Industry News
ICorr were privileged to be invited to Portcullis House in Westminster adjacent to the Houses of Parliament for a special themed event on the topic of ‘Reuse, Renew, or Replace?’ The following series of articles are presented in the same order as presented to the Parliamentary and Science Committee (P&SC) on the 15th October 2024 and are reproduced here with kind permission of SIP, the
P&SC official Journal.
The Journal of the Parliamentary and Scientific Committee (All-Party Parliamentary Group). SIP – SCIENCE IN PARLIAMENT has two
main objectives:
-
To inform the scientific and industrial communities of activities within Parliament of a scientific nature and of the progress of relevant legislation;
- To keep Members of Parliament abreast of scientific affairs.
Visitors were welcomed to the discussion meeting by George Freeman MP, new Chair of the P&SC.
Stephen Tate, President of ICorr, introduced our Institute activities; and especially training, emphasising that improving the competency of corrosion engineers at all levels is a key objective of the Institute. Courses are run, qualifications awarded, specialised meetings held, and financial support given to many including most recently for their YEP – Young Engineer Programme 2024, this time held in London.
Our four specialist presentations were kindly given by Gareth Hinds, Senior Fellow and Science Area Leader, Electrochemistry Group at the National Physical Laboratory, who provided his thoughts on ‘Raising Awareness of Corrosion’; David Parker, Environmental Consultant, who spoke on ‘The Potential of Value Retention Processes (VRPs)’; with Izabela Gajewska, Intertek CAPCIS Consultancy Services, giving us her ideas on ‘Mentoring the Next Generation towards Corrosion Prevention’; and finally Christian Stone of Loughborough University and Concrete Preservation Technologies Ltd describing ‘Advanced Corrosion Management Techniques to Reduce Cost and Risk in Our Built Environment.’ This magnificent
all-round event provided excellent exposure for our Institute.
Industry News
Enhancing Corrosion Inspection
through UAV technology
by Stephanie Okoye, B-Eng, MSc, CEng, AMPP, MICorr
Meet the Author
Stephanie Okoye
Stephanie is a Chartered Senior Corrosion Engineer with over 15 years of experience in the oil and gas sector. Currently with Vysus, her expertise lies in corrosion and integrity management of North Sea Oil & Gas assets, as well as Downstream Gas and Chemical Processing plants. She holds qualifications as a Senior Corrosion Technologist by AMPP (formerly NACE) and currently serves as an Executive member of the Institute of Corrosion (ICorr Aberdeen Branch Committee). Stephanie is also a project management professional with a proven record of leading teams, managing, and delivering several projects successfully.
How Drones are Used for Corrosion Management?
Introduction
In the past, inspectors relied completely on manual methods to conduct corrosion-related inspections of assets prone to degradation. These traditional approaches involved visual assessments or the use of non-destructive testing (NDT) tools to quantify the extent of corrosion. While effective, these methods often proved to be time- and labour-intensive and prone to inherent safety risks where humans are involved. The introduction of drones, or Unmanned Aerial Vehicles (UAVs), has augmented and, in some applications, revolutionised this field by enabling inspections to be carried out more efficiently and with greater safety. Within industries such as oil and gas, UAVs have become indispensable for conducting corrosion-related inspections. These inspections predominantly involve the use of high-resolution optical sensors to obtain enhanced data more safely and efficiently. Drones can navigate vast, challenging environments to capture detailed imagery of inspected items.
With advancements in technology, the images collected by drones can be analysed using cutting-edge artificial intelligence (AI) algorithms and automated systems to assist with the identification of corrosion and other forms of deterioration. Drones not only pinpoint the presence of corrosion but also provide precise data on its location, allowing for accurate mapping and documentation. This capability facilitates future monitoring and creates visual records to track the progression of corrosion over time. Unlike traditional methods, which are manual and time-consuming. Drone inspections offer a safer, more reliable alternative for maintaining the integrity of critical assets.
In Which Areas can UAVs be Utilised for Inspection?
UAVs are versatile tools that can be deployed across various industries and environments, including offshore platforms, onshore petrochemical plants, floating production storage and offloading units (FPSOs), underwater pipelines, bridges, and civil engineering projects. Their adaptability makes them particularly valuable for inspecting assets in hazardous or hard-to-reach locations.
In the UK, UAV operations are regulated by the Civil Aviation Authority (CAA), which mandates that operators obtain the necessary registration and authorisation. Each UAV operator is issued a registration number and a CAA reference number, ensuring compliance with safety and operational standards. Different UAV models cater to a range of inspection needs, each designed to address specific challenges, as may be required by specialist inspection companies. Notably, I have had the opportunity to engage with CAN Group in Aberdeen, who operate a range of UAV technologies through its inspection services business stream. CAN’s fleet of UAVs operated by specially trained pilots is equipped to perform a range of visual, dimensional and thermal imaging inspections and emission surveys in hazardous environments and areas that are typically inaccessible during standard production operations, in support of structural and mechanical integrity condition assessments both onshore and offshore. The information they kindly provided was highly valuable in enhancing
my understanding of the technology behind drones used for
corrosion inspections.
Flyability’s ELOIS 3 Drone: The ELOIS 3 drone is designed for confined space entry, eliminating the need for personnel to access hazardous locations, thereby reducing costs and manpower requirements. It features an integrated Ultrasonic Testing (UT) capability combined with aerial drone solutions, providing a safer and more efficient alternative to traditional UT inspection methods.
Conventional non-destructive testing (NDT) requires inspectors to be within arm’s reach of the data collection point, which can be challenging when inspecting difficult-to-access areas of an asset. For larger components, such as stacks, ballast tanks, or pipe racks, inspectors often rely on mobile elevated work platforms, rope access, or scaffolding to reach measurement sites. These traditional approaches are typically slow, expensive, and pose significant safety risks due to working at height or in confined spaces necessitating specialist training courses and more extensive permit requirements.
Drones offer NDT experts a unique aerial perspective, enabling quick and efficient access to remote or hard-to-reach areas without putting the pilot at risk and are frequently used for cross-country pipeline inspections. This approach significantly reduces operational costs and minimises safety hazards associated with traditional inspection methods.
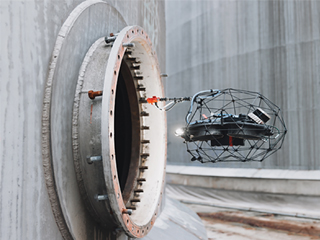
Underwater Applications
UAVs specifically designed for underwater tasks, known as Autonomous Underwater Vehicles (AUVs), have become essential tools for conducting underwater inspections, particularly in detecting corrosion in subsea pipelines. These vehicles are engineered for the unique challenges of underwater environments, which are often harsh and corrosive. Subsea pipelines, frequently exposed to seawater and strong currents, often face aggressive conditions due to their location and from the presence of chloride ions, high salinity, and bacteria, all of which can degrade materials over time together with erosional effects.
AUVs are equipped with advanced technology, including magnetic sensors, high-resolution cameras, and ultrasonic sensors. These tools allow them to accurately identify ongoing corrosion and measure metal thickness, enabling the detection of metal loss and other subsea-related issues. This technological advancement has significantly mitigated the risks previously associated with human divers and the
use of Remotely Operated Vehicles (ROVs), which are more costly and time intensive.
By utilising AUVs, subsea inspections have become safer, more accurate, and more efficient. The ability to conduct detailed assessments without risking human safety or incurring excessive operational costs, has revolutionised the approach to maintaining and inspecting underwater infrastructure.
Detection of Corrosion Under Insulation (CUI)
Corrosion under insulation (CUI) presents one of the most significant challenges in the oil and gas industry. Many pressure systems, including piping, pressure vessels, and tanks, are insulated for process optimisation or personnel safety. Traditionally, detecting CUI has required the removal of insulation to expose the metal substrate, allowing inspectors to identify visible signs of corrosion. However, in many cases, accessing these insulated components is difficult, particularly when water ingress compromises the integrity of the insulation.
UAVs equipped with advanced sensor technologies have emerged as a game-changing solution for inspecting insulated piping and components for early CUI indications. These drones can access areas that are otherwise unreachable from the ground and typically require scaffolding for manual inspection. The UAV sensors capture detailed video and thermal imagery, which are subsequently transmitted to a computer for analysis.
The visual images highlight the surface condition of the component, identifying trouble spots such as damage, degradation, or rust stains on cladding. Thermal infrared (IR) imaging, on the other hand, reveals temperature variations on the insulated surface. For example, IR images may predominantly display warmer tones, such as red, indicating hot fluid inside the pipe. If water or moisture infiltrates the insulation—a precursor to CUI—the affected areas will exhibit cooler temperatures, shown in distinct colour variations. These anomalies are characterised by unique thermal signatures, enabling precise identification of potential problem areas. The data collected is processed and analysed using specialised software, providing actionable insights for maintenance planning. This innovative approach not only eliminates the need for labour-intensive and risky insulation removal but also ensures efficient and accurate CUI detection in hard-to-reach live process areas.
Road Bridges Applications
Corrosion of steel components is a leading cause of deterioration and failure in road bridge infrastructure. Traditional inspection methods often struggle to accurately assess the thickness of steel in corroded areas, as determining the depth of corrosion poses significant challenges. Inspectors typically rely on visual checks to identify corrosion or use ultrasonic waves to measure severely affected areas. However, these approaches necessitate placing probes directly on
the measurement sites, resulting in substantial operational expenses
and logistical challenges when inspecting multiple locations or
entire structures.
Drone technology has introduced a transformative approach to bridge inspections. For example, NTT e-Drone Technology Corporation is currently testing an advanced system that leverages drones and AI-powered image recognition to detect corrosion in steel materials and estimate corrosion depth. This innovative technology combines high-resolution imaging and AI analysis to enhance inspection efficiency while reducing maintenance costs. The testing of this technology is planned to be completed in 2025.
By automatically estimating the depth of corrosion, this technology aims to streamline the inspection process, allowing for rapid and accurate assessments without the need for invasive procedures. The integration of drones with image recognition AI represents a significant advancement in maintaining road bridge infrastructure, ensuring safety, and optimising maintenance efforts.
What are the Examples of Applications of UAVs
in Detecting Corrosion?
Inspection of Flare Stacks and Structural Components
The use of drones has proven invaluable for inspecting flare stacks, support lines, and associated structural components during pre-turnaround maintenance surveys. The primary objective of such inspections is to assess and document the condition of structural steelwork, piping, and cables in plant flare systems. During a recent survey, drones identified areas with minor coating breakdown and l
ight corrosion, as well as some safety concerns. The drones used are equipped to perform 360-degree thermal imaging around flare tips, which helps identify hotspots or other potential concerns. However, in this instance, thermal imaging was not conducted. This technology highlights the versatility of UAVs in ensuring thorough and efficient inspections in complex and potentially hazardous environments.
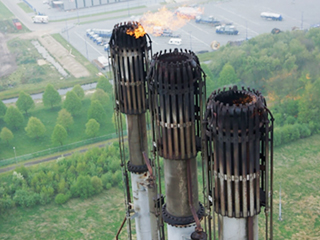
Inspection of Cargo Tanks Using UAVs
Marine Inspection Services recently deployed one of ScoutDI UAVs (Scout 137) to inspect the interior of a cargo tank on an oil tanker. Traditionally, such inspections would have required rope access inspectors working at height, utilising scaffolding or ladders. This approach often entails limited light and air access, creating potentially hazardous conditions for personnel.
In contrast, deploying a UAV equipped with high-quality video capabilities allowed the inspection to be conducted more quickly, safely, and efficiently. The drone’s ability to navigate confined spaces and capture comprehensive footage significantly enhanced the overall inspection process while minimising risks to human workers.
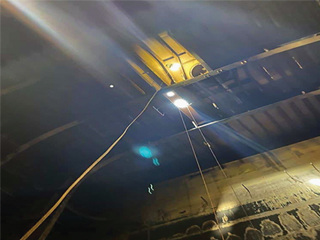
What Are the Benefits of UAV in Detection of Corrosion in Different Environments?
-
Safety, Confined Spaces and Hard-to- Reach Areas: UAVs can easily access confined spaces or remote areas inaccessible to inspectors, like inside storage tanks, pipelines, or high-altitude structures (e.g., wind turbines) and hazardous environments like chemical plants or offshore oil platforms. This environment often presents hazardous conditions, such as toxic gases, high temperatures, lack of oxygen, or narrow passages. Use of UAVs eliminates the need for scaffolding, ropes, or cranes and inspectors to physically enter the hazardous environment, which significantly reduces the risk of accidents and injuries to human inspectors.
-
Visual Inspections: The high-resolution cameras on UAVs capture detailed images of surfaces, allowing inspectors to identify visible signs of corrosion, such as rust, discolouration, or surface damage. These images can be analysed remotely and compared over time for monitoring corrosion progression.
-
Thermal Imaging: Some UAVs are equipped with infrared or thermal cameras which have the potential to detect changes in surface temperature that may indicate underlying corrosion under the protective coatings, such as moisture accumulation or insulation failure or areas where the early stages of corrosion are occurring and hard to notice, without the need to interrupt production.
-
Non-Destructive Testing (NDT): Some UAVs integrate NDT methods, such as eddy current sensors or magnetic flux leakage detection, to assess the integrity of materials without causing damage. These sensors can detect subsurface corrosion and assess metal loss or cracks. Additionally, some advanced UAVs carry specialised equipment like ultrasonic thickness gauges to measure the thickness of metal surfaces. LIDAR (Light Detection and Ranging) can be used to create detailed 3D models of structures, helping to identify areas where corrosion has led to structural deformation. It is not possible to transfer all NDT activities efficiently to UAVs at t
his time.
-
Data Analysis and Reporting: UAVs collect immense amounts of data, which can be processed using Artificial Intelligence (AI) and machine learning to identify patterns of corrosion and predict future risks. This data is often presented in detailed reports with actionable insights for maintenance planning.
-
Cost and Time Efficiency: UAVs significantly lower inspection costs by reducing the need for manual inspection and reduces assets downtime. They also reduce inspection times and the need for additional support services.
What Are the Challenges and Limitations of Utilising UAVs for Inspection?
Despite their numerous advantages, UAVs face several limitations and still requires human intervention as follows:
-
Data Analysis Expertise: The large volume of data collected requires skilled personnel or AI systems for effective analysis.
-
Weather Dependence: Adverse conditions like heavy rain, fog, or high winds can impact UAV performance and data quality.
-
Operational Range: Limited flight times and battery life can restrict UAV operations.
-
High Initial Costs: Acquiring and maintaining UAV equipment, as well as training personnel, involves significant investment.
-
Regulatory Compliance: UAV operators must adhere to strict regulations, which can vary between countries and impact deployment timelines.
-
Pixel Resolution Challenges: Variations in pixel resolution during inspections can affect the accuracy of corrosion depth estimations, particularly in dynamic environments like road bridges.
-
Skill of the Pilot: Requires many different skillsets e.g. piloting, data gathering and interpretation with a thorough understanding of onboard NDT technologies and must be able to multi-task quickly, effectively and safely.
What Are the Challenges and Limitations of Utilising UAVs for Inspection?
-
The field of UAV technology for corrosion inspection is evolving rapidly, driven by advancements in AI, sensor technologies, and robotics. Future developments include:
-
Enhanced AI Algorithms: Improved machine learning models will enable faster and more accurate data analysis, minimising human intervention.
-
Longer Battery Life: Innovations in energy storage will allow UAVs to operate for extended periods, enhancing efficiency for large-scale inspections.
-
Integration with IoT: UAVs may later fully integrate with Internet of Things (IoT) systems, providing real-time data to centralised platforms for seamless asset management.
-
Autonomous Operations: Fully autonomous UAVs capable of navigating complex environments without human guidance are on the horizon, reducing operational challenges further.
-
Advanced Materials: The development of lightweight yet durable UAV components will increase resilience against harsh weather conditions and extend operational capabilities.
Conclusions
The integration of UAV technology into corrosion inspections has revolutionised the Oil and Gas industry, providing unprecedented improvements in safety, efficiency, and accuracy. UAVs facilitate continuous monitoring and early detection of corrosion, minimising associated risks and enabling more informed asset management decisions. With further advancements in sensors, artificial intelligence (AI) and data analytics, the reliability and effectiveness of inspection data have significantly improved in many cases, making UAV-based inspections more precise and actionable. As UAV technology continues to advance, it opens new opportunities for innovation, job creation, and cost-effective maintenance strategies across other industries, ensuring the protection and longevity of critical infrastructure. Expanding the use of UAVs beyond traditional inspection methods will unlock even greater possibilities, allowing industries to achieve enhanced safety, precision, and operational efficiency, safeguarding vital assets worldwide, promoting sustainability and resilience in infrastructure management.
Acknowledgments:
The author wishes to thank the following companies for their assistance with this article.
- www.cangroup.net
- www.flyability.com
- www.marineinspectionservices.co.uk
- www.nttedt.co.jp
- www.scoutdi.com
- www.vysusgroup.com
Industry News
The RedLineIPS SmartPad System, from Cogbill Construction of Texas U.S.A., is a patent-pending Fiber-Reinforced Plastic (FRP) solution specifically engineered to address Corrosion Under Pipe Supports (CUPS) at coastal and offshore facilities in the petrochemical and gas sectors. Designed for above-ground piping systems, the SmartPad System offers a revolutionary approach to external corrosion protection at pipe support points. The system combines tried-and-true materials and components, a saddle-shaped design, and an innovative watertight sealing mechanism to provide durable, efficient, and cost-effective protection for industrial pipes.
Unlike traditional solutions, the RedLineIPS SmartPad System eliminates the need for fixing methods such as epoxy or welding, allowing installation, removal, and reinstallation in minutes.
This capability facilitates rapid visual corrosion inspections, reducing reliance on expensive methods such as radiography
and ultrasound, and thus reducing the overall cost of ownership.
The SmartPad System: An Alternative Solution
to CUPS
The RedLineIPS SmartPad System is a potential breakthrough in external corrosion protection, offering the following key benefits:
- Cost-Effective Maintenance: SmartPads allow rapid visual inspections, reducing reliance on expensive and time-consuming methods like ultrasound or X-ray.
- Moisture Barrier: The integrated closed-cell Hydroseal gasket creates a NEMA-4-rated watertight seal when installed, preventing moisture accumulation.
- Non-Metallic Construction: The FRP material eliminates
metal-to-metal contact, preventing galvanic corrosion.
- Quick Installation: The system can be installed, removed, and reinstalled in seconds without welding, epoxy, or line shutdowns.
- Saddle-Shaped Design: This innovative shape evenly distributes stress, prevents point loading, and protects the
pipe’s coating.
Benefits of the SmartPad System
- Allows rapid visual inspections, reducing operational costs.
- Dampens vibrations and noise for improved system stability.
-
Eliminates metal-to-metal contact, preventing galvanic corrosion.
- Long-lasting, UV-resistant materials.
- No epoxy or welding required.
- Protects a pipe’s protective coating from wear.
-
Reusable components promote sustainability and green initiatives.
-
Suitable for extreme temperatures (-60°F to 400°F). convert
to Centigrade.
Applications and Industry Adoption
The SmartPad System is suitable across industries, including:
- Oil & Gas: Offshore platforms, pipelines, and refineries.
- Petrochemicals: Chemical processing plants.
-
Power Generation: High-pressure, high-temperature
piping systems.
-
Water Treatment: Corrosion protection for water and wastewater facilities.
Early adopters include major industry players such as Chevron, Formosa Plastics, and Nutrien – all at coastal facilities and offshore platforms at the Gulf of Mexico. They have successfully implemented the SmartPad System in challenging environments, achieving significant reductions in maintenance costs and improved pipeline longevity.
For further information contact:
Hani Almufti
Engineer and Manager of Strategic Development
Cogbill Construction, LLC
2325 S. Main Vidor, TX 77662
Hani@cogbillconstruction.com
www.SmartPadSystem.com
Industry News
A new set of best practices created specifically for the Oil, Gas and Petrochemical industries has been released on
18th December 2024, giving guidance on the deployment, usage, inspection strategies and maintenance of Corrosion Under Insulation (CUI) monitoring systems.
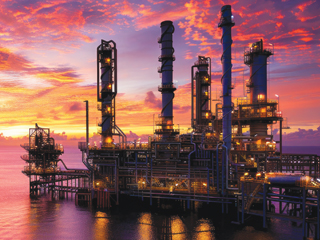
The Recommended Practice document, which is referred to as CUI RP 101 Issue 1 and includes contributions from experienced users throughout the industry, including Aramco, Dow, INEOS and Chevron, contains best practices from asset selection to the use of maintenance management systems, inspection strategies and economic justification principles. It has been developed to enable Asset Owners to optimise inspection and repair strategies and enhance CUI management processes with continuous monitoring systems in the arsenal.
CUI costs the industry billions of dollars every year to mitigate the risk and repair the damage it causes to assets. Unmanaged CUI can result in leaks, leading to process safety incidents, severe harm to the environment, high unexpected repair costs and operational downtime.
Continuous monitoring systems for CUI offer remote detection of localised corrosion and moisture on an asset, while also providing corrosion rates. This empowers Asset Owners to make informed decisions on where and when to conduct repairs, leading to significant cost savings, reduced safety hazards, and minimised environmental risks across the industry.
The key principles outlined in the guidance include:
- Asset selection criterion.
- Organisational recommendations.
-
The process to be used for technical justification, validation and qualification.
- The technology behind a CUI monitoring system.
- Use of remote monitoring in different inspection strategies.
For further information, visit www.corrosionradar.com
or email info@corrosionradar.com
Source: Corrosion Radar Press Release