be running during the meeting.
Corrosion Engineering Division, Latest News
CED Working Day and Symposium on Atmospheric Corrosion in Industrial Applications
The tenth CED Working Day was held on Tuesday 24 April 2018 at The Centre, Birchwood Park, Warrington. Some thirty-nine delegates were welcomed by Chairman, Nick Smart. In addition, there were several exhibition stands, a visit to Wood plc test facilities, and CED Working Group Meetings.
Professor Stuart Lyon (University of Manchester) gave an introductory lecture entitled, ‘Introduction to atmospheric corrosion – mechanisms etc’. Given the large surface areas of materials exposed to the atmosphere, annual losses due to corrosion in the UK are in the order of several hundred million pounds. The atmosphere is one of the most common natural environments to which materials are exposed, however unlike most environments, the atmosphere does not provide constant exposure conditions. Thus, the corrosion rates of similar specimens exposed to the atmosphere have poor reproducibility. The main constituents of the atmosphere are essentially constant, however minor components can affect corrosion rates significantly, for example, the concentration of water vapour can vary over a large range. Three primary sources of air pollution are, volcanic action, vegetation and animal wastes, however sea-spray and dust from the earth also need to be considered. Pollutants are also classified as gaseous, particulate or aqueous (dissolved in rain) and man-made atmospheric pollution includes that from burning fossil fuels, chemical processing, sewage treatment and farming. Stuart went on the explain climate effects, macroclimates and microclimates, and that ISO 9223 provides a classification scheme for ranking pollution in a particular climatic location, which is based on the deposition rates of SO2 and Cl-. Atmospheric corrosion only proceeds when sufficient water is present to solvate ions generated during anodic and cathodic reactions. By definition, at 100% Relative Humidity (RH) condensation occurs. Metal corrosion cannot occur unless there is sufficient liquid water on the surface. The time during which RH exceeds a critical value is defined as the ‘Time of Wetness’ (TOW) and ISO 9223 also includes a scheme for ranking a particular climate in terms of TOW (hrs/year). The standard also provides a classification scheme for the ‘Corrosivity’ of an environment, based on the expected annual corrosion rate over 1 year. Finally, specific mechanisms relating to the atmospheric corrosion of iron and zinc were outlined.
Richard Bewell (Engineering Manager, BAM Nuttall) gave a presentation on, ‘Atmospheric corrosion prevention in the windpower industry’. The ‘Blyth Demonstrator Project’ (located about 5.6 km off the North-East coast of England at a water depth of about 38m) has five 8.3 MW turbines, capable of supplying power to 34,000 homes, with a design life of 26 years, and commercial operations commenced in October 2017. The design is essentially a monopole with a heavy reinforced concrete base approx. 30m diameter x 1.1m deep and using over 1,800m3 of concrete with over 500 tonnes of steel reinforcement per foundation. The towers comprised steel shafts, 60m high x 7.5m diameter with a wall thickness of 70mm. For protection in the splash zone and for atmospheric exposure, Norsok C5M specification was applied.
Cristano Padovani (Wood plc) addressed, ‘Modelling the corrosion behaviour of intermediate level radioactive waste (ILW) containers during prolonged exposure to atmospheric conditions’. The stages involved in waste management are, immobilise and containerise, interim storage, transport to an underground geological disposal facility (GDF) and utilise man-made and natural barriers to prevent/minimise release. The atmospheric corrosion of the stainless steel containers, used for medium- and long-term storage , is induced by chloride-containing aerosols, generated by hygroscopic chloride salts on surfaces. Temperature and relative humidity (RH) determine electrolyte characteristics (e.g. concentration) and hence, corrosivity. The factors investigated were, environmental and corrosion monitoring, pit initiation, and mechanistic and SCC initiation studies. Temperature and humidity fluctuate daily and have seasonal variation for above-ground facilities, but are typically more stable underground. It was found that MgCl2 and CaCl2 were inherently much more corrosive than NaCl (especially with regard to SCC), and that high enough RH can lead to dilution of corrosive ions and prevent initiation or cessation, and that SCC initiation was severely inhibited by induced surface compressive stresses. Mechanistic studies in bulk solution indicated that, under polarization, follow kinetics such as, D = A tn, where D=pit depth, A= a constant, t= time and n is an exponent. Furthermore, it was found that SCC propagated very fast after an ‘apparent’ incubation period. A Parametric model – Atmospheric Corrosion of stainless Steel in Stores (ACSIS) was developed, comprising three basic modules, environmental (is the surface wet ?), corrosion initiation (does corrosion initiate ?), and corrosion propation (if so, how much damage results ?). The Laycock-White-Krouse (LWK) mechanistic model was described and used to relate pit depth as a function of time for high RH’s and different chloride surface concentrations.
‘Assessment of corrosion under insulation and engineered composite wraps using pulsed Eddy-current techniques’ was described by Bill Brown (TRAC Oil and Gas Ltd). This presentation touched on the NDT aspect of atmospheric corrosion. Corrosion under insulation (CUI) is possibly the greatest unresolved asset integrity problem in industry. Current methods for measuring wall thickness under insulation, without removing it, all have severe limitations. In total, there are three eddy current devices available for this. However, TRAC evaluated the recently-introduced ‘Lyft’ – a high-performance reinvented pulsed eddy current (PEC) technique) and also Maxwell produced PEC equipment. Although radiography may also be used, it is generally limited to 6 in. diameter pipework, and computer-aided tomography has also been used. A combined PEC and digital radiography technique was developed by Shell in the early 1990’s. A simplified working model of PEC was described and that the concepts of footprint and average area of a probe are key to understanding what a PEC can and cannot detect. The footprint is affected by the size of the probe and the distance from the component or structure being examined from the probe. The footprint is of utmost importance, as it is the decisive factor in determining the dimension of the inspection grid, edge effect and the smallest volume or defect. Nine case histories using this technique were then given.
Professor Geraint Williams (Swansea University) addressed, ‘Preventing corrosion of galvanized steel in the non-chromate age’. The EU has set a ‘sunset’ date of 2019 for the replacement of hexavalent chromium corrosion inhibitor. The problem of how the performance of new inhibitor pigments could be quantified under atmospheric corrosion was raised. Methods included, external weathering, accelerated salt spray and EIS (immersion in corrosive solutions). Assessment of organic coatings carried out at Swansea University included the use of a Scanning Kelvin Probe (SKP). This involves the use of a reference electrode in a test chamber, without physical contact – i.e. not in a ‘bulk’ electrolyte, providing a ‘spatial map’ of corrosion potentials. Ion exchange materials are promising chromium-free anti-corrosion pigments, in which ‘smart release’ inhibitors are only released whenever a corrosive environment is encountered. ‘Hydrotalcite’ is a layered double hydroxide of general formula Mg6Al2CO3(OH)16.4H2O. The carbonate anions that lie between the structured layers are weakly bound giving the material anion exchange capabilities. Inhibition arises by the sequestered aggressive Cl- ions being exchanged for less aggressive ions. The action of this ion exchange mechanism was studied on hot-dip galvanized steel by SKP. The use of benzothiazole inhibitors as a non-chromate alternative was also mentioned. The mechanism is to stifle the underfilm oxygen reduction reaction. Finally, the next generation of Zn-MgAl alloys for galvanizing was introduced. These are very heterogeneous, comprising a three phase material.
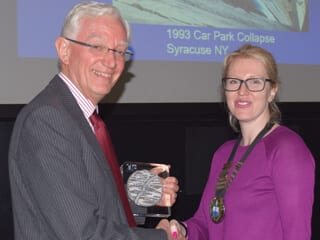
John Broomfield receiving the Paul McIntyre Award from Sarah Vasey.
The second annual Paul McIntyre Award was presented at the meeting to John Broomfield, by Sarah Vasey, President of The Institute of Corrosion. This Award is presented to a senior corrosion engineer, over the age of 30, who as well as being a leading practitioner in his field, has advanced European collaboration and international standards development (in keeping with Paul’s area of interest). Recipients must have established an international reputation in the field of corrosion engineering. John had originally a background in spectroscopy and applied these studies to monolayers on steel surfaces. Later, he worked on problems with PWR reactors in the UK, later transferring to Taylor Woodrow and subsequently carried out work on concrete pre-stressed pressure vessels. Some very interesting slides on the pioneering work he was involved with were shown.
At the close, Nick Smart thanked the speakers, the delegates for attending the working day, Wood plc staff for the conducted tours of facilities, and the exhibitors, for a successful and enjoyable event.
Editor’s note: Text copyright: David Nuttall, released under CC-BY-NC.
Corrosion Engineering Division, Latest News
A collection of recently edited and up-dated technical guidance documents from the CED Coatings group has recently been published in the member’s area of the Institute of Corrosion website. Each document includes extensive referencing to relevant standards and other sources of information. A summary of these documents is presented here. Please note that to access the members area you will need to register or re-register by filling in the on-line form at https://www.icorr.org/members-area.
CED/CT01 Inspection and testing – Surface preparation and organic coating-related inspections 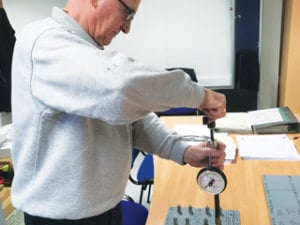
This document discusses the purpose of inspection, the specific areas that a paint inspector might check, the relevant standards and methodologies, the reasons behind the various requirements, and the equipment used. Subject areas include: pre-coating (visual inspection, surface profile checks, extraction of soluble salts, surface cleanliness checks, ambient monitoring) and post-coating (coating thickness checks, adhesion testing, holiday detection). The focus is on those methods which are considered the best, or most commonly used, but an emerging test for post-coating corrosion protection monitoring, namely electrochemical noise measurement, is included as an Appendix.
CED/CT02 Surface Preparation Methods
CT2 provides an insight into the types of preparation methods that are available, the equipment used and how this is related to industry standards. The three common surface preparation methods, i.e. abrasive blasting, hand and power tool, and water jetting, are discussed, with particular attention given to water jetting, which is less well-known than the others. The advantages and disadvantages of each method are also highlighted.
CED/CT03 Organic coating application methods 
This document provides an insight into the available coating application methods and the equipment used. The various application methods described are: brush application, roller application, spray application (including air-, airless-, HPLV-spraying, auto-deposition, and rotating discs and bells), dip coating and flow coating.
CED/CT04 Paint: a definition and generic organic coating types
This document provides an insight into the generic organic coating types that are available, highlighting the types and compositions of the coatings. It begins with a brief definition of what comprises a paint system and an outline of why, when and where anticorrosive paint is used. It provides definitions of resins (e.g. alkyd, epoxy, polyurethane/acrylic urethane, vinyl esters, and silicone-based resin systems), pigments and extenders, solvents, additives (driers, thixotropes, UV absorbers, de-foamers, wetting agents). Some examples of complete paint systems (primer, stripe coat, intermediate coat or coats, and finish coat) are also given.
CED/CT05 TMS: Thermal metal spray 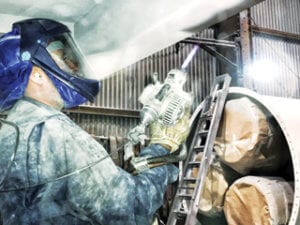
CT05 defines the technique of thermal metal spraying, placing it in context and noting the relevant surface preparation standards. The methodology is then described in detail, including flame spray and arc spray. Properties such as abrasion resistance, galvanic protection, longevity and the permeability of thermal metal spray to water are discussed. This is followed by a section covering the appropriate uses of TMS, as well as noting where it is NOT recommended.
CED/CT06 On-site and off-site application of intumescent fire and corrosion protection coatings for steel structures
This document provides a definition of intumescent coatings and highlights the key issues concerning specification and use of the types of coating appropriate in particular contexts. It also covers, certification, development and handling of the coating, and preparation of the substrate surface, together with the advantages and disadvantages of off-site or on-site application.
An emphasis on the corrosion protection aspects of the intumescent system, and information on the types of system that will be effective in this context, are included in the sub-section on environment. A large number of sources of further information are included towards the end.
Corrosion Engineering Division, Latest News
The 2018 CED working day meeting will be held at the Birchwood Park Conference Centre, Warrington, on Tuesday 24 April 2018 on the subject of ‘Atmospheric Corrosion in Industrial Applications’. An information and registration leaflet is included in this issue of Corrosion Management. Exhibition space will be available for hire.
The Coatings Working group has prepared a series of guidance documents on the following topics:
• Inspection and testing of coatings
• Organic coating application methods
• Surface Preparation methods for coating application
• Paint: a definition and generic organic coating types
• Thermal metal spray coatings
• On-site and off-site application of intumescent fire and
corrosion protection coatings for steel structures
These documents are now available through the members’ area of the Institute’s web site. If you have any comments on them please send them to admin@icorr.org
Corrosion Engineering Division, Latest News
A CED Working day and Symposium on Corrosion Engineering and Concrete was held on Thursday, 27 April at IMechE Engineering Training Centre, Sheffield. The meeting was sponsored by the Institute of Concrete Technology. Some sixty delegates were welcomed by the Chair of CED, Nick Smart (Amec Foster Wheeler), who introduced the Division for the benefit of those who were not members and also outlined the programme for the day. This was followed by an ‘Introduction to the Institute of Concrete Technology’, given by the President, Raman Mangabhai.
Chris Atkins (Mott MacDonald) addressed, ‘The trouble with concrete’. He outlined the origin of the problems with concrete caused by shrinkage and the means of overcoming its poor compressive strength by inserting reinforcement. Settlement cracking was capable of giving rise to 2 mm wide cracks, which could penetrate right up to the rebar. Other aspects of steel corrosion in concrete were then discussed including the electrochemical mechanisms of corrosion, forms of chemical attack that can occur during use, repairing chloride-induced corrosion, cathodic protection, and decisions to repair (covered by BS EN 1504), with BS EN ISO 12696 providing further guidance on conformity.
Next, David Simmons (BAM Nuttall) outlined, ‘The use of coatings to manage corrosion in concrete’. “Getting it right first time” is a phrase that is often used in construction. This applies equally to reinforced concrete if it is to be durable and provide the service life as specified by the end-user. The problem with reinforced concrete is that while engineers fully appreciate the importance of including the reinforcing steel, not much consideration is given to the low-cost, easy-to-use, void filling material that surrounds it. In effect, the concrete cover should be regarded as a protective coating, and must be properly specified, batched and used, which can only be achieved by proper exchange of information between the designer, user, and producer of the concrete.
‘Impressed current cathodic prevention of steel in concrete’ was the subject of the lecture by Hugue Bois (SAPIEM SA, France). Theoretically, steel in concrete should not experience corrosion. The concrete pH is around 13 and this alkaline environment stabilises the iron oxide or hydroxide film, thereby passivating the embedded steel. The concrete layer also presents a low permeability barrier vs. external aggressive species, e.g. chloride ions or carbon dioxide. However, in some cases, ingress of these species reduces the pH to 8 or 9, thus impairing the passive film. Examples of field experience were given, including reinforced concrete steel piles, the use of Mn/MnO2 reference electrodes, and the importance of identifying the various at-risk zones, for example of a sea wall, viz. immersed wall, buried wall, atmospheric, splash and tidal zones.
The final presentation entitled, ‘Latest understanding of the corrosion of Magnox, aluminium and uranium metal wastes in cement’ was given by Hugh Godfrey (National Nuclear Laboratory). An overview of the work that has been carried out in the nuclear industry on the corrosion of Magnox (magnesium/aluminium alloy), uranium and aluminium wastes encapsulated in cements was presented under the following headings: the origin of the waste; how the waste is encapsulated in cement; how the corrosion rates were measured and a comparison of the corrosion behaviour of the three metals. Uranium has the simplest corrosion behaviour – an initial incubation period followed by continuous corrosion and a steady rate. Magnox behaviour is more complex, with the corrosion rate gradually decreasing to a fixed long-term rate. This contrasts with the corrosion rate for aluminium which continually decreases without appearing to reach a steady rate.
The technical talks from this meeting are available (in pdf form) on the members area of the ICorr website.
After the presentations, the delegates were afforded the opportunity of visiting the concrete and corrosion laboratories at Sheffield Hallam University, and to participate in CED Working Group Meetings. The concrete and CP, nuclear and coatings work groups all had successful sessions.