Fellows Corner
Formicary, [1] or ant-nest corrosion [2] – based upon the similarity of substrate damage with an ant’s nest (Figure 1) – dates back about fifty years. [3,4]. Formicary corrosion is a rapid acting process involving the conjoint presence of oxygen (air), moisture and a weak organic acid. It may be regarded as a “hidden” phenomenon because, (a) it is unknown to those who have not experienced it first-hand, and (b) it is challenging to identify, because the surface pin hole leak sites are often so fine that they are not visible to the unaided eye (Figure 2). Generally considered unique to copper, this insidious form of internal corrosion (Figure 1) comprises of micro-pitting networks (akin to tunnels) [5,6] that can fully penetrate small bore tubing in weeks, not years. Pin holes that occur on the outer or inner diameter surfaces are commonly surrounded by zones of discoloured copper, ranging from dull gray/black to red/brown or purple hues (Figure 2). Refrigeration-grade copper tubing, [7] used throughout the HVAC industry, was ravaged for decades (Figure 3) and 10% of all premature failures were attributed to formicary corrosion.[8]
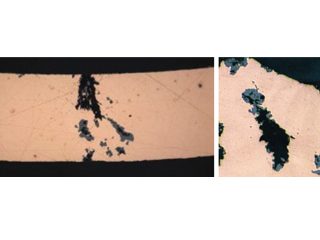
Figure 3: Formicary corrosion common to all HVAC coil manufacturers.
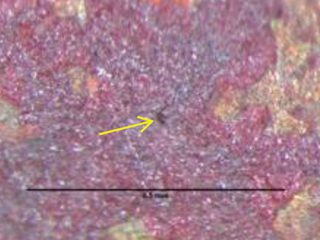
red/brown/purple hues on copper surface.
Figure 2: Tiny pin hole leak location.
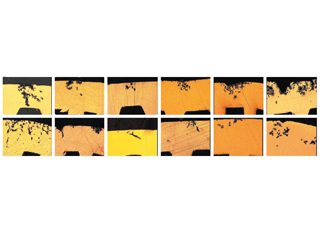
Photomicrographs from different manufacturers; depth of polishing affects the visible spread of damage shown
[9] As-polished.
Copper used in other applications, including heat pumps, dehumidifiers, air coolers, heat exchangers, freezers, and chiller units, can experience formicary corrosion. Identical penetrating attack observed under coatings, lagging, sealant contact, and insulated copper piping, is typically the result of wet conditions and compounds that hydolyse to form carboxylic acids, or other chemical sources, including chlorinated organic compounds (trichlorethane, trichloethylene, etc.), and hydrolysis products from the decomposition of esters, aldehydes and alcohols (carbonyls).
Mechanism of formicary corrosion
Extensive research by the Japanese Copper Development Association [10,11] showed that formicary corrosion occurs when certain residual organic compounds degrade in the simultaneous presence of air and moisture, to produce carboxylic acids, such as formic, acetic, propionic and buteric acids. This finding was pertinent to the HVAC industry (Figure3), where synthetic lubricating oils used for forming coils, and degreasers/detergent cleaners, contained such compounds.
The general mechanism involves a micro anode, where dissolved copper ions combine with carboxylic acids (HCOOO-) to form an unstable cuprous complex Cu(CHOO), which is oxidised to form cupric formate, acetate, etc., 2Cu(CHOO)2 (cuprous complex) and cuprous oxide (Cu2O).
Microcracks with localised intergranular attack, caused by a wedging effect from the volume expansion in forming the cuprous complex and cuprous oxide [6,12] initiate at weaknesses along the corrosion pit wall, exposing more surfaces of copper to perpetuate the advancing corrosion process.
Recognising formicary corrosion
Once the locations of the fine pinholes are found – by water immersion pressure testing, macroscopy, or both – optical microscopy will confirm if the images display the unique metallography of the formicary tunnels (Figures 1, 3), which are significantly different from the smooth hemispherical contours associated with general pitting corrosion of copper (Figure 4).
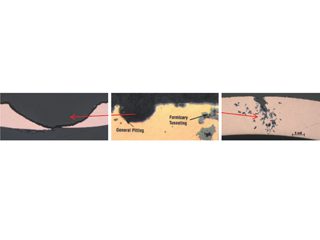
General pitting by halides (chlorides, fluorides). Comparison from coil manufacturer’s report[9]. Subsurface tunnels of formicary corrosion.
Figure 4: Contrasting the two most cited common forms of coil corrosion.
As industries have become more familiar with the causes of formicary corrosion, the frequency of leaks has fallen. Research [13]1 sponsored by the Air Refrigeration Technology Institute (ARTI), to develop a reproducible screening method to determine the mechanisms and effects of corrosion,[14] resulted in a hydrolytic stability test, which uses ion chromatography to ensure that lubricant drawing oils and finning lubricants are free of carboxlic species. A separate pre-screening hexane rinse of copper tubing, provides evidence of residues with carboxylic species identified using Fourier Transform Infrared Spectroscopy (FTIR). Several HVAC equipment manufacturers have made material and design changes, including, tin-plated copper hair pins and tubing less prone to attack, ductless AC units with moisture filters, and all-aluminium tubing and fin construction.
Currently, indoor coil leak failures by formicary corrosion have been attributed to energy- efficient buildings with decreased ventilation that promulgate higher concentration levels of carboxylic acids from building materials, woods, adhesives, disinfectants, cleaning solvents, vinegar seasonings, liquid smoke, cosmetics, etc.
Selected examples of formicary corrosion leakages presented herein, include, HVAC coils with pin holes on the outer (OD) or inner (ID) diameter surfaces (Figures 5, 6), and a heat exchanger from a fabrication shop (Figure 7).
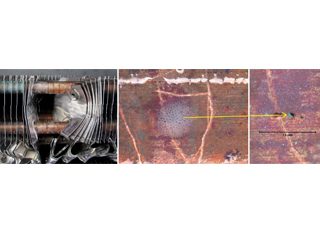
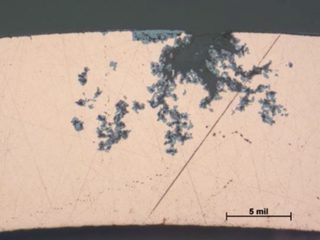
OD-initiated formicary intrusions in defect-free copper.
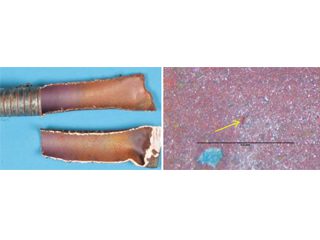
ID of split tube with purple/red-brown surface film. pin hole in purple/red-brown surface film.
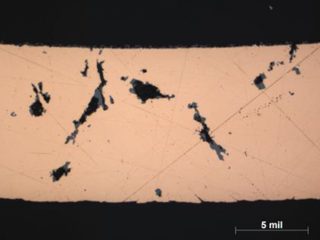
ID-initiated formicary intrusions in defect-free copper.
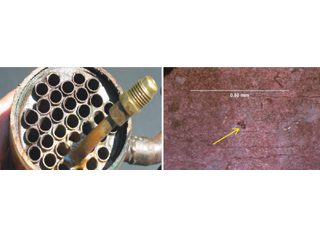
Open end of heat exchanger. Pin hole in purple/red-brown surface film on ID of tube.
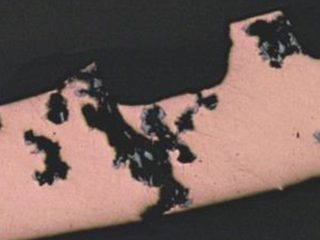
ID-initiated coarse formicary tunnel in defect-free copper.
Pin holes in copper are not always formicary corrosion
Some examples of formicary corrosion have been presented in the previous paragraphs, with brief comments about how it can be assessed and generally avoided by using screening tests on the copper tubing and of the contact environment. Presented In the following paragraphs are some examples where pin holes were wrongly ascribed to formicary corrosion.
• Failed HVAC installation – pin holes found following about 2 to 3 years service were claimed by the coil supplier[15] to display the “worst case of formicary corrosion ever seen”. They were incorrect. The observed damage (Figure 8), and the optical photomicrographs (Figure 9), show no micro-pitting networks – the chacteristic feature for formicary corrosion.
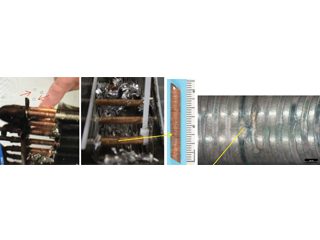
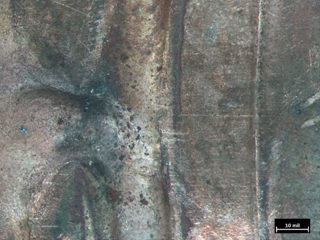
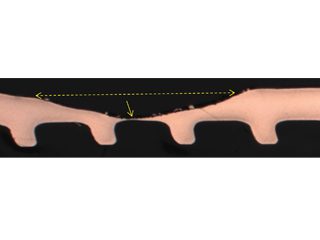
The leak locations along the copper tubing appear to be associated with the design and assembly of the ceiling-mounted units. The repeating geometric pattern of hemispherical- shaped wastage zones close to, or in direct contact with, the aluminium fins, (Figure 9) suggests a modified form of Rosette corrosion,[16] combined with crevice corrosion,[17] and galvanic attack. [18] The additional pitting in the vicinity of the through-wall leaks (Figure 8) is indicative of some form of synergy between these processes.
Rosette corrosion is a somewhat recently recognised corrosion phenomenon,[19] which was encountered in copper hot water cylinders fitted with aluminium anodes. The anodes were installed to prevent type 1 pitting corrosion and was very successfully applied for over 30 years.[20] However, corrosion failures were occurring at the bottom of these cylinders where the water was cooler. This phenomenon was attributed to the interaction of the copper-aluminium galvanic couple [21] and certain impurities in the water that generated reducing species that led to the corrosion at the bottom of the cylinders. This form of corrosion has been essentially eradicated in the United Kingdom, when specifications disallowed the use of aluminium protector rods in 2002.[22] The removal of the aluminium anode and a redesign of the hot water cylinders eliminated the cold bottom thus promoting the growth of a semi-protective corrosion layer.
• Formicary corrosion by contact with sealant – accounting for a blue discoloration surrounding a usually white-colored acoustic sealant (Figure 10), a recent publication wrongly implied that tube failure by formicary corrosion and environmentally assisted cracking (EAC) from such contact was probable. [23] Long-term simulation testing with high relative humidities and temperatures showed this was most unlikely.[24] Without a sustained presence of air and moisture, through-wall penetration by formicary corrosion – a rapid process, as noted earlier – is not expected. Mechanical laps from tube-forming (Figure 10) were wrongly interpreted as EAC with formicary corrosion. This matter was addressed nine years ago, [25] the blue discoloration was nothing more than an aesthetic issue.
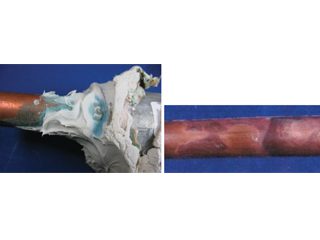
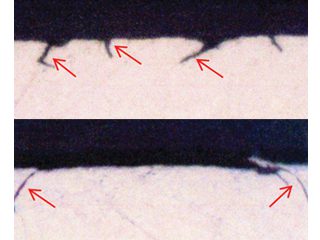
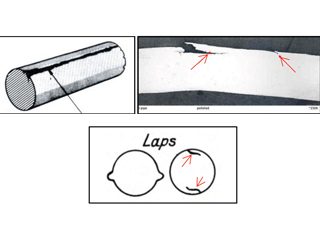
Discussion and conclusions
Formicary corrosion is regarded as a subsurface network of microscopic-corroded tunnels that are considerably larger than the tiny pin holes they connect to, [27] which presents a challenge to those who are aware of the “usual” localised phenomenon of pitting corrosion,which ranked fourth from seven common sources of copper tube corrosion based on over 1,500 investigations over 25 years in domestic water systems. [28] This source noted that all can be mitigated cost-effectively provided that, water quality is maintained, copper tube systems are properly designed and installed, and systems are operated within design parameters.
Formicary corrosion may be active if:
• fluids leak in weeks or months.
• surface zones of discoloured copper (dull gray/black to red/brown or purple hues) are evident.
• copper exposed to air (oxygen), moisture and a weak organic acid, e.g., carboxylic acids, (formic, acetic, propionic, buteric).
• copper exposed to other chemical sources, including chlorinated organic compounds and hydrolysis products from decomposition of esters, aldehydes and alcohols (carbonyls).
• wet conditions persist under coatings, lagging, sealant contact, and insulated piping with compouds that hydrolyse to form carboxylic
acids.
Success in dealing with formicary corrosion, like many other forms of corrosion, is dependent on knowing what it is; knowing how to recognise it; knowing what causes it; and focusing on control, rather than elimination – the realistic goal. [30]
Acknowledgements
The author kindly acknowledges the contributions of Mr. Fred Sherman, Sr. Materials Analyst, for his meticulous contributions to the metallography and laboratory testing, and Mr. Brad Krantz, VP of Laboratory Services, for support and access to Corrosion Testing Laboratories, Newark DE.
References
1.
“For-mi-car-y”: from Medieval Latin, Formica ‘ant’, defined as a nest of ants or an anthill, Oxford Dictionary.
2.
S. Yamauchi, K. Nagata, S. Sato, M. Shimono, J. Japanese Copper & Brass Research Assocn., 22, p.132, (1981).
3.
J.O. Edwards, R.J. Hamilton, J.B. Gilmore, Materials Performance, NACE International, 16, 9, p.18, (1977).
4.
J. M. Keyes, International Copper Research Association Symposium, Belgium, June (1965).
5.
P. Elliott, R.A. Corbett, “Ant Nest Corrosion – Exploring the Labyrinth”, Corrosion Reviews, 19, No. 1, p.1-14, (2001).
6.
R.A. Corbett, P. Elliott, “Digging the Tunnels”, Corrosion Reviews, 20, No. 2, p.51-66, (2002).
7.
DHP copper, alloy C122, UNS C12200, 99.90% copper, ASTM B280.
8.
Go Isobe et al, NACE Corrosion Asia, Paper 105, Singapore, September (1992).
9.
Carrier Corporation, Industry Research Reports “Indoor Coil Corrosion” (2007 to 2011).
10.
T. Notoya, T. Hamamoto, K. Kawano, Corrosion Engineering (Japan), 367, 2, p.1, (1988).
11.
T. Notoya, “Localized “Ant Nest” Corrosion of Copper Tubing and Preventive Measures”,Materials Performance, NACE International, 32, 5, p.53, (1993).
12
D. M. Bastidas, I. Caynela, J.M. Bastidas, CENIM – National Centre for Metallurgical Research, CSIC, Avda, Madrid, Spain, “Ant-nest corrosion of copper tubing in air-conditioning units”, Revista de Metalurgia, 42 (5) September/October, p.367-381, (2006).
13.
Air Refrigeration Technology Institute (ARTI), Report, 21-CR Research Project 611-50055, R. A. Corbett, Corrosion Testing Laboratory, Newark, DE, with input from P. Elliott and T. Notoya, (2003).
14.
R.A. Corbett, “The Development of a Reproducible Screening Method to Determine the Mechanisms and Effects of Organic Acids and other Contaminants on Corrosion of Aluminium-finned copper tube Heat Exchanger Coils, Corrosion 2004, Paper 04321, NACE International,
New Orleans, LA, (2004).
15. Private communication.
16.
Rosette corrosion – the premature failure of copper hot-water cylinders fitted with aluminium rods to prevent Type 1 copper pitting: R.J. Oliphant, Journal of Chartered Institute of Water & Environmental Management, UK, vol 14, p. 207, July (2007). R.J. Oliphant, Causes of Copper Corrosion in Plumbing Systems, Foundation for Water Research Review, FR/R0007, May (2003).
17.
Crevice corrosion – localised corrosion of a metal or alloy surface at, or immediately adjacent to, an area shielded from full exposure to the environment because of close proximity of the metal or alloy to the surface of another material or an adjacent surface of the same metal or alloy. NACE/ASTM G193-12d, Standard Terminology & Acronyms Relating to Corrosion, (2010).
18.
Galvanic corrosion – accelerated metal corrosion because of electrical contact with a more noble metal or nonmetallic conductor in a corrosive environment. NACE/ASTM G193-12d, Standard Terminology & Acronyms Relating to Corrosion, (2010).
19.
R. Francis, Corrosion of Copper and its Alloys: A Practical Guide for Engineers, NACE International, (2010).
20.
R.J. Oliphant, Journal of Chartered Institute of Water & Environmental Management, UK, vol 14,p. 207, July (2007).
21. V.F. Lacey, British Corrosion Jnl., 7, p.36, (1972).
22.
P. Munn, Causes of Copper Corrosion in Plumbing Systems,3rdEdition, Report FR/R0007, Foundation for Water Research September, (2017).
23.
K. Steiner, “Formicary Corrosion and EAC of Copper Tubes in Contact with Building Sealant”, AMPP Annual Conference, Paper No.17846, AMPP, San Antonio, TX, (2022).27.
24.
P. Elliott, “Blue-Stained Sealants Do Not Imply Catastrophic Corrosion of Medical-Grade Copper Piping”, Materials Performance, NACE International, 52, 6, p.57, (2013).
25. ibid.
26.
Laps sourced from: ASM International, Volume No. 11, Failure Analysis & Prevention, Failures Related to Metalworking, p.82, (2002); Rollason E.C., Metallurgy for Engineers, 4th Ed., Edward Arnold, p. 62, (1973).
27. A.H. Brothers, Mainstream Engineering, Rockledge, Fl – internet search.
28.
J. R. Myers and A. Cohen, “Copper-Tube Corrosion in Domestic-Water Systems”, HPA Engineering: Supplement, June, (2005).
29.
P. Elliott, “Fight Formicary Corrosion”, Chemical Processing, p. 37, November (2005).
Peter Elliott
Full section perforation via formicary “tunnels”. 150X Unique “ant”. 500X
Figure 1: Through-wall formicary corrosion and detail of local “ant”.
Removing aluminium fins to expose tiny holes. Soapy bubbles locate miniscule holes by immersion testing with nitrogen.
Figure 5: OD attack in HVAC coil promoted by cleaning/disinfecting wipes containing ethanol, propanol, and a propionate (a carboxylic specie).
OD-initiated formicary intrusions in defect-free copper.
ID of split tube with purple/red-brown surface film. pin hole in purple/red-brown surface film.
Figure 6: ID attack in HVAC tubing by detergent or degreaser contaminated with carboxylic specie. The tube was drawn using lube oil free from carboxylic acids.
ID-initiated formicary intrusions in defect-free copper.
Open end of heat exchanger. Pin hole in purple/red-brown surface film on ID of tube.
Figure 7: ID attack in enhanced copper tubing in a heat exchanger bundle from a fabrication shop. Surface products contained carboxylic (formate) species.
ID-initiated coarse formicary tunnel in defect-free copper.
From left to right. Bubbles show leaks. Aluminium fins stripped to access copper sample. Macro of pinholes on the OD surface.
Close up of OD pinhole leak and surrounding small pits.
Figure 8: Pin hole and other localised pits in one of many HVAC indoor coils.
Detail of OD leak location. As polished. 80X
Figure 9: Through-wall leak location coincides with a repeating geometric pattern of smooth hemispherical pits aligned with the aluminium fin locations.
Blue-stained white sealant; 18 months in service. Superficial etch stains on copper with sealant removed.
Shallow surface laps under sealant. As polished. 500x. Shallow surface laps remote from sealant. 500x
OD – longitudinal surface lap.Photomicrograph of surface laps.Schematics of OD and ID laps.
Figure 10, Blue-stained sealant on copper tubing in hospital installation and shallow surface laps [26] misinterpreted as EACs and the initiation of formicary corrosion.
Fellows Corner
This series of articles is intended to highlight industry-wide engineering experiences, guidance, and focused advice to practising technologists. The series is written by ICorr Fellows who have made significant contributions to the field of corrosion management. This issue features articles on the use of existing pipelines for the transport of hydrogen, by Frank Cheng, Dept. of Mechanical & Manufacturing Engineering, University of Calgary, Canada, and on an interesting aspect of copper corrosion, by Peter Elliott, Corrosion & Materials Consultancy, Inc., Las Vegas, USA.
Suitability of existing pipelines for hydrogen service
It is believed that hydrogen will play a critical role in energy transition, and achievement of the 2050 net-zero emission goal. Hydrogen delivery is integral to the entire value chain of hydrogen economy. Compared with other transportation modes, such as tankers, pipelines provide an economic and efficient means to transport gaseous hydrogen with a high transportation capacity over long distances [1]. Particularly, repurposing existing natural gas pipelines is “a low-cost option for delivering large volumes of hydrogen” [2], contributing to accelerated realisation of a full-scale hydrogen economy, while saving high initial capital costs of constructing new hydrogen-dedicated pipelines.
However, hydrogen embrittlement (HE) can occur on pipelines transporting hydrogen in either blended or pure form, compromising the structural integrity to cause pipeline failures. Compared with newly constructed pipelines, the existing pipelines, after a long time of service in the field, include additional challenges to address in terms of the HE occurrence when converted for hydrogen service.
What is hydrogen embrittlement?
Hydrogen embrittlement is a general term describing the degradation of a material’s (mainly metal) properties and structural integrity, due to hydrogen-metal interactions. HE is a concept serving as an ‘umbrella’ under which many different modes of metallic degradation induced by hydrogen are referred to.
The first mode of HE phenomenon is hydrogen-induced cracking (HIC), which is also regarded as the most dangerous mode of HE-associated materials failure. The HIC occurs when the hydrogen atom concentration at a local site exceeds a threshold value under a given stress condition. Generally, the threshold H atom concentration required to initiate cracks in steels decreases with an increased stress. Many mechanisms or theories have been proposed to explain the HIC occurrence, such as hydrogen-enhanced localised plasticity (HELP), hydrogen-enhanced decohesion (HEDE), adsorption- induced dislocation emission (AIDE), and hydrogen-assisted microvoid coalescence (HAMC) [3].
Presently the dominant mechanisms for HIC of steels are the HEDE and HELP [4]. According to the HEDE mechanism, H atoms can weaken bonds between iron atoms in steels and when the external stress exceeds the atomic cohesive strength of Fe in the presence of H atoms, microcracks can be initiated. The HELP mechanism proposes that H atoms accumulate at dislocations to decrease the interfacial elastic energy between mobile dislocations, enhancing the mobility of the dislocations. As a result, the local deformation can occur at a lowered stress, facilitating plastic deformation and cracking occurrence. The HIC can initiate whether on the surface of a metal (i.e., external HIC,) or inside the metal (i.e., internal HIC).
The second mode of HE is hydrogen blistering, where the H atoms entering the metal become recombined to form hydrogen molecules (H2) at the trapping sites, such as voids. The elevated pressure due to accumulation of H2 molecules at a local site can cause formation of a blister (or bubble) on the metal surface. This hydrogen blistering usually occurs on low-strength and ductile metals where the bubbling process does not initiate cracks. Instead, the metals’ experience a remarkable local plastic deformation. If the metals have a high strength and limited ductility, the hydrogen-elevated pressure can cause cracking by the so-called hydrogen internal pressure (HIP) mechanism.
The most common mode of HE phenomenon is degradation of mechanical properties of the affected metals, which is usually shown as a reduction in fracture toughness and ductility. The direct evidence of this mode is the decrease in fracture elongation in the stress-strain curve measured on hydrogen- charged metals, compared with the tensile behaviour of hydrogen-free metals. Generally, a limited amount of hydrogen atoms may not be sufficient to initiate cracks, but can cause a reduction in ductility of the metals.
Uniqueness of pipeline hydrogen embrittlement in high-pressure gaseous environments
HE can occur on pipelines in high-pressure gaseous hydrogen environments. The entire HIC processes include six steps, i.e., generation of H atoms, adsorption of the H atoms on the steel surface, absorption of the H atoms by permeating into the steel, diffusion of H atoms in the crystalline lattice, trapping (accumulation) of H atoms at local sites, and the crack initiation, as schematically shown in Figure 1. The first three steps, i.e., H atom generation, adsorption, and absorption, depend heavily on the environment, whereas the other steps of diffusion, trapping and cracking, mainly rely on the metallurgical factors.
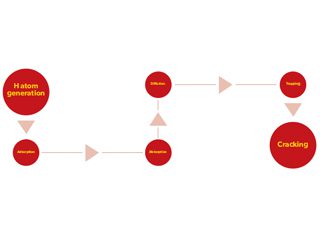
Figure 1. Entire processes for HIC occurrence on metals (steels).
Previous work demonstrated that H atoms can generate and become adsorbed on steel surfaces through a so-called dissociative adsorption mechanism in high-pressure gaseous environments [5]. The Gibbs free energy changes for production of H atoms from gaseous H2 molecules are negative, indicating a thermodynamic feasibility, under pipeline operating conditions with typical temperatures, pressures and H2 gas/natural gas blending ratios. Moreover, the generated H atoms can adsorb stably at On-Top (OT) and 2-fold (2F) Cross-Bridge sites of the Fe (100) crystalline plane, while the hydrogen adsorption at 2F sites is more stable due to a higher electron density and a stronger electronic hybridisation between Fe and H. Upon entering the steels, the H atoms predominantly stay at tetrahedral void sites due to a low energy path and exothermic feature. It has been noted that a uniform distribution of H atoms at the tetrahedral voids in a crystalline lattice would not cause HE or HIC, if the amount of H atoms is within the limit of H solubility. However, the local solubility can be exceeded if H atoms diffuse towards high stress zones, or become trapped at metallurgical features such as grain boundaries, dislocations, and non-metallic inclusions.
Nowadays, substantial studies have been conducted to investigate HE of metals, including pipeline steels, in aqueous environments, where most investigations focused on H atom generation during steel corrosion or cathodic over-protection. Four major differences exist in H atom generation and permeation in steel between a gaseous environment (“gaseous” hydrogen) and the aqueous environment (“cathodic” hydrogen), as listed in Table 1, making it infeasible to directly use data obtained in aqueous environments for HE investigations on pipelines in high-pressure gaseous environments. First, the amount of “cathodic” hydrogen generating during electrochemical cathodic charging, either potentiostatically or galvanostatically, is always substantial. A significant H atom concentration gradient exists between the outside and inside subsurface of the steel. However, the amount of H atoms generated in a gaseous environment is usually limited. After several months of exposure of a pipe steel to high-pressure (10 MPa) H2 gas, the measured H concentration is less than 1 ppm [6]. Secondly, due to the high concentration gradient of H atoms across the steel surface, the permeation of “cathodic” hydrogen is always one way, entering the steel from the adsorption to absorption state. As a comparison, the “gaseous” H atoms, even entering the steel and becoming absorbed inside, can still leave the absorption site and change to adsorption state [5]. Thus, the permeation of “gaseous” hydrogen is reversible. Third, the electrochemical hydrogen-charging usually generates reproducible results, making the testing method (i.e., the Devanathan-Stachurski cell) a standard method for hydrogen atom permeation tests [7]. Although there has been limited work to measure the H atom permeation in gaseous environments, the obtained data are usually scattered, and sometimes, even conflict each other. Finally, both constant concentration model and constant flux model have been developed to fit the electrochemical cathodic H-charging results to derive the H permeation parameters such as H diffusivity, subsurface H concentration and trapping density [8]. To date, a model applied for “gaseous” hydrogen permeation has not been established. Due to the differences listed, the testing results and modeling methods for aqueous “cathodic” hydrogen testing cannot be used for gaseous hydrogen permeation testing.
‘Gaseous’
hydrogen ‘Cathodic’
hydrogen
Amount generated to adsorb on steel surface Limited Substantial
Permeation pathway Reversible between adsorption and absorption One way from adsorption to absorption
Testing results Scattering, and sometimes, controversial Reproducible
Numerical model to derive hydrogen permeating parameters None Constant concentration model and constant flux model
Table 1. Comparison of the H atom generation and permeation in steels in a gaseous environment and in an aqueous environment.
Additional challenges when repurposing existing pipelines for hydrogen service
After a long time of service in the field, existing pipelines become aged and contain various surface defects such as dents, corrosion, scratches, winkles and microcracks. These defects, if passing the assessment criteria [9], would not be required to be repaired, and the pipelines can continue to operate. However, they serve as effective traps to accumulate H atoms. Particularly, dents, a common type of mechanical damage present on pipelines, is a permanent inward deformation on the pipe body, greatly changing the local stress and strain distributions. As a result, the H atoms, once entering the pipe steels, tend to diffuse towards the dent and accumulating locally. Modeling results showed that there were maximum H atom concentrations at both sides of the dent along the circumferential direction, as shown in Figure 2. The H atom distribution coincided with the distribution of hydrostatic stress on the pipe. Moreover, as the dent depth increases, the H atom concentration increases at the local area.
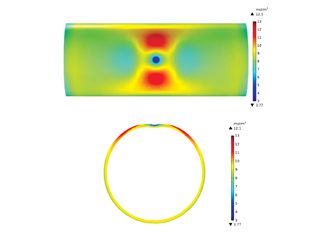
Figure 2. Distributions of the H atom concentration (unit: mol/m3) on an X52 steel pipe segment containing a constrained dent and the cross-sectional view. The dent depth is 3% of pipe outer diameter and the internal pressure is 10 MPa [10].
Different from a dent, a corrosion defect causes metal loss on the pipe wall. Moreover, the corrosion defect is dynamic in nature, and will grow with time in the service environment. It is acknowledged that corrosion is one of the primary mechanisms causing pipeline failures. Generally, the presence of a corrosion defect on the pipe body can decrease the pressure-bearing capability of the pipelines.
Thus, many standards and codes have been developed for corrosion defect assessment. Similar to a dent, if a corrosion defect passes the assessment criteria, the corroded pipelines can continue to operate, without a need to repair the corrosion defect, but a cautious monitoring of the defect growth should be followed. It was confirmed that the H atoms which were originally distributed in the crystalline lattice of a steel would diffuse towards the corrosion defect. Moreover, as the corrosion defect length reduces and the depth increases, the H atom concentration becomes more apparent, as seen in Figure 3.
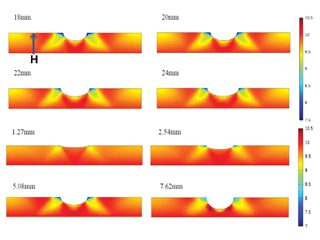
Figure 3. Distributions of the H atom concentration (unit: mol/m3) on an X52 steel pipe segment containing a corrosion defect with varied lengths and depths [10].
A technical assessment programme for the suitability of aged pipelines in hydrogen service
Obviously, a technical programme must be developed to assess the suitability of the existing aged pipelines to transport hydrogen in either pure or blended form. The assessment should consider the synergism of steel metallurgy, stress, and hydrogen, on HE or HIC occurrence. Particularly, the surface defects present on the pipelines should be paid much attention, in addition to the metallurgical features such as grain boundaries, dislocations and non-metallic inclusions, which are effective hydrogen traps. The specific service history of the pipelines which were made of various grades of steel should be considered, and the technical assessment should be conducted case by case. Once successfully developed, the technical assessment programme will be able to: evaluate the possibility of H atoms generation and the amount of H atoms adsorbed on the steel surface under pipeline operating conditions, quantify the accumulated H atom concentration at the surface defects and metallurgical features under given conditions, estimate the threshold H atom concentration at a local defect to initiate cracks under a certain stressing condition, rank the HE susceptibility of the aged pipelines while considering the metallurgical and stress factors, and recommend proper operating conditions (e.g., temperature, pressure and blending ratio) to minimise and eliminate pipeline HE in high-pressure gaseous environments.
References
[1]
A.S. Hawkins, Technological Characterization of Hydrogen Storage and Distribution Technologies, UKSHEC Social Science Working paper no. 21, Policy Studies Institute, London, UK, 2006.
[2]
U.S. Department of Energy, Hydrogen Pipelines, Washington DC, US, 2020.
[3]
Yinghao Sun, Y. Frank Cheng, Hydrogen-induced degradation of high-strength steel pipeline welds: A critical review, Eng. Fail. Anal, 133 (2022) 105985.
[4]
M.B. Djukic, G.M. Bakic, V. Sijacki Zeravcic, A. Sedmak, B. Rajicic, The synergistic action and interplay of hydrogen embrittlement mechanisms in steels and iron: Localized plasticity and decohesion, Eng. Frac. Mech., 216 (2019) 106528–106561.
[5]
Yinghao Sun, Y. Frank Cheng, Thermodynamics of spontaneous dissociation and dissociative adsorption of hydrogen molecules and hydrogen atom adsorption and absorption on steel under pipelining conditions, Int. J. Hydrogen Energy, 46 (2021) 34469-34486.
[6]
G. Golisch, G. Genchev, E. Wanzenberg, J. Mentz, H. Brauer, E. Muth
mann, D. Ratke, Application of line pipe and hot induction bends in hydrogen gas, J. Pipeline Sci. Eng., 2 (2022) 100067.
[7]
M.A.V. Devanathan, Z. Stachurski, The adsorption and diffusion of electrolytic hydrogen in palladium, Proc. Royal Soc., A270 (1962) 90-102.
[8]
Y.F. Cheng, Analysis of electrochemical hydrogen permeation through X-65 pipeline steel and its implications on pipeline stress corrosion cracking, Int. J. Hydrogen Energy, 32 (2007) 1269–1276.
[9]
Guojin Qin, Y. Frank Cheng, A review on defect assessment of pipelines: Principles, numerical solutions, and applications, Int. J. Press. Vessel Pip., 191 (2021) 104329.
[10]
Frank Cheng, Hydrogen transport in aged pipelines II. Technical assessment of the susceptibility to hydrogen embrittlement, AMPP / ASM International Calgary Chapter Luncheon, Calgary, Canada, Oct. 19, 2022.
Frank Cheng
Fellows Corner
This article will look at the Electrochemical Noise Method for corrosion monitoring. Firstly, what are its attractions?
Well, it’s as unintrusive as its possible to get, just using the fluctuations which are produced naturally by the corrosion process to tell us the corrosion rate and also, by looking at the plots, the corrosion processes (the degree to which it affects the item being measured is maybe as little like the effect on the star of using the James Webb telescope to obtain its distance based on the red shift!). Secondly the measurement is quick (a few minutes) and interpretation of results is intrinsically simple. It can operate on battery power and the equipment is portable and with appropriate sensing electrodes it can be used for continuous monitoring. The remainder of this article gives examples of how results can be obtained using the ENM technique, not just from organic coatings, but also from reinforcing bars in concrete, and to screen inhibitors. The inhibitors work is part of an ongoing programme at Nottingham university and the other two pieces of work were done by students in Northampton.
First how does the electrochemical noise arise, and what do the results look like?
Rn= v/ I 1
Where Rn is noise resistance,
v and I are the standard deviations of voltage and current values, respectively, measured during a given time period is given by:
V2 = Vj−Vm)2/(n−1) 2
I 2= Ij−Im)2/(n−1) 3
In equations 2 and 3, Vj is the voltage value measured at the jth time interval, Vm is the mean voltage in the given period of time, Ij is the current value measured at the jth time interval, Im is the mean current in the given period of time, and n is the number of time intervals. [1] For coatings, Rn equates to the DC resistance (Rdc), and EIS (0.1 Hz impedance). [2] There is evidence from this work and others that when there is significant corrosion rate, Rn relates to the value Rp obtained from Linear Polarisation Resistance (LPR). The analysis software creates a value of Rn, and typical ENM data are shown in Figure 1.
The first application of the ENM method described is to an anti-corrosive organic coating system.
The actual Noise arrangement used is known as the single substrate (SS) method, diagrammatically shown in Figure 2. You need two working electrodes for noise measurements, and with the single substrate arrangement you can have these as two areas of painted substrate on the same panel, isolated in lab work, by being contained in cells (but in site work, a dry piece of coated steel with a Calomel electrode in each cell, is adequate). The third electrode (reference) is the panel itself. When you examine an organically coated metal, the noise signal tends to be attenuated by the ionic resistance of the coating, and you end up with that resistance being dominant. In this example, the coating was applied to Q panels, cells were attached, and the coated area within each cell was exposed to 0.1 M chloride solution for several months (with occasional topping up). The ENM results were compared against DC resistance. The results are shown in the Figure 3. As can be seen, some areas of coating started with low values of resistance which tended to drop with time, while others had higher initial values, and these remained high. There was a strong correlation between the Rn values, the Rdc values, and the visual appearance. Also, the effects of thickness and number of coats were investigated. Thickness proved more critical than number of coats, although both were important, the higher the thickness the more protective the coating. The advantage of the electrochemical measurement over visual observation is, a) it tells you what is happening earlier, b) It indicates problems when you cannot see what is going on, c) it can be automated, and d) it gives you a number!
These advantages also apply in the case of the second example, that is measuring the corrosion rate of reinforcing bars in concrete. This is little more complicated to set up. The lab work was designed to be a precursor to taking the equipment out to site so non-glass electrodes were used viz solid-state silver /silver chloride solid electrodes, which worked just as well as Calomel electrodes. There is an ENM arrangement which can be applied to a coating or to concrete, which is the NOCS (No connection to the substrate) arrangement. This offers the attraction of being able to get a result without actually making any connection to the rebar itself. The experimental set up is shown in figure 4 and some typical results in Table 1. This work involved two sets of three bars in mortar, one of which contained no added chloride, and the other of which had 4% added chloride. The results were quite clear, the bars in the 4% were corroding (corrosion rate inversely proportional to Rn) many times faster than the bars in the 0% NaCl, although there was some minor variation between bars. Unlike the coating work, we cannot check these particular samples yet as they are still under test and have not been broken open. However previous published work [3] showed beyond reasonable doubt that the Rn value correlated very well to the subsequently observed corrosion.
The third example is testing inhibitors This was driven by the wish to test green inhibitors and see if they could be used as alternatives to conventional more toxic inhibitors such as propargyl alcohol. The application considered was the need to inhibit corrosion of the steel pipes used to carry the CO2 saturated oil, containing some sea water. The experimental set up is shown in Figure 5. Two small nominally identical rectangular steel samples were contained in a sample holder made employing the ‘additive manufacturing’ process (a form of 3D printing). In this case it was from an ABS polymer powder. The black blanking-off compound was provided by an anticorrosion coating manufacturer. It was found essential to stir the solution to get reproducible results, although in practise a significant flow rate is likely. Some results are shown in Figure 6, where a particular green inhibitor (sugar beet) proved more effective than conventional inhibitors. The lab investigation compared the ENM method both against corrosion loss by ICP-MS analysis, and also against the more commonly used LPR method. This work has not yet appeared in a journal publication. But a paper has been submitted to EUROCORR 2022.
This has been whistle stop tour showing the application of this ENM technique to three different fields. If anybody wants to find out more, get in touch with the author.
1) Yang, L. and Chiang, K.T. (2010) On-line and real-time corrosion monitoring techniques of metals and alloys in nuclear power plants and laboratories. Understanding and Mitigating Ageing in Nuclear Power Plants., pp. 417-455
2) Comparison of ENM, EIS and DC Resistance for Assessing and Monitoring Anti-Corrosive Coatings Douglas J Mills JCSE 2000
3) Mills, D.; Lambert, P.; Yang, S. Electrochemical Noise Measurement to Assess Corrosion of Steel Reinforcement in Concrete. Materials 2021, 14, 5392. https:// doi.org/10.3390/ma14185392
Acknowledgements
The author would like to acknowledge the assistance of Paul Lambert relation to the concrete project, and extend his thanks to students: Tian Yang Lan, Reuben Osahon and Chiata Collins for permission to publish some of their results. And to DCVG company for providing The Noise Measuring Equipment.
Douglas J Mills
Figure 1: Typically Noise plots of current and voltage against time.
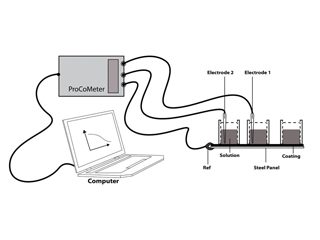
Figure 2: Schematic diagram showing how ENM is applied to coated metal (Single Substrate arrangement) (Solution is typically 0.1 M NaCl).
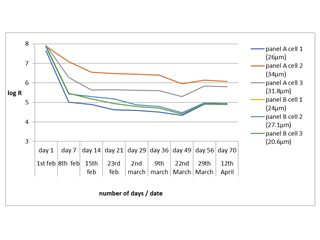
Figure 3: Typical results obtained from Hammerite coating of Resistance against time.
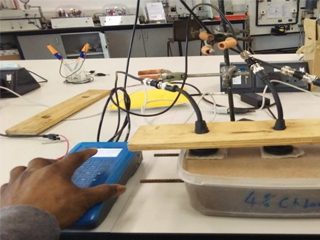
Figure 4: Set up for measuring Rebar in concrete using NOCS arrangement of ENM.
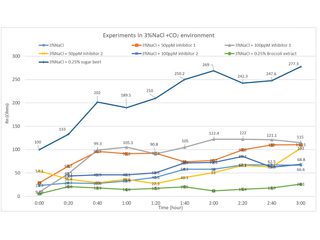
Fellows Corner
This series of articles is intended to highlight industry wide engineering experiences, practical opinions, guidance, and focused advice to practising technologists. The series is written by ICorr Fellows who have made significant contributions to the field of corrosion management. The articles in this issue feature contributions from David Harvey, who gives a personal view of his career as a senior CP Engineer, and Douglas Mills, who discusses the use of Electrochemical Noise Measurement in determining corrosion.
A Career as a Cathodic Protection Engineer
This article highlights some aspects of an interesting and rewarding career in the cathodic protection industry and with the Institute of Corrosion. It aims to show what can be experienced within the workplace and outside of it, in a varied, fascinating and satisfying career over 50 years gained with consultants, oil and gas operators, cathodic protection companies and engineering design houses. Hopefully this will encourage newcomers to the industry that there is great career to be had in cathodic protection.
I, like many others, came into cathodic protection by accident. I joined a CP Specialist Consulting Engineering Company as a draughtsman while still completing my day-release HNC in Electrical Engineering. I was fortunate to have an excellent mentor in David Lewis, former ICorr President, who gave me John Morgan’s “Cathodic Protection” textbook to study. I progressed on to become a CP design engineer. As I did not drive at that time and site visits were limited, I benefitted from picking the brains of my colleagues’ knowledge and site experience, as back then, junior engineers were teamed up with a senior engineer to learn their trade, which regrettably does not happen today. However, one of the enlightening aspects about the CP Industry is that senior engineers are generally very open in sharing their knowledge and experiences – both good and bad – to enable us to continually improve the way we approach projects and produce more cost effective, efficient designs.
CP Engineers come from many different disciplines (e.g. mechanical, electrical, chemical, civil etc) some from grass roots and others from universities. The application of CP to structures requires detailed interaction with all disciplines so one ends up knowing a little about a lot, rather than a lot about a little, unless specialising in one particular area. Rarely are two projects identical as there are so many different parameters to be considered. Today, there are training courses, exams and certification offered by ICorr at all levels from Tester to Senior Design Engineer (Levels 1- 4 of ISO 15257). However, CP is something you also need to learn from field experience – often by trial and error. It is not something you can just study and apply effectively from a desk alone. Design spreadsheets can often contain errors or have bad data inputted so the output needs strong experience to know if it is sound or “rubbish”.
My practical experience was initially gained by secondment to Middle Eastern oil companies. It covered applying cathodic protection to oil and gas fields, pipelines, associated tankage, and marine facilities. This was a very exciting time for a young man who had not previously been out of the UK. Working in the desert oil fields was almost like being on Safari. On return to UK, I was appointed a CP project engineer. Over time, I moved up to Engineering Manager and Consultant in a number of cathodic protection companies, design houses and as an independent consultant.
I was responsible for all aspects of sacrificial anode and major ICCP systems for pipelines, refineries/petrochemical facilities, and inshore/offshore marine structure projects.
My career as a cathodic protection engineer has given me the opportunity to visit and work in more than 25 different countries and meet many exceptional people at all levels. Occasionally, one could find sufficient spare time to visit some of the local tourist attractions, e.g. various roman ruins, Great Wall of China, Great Pyramids, Panama Canal etc. which were very enjoyable benefits I would not have otherwise gained.
ICorr Activities
As the industry expanded in the 1980’s, I became involved in ICorr activities when they had the Joint Venture with NACE (CCEJV), which became the Corrosion Engineering Association (CEA).
Initially, I joined a CCEJV cathodic protection work group to assist with the preparation of a State-of-the-Art Report to be published by ICorr and NACE. This enabled me to learn from my peers and, at the same time, put some of my experience back into the industry for the younger engineers to benefit from. Later, I became Work-Group Chair, then Task-Group Chair. I was then appointed Technical Activities Coordinating Committee (TACC) Chair. This role also included being the Conference Programme Manager for “UK Corrosion” which was a major three-day event in the corrosion world 1987-1991. As TACC Chair, I also attended NACE Committee Weeks and Corrosion Conferences in USA as the UK ICorr/CCEJV representative. This was a tremendous opportunity for interaction with cathodic protection engineers and manufacturers from around the world. Regrettably, after much good work, NACE and ICorr parted company in 1988 and the CEA became the Corrosion Engineering Division of ICorr.
I also became the representative for Pipeline Industries Guild and the Institute of Petroleum on the BSI CP GEL 603 committee in 1985 which was revising the UK CP bible, BS CP1021. This was eventually published as BS7361 in 1991. In 1993 I was elected to chair this committee, a post I held for the next 19 years, coordinating the UK input into numerous BS/CEN CP standards prepared and published during this time.
Apart from the BSI committee, I also became involved in various ICorr committees and Council:
• Member of Council 1998-Present.
• Chair of Professional Assessment Committee 1998 – 2012.
• Chair of CP Certification Sub-Committee 2006-2019.
• Chair of Course Approvals Board 2013-2019.
• Member of CP Governing Board (2002- 2020).
• Member PDTC Committee (1998-2020).
• QA Advisor attaining ISO 9001 Certification.
• ICorr Representative for UK to CEOCOR (2008 – 2012).
• Professional Affiliate Engineering Council Coordinator with Society of Operations Engineers – current role.
• Primary author/updater of 5 ICorr CP training Courses to ISO 15257 for On-land and Marine Structures.
As a result of these activities, I was awarded Honorary Fellow Member of ICorr in 2018.
One of the other milestones in my career was attaining Professional Affiliate Status for ICorr with the Engineering Council. This was followed by the setting up a Registration Agreement with the Society of Environment Engineers enabling suitably qualified and experienced members to apply for registration with the Engineering Council as a CEng, IEng or EngTech. Having set the system up, I thought I should be the guinea pig to try it out. My application was successful and I was awarded CEng. With the demise of SEE, I set up a new Registration Agreement with the Society of Operations Engineers.
As a result, more than 50 of our members have become registered as Chartered Engineers – a tremendous benefit available for our professional members.
In Conclusion
As I look back over the last 50+ years, I can reflect on the many good memories of a varied career, the many friends and colleagues I have worked with and the opportunities I was given to expand my knowledge. I have tried to put back some of this for young engineers to consider that a career in CP can be very interesting and rewarding. To be honest, I still get satisfaction from it and in retirement, I am still dabbling, doing some CP design appraisals/approvals. A long and interesting, satisfying career in CP is very achievable albeit with a lot of hard work.
David Harvey CEng, FICorr(Hon)
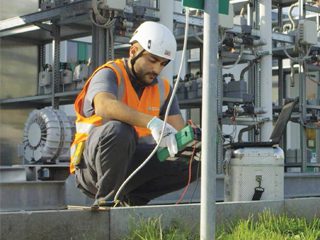
A Cathodic Protection Engineer at work.
Fellows Corner
Carbon steel is widely used a construction material of choice for buildings due to its inherent strength. Steel columns, trusses, girders and beams are the critical building components, failure of which usually leads to progressive collapse of the local and global structures. However, steel has high thermal conductivity which can cause it to lose its structural strength and stiffness as temperature increases. Expansion can also occur.
A non-uniform temperature distribution leads to thermal curvature. Any resistance to free movement of axial thermal expansion will induce internal stresses within the steel member making it frangible. The steel critical temperature for fire protection is the temperature that can cause structural collapse in a fire, and is often taken as 538 °C, as per ASTM E119, which corresponds to the point where it loses 50% of its load bearing capacity.
It is important to understand its mechanical and physical properties to understand how temperature affects steel. The melting point of steel is 1540 °C. Critical temperature is 720 °C, at 538 – 566 °C, carbon steel only retains about 50% of its yield strength. Steel can regain 100% strength if temperature does not exceed 720 °C.
Typical grades of structural steel are A36, A572, A588 and A514. They have yield strengths of 33000-35000 psi, and tensile strength 360000-70000 psi.
Rapid cooling of the steel elements heated between 704 and 843 °C during firefighting operations can also lead to some of the steel microstructure transform into martensite which increases hardness, but introduces brittleness. Below this temperature this transformation does not occur.
The purpose of PFP is to slow down propagation of heat to the structure bearing materials, e.g. steel beams and columns, to give time to evacuate the building before any catastrophic collapse of structural components could occur. Typically, the PFP materials are designed to withstand up to 2 hours of fire exposure per BS 476: Part 21, AS1530 Part 4, and up to 3 hours per ASTM E119 for intumescent products and up to 4 hours for cementitious products.
Most of the PFP materials used can be broken down into the three main categories:
• Cementitious products
• Mineral and fibre board systems
• Intumescent coatings
Cementitious products include cement and concrete, as well as lightweight materials such as mineral fibre, vermiculite or perlite. These products have relatively low thermal conductivity slowing the transmission of heat to the underlying structural steel. Lightweight mesh reinforcement may be required to increase durability for the structures subject to vibration or where mechanical damage is likely.
Fire protection boards are mineral boards (i.e. made of calcium silicate or calcium sulphate) reinforced with fibres and fillers, and can be further optimised for durability, e.g. resistance to humidity and freeze-thaw. The boards are manufactured in the controlled environment at a factory with strict tolerances and measurements. They require extensive supporting constructions, e.g. noggings, and require glue, staples, nails, etc. to be held together. It is typically easy to inspect their quality of installation.
Intumescent (which means “swell up”) coatings are composed of inorganic components contained in a polymer matrix: a combination of an acid source (ammonium phosphate, APP), a carbon source (pentaerythritol, PER) and a blowing agent (melamine). At the early stages of a fire, a large amount of thermal energy is absorbed by the coating, whose temperature increases rapidly. When the temperature of the coating reaches a critical temperature, the polymer matrix melts and degrades to form a viscous fluid. The inorganic acid source in the coating undergoes thermal decomposition normally at temperature of 100-250 °C. At temperature 280 – 350 °C, the blowing agent within the coating decomposes to release large amounts of gas of which some fraction is trapped within the molten matrix. The molten fluid hardens and releases residual volatile to form char. Convective currents are suppressed, and the thermal radiation does not have a “direct” path through the char to the substrate. This behaviour is complex and until now no agreeable model is available to simulate it.
Intumescent coatings are lightweight and can be applied in relatively thin coats. Other advantages include attractive appearance, and small volume occupation. They can easily follow the geometry of structural steel and are generally of relatively low cost. Intumescent coatings can be applied by airless spray, roller or brush, and cure and dry rapidly. Standard QA/QC requirements apply for surface preparation, application and inspection. Workshop application of these coatings has the advantage of better controlled application conditions. However, any structural materials with pre-applied intumescent coatings require careful transportation to minimize damage in transit.
Fireproofing coatings are tested for durability using time-temperature curves in accordance with UL 1709 for hydrocarbon fire exposures. ASTM E-119 is no longer used, as it does not adequately represent the fire exposure experienced in oil and chemical facilities. ASTM E-119 time-temperature curve however can still be used for non-hydrocarbon fires.
Dmitry Sidorin
Fellows Corner
This series of articles is intended to highlight industry wide engineering experiences, practical opinions and guidance, to allow improved awareness for the wider public and focused advice to practicing technologists. The series is written by ICorr Fellows who have made significant contributions to the field of corrosion management. The articles in this issue feature contributions from Bijan Kermani and Dmitry Sidorin.
An overview materials optimisation in CCS
A net-zero energy system to hinder or mitigate global warming driven by burning fossil fuel requires a step change in the way energy is being produced and used. This can only be achieved with a broad suite of technologies including improved energy efficiency, introduction of renewable energy and nuclear power. No mitigation option alone will achieve the desired reduction targets, however, they can be made
more influential when complemented by carbon capture and storage
(CCS) process.
CCS with sequestration can contribute both to reducing emissions and to removing CO2 to balance emissions – a critical part of “net” zero goals. CO2 sequestration is a process by which CO2 is removed from the atmosphere and stored indefinitely in underground locations primarily by means of pipelines. In addition to political and environmental incentives, CO2 sequestration is being considered in tertiary recovery for enhanced oil recovery (EOR) to produce residual hydrocarbon. Many oil and gas operators are looking at materials optimisation for such applications.
This Fellow’s Corner combines current status of corrosion threats and materials options for CO2 pipeline transmission and includes a simple roadmap enabling materials optimisation and outlining any technology gaps that may exist. It starts by describing sources of CO2, means of capture, methods of transportation and sequestration.
Sources of CO2, Capture and Sequestration
CO2 emission arises primarily from human activity and mainly from the combustion of fossil fuels used in different industrial sectors. CO2 is also emitted during certain industrial processes like cement manufacture or hydrogen production and during the combustion of biomass.
The first step in sequestration is CO2 capture. This is done through potentially numerous schemes, some commercially available at present, but all with a significant cost penalty. Capture from the atmosphere is done through biological, chemical or physical processes. The capture system may conveniently be divided into three categories (i) post combustion capture (scrubbing), (ii) pre-combustion capture and (iii) oxyfuel capture, details of which are beyond the scope of the Fellow’s Corner.
Having captured CO2, it needs to be transported and stored for long periods. This can be achieved by sequestration, a process by which CO2 removed from the atmosphere is injected and stored indefinitely. There are currently more than 70 CO2 injection projects in the US, injecting more than 35 million tons of CO2 annually, primarily for EOR.
Briefly, sequestration methods includes (i) geological sequestration, (ii) CO2 EOR, (iii) deep ocean sequestration, (iv) mineral and biological sequestration and (v) terrestrial sequestration again, details of which are beyond the scope of the Fellow’s Corner.
While CO2 has been injected into various geologic formations for decades for EOR purposes and acid gas disposal, the idea of permanent CO2 storage, or sequestration, for the purpose of mitigating global climate change is a fairly novel one with few commercial-scale prototypes upon which to draw guidance in the development of a regulatory framework.
Means of Transportation
Once captured and compressed, CO2 must be transported to a long term storage site as schematically shown in Figure 1 (below). In principle, transmission may be accomplished by pipelines, tankers, trains, trucks, compressed gas cylinders, as CO2 hydrate, or as solid dry ice. However, only pipeline and tanker transmission are reasonable economical options for the large quantities of CO2 associated with, for example, a 500MW power station. Trains and trucks could be used in the future for the transport of CO2 from smaller sources over short distances.
Pipelines
CO2 transmission by pipeline and injection into reservoirs began several decades ago. More than 40 million tons per year of CO2 are currently transmitted through high pressure CO2 pipelines, mainly in North America. Most of the CO2 obtained from natural underground sources is used for EOR.
The Weyburn pipeline, which transports CO2 from a coal gasification plant in North Dakota, USA to an EOR project in Saskatchewan, Canada is probably the first demonstration of large-scale integrated CO2 capture, transmission, sequestration and storage.
Ship Tankers
Ships are now used on a small scale for the transport of CO22 . Large scale transport of CO2 from power stations located near appropriate port facilities may occur in the future.
CO2 would be transported as a pressurised cryogenic liquid, for example at approximately 6 bar and -55°C. Ships offer increased flexibility in routes, avoid the need to obtain rights of way, and they may be cheaper, particularly for longer distance transportation. Ships similar to those currently widely used for transportation of liquefied petroleum gas (LPG) and liquefied natural gas (LNG) could be used to transport CO2.
Corrosion Threats and Severity
Dry CO2 is non-corrosive and relatively easily handled using conventional grades of carbon and low alloy steels (CLASs). However, in the presence of water, the situation is more complicated and system corrosivity would depend on water solubility of the CO2/H2O mixture and therefore, materials used in CCS systems can be subject to corrosion threats in which materials optimisation can take a centre stage.
CO2 readily dissolves in water to form carbonic acidic solution that is highly corrosive to many engineering materials. The accelerating effect of CO2 corrosion is a particularly important safety issue when considering the maintenance schedules and operating life expectancies for pipelines that were not originally designed for CO2 transmission use. Choice of materials for handing CO2 is governed by many parameters including physical state of CO2, water content, its purity and level and nature of impurities.
An additional complicating parameter is the presence of H2S and other potential impurities. A limit on the concentration of H2S is important for two complementing reasons including (i) the likelihood of exceeding sour service limits of materials and (ii) as H2S and O2 may lead to the formation of elemental sulphur which makes system corrosivity even more complex. It should be noted that the presence of small amount of water leads to increasing the iron concentration and pH which results to a low corrosion rate. However, this is difficult to predict and quantify.
High levels of CO2 in the CCS process places the operating conditions beyond the limits of existing CO2 corrosion predictive models and in majority of cases application specific testing may be required. Nevertheless, published data by Institute for Energy (Norway) and Ohio University (USA) indicates that in a condition where CO2 is more than around 50 bar, corrosion rate of CLASs can be estimated to be around 1/10 that predicted by conventional corrosion prediction models.
Materials Optimisation Guidelines
The first step in a systematic materials optimisation process, is to explore the feasibility of using CLAS as it offers satisfactory mechanical properties and economy, although has poor corrosion resistance. System corrosivity assessment therefore is necessary to establish the likelihood of success in using CLASs an area in need of fine tuning. Here a broad guideline is given for handling CO2.
CO2 Only
CO2 can exist in variety of physical states depending on the temperature and pressure. The physical state of CO2 and respective approach to materials selection for CO2 transmission in form of a guideline is shown in Figure 2. The guideline is divided into five conditions depending on the physical state of CO2.
The guidelines in Figure 2, excludes the effect of contaminants (H2S, O2, SOx) and applicability limit for H2O as there are no systematic data on these parameters.
It is apparent that successful utilisation of CLAS is highly dependent on the absence of water and other impurities in which thermodynamic analysis to confirm absence of water throughout the pipeline or tubing over the operational life is essential.
CO2 and Oxidizing Agents
CO2 transmission in the presence of oxidizing gases such as SO2, SO3 and O2 becomes even more complicated. Again in the absence of water, there is no likelihood of corrosion. However, in the presence of water, a combination of oxidizing species (SO2, SO3 and O2) and acidic gases (CO2 and H2S), likelihood of corrosion becomes a serious issue. In such situations, a more prudent approach should be adopted and thermodynamic analysis to ensure lack of water throughout the system and design life becomes even more essential. In practice, injection of CO2 with oxidizing agents should not be contemplated unless proven otherwise. The option is to either remove the oxidizing agents, implement total dehydration or the use of an appropriate grade of corrosion resistant alloy (CRA).
References
1. B Kermani and D Harrop, Corrosion and Materials in Hydrocarbon Production; A Compendium of Operational and Engineering Aspects, Wiley, 2019.
2. Carbon Capture, Transportation, and Storage (CCTS), Aspects of Corrosion and Materials, ed B Kermani, NACE International, 2013.
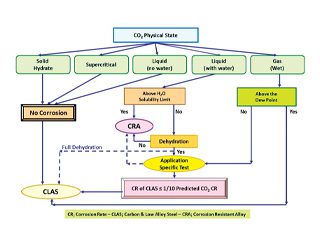
Figure 2 – Materials option guideline for CO2 sequestration.