Institute News
The branch held its 34th annual Christmas luncheon at the beginning of December at the Royal Overseas League in St. James’s. 150 guests enjoyed a four-course Christmas-themed lunch before being entertained by an after-dinner speaker. The event was hosted by George Winning, the new branch chair, who took over from Polina Zabelina in November.
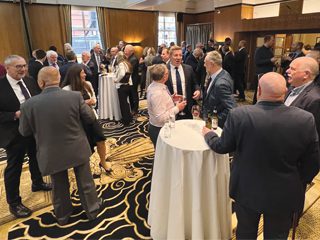
Before Sitting Down to Eat, there Were Pre-Lunch Refreshments, and Time for the Guests to Meet Each Other.
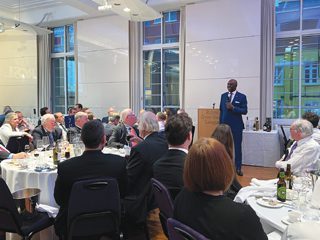
The After Dinner Speaker, Ian Irving.
The After Dinner speaker was Ian Irving, a popular entertainer, who gave an amusing sport-themed talk which was appreciated by the guests.
On the 18th January, (moved from the scheduled date due to transport strikes in London), Michael Harrison, Global Product Director-Linings, Sherwin-Williams, gave a presentation on “The Examination of Lining Performance in Renewable and Biofuels and Feedstocks”, sub-titled “why storing feedstocks for biofuel production presents distinct challenges for the specification of tank linings”, at the usual venue, the Lancaster Hall hotel, Craven Terrace, Bayswater.
Michael has 35 years of experience in the protective coatings industry, responsible for the development and testing of heavy-duty solvent-free linings, with subsequent roles in business support and business development. He has also been the project lead in the revision of ISO 16961 (Petroleum, petrochemical, and natural gas industries—internal coating and lining of steel storage tanks).
According to the International Energy Agency (IEA), biofuel use is growing at around 6% a year, and annual production to meet net zero emissions would need to reach over 10 EJ by 2030, requiring an average growth of around 11% per year. Biofuels have an important role to play in decarbonising transport by providing a low-carbon solution for existing technologies, such as light-duty vehicles in the near term and heavy-duty trucks, ships, and aircraft over the longer term. Indeed, according to the IEA, biofuel demand in 2022 reached a record high of 4.3
EJ (170,000 million litres), surpassing levels last seen in 2019 before the COVID-19 pandemic.
However, storing the lipid feedstocks necessary for the production of biodiesel, renewable diesels, and sustainable aviation fuels presents significant challenges for refiners. To avoid the degradation of tank linings and the subsequent corrosion of storage tanks and contamination of feedstocks, it is essential that proper consideration is given to the particular requirements of storing these materials, including the type of feedstock being stored, operating temperature, and storage duration. Failing to do so risks material contamination, tank corrosion, and even production delays. Increasing biofuel production presents one significant challenge for refiners; however, the lipid feedstocks required for biofuel refining have very different chemistries from fossil-based feedstocks, and it cannot be assumed that storage conditions—and the lining systems of storage tanks, in particular—are the same. To understand the issues faced by biofuel producers, a series of tests were conducted that revealed significant degradation of tank linings over time and at certain temperatures, raising important questions for refiners about how they store the feedstocks necessary for biofuel production and the temperatures to which they are exposed.
A two-stage test was carried out under NACE TM-0174 Procedure B, with test temperatures of 71°C, 82°C, and 93°C (based on project specifications), with evaluation at three monthly intervals extending to a minimum of 24 months. The tank lining systems evaluated included proven systems used in typical fossil fuel-derived feedstock storage applications: solvent-free epoxy phenolic, solvent-free epoxy novolac, and novolac vinyl ester glass flake. Feedstock media tested included a combination of waste cooking oil, waste cooking oil +1% water, beef tallow, and beef tallow + 1% water, as it has been reported that the presence of water accelerates the formation of free fatty acids, especially at higher temperatures.
Under phase one of the tests, the impact of higher temperatures on the test samples was apparent at relatively short exposure times. The effects of higher temperatures on solvent-free epoxy phenolic (which is rated at 135°C in crude oil) were apparent at 71°C. The effects of higher temperatures on solvent-free epoxy novolac (rated to 149°C in crude oil) were apparent at ~82°C. Both lining systems failed at 93°C. Broadly speaking, subjecting lipid feedstocks to temperatures above 60°C results in the production of Free Fatty Acids (FFAs) in lipid feedstocks, and the tests again revealed lower limits for these same two linings, with resistance up to 71°C and degradation above this temperature.
A second stage of testing involved two further elements the examination of the oil composition and how it changes at different temperatures, and the expansion of feedstocks to simulate the conditions in the earlier (water cooking oil) tests. Analysis of the oil composition revealed that, up to 60°C, vegetable oils remain reasonably stable with minimal degradation to FFAs after six months of exposure. FFAs are thought to be the aggressive component behind degradation, and this degradation accelerated at 71°C, where the oil degraded to ~12% FFA content after six months of exposure. At 82°C, the formation of FFAs is considerable (>30%). The degradation also appears to be time-dependent, with the FFA level increasing after only three months at temperatures higher than 71°C. This shows why there is no immediate breakdown and stresses the need for longer-term testing. (The normal recommended duration as per NACE TM-0174 procedure B
is 6 months).
Expanding the feedstocks to simulate the conditions in the earlier (water cooking oil) tests involved the addition of oleic acid alongside an unmodified control. This revealed a correlation with the results seen for waste cooking oil and beef tallow under phase one when laced with an additional 5% FFA, although samples with higher levels of FFAs showed rapid degradation. Analysis of these modified oils by both time and temperature of exposure clearly showed that the presence of additional FFAs accelerated the degradation of the oil. Indeed, FFA formation grew faster under these conditions.
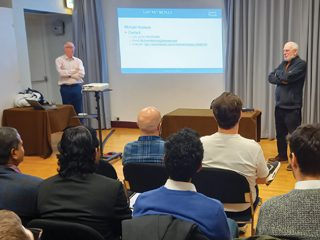
Michael Answering Questions at the End of His Presentation.
Testing on these oils demonstrates that, as anticipated, a novolac vinyl ester system can handle the higher temperatures primarily due to the superior resistance to organic acids (such as the free fatty acids seen in renewable fuels.) However, they present greater complications (flash point, storage stability etc.) during application. The lessons learned from this performance evaluation have provided an array of selection tools for biofuel asset owners and facility managers to select the appropriate lining system for their specific processes and needs.
Michael was thanked for his interesting talk and presented with an ICorr pen in appreciation. Information about future branch presentations can be found on the back cover of this magazine, and on the events page of the Institute website. Currently all talks are being held in person at the Lancaster Hall hotel.
Institute News
On November 28, 2023, the Aberdeen Branch meeting welcomed Dr. Douglas Mills and Tianyang Lan with an online talk entitled ‘Assessment of anti-corrosive organic coatings and green corrosion inhibitors by electrochemical techniques, particularly electrochemical noise measurement (ENM).
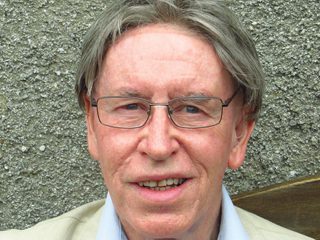
Douglas Mills gained a PhD in anti-corrosive coatings from Cambridge University, and after spells at the BNF Metals Technology Centre and the Nuclear Power Company, he has worked in academia and has continued to conduct and supervise research in the field of electrochemical methods for application to coatings, studying and advancing the electrochemical noise method. He was for fifteen years the Technical Secretary of the Institute of Corrosion and is also involved in standards development.
Recent Developments in Electrochemical Noise Measurement (ENM) Techniques
ENM is a series of techniques that can be used to assess the corrosion protection effectiveness of organic coatings. The advantages of the techniques are that they are non-intrusive and both ‘quick and easy’ to operate. The interpretation of the gathered
data is not complicated. The main purpose of ENM is to obtain a single parameter, the Noise Resistance (Rn) which relates to protective ability.
This is the standard deviation of the potential series / standard deviation of the current series.
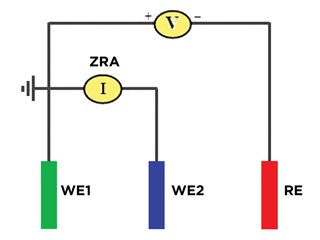
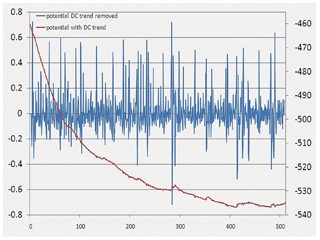
To obtain an R value, three electrodes are required: two nominally identical working electrodes (WE1 and WE2) and one reference (Re). The natural fluctuations of voltage (potential noise) are measured between WE and RE. At the same time, the natural fluctuations of current (current noise) are measured between the two WE electrodes.
The EMN data is typically gathered over about 4 minutes at 0.5-second intervals (512 data points). Repeat runs are made.
The criteria developed in 1948 by Bacon, Smith and Rugg defined the following:
• less than 106 Ωcm2 – poor corrosion protection,
• between 106 Ωcm2 and 108 Ωcm2 – intermediate level of corrosion protection,
• more than 108 Ωcm2 – good corrosion protection.
There are a number of different configurations of Electrochemical Noise Measurement techniques as shown in the schematic the Standard Bridge method, the single substrate, and the NOCS termed ‘No Connection to Substrate’.
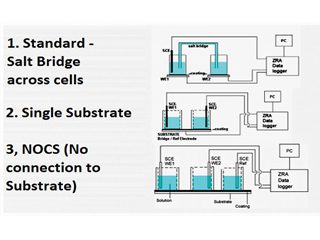
The experimental work had the following aims:
1. Examination of different arrangements of ENM on a range of coated samples and comparison between them.
2. Checking the reproducibility of results and considering the more practical application of this technique in the field.
3. Investigation of NOCS arrangement of ENM.
Mild steel Q-panels were coated with an appropriate coating in the laboratory by a spreader bar.
The types of coating used in the experiments were mainly polyurethane with some Alkyd and others such as Waterborne Epoxy. To get exposure of the coated plates to the corrosive solution, plastic tubes were attached to the samples and sealed with silicon before filling with 3% Na Cl solution- the area of exposure was ~ 4 cm2. Saturated Calomel electrodes were used to measure the Electrochemical noise. An electrometer (Keithley 610) was used to make DC (Direct Current) measurements to compare Rn values with DC resistance values.
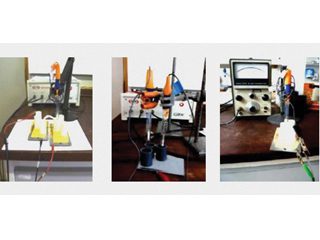
Reproducibility experiments were conducted over a period of 5 days, and they demonstrated that the technique gave stable results after multiple set-ups of the experimental apparatus.
A study was conducted to establish if one area of higher or lower resistance could be detected using the apparatus, i.e., if the Rn value of one area was different than for the other two, are we able to detect the odd one? If so, could we measure its value? A design experiment was set up using all permutations to compare high and low combinations of the coated plate resistances.
Designation of Cell DC Resistance Value (Ω)
A 6,40E+09
B 6,35E+09
C 6,40E+09
Designation of Cell DC Resistance Value (Ω)
X 5,50E+07
Y 1,05E+07
Z 1,30E+07
Six areas were used, three with high resistances A, B, C and 3 with lower resistances X, Y, Z, six combinations altogether.
In conclusion for this work, one single NOCS measurement, made with ACM equipment, when one cell was different from the other two, the research team could, by making multiple measurements, obtain the different value of Rn in the combination when the odd one was connected to WE1.
Using ECN for Green Inhibitor Testing
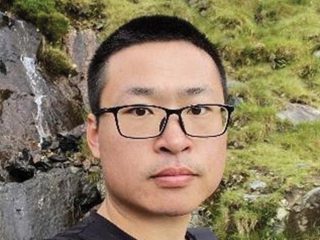
Tianyang Lan of DC Voltage Gradient Technology and Supply Ltd (DCVG).
Tianyang Lan has obtained both a BSc and MSc in General Engineering at the University of Northampton. During his studies, he conducted some Electrochemical Noise research projects under the supervision of Dr. Mills. He has worked as a researcher at the University of Nottingham, Department of Environmental Engineering, applying electrochemical noise and LPR (Linear Polarisation Resistance) techniques to the testing of green inhibitors. He is now working at the DC Voltage Gradient Technology and Supply Company, which has kindly provided various research equipment for the detection (e.g., ENM) and prevention (using coatings and CP) of pipeline corrosion.
Tianyang demonstrated how the EN Bridge Method can be used to assess a number of chemical inhibitors, both green and standard, for the corrosion of steel in hydrochloric acid.
The solution acts as a conduction ‘Bridge’ in the arrangement. The cell comprises a salt bridge with two working electrodes (5 x 2 cm2 carbon steel) with a Saturated Calomel Electrode as the Reference one. Test specimens were blanked off using a Corrocoat Zip E type coating giving an exposed area of 4.5 x 1.5cm2. Specimen holders were manufactured from an ABS material using 3D printing. The stirring speed was related to the size of the stirrer, (e.g. around 300 RPM for 3 cm stirrer).
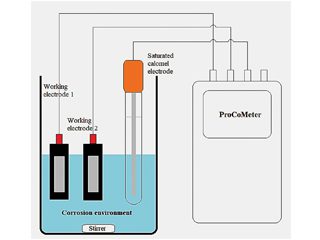
The study environments were:
• 1 % Propargyl alcohol (C3 H4 O). in 3 levels of HCl: 0.37 %, 2.6 %,
and 5.5 %.
• 0.25 % Green inhibitor (Broccoli or sugar beet) in 3 % NaCl + CO2 /
2.6 % HCl, including two commercial inhibitors.
Propargyl alcohol (PA) is commonly used as an effective inhibitor in HCl solutions in the oil and gas industry. The green inhibitors were experimental test additions.
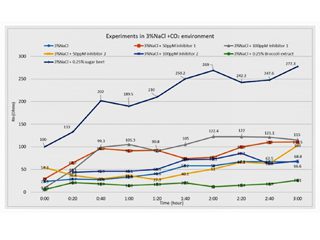
The results showed that, in Acid, PA provided significant corrosion protection (i.e. a higher Rn), especially in the highest concentration of 5.5% HCl environment. This result follows conventional theory. In 3% NaCl with CO2 bubbling through, the Rn values were found to be increasing over time, apart from when the Broccoli was added, where it actually increased corrosion compared with the control. The 100 ppm dose did better than 50 ppm for both commercial inhibitors, but surprisingly, Sugar beet showed the highest Rn value and also the biggest increase over time, suggesting potential as a green corrosion inhibitor. Comparison was made between the ENM and LPR methods using measurements on the same samples.
• ENM requires two separate iron specimens as working electrodes and one reference electrode.
• LPR measurement requires one working electrode, one reference electrode, and an additional counter electrode. It imposes an external current (±30mV) of the open circuit potential on the specimen.
In summary, the ENM approach gave comparable results to the more established Linear Polarisation Resistance (LPR) method. Further technical events are upcoming by the Aberdeen Branch, refer to Diary Dates at the rear of the magazine.
Abstracts of potential papers for the Aberdeen Technical Programme are always welcome, and anyone wishing to present should correspond with the 2024/2025 Technical Programme Co- ordinator: mei ling cheah meilingcheah@gmail.com Further Information about the Aberdeen Branch, and past presentations, may be found on their website page: Aberdeen Branch – Institute of Corrosion (icorr.org) and to join the Aberdeen Branch mailing list, please contact: icorrabz@gmail.com
CAPTIONS:
Douglas Mills, Senior Lecturer at
University of Northampton.
Left: The Electrode Arrangement is
Shown Here.
Graph Below:
All Data Obtained
Has to be Normalised by Detrending to Get the DC Potential Signature.
Different Configurations of ENM.
Measurements for a Range of Samples in Bridge and Single Substrate Arrangements of ENM and the Measurements of DC as a Comparative Method for ENM (L-R Salt Bridge, Single Substrate and DC Resistance).
Different ProCoMeter Resistances Deployed for Testing Purposes with Automated Switching of ACM Box.
The ProCoMeter Set-Up.
Various Inhibitors in 3 % NaCl + C02
Institute News
I hope this communication finds you all very well, and many thanks to all our clients, new and old, for continuing support.
During November and December 2023, CORREX was making inroads into becoming one of the ‘approved training providers’ for CITB, Construction Industry Training Board. I am very pleased to say that we gained this status in the last couple of weeks before the close of 2023. What this means is that the ICATS courses are now subject to a levy payment for clients that are registered with CITB and have their own unique employer CITB levy registration number. For example, our main course, ICA, Industrial Coating Applicator, is a Tier 3 course and now has a levy payment of £240 per student.
If you have your own number, please let me know, and when you carry out any training, I can add them to our portal, and then payments are automatic.
Please contact me if you require further information. We will also be introducing a complete suite of new forms very soon. These forms will replace any you have and are ISO 17024 (training provider qualification) compliant. Trainers and companies will also be sent emails updating this information.
I hope you enjoy a really good and prosperous new year.
Kind regards
Kevin Harold CORREX Ltd Managing Director
kevin@paintel.co.uk
Institute News
Welcome to the first issue of 2024!
Our present issue is dedicated to the theme “Corrosion in Concrete”. Problems with concrete structures have continued to dominate our headlines of late.
Paul Chess has authored the first technical article, “Recent Advances in understanding of corrosion of steel in concrete”. This article is a condensed and restricted version of his recent book. The corrosion process in reinforced concrete is a lot more complex than previously considered. Paul Chess has described the corrosion of steel in concrete very well. The second article is “The performance and assessment of galvanic anodes in concrete structures,” authored by C. Stone, G. Glass, and D. Bewley.
This article discusses the development of galvanic corrosion control for reinforced concrete structures, taking into account the evaluation and performance of the system through three case studies. Chris Atkins has written the third article, “Reinforced autoclaved aerated concrete in the UK” which follows on from his recent talk to our North West branch.
We invite industry news, technical articles, and articles for fellow’s corner from you in whichever part of the world you are based please send all your content for consideration to editor@icorr.org
I would like to wish you all the success and happiness in 2024.
Dr Shagufta Khan, FICorr
Consulting Editor
Institute News
Dear Members,
Welcome to our New Year edition of Corrosion Management. I do hope you all had a well-earned rest and enjoyed your break. You will have noted from our Nov/Dec magazine that we have a very full diary programme for the next 6 months across our branches, with more events still to be announced by our North-West and Midlands branches. Our training divisions also have very full schedules ahead of them. During 2024, we also expect to roll out more in-company training courses, both in the UK and overseas.
This year marks a very special occasion for the Corrosion World with the 100th anniversary of the publication in 1924 by U. R. Evans: The Corrosion of Metals, the first textbook specifically devoted to the subject. Ulick Richardson Evans studied at King’s College, Cambridge, and was described in the Biographical Memoirs of Fellows of the Royal Society as the “Father of the modern science of corrosion and protection of metals.” His major contribution to the subject involved placing on a firm foundation for the electrochemical nature of corrosion. Ulick
continued to publish research papers for the next 50 years, as well as updating his classic text, which was subsequently translated into many languages, including German, French, and Russian. The works of Ulick have been taught to numerous young Corrosion Engineers and for over 60 years, our own institute has continued to educate and train others in the prevention of corrosion.
The prime mover and brainchild for the formation of an Association of Corrosion Engineers in the UK was Dr. John Tiratsoo, who was the owner and driving force behind a magazine called ‘Corrosion Prevention and Control.’ He initially included in this magazine a section entitled ‘Corrosion Engineer,’ which was first issued in April 1959 and he then convened the inaugural meeting on the 21st May of that year at their offices at 97 Old Brompton Road, London. The association was therefore formed on that date, and an announcement was made to the national press at a social event at the Rembrandt Hotel on the 29th May 1959. With that in mind, the Institute has been exploring, of late, the possibility of some new U.K. branches and also further Overseas representation in the Middle East and Far East. The first of these will cover Wales and the South-West Region, which will host its inaugural event and AGM on 21st March 2024, and we are optimistic for a Central Scotland branch following that later in Q2 2024.
I wish you all every success in the year, head, wherever you work and in whatever you do, to help us grow our much-respected organisation.
With my best regards,
Stephen Tate, President: Institute of Corrosion