Fellows Corner
This series of articles is intended to highlight industry-wide engineering experience, guidance and focused advice to practising technologists. It is written by ICorr Fellows who have made significant contributions to the field of corrosion management.
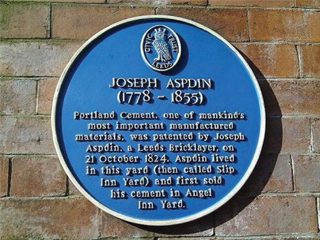
1824 and All That – A Celebration of The Bicentenaries of CP and PC
Paul Lambert, Head of Materials and Corrosion Technology at Mottmac
On January 22, 1824, the Philosophical Transactions of the Royal Society in London received a paper entitled ‘On the corrosion of copper sheeting by sea water, and on methods of preventing this effect, and on their application to ships of war and other ships’. The author was Sir Humphry Davy, and it describes a study with his colleague Michael Faraday into what we now know as cathodic protection, which celebrates its 200-year anniversary in 2024. It was many years later before the true value of cathodic protection was recognised for the protection of buried and submerged steel structures. It was championed by the formation of the Texas-based Mid-Continent Cathodic Protection Association in 1938, which by 1943 had evolved into the National Association of Corrosion Engineers (now AMPP) in the USA.
But that is only half the tale. On October 21st 1824, a bricklayer in Leeds patented a new formulation of hydraulic binder for mortar and concrete which he called Portland cement due to its similarity to the popular structural stone, especially when mixed with beach sand. Portland cement eventually dominated the manufacture of all concrete worldwide.
200 years on, the long-term durability limitations of Portland cement concrete are regularly made good by the application of cathodic protection, making 2024 a very important year for those involved in reinforced concrete and its remediation.
Happy 200th birthday to Cathodic Protection and Portland Cement.
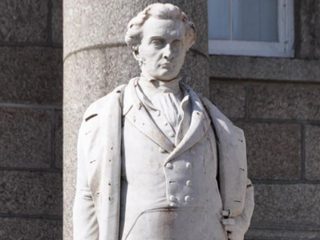
Sir Humphry Davy of Penzance (1778 – 1829).
Photo courtesy of Pen with Local History Group
https://corrosion-doctors.org/Corrosion-History/CP-History.htm
Fellows Corner
Douglas Mills undertook PhD research on anti-corrosive coatings at Cambridge University and has worked on and off in this field since. After spells at the BNF Metals Technology Centre and the Nuclear Power Company, in recent times he has worked in academia, and apart from teaching materials, he has continued to conduct and supervise research in the field of electrochemical methods for application to coatings, particularly studying and developing the electrochemical noise method. He was for fifteen years the Technical Secretary of the Institute of Corrosion and is also involved in standards development.
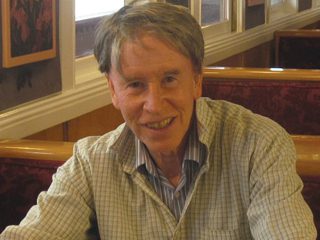
Douglas Now Lays Down His Story:
I have had an interest in archaeological corrosion ever since I did work in this area many years ago at the British Non-Ferrous (BNF) Metals Technology Centre in Wantage. This was “An examination of artefacts brought up from the seabed after 262 years”. In 1707 several ships of the line from a fleet of twenty one under the command of Sir Cloudesley Shovell, hit the rocks of the Scilly Isles during a fierce storm and sank. This included the flagship HMS Association. In 1969 a team of divers under the overall control of Roland Morris recovered many artefacts. The BNF was given a Royal Society grant to examine these, and it fell to me to carry out much of the work. Conducting chemical analysis as well as metallographic studies, enabled us to find out (and comment on) the type of corrosion, the nature of the corrosion product and the extent of corrosion. Also, the composition and metallurgical structure of the metals/alloys were compared with similar alloys used today. The items included, brass dividers a bronze cutlass handle lead musket balls and silver pieces of eight as well as lead pipe, pewter platters, a copper spike, and (bronze) ship’s bells. (There was also bronze cannon although my work did not extend to examination of these).
I did this work under the direction of Hector Campbell. one time editor of the British Corrosion Journal, with whom the 70page report was written.
Much later I became involved with the Maritime Museum in Gdansk.
I was able to pass this report over to Kasia (their corrosion expert). The museum had bits from two ships (“Copper Ship” and “Solen”) which sank in the Baltic a similar length of time ago). On the metallurgical side, the composition of many of the alloys used was surprisingly close to what might be used today and many were also reasonably pure for example.
• Lead musket balls: afforded an interesting comparison with musket balls from the Swedish warship Wasa, visible in its entirety in museum in Stockholm, which sank some 60 years earlier in the Harbour there. This was possible because the original size and weight of musket balls was known and hence (assuming linear) we could work out the corrosion rate and compare them. What was found was that sea water conditions in the Scilly Isles (clean and turbulent) afforded a less aggressive environment than Stockholm harbour (polluted) led to about half the rate of corrosion.
• Brass dividers: These had undergone hardly any corrosion; the points made of iron had rusted away completely (bimetallic corrosion), and maybe they provided galvanic protection in the early stages. But it was the fact that the brass was single phase and contained some arsenic (a useful inhibitor of dezincification) that probably saved the dividers.
• Bells: one from HMS Romney (probably!) and one from HMS Association. These, despite similar composition (two phase: one copper rich and one tin rich), had corroded in quite different ways with one phase being attacked in one bell and the other phase in the other. Interesting polarisation / potentiostatic work done in the lab revealed that the two bells had probably been subjected to different environmental conditions – half of one bell having been buried in mud while the other bell was freely exposed to sea water.
• Pieces of eight: The interest here was in developing a more efficient cleaning method compared with the normal one which was lengthy and removed significant amount of silver, achieved partly by using an electrochemical method.
Protective Coatings and Electrochemical
Assessment Methods
This kind of research i.e., towards understanding long term corrosion and its prevention, has relevance today to both the storage of nuclear waste and conservation. The afore mentioned Kasia and I have collaborated in developing an electrochemical assessment method for corrosion protective coatings. The specific interest here is in how do you keep things in the museum environment from continuing to corrode? But there are also ancient artefacts outside like statues. The most common approach is application of
thin, invisible organic coatings. Getting the right coating is quite a challenge as the appearance must not to be altered. The Museum at Gdansk had a bell and bowls which had been protected by these thin transparent coatings. How do you assess such coatings? One approach is to use Electrochemical measurement techniques like DC resistance or Electrochemical Noise. Some recent work done in Northampton University tested four such coatings and concluded that Paraloid (conservation grade acrylic lacquer) coatings were the best. But only if you applied two thin (typically
10-20mm) coats.
Other Discoveries
Moving back to the discovery phase on a more local level i.e., people discovering archaeological items in the earth, the father of a friend found a large cannon ball in the south of England which I was invited to have a look at. It had a thickish layer on the outside and this interestingly was not iron based but contained large amounts of lead.
The inside of the cannon ball was very likely cast iron, based on its hardness and the calculation of density (between 6.8 gm/cc and 7.5 gm/cc. Cast Iron has a density of 7.3 gm/cc.)
• Outer lead casing – why was the outer lead put on? Was it a corrosion protective layer? What was the environment that caused the more noble lead to corrode so extensively? (apparently faster than the musket balls in the sea, as all the lead exterior was destroyed). Was it pure lead or some lead alloy which was more corrodible? Maybe the smoother lead surface assisted in the firing (that seems very plausible). One possibility is that it was never used in anger but was lost while being transported. Such cannon balls were used on big ships (even as early as the Mary Rose, Henry VIII’s flagship, from the early 16tH century) So it could have been travelling between the Arsenal and Portsmouth when it “fell off a cart!”
In summary lots of questions raised and only speculative answers! This is the fascination with any investigation of archaeological corrosion. It leaves plenty of room for the Imagination!
References:
1. H. S. Campbell and D. J. Mills Marine Treasure Trove – A Metallurgical Examination Metallurgist & Materials Technologist October 551 (1977).
2. Mills, D.J.; Schaefer, K.; Wityk, T. In-Situ Evaluation of the Protectivity of Coatings Applied to Metal Cultural Artefacts using Non-Destructive Electrochemical Measurements. Corros. Mater. Degrad. 2021, 2, 120–132. https://doi.org/10.3390/cmd2010007.
3. Schaefer, K.; Mills, D.J. The application of organic coatings in conservation of archaeological objects excavated from the sea. Progress in Organic Coatings Volume 102, Part A, January 2017, Pages 99-106.
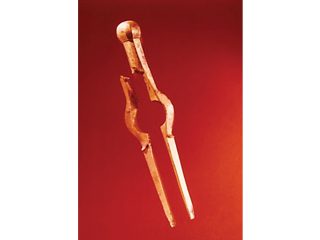
Brass dividers
(almost no corrosion).
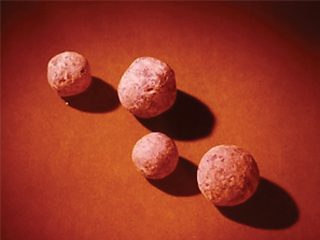
Lead musket balls with varying rates of corrosion according to submersion condition.
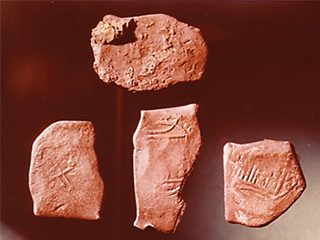
Pieces of eight after electrochemical cleaning.
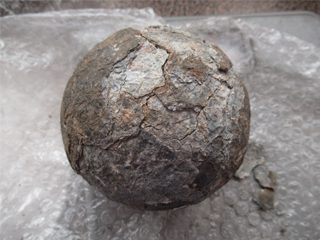
Cannon Ball (weight 4 kG (9 lbs) Diameter 11cm (density 6.8-7.5) with Corrosion Product about 1-2 mm thick.
Fellows Corner
This series of articles is intended to highlight industry-wide engineering experience, guidance, and focussed advice to practising technologists. It is written by ICorr Fellows who have made significant contributions to the field of corrosion management. This issue features The Corrosion Resistant Properties of novel cements, concretes, and reinforcement by John Broomfield of Corrosion Engineering Solutions Ltd.
The Corrosion Resistant Properties of Novel Cements, Concretes, and Reinforcement
We use more concrete than any other material other than water. However, each tonne of concrete has a significant carbon footprint and the technical press is full of articles on new ways of reducing that carbon footprint by modifying its constituents. There are many ways of doing this, most of which involve changes in the internal chemistry of the finished product.
Concrete is made from cement, fine and coarse aggregates, and water. To this may be added other materials or admixtures, such as superplasticisers to increase workability during placement on site, set retarders or accelerants for hot or cold climate work, or even corrosion inhibitors for aggressive conditions where the steel reinforcement needs extra protection. The cement itself can be Portland cement or, more commonly these days, a blend of Portland cement and other cementitious materials such as pulverised fuel ash (pfa), ground granulated blast furnace slag, microsilica or metakaolin. The perceptive reader will note that some of these materials are going through their own changes and availability issues in response to the need to reduce carbon emissions. There are reports in the press of applications to mine deposits of pfa from ash pits as the supply of material direct from operating coal fires plants is diminishing.
The methods of achieving the required performance and durability of blended cements are covered in UK and European standards BS EN 206 parts 1 and 2, and BS 8500 parts 1 and 2. The latter gives tables of exposure conditions along with the necessary mix design, and minimum cover requirements to achieve a required minimum design life for a given exposure condition. There is also BS EN 197-1:2011 Cement Composition, specifications and conformity criteria for common cements, which gives the specifications of 27 distinct common cements, 7 sulphate resisting common cements as well as 3 distinct low early strength blast furnace cements and 2 sulphate resisting low early strength blast furnace cements and their constituents.
Portland cement based concretes provide corrosion protection to reinforcement in two ways, as a semi permeable coating and as a corrosion inhibitor. Concrete is permeable to water and oxygen. The reason that reinforcing steel embedded in concrete does not corrode is that the pores in concrete contain an excess of calcium hydroxide and other hydroxides, maintaining a pH of 12 to 14 [1]. The upper level is carefully controlled because some aggregates are at risk of alkali aggregate reaction which leads to the creation of an expansive gel which will damage the concrete.
However, in order to prevent corrosion, the pH must stay above 11, which is the threshold for corrosion. There are two mechanisms for inducing corrosion in reinforced concrete structures without physical damage to the concrete cover to the steel. One is carbonation; the process where atmospheric carbon dioxide reacts with pore water to form carbonic acid and neutralise the excess calcium hydroxide in the pores. This leads to a carbonation front which progresses through the cover. Once it reaches the steel, the pH drops below 11 and corrosion can occur. The other process is chloride attack. The chloride ions in solution (usually from sea water or deicing salts) diffuse through the concrete cover to the steel. Once the concentration at the surface exceeds a threshold level, the passive layer on the steel breaks down and corrosion ensues.
Over the years since the 1970s, much work has been done to understand these mechanisms in Portland cement based concretes. We have a simple equation to estimate the rate of carbonation of the form, x = kt½ here x is the carbonation depth, t is time and k is a constant which can be measured or estimated on a structure by structure and microclimate basis.
For chloride ingress the equation is more complicated, as Fick’s second law of diffusion applies and the threshold concentration must be estimated. However, there is much guidance now available on the parameters for predicting chloride diffusion rates into Portland cement and blended concretes [1].
However, this type of guidance has not been developed for non-Portland cement based concretes. While civil engineers have great expertise and applicable useful standards and test methods for determining the physical characteristics of new concrete, when it comes to the more chemically based properties, such as corrosion resistance and durability, there is far less guidance and often less in-house or externally available expertise.
When blended cements were used with high levels of alterative cementitious materials, there was concern that the alkali reserves would be depleted, increasing the rate of carbonation and possibly also chloride diffusion. However, since these blends were less porous than ordinary Portland cement concrete, testing and experience soon showed that there was no loss of durability. In fact, durability increased. However, there are new alternatives to Portland cement itself such as alkali activated cementitious materials (AACM). Because AACM has no Portland cement, it is outside EN 197-1, EN 206 and BS 8500. To prove a candidate new AACM is durable, EN 197-2 and EN 206 permit users to demonstrate equivalence and show the material has the required structural and durability properties.
As might be expected, AACM initially has a pH that is higher than conventional Portland cement and concrete (14 or so), but the alkali reacts during the setting process. There is therefore a concern that this cement free, lower carbon concrete does not have the same reserve of solid Ca(OH)2 to buffer carbonation, so it would carbonate faster than an equivalent convention Portland or blended cement concrete mix.
Recent testing suggests something else is going on. It seems the initial carbonation rate is higher, but a pore blocking process then seems to start, blocking CO2 ingress, and the rate of carbonation slows right down. The steel therefore remains in a dense, high pH matrix. However, this good performance may be product and mix specific. This suggests that the carbonation rate equation above is not applicable to AACM concretes, or that the constant k may be harder to determine over the long term.
RILEM (The International Union of Laboratories and Experts in Construction Materials, Systems and Structures) have produced a State of the Art Report on Alkali Activated Materials [2], which is a comprehensive review of these materials, their formulations, chemistry and performance. It discusses the durability of the material and of structures made with it, as well as the testing of the materials during production and casting and also field testing of existing structures. It found considerable variability in performance and test results, particularly with regard to transport properties, corrosion performance and durability. The lack of specifically applicable performance standards was a concern.
Another major contribution to the field is “The Field Performance of Geopolymer Concrete Structures report” by the Cooperative Research Centre (CRC) for Low Carbon Living Ltd in Australia [3]. The report describes in-situ testing and core sampling of geopolymer (alkali activated) concrete at four sites across Australia and long-term performance monitoring of two geopolymer concrete structures. The field test results found extremely variable resistance to carbonation and to chloride ingress and the authors stated that this confirms the necessity of developing performance based specifications for Geopolymer concretes
Like the RILEM report, the CRC report concludes that suitable testing methods are required to assess the performance of concrete in order to assist engineers to specify Geopolymer concrete conservatively and confidently, particularly in more aggressive environments.
Unlike the physical testing of concrete for properties such as cube strength, the durability testing is more complex. We need to understand the chemistry of the material and how it changes over long periods of time if it is to be used with conventional steel reinforcement. We already have examples of unsuitable use of specialised concretes most recently reinforced autoclaved aerated concrete leading to failures and expensive repairs or rebuilding.
The obvious corrosion related tests for novel concretes are for the alkali reserves in concrete to be measured and its resistance to chloride and carbonation. There are tests for these under BS EN 205 and BS EN 1504. However, we know that these properties can be very variable for alkali activated materials and change over the long term so a full understanding of the chemistry and its changes over time are required before we can develop prescriptive tests.
As one of the concluding statements of the RILEM Report states. “These issues are by no means limited to the area of AAMs – these points are relevant across many areas of non-traditional cement and concrete development and commercialisation”. The replacement of Ordinary Portland cement based concretes with new materials expected to perform and be durable for many decades is a challenge for engineers in the construction industry.
Of course, one solution to the corrosion risks of reinforced concrete is to use alternative reinforcement. There have been corrosion resistant reinforcement materials available for many decades. For ferrous materials these include galvanised steel reinforcement, fusion bonded epoxy coated reinforcement, a range of stainless steels and low alloy steels. These are reviewed in the AMPP/NACE State of the Art Report on Corrosion Resistant Reinforcement [4]. Some of the ferrous materials can on the whole be treated by conventional testing both in the laboratory and on site, the coated ferrous reinforcing bars, less so.
However, there is now a range of non-metallic reinforcements, including glass and carbon fibre reinforced polymers and more recently basalt. These are polymers with fibre reinforcement. While we can detect ferrous reinforcement in a structure with electro-magnetic based cover meters, we have no simple way of detecting these materials. Will we be using more ground penetrating radar to detect non-metallic reinforcement? Has any work been done on detecting these alternative reinforcement materials once they are cast into a structure?
Do we understand the deterioration mechanism for these products? The failures of fusion bonded epoxy coated reinforcing bars in Florida were partly due to the softening and debonding of the epoxy in a saturated environment, particularly where the coating was stressed on the outer radius of bends. These failures happened over a few years. Could similar degradation of polymer-based reinforcement occur in concrete over the decades? If so, how will we detect it? We have NDT techniques such as reference electrodes, resistivity meters and linear polarisation to provide information of the corrosion condition of ferrous reinforcement. We have no equivalent tests for polymer-based reinforcement. If we start putting alternative reinforcement materials in alternative concretes will we understand their interactions in the short and long term?
It is obviously important to innovate to reduce the carbon footprint of the construction industry and improve the durability of the built environment. However, we need a deep understanding of the materials we are using as well as suitable standards and test methods and equipment to ensure the products we use can perform in the environment they are exposed to and can be assessed and maintained throughout their lives which will last for many decades. Corrosion engineers have a major role to play in the understanding, testing and developing performance-based specifications and tests for the new wave of low carbon and corrosion resistant materials in the construction industry.
The author would like to acknowledge the help of Professor Peter Robery for his advice on alkali activated concretes and the RILEM and CRC reports.
References
1. Broomfield, J.P. Corrosion of Steel in Concrete, 3rd Ed. Publ. CRC Press London, 2023.
2. John L. Provis, Jannie S.J. van Deventer Editors, Alkali Activated Materials State-of-the-Art Report, RILEM TC 224-AAM Publ. Spinger, 2014.
3. Stephen Foster et al. The Field Performance of Geopolymer Concrete Structures report RP 1020 by Cooperative Research Centre (CRC) for Low Carbon Living Ltd in Australia, 2018.
4. NACE Publication 21429-2018-SG – State of the Art Report on Corrosion-Resistant Reinforcement Publ. AMPP, Houston TX.
CAPTIONS:
Hilti Ferroscan, a scanning cover meter, can identify the size and depth of steel reinforcement. New techniques will need to be developed for detecting and locating non ferrous reinforcement.
Fellows Corner
This series of articles is intended to highlight industry-wide engineering experience, guidance, and focussed advice to practising technologists. It is written by ICorr Fellows who have made significant contributions to the field of corrosion management. This issue features an introduction to intumescent coatings, by Brian Goldie.
Passive Fire Protection – Intumescent coatings
Today most buildings and structures have some degree of fire protection in order to protect lives, delay possible structural collapse allowing for evacuation, provide areas of temporary refuge in the case of fire, and ensure the integrity of escape routes, by preventing or delaying the escalation of a fire and protecting high-value assets.
There are two basic types of fire protection: active and passive. Active fire protection includes alarms and detection systems, sprinklers and water deluge systems, firefighting equipment and foam and powder extinguishers. Passive fire protection involves materials such as concrete, mineral fibre boards, vermiculite, cements, and intumescent coatings. This article will describe how intumescent coatings can achieve passive fire protection in many structure types including offshore platforms or floating facilities, such as FPSOs and FLNGs, and commercial buildings.
Intumescent coatings have been used to protect the steelwork in buildings and other structures from fire for approximately 40 years. These coatings work by swelling up in the event of fire and physically creating a barrier between the steel and the fire for as much as 4 hours in some cases. Steel begins to lose its structural strength at about 400 C, and these coatings can delay the time it takes to reach this temperature (Figure 1). Intumescents are often referred to as thin- film or thick-film coatings.
Thin-film intumescents are typically single component solvent or waterbased products, and have dry film thicknesses (DFTs) of less than 5 millimetres. In the last few years new technologies, such as multi-component methacrylate, or “hybrid” products, have been brought to the market, offering specific advantages over the traditional products.
Thick-film coatings are typically solvent-free, epoxy-based with DFTs of up to 25 millimetres.
The acceptance and use of intumescent coatings increased dramatically in Europe in the 1980s as the major oil companies learned of their ability to protect structural steel from the extreme heat caused by hydrocarbon fires, including jet fires caused by leaking hydrocarbons. Also, exposed steel was used more prevalently in the design of commercial structures and high-rise buildings, increasing the use of thin-film intumescents, which looked more like conventional paint and therefore could meet the aesthetic requirements of architects.
How Do Intumescent Coatings Work?
Intumescent coatings react to fire by expanding to form a carbon “char” with low thermal conductivity, which essentially forms an insulating layer reducing the rate of heat transfer and extending the time necessary to reach the critical failure temperature of the underlying steel.
It’s a complex chemistry incorporating the organic binder resin (coating) — typically an epoxy (hydrocarbon fire) or acrylic (cellulosic fire), and an acid catalyst, for example ammonium polyphosphate, which decomposes to yield a mineral acid. This acid reacts with a carbonific source, for example, pentaerythritol, to produce a carbon char. A spumific (foam-producing) agent, such as melamine, reacts with the acid source and decomposes, evolving into an inert gas which then expands the char. These are the basic reactions taking place, although more complex interactions also occur. Reinforcing mesh can be used to support the formed char.
Cellulosic vs. Hydrocarbon Fires
A cellulosic fire has a fuel source composed mainly of cellulose — for example, wood, cardboard, or paper. Hydrocarbon fires are fuelled by hydrocarbon compounds and ignite and grow exceedingly fast, achieving high temperature almost immediately after ignition, greater than 1,000C in less than five minutes (Figure 2). Cellulosic fires are slower to reach maximum temperature but may eventually reach or surpass the temperature of a hydrocarbon fire.
A hydrocarbon pool fire is defined as a turbulent diffusion fire burning above a horizontal pool of vapourising hydrocarbon fuel, where the fuel has zero or low initial momentum. A jet fire is a turbulent diffusion fire resulting from the combustion of a fuel continuously released with high pressure.
Testing Intumescent Coatings
No two fires are the same. The conditions depend on the type and quantity of fuel, the availability of oxygen and ambient conditions. For reproducible product testing. “standardised” fires have been defined, for example, BS 476 (parts 20 and 21) “Fire tests on building materials and structures” and EN 13381 (part 8), “Test methods for determining the contribution to the fire resistance of structural members” describe how intumescent coatings are tested with cellulosic fire exposure. Performance depends on coating thicknesses, the types of steel section, I-section, hollow section, and the section orientation, i.e., beam or column.
Other test standards include UL 1709, “Rapid Rise Fire Tests of Protection Materials for Structural Steel” for hydrocarbon fire exposure, ISO 22899-1, “Determination of the resistance to jet fires of passive fire protection materials”. Different standards apply to marine applications. It is not possible to test every variation, so the test results are analysed to produce an assessment of performance.
Ensuring Durability
To protect steel in a fire, a coating must be resistant to the environment and be intact at the time of the fire. Poor durability can lead to ineffective fire protection resulting in structural failure during a fire and expensive restoration afterwards. Poor durability can also lead to corrosion of the substrate, compromising structural integrity. To ensure durability of intumescent coatings the key ingredients — ammonium polyphosphate, melamine and pentaerythritol — are all sensitive to moisture, and must be formulated carefully.
Different resins are used to prepare intumescent coatings for different applications. Water-based acrylic materials are formulated for use in mainly dry, internal locations. Solvent- based acrylic materials are used to formulate intumescent coatings for use in internal or sheltered external locations.
Solvent-based or solvent-free epoxy materials are used to formulate intumescents that can be used in any location. These resins have different weathering performance, and therefore, protection capabilities.
To test the durability of an intumescent coating, standard coating test procedures are used, such as NORSOK M 501, “Surface preparation and protective coating,” Underwriters Laboratory, UL 2431, “Rapid Rise Fire Tests of Protection Materials for Structural Steel”, European Technical Approval Guidance, EAD350402-00-1106, “Reactive Coatings for Fire Protection of Steel Elements”, and/or EN16623, “Reactive coatings for fire protection of metallic substrates. Definitions, requirements, characteristics and marking.”
In addition, the intumescent coating should not spall or crack in use, be resistant to atmospheric and chemical attack and be re-coatable with itself — even after prolonged curing. There should also be excellent bonding between substrate, primers and the intumescent to combat the problems of under-film corrosion.
Specifying Fire Protection
Firstly, the item to be protected must be identified, whether it is structural steel, vessels, or divisions such as fire-resistant bulkheads, or decks, on petrochemical facilities. The general rule is, the thicker the coating, the longer the protection – up to a limit. The thickness of the intumescent used will depend on the weight and type of the steel member being protected. As the weight of steel decreases, the thickness of the intumescent should increase. Lightweight steel sections will heat up faster than heavier sections and will therefore need more protection for a given time.
Rather than just figuring the weight of the steel, specific calculations must be made in order to determine the appropriate thickness of the coating, taking into consideration the shape, or shapes, of the steel and accounting for any cut-outs or irregularities in the beams. The critical steel temperature which must be protected against should be defined — for example, structural steel between 200 and 750 C, and vessels between 200 and 350 C.
Next the section factor must be considered, as well as the fire protection period of between 30 minutes and four hours. The section factor (Hp/A) is the ratio of the fire exposed perimeter to the cross-sectional area of the steel (Table 1).
Most intumescent coating suppliers provide guidance in calculating the thickness of the coating required for a specific use and some have dedicated departments staffed with trained fire engineers who will do the calculations for you. For cellulosic fires, the products will have 3rd party certification to national or international standards (BS 5476 or EN13381). For hydrocarbon fires, the products will have certification from bodies such as Lloyd’s Register, Det Norske Veritas, or Underwriters Laboratories.
Consideration must also be given to the service environment the structure or vessel will be exposed to, as well as any special requirements such as blast resistance, high or low substrate temperature or cryogenic spill protection.
Conclusion
In addition to offering fire protection for up to four hours, intumescent coatings offer speed of application, shop or field application, aesthetic appearance and ease of inspection and maintenance.
Intumescents can protect a variety of steel surfaces from structural columns and cellular beams, to building components, vessels, and complex shapes. They can be formulated to protect against cellulosic and hydrocarbon fires including jet fires and fires resulting from explosions.
I would like to acknowledge the assistance of colleagues at JPCL, and Rick Perkins, Global Technical Manager – Fire, Sherwin-Williams Protective Marine Coatings, in compiling this article.
Brian Goldie
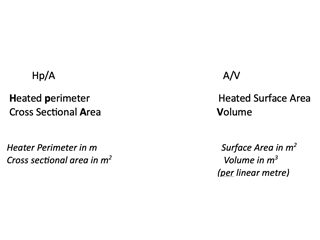
Table 1. Ratio of surface exposed to the fire, and “heat sink”.
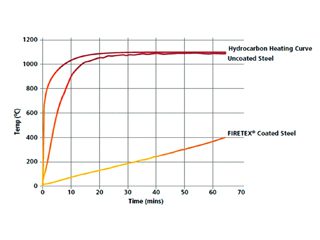
Fig. 1: This graph illustrates the effect of intumescent coating on steel temperature in a hydrocarbon fire.
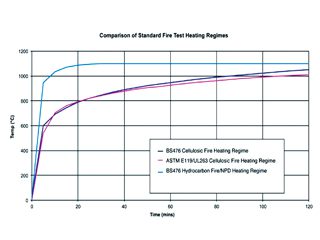
Fig. 2: This graph compares the heat-up rate of cellulosic and hydrocarbon fires.
Corrosion Control, Fellows Corner
Telling the Truth and Nothing But the Truth
Peter Elliott, Corrosion & Materials Consultancy, Inc., Las Vegas, USA.
This is the first in an occasional column, to inspire new graduates into working within our industry, by highlighting the interesting and varied aspects of a career in corrosion control, as experienced by members of the institute.
Times change, as does the understanding of corrosion and its control. As a graduating metallurgist with interests in high temperature oxidation and corrosion, my first research job, with Imperial Metal Industries, Birmingham, was the challenge of developing a metal, actually a refractory metal alloy containing tantalum, hafnium and niobium, that could survive a round trip into space. Using a high-temperature glaze from the Potteries as a coating – it worked. My interests were further enhanced by attendance at a local Institute branch meeting on corrosion by Professor T.K. (Ken) Ross, a chemical engineer, who enticed me to leave the space race and join him at what was then the University of Manchester Institute of Science and Technology (UMIST). He invited me to conduct research and asked if I knew anything about boilers. To my surprise, when I replied “no”, he replied “Perfect, I want someone with an open mind. Come and join us. When can you start?”
The return to my hometown of Manchester, to a Chemical Engineering Department, which in 1968, witnessed the creation of the Corrosion and Protection Centre – the first such academic department in the world to focus on teaching, research and industrial consulting services addressing corrosion and its control. Joining the UMIST staff my interest in boilers grew, but, by noting that metals don’t always stay hot, so did my knowledge in aqueous corrosion,including the measurement of atmospheric corrosion, which was particularly valuable – see below.
For countless years perceptions about corrosion have suggested that this often visually alarming disease is unsurmountable. Corrosion cost surveys proclaimed enormous financial losses, classed as high percentages of the Gross National (or Gross Domestic) Profit.[1] Akin to cancer and other diseases, there are parallels with corrosion control, where advances in monitoring, understanding, and treating causes with palliative cures, has grown significantly. Over the years I have noted parallels to the UK National Health Service that operates more as a National Disease Service, where exercise and healthy foods were lacking, medicines were not taken, examinations were not performed, and surgery or continued hospitalisation was required. A better understanding of corrosion, promulgated by professional societies, at least recognising (better still understanding), the interplay of thermodynamics [can a material react?] and kinetics [how fast can it be ?]. Those who seek young, experienced chemists, engineers, and metallurgists, are apparently ignorant to this oxymoron; age hardening (misquoted) reflects years of experience along with expertise.
I have continued my interest in corrosion failures – from establishing a museum in what was the UMIST Corrosion & Protection Centre so many years ago, to sharing examples at countlessmeetings and in publications.[2] I am particularly fascinated by unusual cases, for example a case that revealed a “crack” is not a crack, which brings
back memories of Turner’s Laws of Corrosion, e.g., “Nor all
that be cracked, needeth it be SCC”.[3]
The case in question pertains to a leak in the top of a ¾”- diameter domestic cold-water pipe, which after 21 years’ service, was first attributed to a lateral crack (Figure 1A), until laboratory examination showed a complex pattern of localised pitting from the inside of the pipe (Figure 1B). The cause was apparent when the farmhouse homeowner shared the history of his convenient (for him) but unusual water sources, comprising of two years “dirty” well water, followed by 20 years of soft rainwater collected from the roof of his building. These uniquely different conditions favoured localised pitting, which progressed with sustained attack from the soft water that ultimately fully penetrated through the top of the copper pipe as the pinhole leak. The copper was not defective; there was no evidence of stress corrosion cracking.
To date, with over two million airline miles and many thousand traveled by road, my response to the question “what have you learned most?” is my knowledge of geography! In a recent litigation matter an opposing expert stated that my report was biased. A few months later – when monitored atmospheric data was available – truth prevailed. The settlement was enhanced as the bias was refuted. Telling the truth is the key to corrosion control.
References
1. Hoar report (UK), NIST, Library of Congress (USA)
2 P. Elliott, Gallery of Corrosion Damage”, Metals Handbook, 13B, ASM International, p.629-646, 2005.
3 M. E. D. Turner (Mervyn) – deceased – private communication.
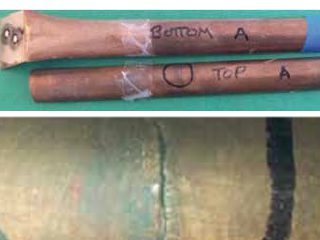
Fig 1A “Crack” in top of ¾”diameter copper pipe.
Detail of “crack.”
OD top pf pipe.
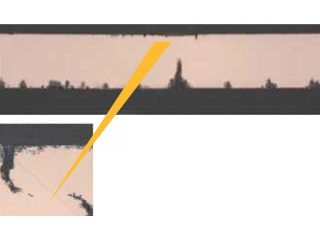
Close to “crack” location.
Fellows Corner
This series of articles is intended to highlight industry-wide engineering experience, guidance, and focussed advice to practising technologists. It is written by ICorr Fellows who have made significant contributions to the field of corrosion management. This issue features the problem of galvanic corrosion in tanks, by Chris Googan, antiCORR (Anticorrosion Engineering Ltd).
Galvanic Corrosion – Getting the Message Across
Readers of Corrosion Management will be familiar with the perils, and mitigation, of galvanic corrosion. However, the engineering world at large is often unaware of the pitfalls. This article illustrates this with three case histories drawn from the effluent treatment industry. What is interesting is, not so much that the problems arose, but the conflicting remedial measures recommended by (so-called) corrosion experts called in
to help.
Case 1 – Poultry Processing
The first case was a waste-water treatment tank at a UK poultry processing facility. As can be seen in Figure 1, this included stainless steel processing equipment which was electrically earthed to the tank. The effluent treated was warm, intentionally aerated and, being relatively chloride-rich, was highly conducting. The tank supplier recognised this as a galvanic corrosion situation, and that it was made all the more damaging by the very high ratio of the stainless steel area to that of carbon steel at lining defects. Accordingly, the supplier warned the owners of the problem, whilst at the same time prudently withdrawing its warranty.
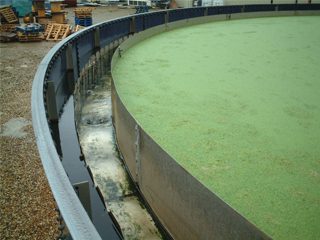
In response, the owners declined to invest in corrosion expertise. Guided by their accountant, they elected to remedy the situation by cathodic protection (CP), a plausible but, in this case, optimistic approach. Dispensing with the cost of any CP evaluation or design, some small anodes were procured. It is, however, by no means clear how, or indeed if, these anodes were actually installed. In any event, the outcome was all too predictable. Within a matter of weeks, the tank was leaking like a sieve (Figure 2), its role having changed from effluent treatment to effluent dispersal!
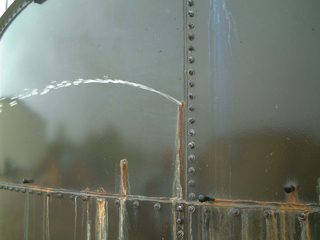
Fortunately, this amusing case was not particularly costly. Since the tank was relatively small, the pragmatic remedy was to rebuild it in GRP.
Case 2 – Municipal Refuse Treatment
The second case involved several very large effluent aeration tanks constructed for municipal refuse treatment facilities in northwest Europe. Even before formal handover, the tanks were found to be springing leaks, to the consternation of the owners and the exasperation of the environmental authority. Investigation revealed dramatic holes in the shells (Figure 3).
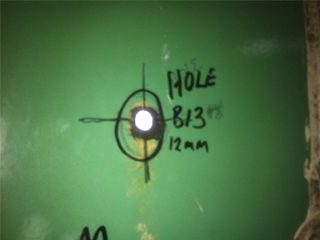
The facility EPC contractor interpreted the problem as defective lining, and called in lining experts. Time and money were then invested in carrying out lining repairs in the hope that this would remedy the problem. Unfortunately, it seems the lining experts had forgotten their galvanic corrosion lessons. They missed the fact that the very well-lined carbon steel tanks contained multiple bare stainless steel nozzles. As in Case 1, the cathode to anode area ratios were enormous, so the galvanic corrosion penetration was very rapid (the steel effectively undergoing electrochemical machining). Improving the quality of the lining on the carbon steel breached a cardinal rule of managing galvanic corrosion, which is to coat the cathode. All the re-lining work achieved was that the tanks developed leaks even more quickly when returned to service.
Eventually corrosion expertise was called up. The solution was straightforward: paint the stainless steel, and install a modest sacrificial anode provision. Unfortunately, however, the EPC contractor was unwilling to engage in what it regarded as the “untried” technology of CP. Facing litigation, it took the financially punishing step of demolishing the tanks and rebuilding them in polymer-lined reinforced concrete.
Case 3 – Beverage Manufacturing Effluent
In many ways, Case 3 was similar to Case 2. It involved a number of large aeration tanks for treating effluent produced by a major European beverage manufacturer. Again, the carbon steel tanks were very well lined, but they contained stainless steel inlet piping and aeration equipment. Some credit is due to the designers who recognised the potential for galvanic corrosion. They addressed it, in accordance with good engineering practice, by ensuring that the stainless steel piping and diffusers were electrically isolated from the tank (or so they thought).
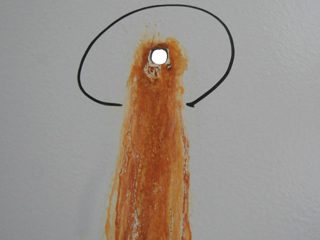
Experience tells us that a corrosion engineer can always call for electrical isolation between tanks and piping. But, in practice, the electrical engineers will always be working to achieve the opposite for the purpose of electrical safety. Thus, although the piping was electrically isolated at the point of entry to the tanks, both piping and tank walls were bonded into the common site electrical earthing system. So, notwithstanding the design intent, a galvanic cell with an adverse cathode to anode area ratio was created. Inevitably, galvanic corrosion occurred and the tanks leaked (Figure 4).
Unlike the EPC contractor in Case 2, the Owner of this facility called in corrosion, rather than lining, expertise. The corrosion specialist advised installing CP. This was accepted by the owner, and a competent contractor was engaged to supply a simple, but effective, system of sacrificial anodes suspended from cantilevered brackets fixed to the tank rim (Figure 5).
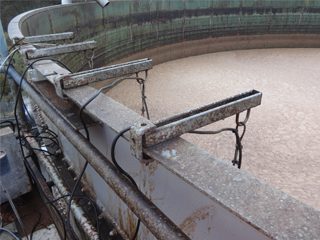
The tanks were patch-repaired and returned to service. When they were inspected five years later, the tanks were found to be in good condition. Corrosion of the tank walls, galvanic or otherwise, had been effectively suppressed.
Corrosion Community Responsibility
Doubtless, those involved in these three cases are now more aware of galvanic corrosion, and how not to manage it, than previously. Unfortunately, there remain too many engineers who, although competent in their own discipline, find themselves taking galvanic corrosion engineering decisions without even a rudimentary comprehension of the basic principles. Therefore, the question for corrosion professionals is, are we doing enough to get the right messages to the right people?
Chris Googan
Figure 1
Figure 2
Figure 3
Figure 4
Figure 5