Fellows Corner
In this issue, we have three articles from experienced Fellows who have made a significant contribution to the understanding of corrosion and its prevention. The first follows on from the topic in the last issue, where Brenda Peters discusses the application of protective coatings, and what needs to be done beforehand. Secondly, Joseph Itodo Emmanuel describes the corrosion protection of buried structures, and finally James McLaurin explains how the design of a steel structure can influence its protection, specifically from bi-metallic corrosion problems.
Corrosion protection by protective coatings
The institute of Corrosion is split about 50:50 between Engineers and Scientists, and across several different disciplines, the common ground is in Corrosion Prevention, and there are many overlaps within the fields of expertise. Following on from the Fellow’s Corner column in last issue of Corrosion Management, the emphasis of this article is on paint as a means of corrosion protection. Paints generally falls into two categories, decorative and industrial (protective), and paint manufacturers have tended to split their manufacturing and R&D, specialising in one or the other. However, decorative paint can be protective and industrial paint can be decorative. When we talk about “Industrial” or protective paints, we are usually referring to the prevention of steel from rusting. These paints are the most sophisticated technically engineered paints, but they tend to be applied by the least qualified painters. This is why the Correx ICATS (Industrial Coating Applicator Training Scheme) programme was developed to improve the quality and longevity of the finished product. In addition, many manufacturers will run their own training schemes on how their particular product should be mixed and applied and the limitations of the ambient conditions. Paint inspectors are also employed to ensure that the paint is stored and applied correctly, and the surface preparation is to the specified standard. These paint inspectors are normally trained by ICorr or NACE or both, so what can go wrong?
When applying paint to new steel a primer coat is applied to promote adhesion and protect the surface against corrosion, however preparation of the steel prior to painting is paramount. When investigating paint failure, it is a bit “chicken and egg”, did the steel corrode and push off the paint or did the paint fail allowing the steel to corrode.
When the steel leaves the mill, it will have some level of millscale on the surface which is blue/black in colour, although this surface can look nice and smooth and suitable for painting, this millscale is however only loosely adhered to the underlying steel, and will scale off after painting. This can often be seen on hand rails and post made from tubular steel which has not been blast cleaned.
To prepare steel for painting, several methods can be used, which depend to an extent on the end use of the material, for example, steel can be pre-treated to inhibit rust and passivate the surface: examples of which are in hot dip galvanising, where the steel is “pickled” in acid to remove rust and millscale then immersed in a vat of molten zinc, which forms layers of zinc alloys at the interface with the steel, culminating in a layer of pure zinc on the surface, and this can be difficult to paint as it is smooth and can result in poor adhesion. It can be left to weather so that zinc oxides form on the surface resulting in roughening which provides a key for the paint to adhere to, or alternatively a variety of primers are available which etch into the surface. These include, acid etch epoxy primers and more the commonly used “T Wash”, a mordant solution originally developed by British Rail, which is a phosphoric acid solution containing alcohol and copper carbonate as an indicator. The solution reacts with the surface of the zinc and a black coloration is formed, anywhere it doesn’t react and show this colour change can indicate previous contamination on the galvanising and these areas need to be washed, degreased and retreated.
Steel can be treated with hot metal spray (Thermal Spray) as an alternative to hot dip galvanising creating an anti-corrosive layer with a profiled surface to which paint can be applied. This is normally zinc or aluminium and is often used for high temperature conditions.
Similarly, steel can be “phosphated” by dipping in a bath containing a solution of zinc in phosphoric acid forming a thin layer of zinc phosphate on the surface, and which is commonly used in the automotive industry. This can then be undercoated and a decorative finish coat applied on top. The paint can be applied electrostatically in a powder or liquid form then heat cured or applied by spray, roller or brush.
However, in the heavy duty protective coatings field, steel supplied from the factory has to be blast cleaned to remove all millscale and rust, and then primed within a short period of time to prevent flash rusting from forming on the surface. Epoxy primers are commonly used, but these need a good steel surface profile to form a key to ensure good adhesion, so the profile of the blasted steel needs to be checked before application of the paint. As epoxies cure by chemical reaction, they will continue to cure over time until they become fully cross linked, and at this stage they become unsuitable for overcoating, so the manufacturers’ overcoating times must be adhered to enable the following coats to adequately bond with the surface of the epoxy. If the overcoating time is exceeded, these coats will eventually lose adhesion at the interface with the epoxy, and detach. Epoxies, like most protective coatings, are also sensitive to ambient conditions, they won’t normally cure if it is too cold, and if there is any condensation on the steel, or if they get wet before they cure can prevent them from curing properly. For example, with amine cured epoxies, the amine can react preferentially with moisture resulting in undercure, and if moisture gets on the surface before they
are fully cured, amine bloom can occur resulting a dull and chalky surface. Therefore, attention to temperature and dewpoint are very important. Epoxy coatings have been developed which are moisture tolerant and some can even be applied underwater and are utilised for subsea repairs.
When epoxy primers are used then these need to be finished with a decorative acrylic or polyurethane top coat as these are UV resistant – epoxies yellow with sunlight and colours fade through chalking. Acrylics retain their colour longer. Similarly, for alkyd based systems, urethane alkyd top coats are used as these are tougher and have greater longevity.
Historically red lead primers were used, although these were phased out in the late 1960s due to toxicity and leaching they can still be found on many steel structures, and cause problems when it comes to maintenance (full containment and special disposal are necessary). These have been replaced by zinc rich or other anticorrosive primers.
Similarly, some steel structures have existing coats of chlororubber or acrylated rubber, which have good corrosion resistance and longevity. However, these can also pose problems during maintenance painting, as they are incompatible with solvent based coating like epoxies, and cannot be refurbished with anything else.
Whichever paint system is chosen it is advisable to use material supplied by the same manufacturer as these are developed to be compatible with each other, and if a failure should occur then there is less anomalies to be considered. Manufacturers will offer a full paint system with primers undercoats and finish coats, for a specific end use.
Brenda Peters
Fellows Corner
In this series of articles by practitioners who have made a significant contribution to the field of corrosion protection, the editor discusses paint technology.
Over the past 18 months this column has concentrated on topics relevant to the corrosion engineers, however, there is a need to address the part that protective coatings play in the corrosion protection of structures. In an attempt to address this imbalance, this issue will feature an introduction to paint technology, and how protective coatings fit into the overall corrosion protection scenario.
Paints and coatings are used to protect and decorate, however, before we consider the properties of paints and how they work, it is necessary to consider “what is a paint”.
All liquid paints are composed of three basic ingredients, resins, pigments and solvent. The resin is the film forming portion of the paint – it holds together the pigment particles and binds the paint to the surface. The resin plays the main part in contributing to the durability, strength and chemical resistance of the final film. Paint types are often referred to by the type of resin in the formulation, so when we talk about an alkyd or epoxy for example, we are referring to the main resin used to make the paint.
The second ingredient in a paint is the pigment. This is a relatively insoluble finely divided powder, or more commonly a mixture of powders. The pigment(s) primarily provide hiding power (opacity), and colour, but they also improve corrosion and weathering resistance, increase paint adhesion, decrease moisture permeability and control gloss. The final ingredient, the solvent, “carries” the resin and pigment(s) and controls the viscosity, such that the paint can be applied to a surface. The chemical ingredients in each of the components vary widely from one generic type of paint to another, in addition each of the components (resin, pigment and solvent) are also usually mixtures of different materials. For example, a paint formulation may contain three or four solvents – one solvent dissolves the resin, while some are used to control evaporation, and others are used to dilute the solution (control viscosity). It is not important for a user to know all the ingredients in a paint, suffice that he knows the properties.
The words, paint and coating, are used interchangeably – they mean virtually the same thing. However, it is necessary to distinguish between a coating system and a coat of paint. A coating system is more than just the material applied, it also refers to other factors such as the surface preparation requirements, the application of a number of coats of paint, in a specific order, and the thickness of each coat of paint. A coat of paint is a single layer, applied to form a coherent film when dry.
The common designation of a series of coatings applied to a surface is primer, intermediate or build coat, and top coat. Normally each coat contains properties that contribute to the success of the total coating system.
Function of each coat
The primer is the first coat applied to the surface. The main function of the primer is to provide adhesion to the substrate – if the primer doesn’t stick, then the whole coating system will fail. The primer also provides a key for the rest of the system.
The intermediate coat is required in many coating systems to provide one or more of the following functions; increase film build, improve chemical resistance, or serve as an adhesion or tie-coat between primer and topcoat where they are not compatible.
The topcoat is intended to be the last coat applied. This provides the weather and/or chemical resistance and also imparts characteristics such as colour, gloss wear resistance, abrasion resistance.
Considering the two main reasons for painting – protection and decoration, this article will concentrate on the protection properties. A paint can protect against, amongst others, abrasion, chemicals and fire, but probably the most common protection use is to prevent corrosion of steel.
There are three recognised ways that coatings protect steel against corrosion, providing a barrier, inhibition and sacrificial action.
Barrier protection is just as the name implies, the dried paint film blocks moisture from reaching the steel surface. All coatings do allow moisture and oxygen to penetrate them to some extent, this is called permeability. Coatings which protect by a barrier mechanism have very low permeability. Typical barrier coatings are 2-pack epoxies and polyurethanes, although there are additives which can reduce permeability further (see below).
Coatings that protect by inhibition contain active pigments to inhibit or interfere with the corrosion reaction on the steel surface. Typical traditional inhibitive pigments were lead compounds and chromates. However, concerns about toxicity and environmental pollution have led to their replacement with so called non-toxic anticorrosion pigments such as phosphates, and many proprietary materials. As moisture passes through the film, the anti-corrosive pigments slowly dissolve and depending on their chemistry interfere with either the anodic or cathodic reaction and thus retard corrosion.
The third mechanism is sacrificial action and is the way that zinc rich primers protect steel. These primers are highly loaded with zinc, such that the zinc is in contact with itself and the steel surface. As zinc is more active than steel, and if the elements necessary for corrosion are present, then the zinc will corrode in preference to the steel (i.e. sacrifice itself), and hence protect the steel. Zinc rich paints are classified into two types, inorganic and organic. This classification refers to the resins used in the formulation and not the form of the zinc. The binder (resin) in inorganic zinc rich coatings is a form of silicate, and organic zinc rich paints are nowadays typically epoxy based.
Returning now to the paint system. This is designed to give optimum protection to the steel or metal substrate by combining the properties of the various coats. Thus for very long term protection, an inhibitive primer, or more particularly a zinc rich primer, would be combined with a barrier intermediate coat and topcoat. In this way, two protective mechanisms are used to give long life protection.
The permeability of a paint and hence its barrier properties are related to the resin used, with oleoresinous and alkyd paints having high permeability and epoxy and polyurethanes having lower permeability due to their highly cross-linked structure. Within each generic class of paint, permeability can be further reduced by formulation, and in particular the use of plate-like pigments such as micaceous iron oxide (MIO) and aluminium flakes. These special pigments orientate themselves parallel to the surface when the paint dries and provide an extremely low permeability film (they effectively increase the path length moisture has to take to reach the metal surface). In a similar manner, permeability can be reduced by increasing film thickness although there is a limit to this before other properties start to suffer.
No matter which type of paint is used, if proper surface preparation is not carried out then vastly inferior performance will be obtained. Surface preparation is essential in two important areas, it provides an anchor for the coating and it allows intimate contact between the coating molecules and the metal surface, and this will be the topic
for a future column.
Fellows Corner
Non-metallic materials are an essential element of facilities engineering in upstream E&P operations, being widely used in a range of functions from seals and corrosion barriers to piping and structural elements. This short article offers a brief insight into the capabilities of some of the available options.
In common with metallic materials, the selection and successful use of non-metallics is dependent on a detailed understanding of the way in which each material responds to the service environment over the life of the component, or system. Degradation of the capabilities of non-metallic materials can occur through a range of physical and chemical processes.
Elastomers (or rubbers), are widely used in oilfield sealing applications. These are highly elastic, polymeric materials, used in compression seals in a range of downhole, subsea, topsides and pipeline applications. Various nitrile and fluorocarbon-based materials are typically used to span the range of temperatures, pressures and fluid environments, met in oilfield operations. Processing of these materials involves “vulcanisation” or curing, using small amounts of sulphur, amines or peroxides to create highly flexible and extendable polymers.
A number of key failure modes can affect elastomer seals. Some relate to the elastomer material being used outside its working temperature range, or in fluids with which it is incompatible. This can lead to chemical embrittlement, softening, compression set, large volume changes, and loss of elasticity at low temperature – any or all of which can lead to a seal failing. Pressure related failure modes can also be important. Extrusion damage occurs when a rubber seal is forced into the gap which it is sealing as a result of the applied pressure. Gas decompression damage occurs primarily in dry gas duty, being qualitatively similar to the “Bends” suffered by divers when returning to surface.
Qualification of seals and the material’s performance in any component or system, is typically carried out using a combination of materials and system testing, taking account of the time and temperature dependent properties of the materials involved. Finite element analysis (FEA) modelling of the complex, non-linear and time dependent materials properties of elastomers has proven vital in understanding some applications.
Further applications of a range of elastomer materials are to be found in hydraulic and transfer hoses, and in the flexible joints that are incorporated in metal drilling and catenary risers.
Thermoplastic materials, such as polyethene and nylon, find wide application in controlling the internal corrosion of steel pipelines. Such materials are fundamentally different in nature to elastomers, having a much smaller elastic range, and the way in which they are used is therefore somewhat different. As their name suggests, these materials are reversibly melt-processible, often being formed by extrusion for oilfield use. Materials are typically differentiated by their maximum service temperature capabilities, and their resistance to particular service fluids. So, for example, polyethylenes are typically used in water duties to a maximum of 60°C or so, while nylons can be used in hydrocarbon production service up to 90°C.
Thermoplastic liners have an extensive track record, both onshore and offshore, in providing a corrosion barrier within carbon steel pipelines, particularly for water injection service, where suitable metallic options are typically much more expensive or much less reliable. There are a number of “pull-through” liner technologies which can offer cost effective solutions to mitigate internal corrosion challenges in both new build projects and in rehabilitation. Often these involve “tight-fit” polyethylene liners, which have their outer diameter mechanically reduced, while they are pulled into a steel pipe. Release of the pulling force allows the polymer to relax back against the internal diameter of the pipe, which remains the structural element of the pipeline. Another option is the use so-called Reinforced Thermoplastic Pipes (RTPs) which are used, with good economic benefit, as loose fit, “slip liners” or even as stand-alone pipelines, in a range of production and injection services. These are composites in which glass, aramid or carbon fibre, or wire, reinforcement, is wound over a plastic pipe, in order to increase its pressure capability.
Thermoplastic materials additionally find wide application in unbonded flexible pipes, importantly being used as the internal and external sheathes in these complex pipe structures. The flexibility of these pipes often enables faster or more convenient offshore installation and hook-up, and provides excellent fatigue resistance in a range of harsh environments. Several thermoplastic materials are used as internal pressure sheathes, responsible for primary containment. Nylon materials are widely used in production service up to 60 – 90°C, with fluoropolymers used at high temperature, to around 130°C. In water injection, polyethylene is normally used. External, or outer, plastic sheathes contain the whole pipe structure, helping to keep the high strength steel wire reinforcement out of contact with seawater. Typically, this sheath is made of polyethylene for static pipes and nylon for pipes used in dynamic service.
Thermosetting materials, such as epoxy and phenolic resins, form the basis of a further set of related oilfield corrosion protection technologies. These materials employ a chemical hardener to permanently, and irreversibly, “set” the polymeric resin, often with temperature applied during curing to accelerate that reaction.
Fusion bonded epoxy (FBE) is used very widely as an external pipeline coating. It is applied as a powder to a carefully prepared surface, and melted and cured in situ to give a coating approximately 0.5 mm thick.
FBE also finds wide use as the base layer in multilayer coatings with polyethylene and polypropylene. Further, options for subsea insulation involving the incorporation of glass microspheres into thermoplastic layers are also widely accepted, for use on subsea pipelines. The thermoplastic nature of these materials allows the pipelines to be reeled for transport and installation, where required. Where more rigid insulation is acceptable, systems incorporating glass-microspheres into epoxy resins can be applied, for example to subsea manifolds.
Epoxy resins, and similar materials such as vinyl esters, find wide use in the painting and external protection of structures and equipment, as well as in the internal coating of vessels, typically in combination with glass flake fillers.
Glass reinforced epoxy pipes find a range of downhole, piping and pipeline applications, mostly in water service. Typically, this kind of pipe is rated to 16 bar design pressure, although some small diameter products can go much higher than this, for example in downhole tubing applications. A range of adhesively bonded, mechanically jointed and threaded connections are used across the industry. Qualification of composite pipes, and other non-metallic pipe options, is normally undertaken through a series of full-scale pipe tests, including: pressure rating using long term (10,000 hr) testing of pipe and end fittings, characterisation of minimum bend radius for storage, transportation and operation, characterisation of axial load capability, testing of capability of the product to handle gas service, and performance of the product in UV. A range of other engineering design issues also need to be worked through with each product, such as internal surface roughness, heat transfer co-efficient, and pipe expansion due to pressure and temperature.
Glass reinforced epoxy pipes can also be used as a liner, with composite lined downhole tubing having a long track record of successful onshore use in a range of corrosive services, and in offshore water injection. Some composite liners are capable of continuous service at up to 80°C in water-based applications. Insertion of the stiff liner into the steel host, on a joint-by-joint basis, leaves a small annulus between the liner and the host which is typically filled with cement, to transfer mechanical and pressure loads to the carbon steel host. Modified tubing connections allow the liner to be properly terminated, with thermoplastic corrosion barriers providing continuity of corrosion performance.
Finally, it is worth mentioning the use of external epoxy composite wraps to repair and reinforce topsides piping. This is a very convenient repair technology that does not involve hot work and which can be used to seal thinned, cracked or holed piping, at very least as a temporary solution until full repair can be affected.
The use of non-metallic components is an integral part of the materials selection challenge in oil & gas production. Given their frequent role in maintaining a primary or secondary containment, selection and use of these materials should be as carefully scrutinised as with the metallic components within any well, processing facility or pipeline.
For additional information see, B Kermani and D Harrop, Corrosion and Materials in Hydrocarbon Production; A Compendium of Operational and Engineering Aspects, Wiley, 2019, Chapters 9 & 15.
Fellows Corner
In this series of features from ICorr Fellows who have made significant contributions to the field of corrosion protection, Malcolm Morris discusses the use of Thermal Sprayed Metal Coatings.
An Introduction to Duplex Thermal Sprayed Aluminium (TSA)
Thermal metal spraying is a process by which a steel substrate is protected from corrosion by coating with atomised particles of softened or molten metal. The most commonly applied metals used for this process are aluminium (TSA), or zinc (TSZ), however any metal which is ductile and able to be produced in a wire form can be thermally sprayed, (e.g. tungsten, molybdenum, lead, and even silver or gold), plus combined alloys of zinc and aluminium.
The most common methods of application are:
Gas Applied: A process in which a coil of metal wire is fed to the tip of an application gun, where the metal is melted by a gas flame, and the molten metal is simultaneously atomised by compressed air jets and directed onto the substrate.
Arc Applied: Similar to gas applied – Arc spraying is performed by feeding two electrically conducting metal wires towards each other. An electric arc is produced at the point just before the wires meet. The arc melts the metal wires, and a high-pressure air line is used to atomise the molten metal into fine droplets which are sprayed onto the previously cleaned and prepared steel surface. Arc application gives faster productivity compared to gas application.
Thermally sprayed surfaces have historically been supplemented with protective coatings, in order to increase the level of protection, and also as a cosmetic coat to mask the appearance of the corrosion products of the metal spray, which appear as aesthetically poor, white salt deposits. Paint systems range from a relatively thin single coat (designed to fill and seal the porous voids in the film, which naturally occur in the application of the metal spray), to multi-coat high build systems which are intended to significantly extend the service life of the structure.
A common feature of all thermal spray coatings is their lenticular or lamellar grain structure. Due to the nature of the application, the molten metal cools and solidifies instantaneously upon impact with the substrate, forming a porous matrix of flattened metal particles, interspersed with inclusions of metal oxide and unmelted metal. This porosity is sealed by normal ageing, through formation of salts of the component metals (oxides, hydroxides, carbonates, etc.), or as stated above by sealing, and or, painting.
The correct surface preparation is essential, involving cleaning followed by grit blasting to preferably white metal, Sa3 (BS EN ISO 8501-1), with a surface profile of at least 75µm. This provides the chemically and physically active surface needed for good bonding of the sprayed metal.
Both zinc and aluminium are anodic to steel. Zinc affords greater electrolytic activity than aluminium, providing good galvanic protection to steel exposed in the atmosphere. Breaks in the coating are protected by the galvanic couple, i.e. the zinc corrodes, rather than the structural steel, and its’ corrosion products will self-seal the breaks in the coating.
Aluminium is less active than zinc. Aluminium’s protection of the substrate relies more on a thin oxide passivating film at the surface, however because aluminium is less active than zinc, it cannot protect breaks in the coating.
It has been reported in the literature that the maintenance-free service life of an unprotected aluminium alloy metal spray coating on a typical bridge was predicted to be 25-40 years. Using a sealer and topcoat over the metalised layer is predicted to extend the service life 15-20 years [1]. Also, testing at SINTEF, Norway, in natural seawater, gave free corrosion rates of 2 to 3 microns per year after 11 months of exposure for both Al and Al 5% Mg. This would imply a service life of 60 years for a 200-micron Thermal Sprayed Aluminium Coating [2].
TSA with a single coat of sealer has a track record stretching over several decades, however the disadvantage of this system is the dull, rough appearance of the metal spray. Since the sealer is only applied as a thin coat, it is not possible to enhance the surface appearance, and the corrosion products of the metal spray may become obvious within a short period.
This led to the application of a high-performance paint specification on top of the metal spray in order to enhance its durability, and these so-called duplex systems have been used extensively, based on both TSA and TSZ processes. TSA based systems were specified in the Norwegian Offshore sector, with TSZ used widely on structures such as road bridges.
TSZ systems have performed very well over extended periods (up to 30 years), however TSA duplex systems began to display signs of premature breakdown of the coating system, coupled with extensive degradation of the metal spray coating. Examples of such breakdown included Hutton TLP, Sleipner Raiser Platform, Troll A platform, and at the Troll plant at Kollsnes.
Thermal metal spray coatings have a long service track record in the petrochemical and marine sectors listing advantages such as:
- Limited maintenance
- Low service life cost
- Superior adhesion
- Resistant to mechanical damage
- Self-healing
- No drying or curing time
- Wide range of operating temperatures: -45°C to 538°C
Research was carried out with a series of panel exposures using both gas and arc applied TSA, plus TSZ. These metal sprayed substrates were sealed with a selection of different sealers, and then overcoated with a medium build epoxy MIO/polyurethane specification, and also a high build glass flake epoxy. Panels were immersed in salt water and fresh water, plus natural weathering in both industrial and marine environments.
The results of this series were quite startling. After 24 months saltwater immersion severe degradation of all the paint systems over TSA was observed; with extensive degradation of the underlying metal spray. The large quantities of white aluminium corrosion products effectively blew off the paint system. No differences were observed between any of the different sealers, or between gas or arc applied TSA. All systems applied over TSZ were satisfactory on immersion up to 12 years salt water immersion. All fresh water and atmospherically exposed panels also performed well up to 12 years.
From this testing, it was evident that application of high build coating systems over TSA gives very poor performance when subjected to high chloride salt environments, such as hot salt spray or salt water immersion. The speed of the failure is variable, possibly depending upon the efficiency of the sealer coat, however the end failure effect is the same in all cases. Performance of the same specifications on natural weathering in an industrial C3 environment and fresh water immersion is generally good. Thermally sprayed zinc substrates perform well in all environments.
The definitive document on the theory of degradation of coating systems over TSA was published in 2004 by Torstein Rossland of Statoil [3]. The paper describes a number of system failures in the North Sea oil industry, and suggests the following mechanism for coating failure.
When the duplex coating is in galvanic contact with bare steel, galvanic corrosion of the thermally sprayed aluminium is initiated. Cathodic oxygen reduction takes place at the bare steel, while anodic dissolution of the thermally sprayed metal takes place under the organic coating.
In chloride containing environments, such as in marine atmospheres, chloride ions migrate under the organic coating to maintain the charge balance. Aluminium chloride is then formed.
This is highly unstable in the presence of water, reacting to form hydrochloric acid. The electrolyte under the organic coating will therefore be acidic. Cathodic hydrogen evolution will start under the organic coating, which will increase the corrosion rate of the TSA. The TSA will not be passive in the low pH electrolyte. Hence, the thermally sprayed aluminium corrodes actively and rapidly. The organic coating holds the aggressive electrolyte at the surface. TSA with only a thin sealer will not suffer from this type of degradation since the aggressive electrolyte will migrate out of the sealer.
The recommended treatment for pure aluminium metal spray in a high chloride environment would be to apply a thin sealer coat to fill the porosity in freshly applied TSA in order to prevent corrosion through the pores before the surface can self-seal naturally by weathering, and then protect the substrate from corrosion as intended.
It should be noted that thermally sprayed zinc, or aluminium alloys, do not suffer from the same problems when overcoated by high build coating systems in high chloride environments.
References
1) Journal of Protective Coatings & Linings, May, 1995.
2) Materials Performance, April, 1995. Authors: Karl P. Fischer, William H. Thomason, Trevor Rosbrook, Jay Murali).
3) Rapid degradation of painted TSA. Author: Torstein Rossland, (Statoil, Bergen, Norway ).
Fellows Corner
This series of features in Corrosion Management intends to highlight industry wide engineering experiences, practical opinions, and guidance, to give improved awareness for the wider public, and focused advice to practicing technologists. The series is written by ICorr Fellows who have made significant contributions to the field of corrosion protection through past industry involvements. Corrosion Management is pleased to publish this month’s contribution by Bijan Kermani, FICorr.
Metallic Materials for Hydrocarbon Production
Several categories of alloy are used in the energy sector, and in particular, in hydrocarbon production facilities, to enable successful and trouble free operations. The majority of the components of these facilities are manufactured from metallic materials, commonly carbon and low alloy steels (CLASs), which are readily available in the volumes required and able to meet many of the mechanical, structural, fabrication and cost requirements. However, the inherent corrosion resistance of CLASs is relatively low, and their successful application requires combination with one or more whole-life forms of corrosion mitigation against both internal and external exposure conditions, and/or the use of corrosion resistant alloys (CRAs).
The main materials used in hydrocarbon production fall broadly into three categories, ferrous, non-ferrous and non-metallic materials, in which ferrous materials covers three types, carbon steels, CLASs and CRAs, broad details of which are summarised in Table 1. This article briefly addresses only the ferrous materials, which are the essential materials of construction for CAPEX intensive items (tubular and pipeline), their ranges, examples, related standards and their resistance to principal types of corrosion threat in hydrocarbon production (metal loss CO2 corrosion. and resistance to sulphide stress cracking, SSC, in the presence of H2S). These are summarised and characterised briefly in Table 2 and are as follows:
CLASs: A wide variety of CLAS grades are used across this industry sector and are the principal materials of construction and the first, optimum, and base-case choice for many applications. They normally have low metal loss corrosion resistance. The most notable categories of CLAS according to the application include, structural services and pressure containment.
Structural Services
These commonly utilise “structural” steel products in the form of rolled plate, various sectional shapes and tubular sections, although cast or forged products may also be used. Typical applications include offshore structures, sub-sea module support frames, pipe racks, process equipment saddles and, in some instances, low criticality storage tanks. They contain Mn (typically 0.5 – 1.5%) and limited quantities of other alloying elements such as Nb, Ti and V. Structural Steels generally have adequate properties over a range of temperatures lying between approximately -50°C to +50°C, depending on the local environmental conditions, e.g. in arctic, temperate or tropical conditions. They are normally weldable and have a yield strength not exceeding 350 MPa.
Pressure Containment
C/Mn or lean alloy steels may be used for process plant, vessels, pipe work, pipe fittings and valve bodies requiring pressure containment. However, steels with an increased alloy content of Cr, Ni, Mo, so called low alloy steels, are employed to give mechanical properties suitable for a temperature range lying within the limits of approximately -80°C (characteristic of Joule Thompson cooling) to approaching 600°C (characteristic of a number of refining processes). Typical applications requiring pressure containment include drill pipe, casing and tubing, linepipe, process pipework, pressure vessels and heat exchangers. Generally CLAS has low resistance to metal loss corrosion while sour service grades have good tolerance to SSC.
While metallic materials used for subsurface applications (wells) are seamless with relatively high strengths (normally yield strength >500 MPa) and have no requirement for welding (threaded connections are used), other applications including, flowlines, topside/surface facilities and pipeline/trunklines require materials with the ability to be welded and normally have lower yield strength (not exceeding 700 MPa).
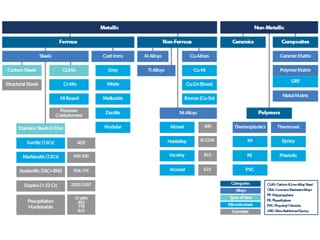
Table 1. Range of metallic and non-metallic materials used in the construction of hydrocarbon production facilities.
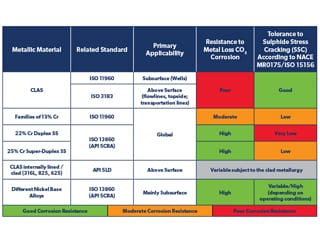
Table 2. Range of CAPEX intensive metallic materials (tubing and pipelines) and their relative corrosion performance.
The new generation of low Cr containing steels with 1 to 5%Cr offer slightly improved metal loss corrosion resistance, optimality for well completion applications.
CRAs: While CLASs, or in combination with corrosion prevention systems, may offer suitability for some applications, corrosion resistant alloys (CRAs) containing amongst other elements, Cr, Mo, N, W, Nb, Ni, Co have emerged as alternative more corrosion resistance choices. Increasing alloying elements invariably leads to increasing costs. Even though CRAs are more costly to procure in terms of CAPEX, they may offer more favourable whole life cost with lowering risk in terms of corrosion threats.
CRAs are primarily restricted for use in subsurface (well completion) and as internal cladding of manifolds and internal cladding of risers due to their relative cost. However, based on whole life cost comparison they may become economical for specific applications.
There are many categories of CRAs. These are generally divided into groups or families of alloys that have common characteristics or microstructures. These are summarised in Table 1 and include: 13Cr Steels. The family of 13Cr stainless steel (SS) exhibit good metal loss corrosion resistance with good strength. They contain 13%Cr and some other minor elements. A new generation of this family contains 15-17Cr, or alloyed 13Cr containing Ni and Mo, have improved metal loss corrosion and top temperature limit. They are primarily for subsurface applications, although weldable/lean grades are considered for infield flowline/pipeline applications. Generally, they have low resistance to sulphide stress cracking (SSC).
Duplex Stainless Steels
Duplex and super duplex SS derive their properties from the balance of phases between ferrite and austenite by the addition of Cr, Ni and Mo. They are designed to provide better corrosion resistance than the 13Cr families, particularly resistance against chloride pitting corrosion and they have higher strengths, although their tolerance to environmental cracking (EC) in the presence of H2S is low.
Other CRA
Other types of CRA include several categories of alloy containing varying amounts of Cr, Ni, Mo and other alloying elements, and also Ti alloys some of which do not fall into the ferrous category. These offer superior metal loss, corrosion, as well as tolerance to environmental cracking (EC) in the presence of H2S, chloride, and also when elemental sulphur is present. While some grades of Ti alloys have been successfully used in well completion (sub-surface), these are not covered in the present article.
Additional reading: B Kermani and D Harrop, Corrosion and Materials in Hydrocarbon Production; A Compendium of Operational and Engineering Aspects, Wiley, 2019.
Fellows Corner
The latest article from ICorr Fellows who have made a significant contribution in the field of corrosion control is by Dr Sadegh Parvisi, Senior Principal Materials Engineer, McDermott, who describes the role of a Corrosion, Materials and Metallurgy Engineer. With some decades of professional engineering experience in engineering companies, operations and R&D, the author now shares this experience with fellow workers in ICorr.
The role of the Corrosion, Materials and Metallurgy Engineer in the integrity of Oil and Gas projects
This brief article is intended to highlight some strategic ideas to enhance the interaction of the Corrosion, Materials and Metallurgical (CMM) discipline with other fields, to improve the integrity of a project and enhance the reliability of the plants. It also aims to show the workflow, and identify the mechanism of interaction between all the disciplines engaged in the execution of a project.
Why CMM ?
Today’s corrosion engineers cannot produce meaningful and reliable outputs without having a proper relevant knowledge of Materials and Metallurgy. For instance, for a corrosion engineer it is not sufficient to only know the electrochemical processes well, but it would also be necessary for him/her to have a clear idea of the difference between PVC and CPVC. The CMM engineer should also understand, for example, the role of molybdenum on pitting and crevice corrosion of stainless steels, and to assess that even if this is not an issue, it is still vital to be aware of the huge cost impact of selecting between SS304 and SS316 steels in a LNG project. Hence this being considered as a single discipline which is named CMM.
Why is this subject important?
Consistency between the engineering project specification documents has a significant effect in the integrity of a project. This consistency cannot be achieved unless a dynamic interaction is built between the engineering disciplines. Quite often, it has been experienced that the final version
of the Piping and Instrumentation Diagram (P&ID) is not compatible with the material selection specification or report. Piping classes specifying the material of construction’s corrosion allowance divert from the
as-built P&IDs etc. The root cause of these discrepancies lies in the lack of
proper communication between relevant engineers, in particular in the CMM discipline.
Phases of Project
Any project can go through different phases before it reaches a ‘live’ production. For example:
- Conceptual
FEED
Detailed Engineering
Procurement
Fabrication & Inspection
Installation
Pre-commissioning
Commissioning
Trial Period
Operation
Maintenance
Mothballing
Extension/Revamping
Conceptual
Front End Engineering Design (FEED)
Detailed Engineering
Procurement
Fabrication & Inspection
Installation
Pre-commissioning
Commissioning
Trial Period
Operation
Maintenance
Mothballing
Extension/Revamping
This article intends to briefly address some of the key activities in each phase.
Conceptual Phase
The most fundamental phase in which preliminary materials selection and
corrosion control, based on Statement of Requirement (SOR), and in line
with process design parameters, are made.
- Innovation, discussion meetings with reputed vendors
Risk of employing new technologies should not be ignored
Optimisation and cost savings to be looked at carefully
Discussion and agreement with the client on any software to be utilised
before it gets too late
Site visit by CMM engineer can be very useful, if not crucial
FEED Phase
- The project statement of requirements should detail scope of work for
this discipline
Optimisation process, i.e. risk analysis and economic analysis should
be conducted
Detailed Engineering comprises
- FEED endorsement
Endorsement correction, HAZOP, licensor, etc. Corrosion control check-
ups, Approved changes
Full definition of materials (e.g. exact grade of titanium, etc., for example)
Basis of material selection to be consistent with FEED
Materials requisition and any technical deviation
Critical review of package material, request for compliance
Setting and finalising materials selection, as built
Material selection control manual
Procurement and Construction
- CMM to ensure compliance to specifications, and ensure that an exotic
material choice is not necessarily fit for service.
Vendors technical bid and Concession Request (CR) document
Upgrade requests from vendor should be assessed carefully
Participate in pre-production meeting
Materials selection change request during construction on CP, painting,
storage, etc.
Issuing close-out report for as built condition
No compromise to be made if it could affect integrity
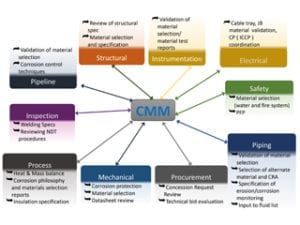
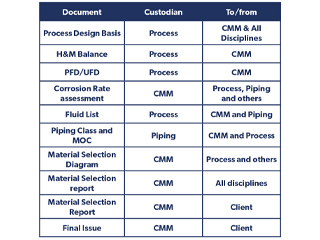
Table of typical workflow for issuing a corrosion control material selection table/report.
Pre-commissioning
The CMM engineers to be alert to some of the procedures in the manual, such as hydro testing, and that they are practiced carefully.
The Interaction mechanisms
The simple diagram shows the relationship between the CMM engineer and the other disciplines, and the table summarises the links between a process engineer and a piping engineer, as the main disciplines interacting with the CMM engineer in any oil and gas project, in order to have a robust and solid material selection philosophy. Similar tables can be produced to include other disciplines’ scope of activities, for instance in applying a corrosion mitigation technique by ICCP, the interaction between CMM, pipeline, civil and electrical engineers should be clearly defined.
Summary
It is important to note that a continuous and integrated input and engagement of the CMM engineer is vital throughout all stages of a project, since the integrity, reliability and safety of the plant depends significantly on the degradation mechanisms and materials selection strategy – the backbone of a CMM engineer’s expertise.
The Oil & Gas company should ensure active participation of the CMM engineer and appropriate interaction of them with other disciplines throughout the project.
It is recommended that
- The engineering director/company should ensure that there is a
continuous active participation, and appropriate interaction, of the
CMM engineer with other disciplines. It is also important that a proper
organisational chart is developed before the start of the project, and
the position and the work scope of the CMM engineer is defined for the
project, without any budget constraints for this important discipline.
The harmful misconceptions that “Nothing Can Be Done About
Corrosion!” are avoided
There is increased awareness of the large cost of corrosion and potential
savings that can be made
A sound Corrosion Management strategy should be set-up by changing
policies, regulations, standards, management practices and attitudes, to
increase corrosion mitigation savings
The education and training of staff in recognition of corrosion control
should be improved