Institute News, Uncategorized
The Institute of Corrosion is very pleased to welcome new company member – Midland Corrosion Services (MCS) based in Derbyshire.
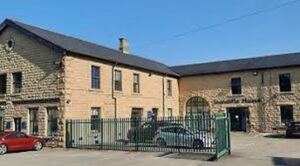
Midland Corrosion Services (MCS) are Corrosion Specialists established in 2001 by Dr. Phil Munn as Director of the company. Following his retirement, Dr. Zuojia (George) Liu took over from Dr. Phil Munn in April 2021 as the Senior Manager and now promoted to Technical Director to manage daily tasks for MCS.
MCS established as one of the leading corrosion consultancy and testing companies has been providing independent testing and consultancy services to water services, building / construction and water/wastewater treatment industries in corrosion investigation and protection since 2001, with a dedicated team of professionals with over 60 years of joint experience in corrosion and materials testing, engineering, assessment and consultation and a culture of responding quickly to clients’ requests.
Key Activities:
- Corrosion Protection Consultation
- Customised and Standard Corrosion/Materials Compatibility Testing
- Evaluation/Testing of Corrosion/Scale Inhibitors under NSF CIAS approved (National Sanitation Foundation – Corrosion Inhibitor Approval Scheme)
- Expert Witness for Litigation Support
- Failure Investigations in Heating/Chilled/Hot/Cold Water Systems i.e. all HVAC components
- Material Selection Evaluation
- Water Analysis Services
- Weight Loss/Corrosion Rate/Coupons Assessments
Accreditations:
Photo: MCS Failure Investigation
Its main area of expertise is in building services (closed heating and chilled water systems & domestic hot and cold-water systems) and water services/analysis. MCS investigate and assess corrosion in pipework, heat exchangers, boilers, pumps, valves, seals and much more. MCS also provide lab and coupon testing and failure investigation for various metallic materials such as copper (& copper alloys), brass, carbon steel, stainless steel, galvanised steel, cast iron, aluminium alloys, rubber/EPDM lining material. MCS are accredited to ISO 9001:2015 and ISO 17025.
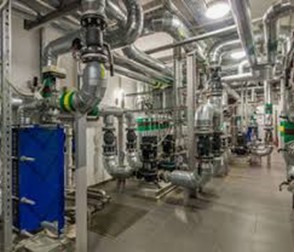
Photo: MCS Building Services Support
The company specialises in providing customised corrosion testing for material corrosion performance evaluation and material selection, serving to date a broad mix of over 300 contractors/clients from major blue-chip construction and wastewater treatment companies to small plumbing firms and domestic properties. MCS are also part of the NSF CIAS approval scheme for testing of corrosion inhibitors used in closed heating and cooling systems and the only NSF approved test laboratory in the UK to perform the CIAS test procedure.
In May 2018, MCS became part of the Sandberg Group, which is a world-renowned material testing company which provides additional access to highly professional and independent consultants, laboratories, site survey teams and testing as well as specialised analytical equipment.
They now also collaborate with Sandberg to provide NDT [1] service for pipework inspections, weld inspection and corrosion investigation in rail, building and concrete sectors.
As from 2021, MCS have expanded the business fields to corrosion testing and consultancy of water systems of mansion-level properties, food, agriculture plants, fire sprinkler system and incinerator ductwork pipe system.
MCS is a strong advocate of preventing corrosion damages before they occur and can offer advice on materials selection, design and root causes of failure to minimise the risk of corrosion and failures. Over the years MCS has provided advice on materials selection and corrosion protection over a diverse project range.
For further information please contact:
Midland Corrosion Services Ltd
Stancliffe House
Whitworth Road
Darley Dale
Derbyshire
DE4 2HJ
Tel: 01629 733162
Email: info@midlandcorrosion.co.uk
Web: www.midlandcorrosion.co.uk
Institute News, Uncategorized
New Corporate Member – ICorr Welcomes Hempel: Helping shape a brighter future with sustainable coating solutions
Shaping a brighter future
Hempel is a global supplier of coatings across industries. From bridges and ships to wind turbines and homes, Hempel’s products can be found in almost every country, protecting the world’s buildings, infrastructure and other assets from corrosion. Hempel coatings are essential to their customers’ businesses. They help minimise maintenance costs, improve aesthetics, reduce waste and increase energy efficiency in the operation of assets. They extend the lifetime of the assets they protect – helping lower the asset’s environmental and carbon footprint across its entire lifecycle.
Hempel was established in Denmark in 1915 and today employs people across the globe. It’s headquartered in Kongens Lyngby, near Copenhagen, Denmark.
For the wider good
Hempel is majority-owned by The Hempel Foundation, which ensures a solid economic base for the Hempel Group and supports cultural, social, humanitarian and scientific purposes around the world.
In 2023, The Hempel Foundation donated €23 million to development initiatives in the fields of education, biodiversity and science.
Committed to sustainable development goals
Hempel are committed to the UN Sustainable Development Goals. The UN SDGs are integrated and indivisible and our Hempel goals work in a holistic way to support them.
- We are reducing CO2 emissions in our own operations and in our value chain and switching to renewables.
- Our products contribute to a more sustainable and resilient infrastructure.
- We are pursuing resource efficiency and circularity and reducing harmful substances.
- We are committed to health and safety and the promotion of diversity and inclusion.
- We promote ethical behaviour and good environmental practices in our supply chain.
- We collaborate widely and pursue effective partnerships.
Sustainability at the heart of business
Sustainability Leadership is a key pillar of Hempel’s Double Impact business strategy. For Hempel, sustainability leadership means being a frontrunner within the paints and coatings industry by enabling customers to meet their sustainability ambitions.
To achieve on these ambitions, Hempel works dedicatedly on sustainability initiatives, with a focus on reducing its environmental footprint, enhancing its social impact and maintaining its strong corporate governance standards.
Liquid engineering – R&D
Hempel strives to be the best in the business – and that means always looking for innovative ways to improve coating performance, as well as new ways for coatings to improve the world. With R&D centres across Europe, the Middle East, Asia and America, their R&D teams work with customers, research institutes, suppliers and other industries to push the boundaries of what coatings can do – always with the aim of improving customers’ business performance.
Hempel’s R&D work focuses on:
- Research into the latest paint technologies
- Developing new customer-focused products and solutions
- Partnering with customers to tailor solutions
- Reducing the environmental impact of coatings
- Increasing the sustainability value derived from the use of coatings, including extending the lifetime of assets and increasing the energy efficiency of operating assets
Driving innovation in protective coatings
As a global supplier of coatings across industries, Hempel develops advanced coatings solutions to protect assets, reduce maintenance and enhance performance. One leading example is ‘Avantguard’, a patented technology that sets new standards in corrosion protection.
https://www.hempel.com/inspiration/sustainability
For over 10 years, this innovative coating solution has extended the lifetime of steel structures across a wide range of applications, from wind towers and bridges to airports and skyscrapers. It not only prolongs the lifespan of assets but also simplifies application, reduces maintenance costs and lowers CO₂ emissions. It’s the ideal corrosion protection solution for any forward-thinking asset owner, consulting engineer, contractor or applicator.
Avantguard is the world’s first zinc-rich primer to fully utilise its zinc content by activating all three methods of corrosion protection: the barrier, the inhibitor and the galvanic effect.
With its unique properties, Avantguard ensures superior durability and reduced environmental impact in addition to its easy application; offers fast drying, fewer coats, and an excellent crack-resistant finish.
And with the recent launch of Avantguard 750 Pro, setting a new industry standard for corrosion protection and building on over a decade of Hempel’s patented Avantguard technology, Hempel reaffirms its dedication to sustainability and high-performance coating systems.
Contact
For more information, visit Hempel’s website www.hempel.com or reach out to the team at hempel@hempel.com.
Institute News
By Izabela Gajewska
On behalf of the Institute of Corrosion, Izabela Gajewska, MICorr, and Eilidh MacDonald, MICorr, had the privilege of attending the Smeatonian Society of Civil Engineers’ Discussion Dinner on 27th November 2024 at the iconic One Great George Street, headquarters of the Institution of Civil Engineers (ICE).
This marked the first time in history that younger members of ICorr participated in the Smeatonian Discussion Dinner. It is hoped that this will be the beginning of a lasting relationship between the Institute of Corrosion and the Smeatonian Society.
Founded in 1771, the Smeatonian Society remains a key hub for regular insightful engineering discussions, generally over a meal.
These discussions take the form of an introductory presentation followed by group discussions which are summarised to the
gathering by rapporteurs. Traditionally, meetings take place on the
last Wednesday of January, March, April, October, and November,
with adjustments to avoid holiday conflicts. The October meeting
is normally a lunch; all other meetings are dinners with a variety
of formats.
At Discussion Dinner, a member or guest is invited to speak on a topical subject and lead a discussion under the Chatham House Rule. The Society’s meetings do not seek to replicate meetings of the Royal Academy of Engineering or those of the engineering institutions. Topics for discussions are normally on matters of general engineering interest or wider societal subjects.
The recent discussion evening focused on the challenges and opportunities facing engineering today, with a strong emphasis on Materials Engineering, a topic less familiar to many Smeatonians, introduced by Stephen Shapcott, the recipient of this year’s prestigious Smeaton Medal.
The discussions highlighted how materials engineering plays a vital but often underappreciated role in solving today’s pressing issues. A key takeaway was the need to move beyond simply sharing ideas across disciplines and industries, and instead fully integrate them to create more cohesive and impactful solutions. There was also a significant focus on inspiring future engineers through modernised education, including updates to programmes that incorporate cutting-edge materials science and sustainability topics to better reflect current industry needs, and promoting sustainability through smarter, more efficient materials.
Lastly, the discussion focused on how industries can better leverage advances in materials science, particularly in the context of urgent climate action. This includes investing in innovative corrosion resistant materials like graphene for energy storage and fostering stronger collaboration with research institutions to stay at the forefront of developments. However, even commonly used materials require continuous innovation, especially in areas like reuse and recycling, to create a more sustainable future.
Rod Muttram, Honorary Treasurer of The Smeatonian Society of Civil Engineers, expressed his gratitude to Stephen Shapcott for expanding and sharing knowledge, a tradition that has been central to the Society for over 250 years!
For more information about the Smeatonian Society,
you can watch the YouTube video they commissioned for
the 300th anniversary of Smeaton at
www.youtube.com/watch?v=rhfzCcPuofY and visit
their official website at www.smeatonians.org
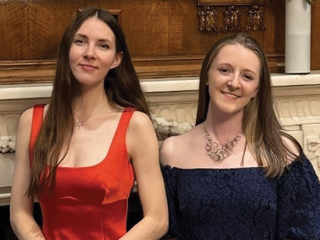
Photo: Izabela Gajewska (Left) and Eilidh MacDonald (Right) Pictured at the Dinner in the Smeaton Room of the Institution of Civil Engineers (ICE), One Great George Street, Westminster, London.
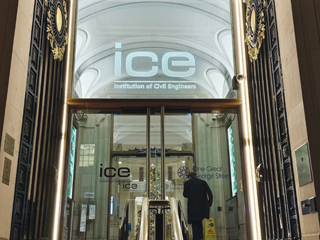
Photo: The Entrance to Institution of Civil Engineers (ICE), One Great George Street, Westminster, London.
Institute News
ICorr is a member of the Science Council, which means we can offer you the opportunity to become a Chartered Scientist (CSci). In this article, they explain what they do and what 2025 has in store.
The Science Council was established by Royal Charter just over 20 years ago and registered as a charity in 2009. Its official purpose is ‘to promote the advancement and dissemination of knowledge of
and education in science, pure and applied.’
It does that by being a membership organisation for professional bodies and learnt societies across the breadth of science and by providing professional registration. This interdisciplinary community of over 30 organisations is mutually supportive and can amplify the achievements and concerns of the scientific disciplines where there is common interest.
The Science Council holds four professional registers: Registered Science Technician (RSciTech), Registered Scientist (RSci), Chartered Scientists (CSci) and Chartered Science Teacher (CSciTeach).
In order to join a register, you need to be a member of ICorr or another of its Licensed Members, hold a relevant qualification or demonstrate equivalent achievement, meet the standards of competence for the relevant register, and agree to follow the code of conduct and undertake continuing professional development (CPD).
They help potential Registrants by holding a free online Introduction to Professional Registration workshop every month. Last year they also introduced Application Sprint: A Masterclass in Professional Registration. This intensive one-day workshop supports you to prepare a first draft of your competence report, the main part of your application. Dates for this year will be announced soon.
The Science Council is run by a small but effective team, led and supported by chief executive Professor Della Freeth. Della took up the role in August 2023, bringing significant experience of education, training and leadership developed in secondary school teaching, several senior roles in universities and the Royal College of Physicians.
Over the past 18 months, Della has worked with the team to make sure the Science Council is focused on bringing its members together and supporting its current and future Registrants. Key work has included making sure professional registration is accessible, continuing the technical education project in partnership with the Gatsby Foundation, and championing equity, diversity and inclusion through its Progression Framework in collaboration with the Royal Academy of Engineering.
Last year, Della worked with Science Council Members, staff and the Board of Trustees to develop the organisation’s strategy for 2025-2028. It will be published in spring this year, but Della was happy to give us a taste of what is to come.
“We are excited about working with our Members, Registrants and partners on the next stage of our journey,” she said. “We always start with our vision and purpose, as they remind us why we are here in the first place. We aim for a diverse and growing science profession that is trusted, respected, innovative and equipped to meet regional, national and global challenges. And our role in that is to connect the science professions and offer professional recognition for scientists, science technicians and science teachers.
“Over the next three years, we will focus on delivering our core business as effectively as possible. We’ll keep reviewing our standards to make sure they inspire current and future Registrants. We’ll bring our members together, amplifying their achievements and views in areas of common interest. We’ll work to increase the number and diversity of Registrants and volunteers, and to enhance their sense of belonging to our community.
“We’re also going to develop relationships with more employers, supporting them to invest in and support their staff. We’ll make sure our work on apprenticeships, T Levels and other technical qualifications is embedded in what we do for the long term. And we’re going to make sure that our website and other elements of our digital architecture are fit for purpose.”
Interested?
Read more information about professional registration with the Science Council and applying via ICorr or visit the Science Council website:
www.sciencecouncil.org
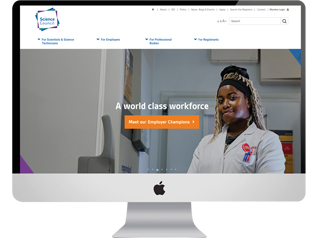
Photo: An example of the Science Council website homepage.
Institute News
On 17th January 2025, following a successful handover meeting led by Dr Danny Burkle and Izabela Gajewska, we are thrilled to introduce Kathy as the new Young ICorr Chair.
Both Danny and Izabela have dedicated significant effort to advancing Young ICorr initiatives, and while they now step back from the leadership role, they will remain supportive members of the new committee. This collaborative approach promises a seamless transition and continued progress for the group. Kathy brings an impressive background and lots of enthusiasm to this role. Here’s a bit about her in her own words:
“Hi, I’m Kathy, and I’ve been in the corrosion field for several years now. After completing a Master’s in Chemistry at the University of Hull, I worked as a Technical Service Manager at Teal and Mackrill, a specialist coatings manufacturer, while also working as an ICorr-qualified Coating Inspector. After several years in this role, I pursued a PhD in Corrosion at The University of Manchester, where I became more involved in ICorr activities, joining the Northwest Committee and initiating a student lecture series. I now work at the University of Leeds
as a research fellow in Corrosion. I’m excited and looking forward to developing more opportunities and activities for
the Young Members of ICorr, and I’m incredibly grateful for
this opportunity.”
Kathy’s vision for Young ICorr focuses on fostering engagement and creating opportunities that empower young professionals in the field of corrosion. Her leadership is guided by enthusiasm, collaboration, and a strong commitment to developing initiatives that support career development.
The Young ICorr Committee is actively seeking further proactive and enthusiastic individuals to join and contribute to the future of ICorr’s young members. If you’re looking for an opportunity to make a difference, now is the perfect time to get involved!
Let’s all join in welcoming Kathy to her new role and look forward to the exciting journey ahead for Young ICorr!
Please contact Kathy on youngicorrchair@icorr.org to register your interest in joining the Young ICorr committee.
Kathy brings a wealth of experience and enthusiasm
to the role. Her background includes:
- A MSc in Chemistry, from the University of Hull.
-
Industry experience as a Technical Service Manager
at Teal & Mackrill, specialising in protective coatings.
- Becoming an ICorr qualified Coating Inspector.
-
Completing a PhD in Corrosion at The University
of Manchester, where she initiated a student lecture series.
-
Currently working as a Research Fellow in Corrosion
at the University of Leeds.
Institute News
By Sarah Bagnall
In 2024, the Institute of Corrosion took a significant step toward expanding its reach
and promoting the importance of corrosion prevention in the Wales and South-West region of the UK.
With the establishment of the Wales and South-West Regional Branch, ICorr aims to foster greater collaboration and knowledge sharing within this vital area of engineering.
The formation of this regional branch reflects a growing need to address corrosion-related challenges in industries such as petrochemical, manufacturing, energy, infrastructure, and marine, which are particularly prevalent in the coastal and industrial regions of Wales and the South-West. The new branch will provide a platform for professionals to gather, exchange ideas, and gain a deeper understanding of corrosion issues, as well as cutting-edge strategies for prevention.
Key Events Held in 2024
Throughout 2024, the Wales and South-West Regional Branch hosted a series of events in cities such as Bristol, Port Talbot, Swansea, and Southampton. These gatherings served as key opportunities for local industry leaders, engineers, and academics to meet, learn, and discuss the latest advancements in corrosion science and technologies. Topics covered included innovative corrosion prevention methods, case studies, and industry best practices aimed at enhancing durability and reducing costs.
In addition to technical presentations and workshops, these events featured networking opportunities, allowing members to connect with peers and potential collaborators. This helped foster a sense of community within the region, strengthening relationships among professionals working in similar fields.
Looking Ahead: Events in 2025
Building on the success of 2024, the Wales and South-West Regional Branch will continue its mission to promote the understanding and prevention of corrosion. With events
planned across the region in locations such as Pembroke,
Cardiff, Plymouth, Southampton, and Swansea, the branch will ensure its activities are accessible to a wide range of professionals. By rotating event locations, ICORR hopes to reach even more individuals and organisations that may benefit from greater awareness and understanding of corrosion issues and prevention techniques.
These upcoming events will also offer valuable opportunities for learning and collaboration, featuring expert speakers and interactive sessions. The regional branch is committed to addressing the diverse needs of the region.
Strengthening Regional Collaboration
The Wales and South-West Regional Branch of ICORR also aims to work alongside other professional organisations in the region, such as the Southern Joint Branch of the Royal Institution of Naval Architects (RINA) and the Institute of Marine Engineering, Science & Technology (IMarEST), the Institute of Materials, Minerals and Mining (IOM3), and the Institution of Chemical Engineers (IChemE).
By working together with these groups, ICORR seeks to broaden the scope of its events and initiatives, offering a more interdisciplinary approach to corrosion prevention and management. This collaboration will help facilitate knowledge transfer across industries, bringing together professionals from different sectors who may face similar corrosion-related challenges. Additionally, these partnerships will support the development of innovative solutions to complex problems, ultimately advancing the field as a whole.
For more information, contact swchair@icorr.org
You can also keep up to date on events by visiting our LinkedIn page; https://www.linkedin.com/groups/12992293/ and our Website page www.icorr.org/wales-and-south-west-branch/please scroll down to Local Technical Programme
for Past presentations.
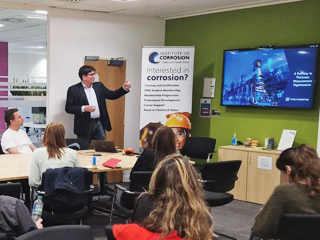
Photo: Delegates at the 2024 Bristol Event.
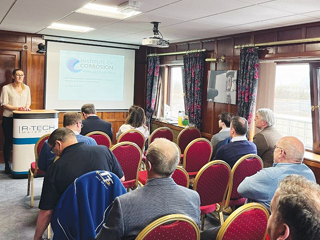
Photo: Delegates at the 2024 Port Talbot Event that launched the Branch.